Ultra-small Size BGA/IC Substrates Manufacturer.High speed and high frequency material packaging substrate Manufacturer.
The rapid development of modern electronic devices requires smaller and more powerful components to meet increasingly compact designs and higher performance requirements. Under this challenge, ultra-small size BGA/IC substrates emerged as the times require, becoming a new milestone in precision electronic assembly. They not only provide higher integration and performance for electronic products, but also achieve wider applications in many industries such as medical and communications, promoting the progress and innovation of electronic technology.
What are Ultra-small Size BGA/IC Substrates?
Ultra-small size BGA/IC substrate is a highly precise electronic substrate that uses the most advanced technology and materials to integrate chips and other electronic components into a tiny space. This technology makes it possible to achieve more functionality and performance within a restricted space.
With the continuous advancement of technology, modern electronic devices have increasingly higher requirements for size and performance. Ultra-small size BGA/IC substrate emerged as an innovative solution. It uses advanced manufacturing processes to integrate multiple electronic components into a tiny space, thereby achieving a highly integrated and compact design of the circuit. Compared with traditional circuit boards, ultra-small size BGA/IC substrates have higher integration and smaller size, and can implement more functions in a limited space, thus meeting the requirements of modern electronic equipment for miniaturization and lightweighting. needs.
The manufacturing process of ultra-small size BGA/IC substrates is very complex and requires advanced manufacturing equipment and precise processes. During the manufacturing process, it is first necessary to design a circuit layout that meets the requirements, then use photolithography technology to transfer the circuit pattern to the surface of the substrate, and then use soldering technology to precisely connect the chip and other electronic components to the substrate. Finally, testing and quality control are carried out to ensure that the performance and reliability of the product meet standard requirements.
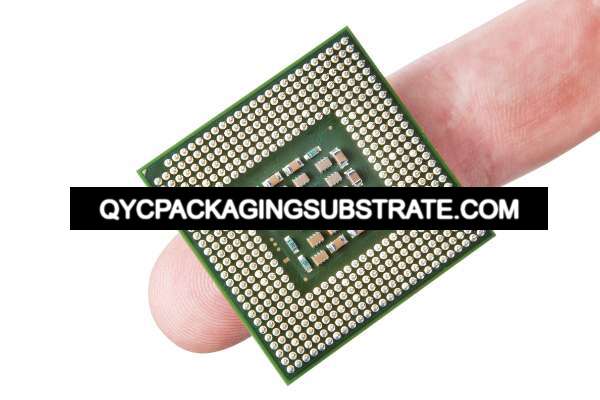
Ultra-small Size BGA/IC Substrates Manufacturer
Ultra-small size BGA/IC substrates are widely used in many fields, such as consumer electronics, medical equipment, communication equipment, etc. In consumer electronics products such as mobile phones, tablets, and smart wearable devices, ultra-small size BGA/IC substrates are particularly widely used, enabling thinner and smarter product designs. In the field of medical equipment, ultra-small size BGA/IC substrates can achieve miniaturization and portability of medical equipment, improving the portability and applicability of medical equipment. In the field of communication equipment, ultra-small size BGA/IC substrates can achieve miniaturization and high performance of communication equipment, and improve the transmission rate and stability of communication equipment.
In general, the emergence of ultra-small size BGA/IC substrates provides new possibilities for the design and manufacturing of electronic equipment, and will bring more innovations and surprises to the development of future electronic equipment.
Ultra-small Size BGA/IC Substrates design Reference Guide.
Ultra-small size BGA/IC substrate design is a comprehensive task that requires engineers to fully consider multiple factors to ensure the performance and reliability of the final product. Design reference guides provide valuable advice and tips to help engineers optimize their designs for optimal performance.
First of all, circuit layout is a crucial part of designing ultra-small size BGA/IC substrates. Reasonable circuit layout can minimize signal interference and crosstalk and improve the stability and reliability of the circuit. Engineers need to consider placing critical circuit components in appropriate locations to minimize signal transmission path lengths and take steps to reduce signal reflections and leakage.
Secondly, thermal management is an aspect that requires special attention when designing ultra-small size BGA/IC substrates. Due to the increase in integration and reduction in size, ultra-small size BGA/IC substrates usually face higher heat density and heat dissipation issues. Therefore, engineers need to design effective heat dissipation structures, including heat sinks, heat dissipation holes, etc., to ensure that the temperature of chips and other critical components is maintained within a safe range.
In addition, signal integrity is also an aspect that requires special attention when designing ultra-small size BGA/IC substrates. Due to the compactness of circuit layouts and the complexity of signal transmission paths, signal integrity can be severely affected, resulting in signal distortion and performance degradation. Therefore, engineers need to take measures to reduce the length and loss of the signal transmission path, and adopt appropriate signal layer stacking and impedance matching technology to ensure stable transmission and accurate reception of signals.
To sum up, designing ultra-small size BGA/IC substrates requires engineers to fully consider circuit layout, thermal management, signal integrity and other aspects, and take corresponding measures to optimize the design to achieve the best performance. The design reference guide provides engineers with valuable suggestions and tips to help them better meet this challenge and achieve optimal design of ultra-small size BGA/IC substrates.
What material is used in Ultra-small Size BGA/IC Substrates?
The performance and reliability of ultra-small size BGA/IC substrates depend largely on the materials selected. To ensure that these substrates operate stably and provide excellent performance under various environmental conditions, engineers often choose high-performance materials for manufacturing.
Among them, one of the most common materials is special fiberglass reinforced resin, namely FR-4. FR-4 is a very strong and durable material with excellent insulating properties and mechanical strength that can withstand vibration and shock, thereby protecting circuits from damage. In addition, FR-4 also has good heat resistance and corrosion resistance, and can operate stably in various harsh environmental conditions.
In addition to FR-4, ultra-small size BGA/IC substrates often use metal with high thermal conductivity as part of the material. These metals are often used in thermal layers or thermal pads to help effectively disperse and remove heat, preventing chips and other critical components from being damaged by overheating. By using metals with high thermal conductivity, such as copper or aluminum, the heat dissipation efficiency of the substrate can be improved and the stability and reliability of the circuit can be ensured.
To sum up, the materials used in ultra-small size BGA/IC substrates, such as special glass fiber reinforced resin and high thermal conductivity metal, are designed to provide optimal performance and reliability. The selection of these materials has been carefully considered to ensure that the substrate will perform well in a variety of application scenarios and meet the stringent performance and stability requirements of modern electronic devices.
What size are Ultra-small Size BGA/IC Substrates?
When talking about the size of ultra-small BGA/IC substrates, we inevitably think about the impact of their tiny size on electronic assembly and device design. While they are indeed small in size, their size and shape are also carefully designed and standardized to ensure that they are compatible with existing equipment and technology and can function in a variety of application environments.
First, let’s look at the size of ultra-small size BGA/IC substrates. These substrates typically range from a few millimeters to a few centimeters, depending on their design goals and required functionality. Due to their tiny size, ultra-small size BGA/IC substrates can be easily integrated into a variety of devices and systems, from portable consumer electronics to medical equipment and industrial control systems.
Secondly, the shape of ultra-small size BGA/IC substrate is also worthy of attention. Although they typically take a rectangular or square shape, in certain applications other shapes may be used to maximize the available space and meet specific design needs. No matter the shape, these substrates are designed with careful consideration to ensure their performance and stability.
In addition, the standardization of ultra-small size BGA/IC substrates is also very important. By developing and following uniform size and shape standards, manufacturers and designers can ensure that their products integrate seamlessly with other equipment and technologies, thereby reducing production costs and accelerating time to market.
Overall, although ultra-small size BGA/IC substrates are very small, their size and shape are carefully designed and standardized to ensure that they can perform optimally in various applications and integrate with existing equipment and technology compatible. This makes them ideal for many precision electronic assemblies and brings tremendous convenience and innovation to a variety of industries.
The Manufacturer Process of Ultra-small Size BGA/IC Substrates.
Manufacturing ultra-small size BGA/IC substrates is a highly precise process involving multiple key links. Each step has a direct impact on the quality and performance of the final product.
First of all, lithography technology is one of the core steps in manufacturing ultra-small size BGA/IC substrates. This process involves transferring designed circuit patterns to the substrate surface through photolithography. In this process, a high-precision photolithography machine is needed to project the designed pattern onto the photosensitive material, and then develop and etch it to form a precise circuit pattern.
Secondly, welding is another crucial link. Chips and other components on ultra-small size BGA/IC substrates need to be precisely connected to the substrate. Surface mount technology (SMT) is usually used. The components are fixed on the surface of the substrate by melting solder paste, and soldered using high-temperature hot air or a reflow oven to ensure a strong and reliable connection.
Finally, the testing phase is crucial. After manufacturing, each ultra-small size BGA/IC substrate needs to undergo rigorous testing to ensure its normal function and stable performance. Commonly used test methods include functional testing, reliability testing, temperature cycle testing, etc. to verify the stability and reliability of the product under various conditions.
In general, manufacturing ultra-small size BGA/IC substrates requires highly sophisticated equipment and technical support, and every step is crucial. Only through careful design and strict control of the manufacturing process can high-quality, high-performance ultra-small size BGA/IC substrates be produced to meet the needs of modern precision electronic assembly.
The Application area of Ultra-small Size BGA/IC Substrates.
Ultra-small size BGA/IC substrates are widely used in various fields. Their small size and high performance make them ideal for many precision electronic assemblies. In the field of consumer electronics, ultra-small size BGA/IC substrates are widely used in mobile devices such as smartphones, tablets, and smart watches. As consumer electronics products have increasingly higher requirements for volume and performance, ultra-small size BGA/IC substrates can implement more functions in a limited space and provide users with a better experience.
In the field of medical equipment, the application of ultra-small size BGA/IC substrates is also very important. Medical devices often require highly precise functionality and stable performance to ensure accurate diagnosis and treatment. Ultra-small size BGA/IC substrates can implement complex circuit functions in medical equipment while maintaining the compactness and portability of the equipment, bringing great convenience to the medical industry.
In the field of communication equipment, ultra-small size BGA/IC substrates are also widely used. Whether it is a mobile phone base station, satellite communication equipment or network router, high-performance electronic components are required to support their complex functions. Ultra-small size BGA/IC substrates can realize highly integrated circuit functions in these communication equipment while providing excellent performance and reliability, providing important support for the development of the communication industry.
In addition to the above fields, ultra-small size BGA/IC substrates are also widely used in automotive electronics, industrial control, aerospace and other fields. With the continuous development and innovation of technology, ultra-small size BGA/IC substrates will continue to play an important role in promoting the progress and development of various industries.
What are the advantages of Ultra-small Size BGA/IC Substrates?
The advantage of ultra-small size BGA/IC substrates lies in its many advantages compared with traditional circuit assembly methods. These advantages include higher integration, better thermal management capabilities and higher reliability, which provides a good foundation for the development of electronic products. Design and production bring great convenience.
First, ultra-small size BGA/IC substrates have higher integration levels. Due to its advanced design and manufacturing technology, ultra-small size BGA/IC substrate can integrate more functions and components in a very small space. This means that more complex circuit designs can be realized in a limited space, thus providing the possibility for performance improvement and functional enhancement of electronic products.
Secondly, ultra-small size BGA/IC substrates have better thermal management capabilities. Since the operation of electronic devices often generates large amounts of heat, effective thermal management is crucial to keeping the device operating stably. The ultra-small size BGA/IC substrate adopts advanced materials and designs, which can conduct and dissipate heat more effectively, thereby keeping the temperature of electronic components within a safe range and improving the stability and reliability of the equipment.
Finally, ultra-small size BGA/IC substrates have higher reliability. Traditional circuit assembly methods may be affected by problems such as weak soldering connections and easy circuit interference. Ultra-small size BGA/IC substrates use advanced surface mounting technology and soldering processes to achieve more stable and reliable connections. , reducing the risk of component damage and failure and extending the service life of the equipment.
Taken together, the advantages of ultra-small size BGA/IC substrates in terms of integration, thermal management and reliability make them an important choice in the design and production of modern electronic products. By using ultra-small size BGA/IC substrates, designers can achieve higher performance, more stable and reliable electronic products, meet the growing market demand, and promote the progress and development of electronic technology.
FAQ
What are the advantages of ultra-small size BGA/IC substrates compared to traditional packaging?
Ultra-small size BGA/IC substrate has higher integration and better thermal management capabilities than traditional packaging. Thanks to its design using advanced technologies and materials, it can integrate more functions and components into a very small space, resulting in higher performance. In addition, the bottom connection method of the BGA package can provide better heat conduction, help to effectively dissipate heat, and improve the stability and reliability of the device.
Which industries are ultra-small size BGA/IC substrates suitable for?
Ultra-small size BGA/IC substrates are suitable for various industries, including but not limited to consumer electronics, medical equipment, communication equipment, aerospace, etc. In these industries, there are strict requirements for the size and performance of electronic products. Ultra-small size BGA/IC substrates can meet these needs and achieve the smallest possible physical size while ensuring performance, making products lighter and more portable.
What are the key steps in the manufacturing process of ultra-small size BGA/IC substrates?
The manufacturing process of ultra-small size BGA/IC substrates includes multiple key steps such as design, prototype production, and mass production. Among them, the design stage needs to determine key parameters such as circuit layout and material selection based on product requirements and technical specifications; the prototype production stage verifies the feasibility and performance of the design through processes such as proofing and testing; the mass production stage involves material procurement, printing, and electroplating , welding, testing and a series of processes to ensure product quality and stability.
What issues should be paid attention to during the design process of ultra-small size BGA/IC substrates?
When designing ultra-small size BGA/IC substrates, special attention needs to be paid to issues such as signal integrity, thermal management, and electromagnetic interference. Reasonable circuit layout and signal line design can minimize signal distortion and crosstalk; good thermal management design can ensure that chips and other components maintain appropriate temperatures when working and avoid overheating damage; effective electromagnetic shielding and suppression technology can reduce The influence of external interference on the circuit improves the stability and anti-interference ability of the system.