Specializing in the production of ultra-small FC-LGA substrates, our manufacturing facility prides itself on precision engineering and advanced technology. With a commitment to innovation, we craft substrates that meet the most stringent size requirements without compromising performance. Our expertise lies in creating compact yet robust substrates, tailored to the demands of modern electronics. From concept to delivery, we ensure meticulous attention to detail, guaranteeing the highest quality products for our clients. Trust us as your premier partner for ultra-small size FC-LGA substrates, where excellence meets efficiency in every component we produce.
With the rapid development of electronic technology, modern consumers have higher and higher requirements for equipment, requiring smaller and higher-performance electronic components. In this wave of technological innovation, ultra-small size FC-LGA (Flip Chip Land Grid Array) substrate has shown unique advantages and potential. This article will delve into the key features, manufacturing processes and application areas of ultra-small size FC-LGA substrates, as well as their important role in promoting the development of electronic technology.
What are Ultra-small Size FC-LGA Substrates?
FC-LGA substrate, namely Flip Chip Land Grid Array substrate, is a substrate using flip chip packaging technology. Compared with traditional packaging methods, FC-LGA substrates introduce higher flexibility and performance advantages in electronic component design. Its main features include miniaturization, high-density layout and low resistance.
First of all, the miniaturization of FC-LGA substrate is one of its outstanding features. Due to the use of flip chip packaging technology, the chip is flipped directly onto the substrate, so the overall packaging structure is more compact. Compared with traditional packaging methods, this enables the FC-LGA substrate to accommodate more functional units within the same size range and achieve higher integration.
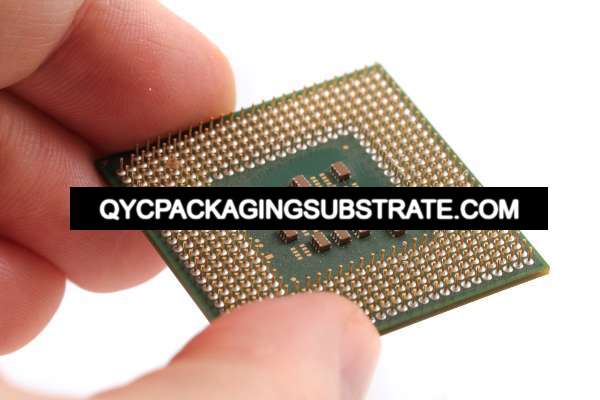
Ultra-small Size FC-LGA Substrates Manufacturer
Secondly, FC-LGA substrate has the advantage of high-density layout. The FC-LGA substrate enables a denser pin layout by flipping the chip and soldering it to the pin grid on the substrate. This layout method not only effectively utilizes the surface space of the substrate, but also increases the connection density between pins, thereby enabling the integration of more functions in a limited space.
In addition, the FC-LGA substrate also has the characteristics of low resistance. Since the chip is directly connected to the pins of the substrate, the electrical signal transmission path is shorter and the resistance is lower, thereby reducing signal transmission delay and energy loss. This is particularly important for high-performance application scenarios, which can improve the response speed and energy efficiency of the system.
In general, FC-LGA substrate has become an important choice in the design of modern electronic components due to its miniaturization, high-density layout and low resistance. Through flip-chip packaging technology, it achieves a more compact design and higher performance levels, providing strong support for the development of various electronic devices.
Ultra-small Size FC-LGA Substrates design Reference Guide.
Ultra-small Size FC-LGA Substrates (ultra-small size FC-LGA substrate) is an advanced technology of great significance in the design of electronic components. This substrate uses flip-chip packaging technology, providing an ideal solution for miniaturization and high performance of electronic devices. The following are key points to consider when designing ultra-small size FC-LGA substrates:
Size and layout
When designing ultra-small size FC-LGA substrates, it is necessary to accurately grasp the size and layout. Dimensions should be determined taking into account the required functionality and component count while ensuring compatibility with other components of the device. Layout design requires reasonable arrangements of chips, pins, through holes and other components to ensure smooth signal transmission without interference.
Pin design
The pin design of ultra-small size FC-LGA substrate is crucial. The pin layout should be dense but not crowded to ensure good connectivity and reliability. The arrangement of pins needs to take into account signal transmission efficiency and signal integrity to avoid electromagnetic interference and crosstalk.
Material selection
Selecting suitable materials is crucial for the design of ultra-small size FC-LGA substrates. Commonly used substrate materials include FR-4, high-frequency dielectric materials, etc. The material’s thermal properties, electrical properties, mechanical strength and other properties need to meet design requirements, taking manufacturing costs and reliability into consideration.
Thermal management
Due to the high integration and high power density of ultra-small size FC-LGA substrates, thermal management is an important consideration in the design. Effective heat dissipation design can improve the stability and reliability of the system and extend the service life of the equipment.
Signal integrity
When designing ultra-small size FC-LGA substrates, attention should be paid to signal integrity issues. Reasonably design the layout of signal leads and power leads to reduce signal transmission paths, reduce signal attenuation and delay, and ensure stable transmission and accuracy of signals.
Manufacturing process
The manufacturing process is critical to the quality and performance of ultra-small size FC-LGA substrates. Appropriate manufacturing processes and production equipment need to be selected to ensure the manufacturing accuracy and reliability of the substrate. At the same time, strict process control and quality inspection must be carried out to ensure that the product meets the design requirements.
To sum up, designing an ultra-small size FC-LGA substrate requires considering many aspects such as size and layout, pin design, material selection, thermal management, signal integrity and manufacturing process. Reasonable design and precise manufacturing processes can achieve high performance and stable and reliable operation of the substrate, providing strong support for the development of electronic equipment.
What material is used in Ultra-small Size FC-LGA Substrates?
The performance and reliability of Ultra-small Size FC-LGA Substrates depend largely on the materials selected. The following are the materials commonly used in the design and manufacture of Ultra-small Size FC-LGA Substrates and their characteristics:
Substrate material
Common substrate materials include FR-4 glass fiber reinforced epoxy resin, high-frequency dielectric materials, etc. FR-4 is a commonly used standard substrate material with good mechanical strength, heat resistance and electrical properties, and is suitable for general electronic applications. High-frequency dielectric materials have higher dielectric constants and lower dielectric losses, making them suitable for high-frequency and microwave circuit applications.
Conductive layer
Ultra-small Size FC-LGA Substrates often require layers with conductive properties to achieve electrical connections between chips and pins. Commonly used conductive layer materials include copper, silver, etc. Copper is a common conductive material with good conductivity and processability, and can form complex conductive patterns through processes such as chemical etching. Silver has higher electrical conductivity and is suitable for applications that require higher resistance.
Solder mask
The solder mask is used to encapsulate and protect Ultra-small Size FC-LGA Substrates to prevent the pins and pads on the circuit board from being oxidized. Commonly used solder resist materials include solder paste, pads, spray solder resist, etc. The solder resist material should have good adhesion, heat resistance and environmental protection to ensure welding quality and product reliability.
Packaging materials
Encapsulation materials are used to protect chips and circuit components from mechanical damage and environmental erosion. Commonly used packaging materials include epoxy resin, silicone, etc. Epoxy resin has good mechanical strength and heat resistance and is suitable for general packaging applications. Silicone has good flexibility and corrosion resistance, and is suitable for applications with high requirements for earthquake resistance and waterproofing.
In general, the material selection of Ultra-small Size FC-LGA Substrates requires comprehensive consideration of electrical properties, mechanical properties, heat resistance, environmental protection and other factors. Appropriate material selection can ensure the stability and reliability of the substrate and provide effective support for the performance improvement and size reduction of electronic devices.
What size are Ultra-small Size FC-LGA Substrates?
The size of Ultra-small Size FC-LGA Substrates is an important factor that needs to be carefully considered during the design and manufacturing process. The determination of size directly affects the integration level of the substrate, layout density and compatibility with other device components. Here are some important considerations regarding Ultra-small Size FC-LGA Substrates sizes:
Total measurement
Ultra-small Size FC-LGA Substrates usually have a smaller overall size, which is one of the keys to their miniaturization in electronic devices. The overall size needs to be determined based on specific application needs and functional requirements. It is necessary to ensure sufficient functional integration and take into account the space limitations and structural design of the equipment.
Chip size
The chips usually carried by Ultra-small Size FC-LGA Substrates are also relatively miniaturized to adapt to the size and layout requirements of the substrate. The determination of the chip size needs to take into account factors such as the chip’s function, integration level, and manufacturing process limitations to ensure the matching and stability of the chip and the substrate.
Pinout
The pin layout of ultra-small size FC-LGA substrate is also one of the important considerations in size design. The layout of pins needs to be compact but not crowded to ensure connection reliability between pins and stable signal transmission. Proper pin layout can maximize substrate integration and performance.
Thickness
In addition to length and width, the thickness of ultra-small size FC-LGA substrate is also an important parameter to consider in design. The determination of the thickness needs to take into account the mechanical strength, thermal conductivity of the substrate and the structural design of the overall device. Appropriate thickness can ensure the stability and reliability of the substrate, and also help improve thermal management and heat dissipation.
To sum up, the size design of Ultra-small Size FC-LGA Substrates needs to comprehensively consider multiple aspects such as overall size, chip size, pin layout and thickness. Reasonable size design can maximize the integration and performance of the substrate, providing strong support for the miniaturization and high performance of electronic devices.
The Manufacturer Process of Ultra-small Size FC-LGA Substrates.
Manufacturing ultra-small size FC-LGA substrates requires advanced processes and equipment support. From the selection of substrate materials to printing, etching, assembly and other process links, precise control and a high degree of automation are required to ensure substrate quality and production efficiency.
First of all, in the manufacturing process of FC-LGA substrate, it is crucial to select the appropriate substrate material. Common substrate materials include FR-4 glass fiber reinforced epoxy resin and high-frequency dielectric materials. These materials need to undergo rigorous screening and inspection to ensure that their performance meets the design requirements and can be used stably and reliably during the manufacturing process.
Secondly, the printing process is one of the key steps in FC-LGA substrate manufacturing. During the printing process, special ink or conductive powder is used to print the circuit pattern onto the surface of the substrate. Printing accuracy and uniformity are crucial to the quality and stability of circuit connections, so the accuracy and stability of printing equipment also need to be guaranteed.
Next is the etching process, which removes excess metal material from the substrate surface through chemical etching to form the required circuit pattern. The etching process requires controlling parameters such as the concentration, temperature, and time of the etching solution to ensure the etching effect and accuracy. At the same time, the etched substrate also needs to be cleaned and surface treated to remove etching liquid residues and ensure surface flatness.
The last is the assembly process, which is to assemble components such as chips, components and pins onto the substrate, and then weld and package them. During the assembly process of ultra-small size FC-LGA substrates, high-precision automation equipment and precise operating techniques are required to ensure accurate positioning and stable connection of components. The welding process requires control of parameters such as welding temperature, time and pressure to prevent component damage and poor weld quality.
To sum up, manufacturing ultra-small size FC-LGA substrates requires advanced technology and equipment support, which involves substrate material selection, printing, etching, assembly and other aspects. Only a precision-controlled and highly automated manufacturing process can ensure that substrate quality and production efficiency meet design requirements, providing strong support for performance improvement and size reduction of electronic equipment.
The Application area of Ultra-small Size FC-LGA Substrates.
Ultra-small size FC-LGA substrate plays an important role in various electronic devices. Its miniaturization, high-density layout and stability make it an ideal choice for a variety of application scenarios. The following are some common ultra-small size FC-LGA substrate application areas:
Smart phone
As a necessity for people’s daily lives, smartphones need to implement rich functions and performance in a limited space. The ultra-small size FC-LGA substrate can realize highly integrated circuit design, allowing smartphones to have a smaller and lighter design while providing stable and reliable performance.
Tablet
Tablet computers are one of the mainstream devices for mobile office and entertainment. Their thin, lightweight and portable designs pose challenges to the size and layout of circuit boards. The ultra-small size FC-LGA substrate enables a more compact design and provides higher integration and performance for tablet computers.
Wearable device
With the development of wearable technology, more and more people are paying attention to wearable devices such as smart watches and smart glasses. These devices have very strict size and weight requirements, and the ultra-small size FC-LGA substrate can just meet these requirements and achieve a lightweight and comfortable wearing experience.
Portable medical equipment
In the medical field, portable medical equipment such as portable electrocardiographs, sphygmomanometers, etc. play an increasingly important role in diagnosis and monitoring. The ultra-small size FC-LGA substrate can help these devices achieve compact designs, making them easy to carry and use, while ensuring the performance and reliability of the devices.
Industrial control and automation
In the field of industrial control and automation, ultra-small size FC-LGA substrates also play an important role. These substrates can be used in factory automation systems, robot control, sensor networks and other fields to help realize the intelligence and automation of equipment.
In general, ultra-small size FC-LGA substrates are widely used in many fields such as smartphones, tablets, wearable devices, portable medical equipment, and industrial control and automation. Its miniaturization, high performance and stability provide strong support for the development of these devices and promote the continuous progress and innovation of electronic technology.
What are the advantages of Ultra-small Size FC-LGA Substrates?
FC-LGA substrate (Flip Chip Land Grid Array) has many advantages compared with traditional packaging technology. These advantages make it an indispensable and important component in the design of today’s electronic products. The following are the main advantages of FC-LGA substrate:
Higher integration
The FC-LGA substrate uses flip-chip packaging technology to flip the chip directly onto the substrate, thereby achieving a higher level of integration. Compared with traditional packaging technology, FC-LGA substrate can accommodate more functional units in a smaller space, making electronic product design more compact and efficient.
Lower resistance and inductance
Because the chip is directly connected to the pins of the substrate, the FC-LGA substrate is able to reduce circuit path length, thereby reducing resistance and inductance. This helps to improve the transmission speed and stability of the circuit, reduce signal delay and distortion, and provide better performance for high-performance electronic products.
Better cooling performance
The flip-chip packaging method of FC-LGA substrate helps improve heat dissipation performance. The chip is directly connected to the substrate, making heat dissipation more efficient and able to conduct heat to the surface of the substrate faster and then dissipate it to the external environment. This is particularly important for electronic products that require long-term high-load operation, and can effectively maintain the stability and reliability of the equipment.
Higher reliability
The FC-LGA substrate adopts a soldering connection method, which has higher reliability than the solder ball connection of traditional packaging technology. Welded connections can provide greater mechanical strength and shock resistance, reduce the risk of breakage and loosening between components, and increase the service life and stability of the equipment.
Improved production efficiency
Compared with traditional packaging technology, the manufacturing process of FC-LGA substrate is more simplified and the production efficiency is higher. The flip-chip packaging method can reduce intermediate steps in the assembly process, shorten the production cycle, reduce manufacturing costs, and improve production efficiency.
To sum up, FC-LGA substrate has the advantages of higher integration, lower resistance and inductance, better heat dissipation performance, higher reliability and improved production efficiency. These advantages make FC-LGA substrates widely used in today’s electronic product design, providing strong support for performance improvement and size reduction of various electronic devices.
FAQ
What is the difference between FC-LGA substrate and BGA substrate?
FC-LGA substrate and BGA substrate are both common packaging technologies, but there are some differences between them. The main difference is how the chips are connected. In FC-LGA substrate, the pins of the chip are connected directly to the substrate, while in BGA substrate, the pins of the chip are connected to the ball pads of the substrate. In addition, the FC-LGA substrate requires the chip to be flipped over during the packaging process, while the BGA substrate does not. Therefore, FC-LGA substrates have higher integration and better heat dissipation performance, while BGA substrates have higher reliability and simpler manufacturing processes.
What electronic products are FC-LGA substrates suitable for?
FC-LGA substrate is suitable for various electronic products, including smartphones, tablets, wearable devices, portable medical equipment, industrial control and automation equipment, etc. Its miniaturization, high performance and stability make it widely used in these fields.
Is the manufacturing process of FC-LGA substrate complicated?
The manufacturing process of FC-LGA substrate is relatively complex and requires advanced equipment and precise control technology. The manufacturing process involves multiple links such as substrate material selection, printing, etching, and assembly, and requires a high degree of automation and precision control to ensure substrate quality and production efficiency.
What are the advantages of FC-LGA substrate?
Compared with traditional packaging technology, FC-LGA substrate has the advantages of higher integration, lower resistance and inductance, and better heat dissipation performance. This makes it an indispensable and important part of today’s electronic product design.