Ultra-Small Size Package Substrates Manufacturer.The manufacturer specializes in crafting ultra-small size package substrates, meticulously engineered for cutting-edge electronics. With precision and expertise, they fabricate substrates to exacting standards, catering to the demands of compact and sophisticated electronic devices. Their dedication to quality ensures each substrate meets stringent specifications, guaranteeing optimal performance and reliability. Leveraging advanced technologies and innovative techniques, they push the boundaries of miniaturization, enabling the creation of next-generation electronics. As pioneers in their field, they play a pivotal role in shaping the landscape of modern electronics, offering solutions that are both compact and powerful.
In the rapid development of modern electronic technology, ultra-small size package substrates (Ultra-small Size Package Substrates) have become key components and are widely used in various high-tech equipment and systems. Ultra-small packaging substrate is a flat plate used to support and connect electronic components. It is usually made of materials such as fiberglass reinforced epoxy (FR4) and has dimensions ranging from a few millimeters to several centimeters. Its manufacturing process includes substrate material preparation, wire etching, component assembly and testing, etc. Widely used in consumer electronics, automobiles, aerospace, medical equipment and other fields. Its advantages include compact size, high reliability, ease of mass production, good signal integrity and superior thermal performance.
What are Ultra-small Size Package Substrates?
Ultra-small Size Package Substrates (Ultra-small Size Package Substrates) are flat plates used to support and connect electronic components. They are usually made of non-conductive materials and have conductive paths etched or printed on their surfaces. These conductive paths, called wires, provide the electrical connections between electronic components. The design and manufacturing technology of ultra-small package substrates make them particularly suitable for applications with stringent size and weight requirements, such as portable electronic devices and high-density integrated circuits.
The core function of ultra-small packaging substrates is to provide a stable physical platform while enabling complex electrical interconnections. The substrate material usually uses fiberglass reinforced epoxy resin (FR4), which has excellent mechanical strength and electrical properties. In addition, according to different application requirements, materials such as ceramics, polyimide, and metal core substrates can also be selected. These materials can not only withstand high temperature and high pressure environments, but also ensure the stability and reliability of electrical characteristics.
In modern electronic devices, size and weight constraints are becoming increasingly stringent, especially in portable devices and high-density integrated circuit applications. Smartphones, wearable devices, micro sensors, etc. all require ultra-small packaging substrates that can provide higher integration and smaller footprints. This requires a high degree of precision in the design and manufacturing process to ensure that every conductive path can accurately connect the various electronic components.
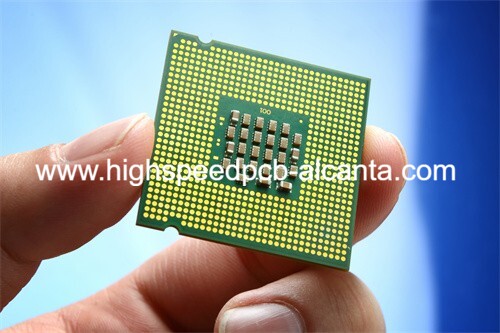
Ultra-Small Size Package Substrates Manufacturer
The process of manufacturing ultra-small packaging substrates involves multiple steps, each of which is critical. It begins with preparation of the substrate material and layer alignment, followed by etching or printing of the wires. Next is drilling holes to facilitate the installation of electronic components. In order to protect the wires and ensure the soldering quality of the components, a soldering mask also needs to be applied. Finally, the components are assembled and tested. These steps require highly sophisticated processes and equipment to ensure the reliability and performance of the final product.
Ultra-small packaging substrates are widely used in various high-tech fields, including consumer electronics, automobiles, aerospace, medical equipment, telecommunications, and industrial automation. In these areas, ultra-small packaging substrates are used to make products ranging from smartphones and computers to automotive control systems and medical imaging equipment. For example, in smartphones, ultra-small packaging substrates not only support complex circuit designs, but also help reduce the overall size and weight of the device, improving portability and user experience.
In short, ultra-small packaging substrates play a vital role as basic components of modern electronic devices. They not only meet the needs of high integration and small size, but also provide reliable electrical connections and excellent performance through precision design and manufacturing technology. With the continuous advancement of technology, ultra-small packaging substrates will play a greater role in more fields, promoting the development of electronic products in the direction of smaller, lighter, and smarter.
The types of Ultra-small Size Package Substrates
In the design and manufacturing of today’s high-tech products, ultra-small size package substrates (Ultra-small Size Package Substrates) play a vital role. These substrates not only need to meet stringent size and weight requirements, but also provide reliable electrical performance and mechanical strength. According to different application needs and design requirements, ultra-small packaging substrates can be divided into the following types:
Rigid substrate
Rigid substrates are usually made of fiberglass reinforced epoxy resin (FR4), which has excellent mechanical strength and thermal stability. They are widely used in consumer electronics such as smartphones, tablets and laptops. This type of substrate is characterized by strong durability and the ability to withstand stable operation in high-frequency and high-temperature environments.
Flexible substrate
Flexible Substrates are made of flexible materials such as polyimide (PI) or polyester (PET) and have excellent flexibility and bending properties. They are commonly used in applications that require complex three-dimensional layouts and dynamic bending, such as wearable devices, medical equipment, and some industrial sensors. The main advantages of flexible substrates are their ability to fit into the limited space inside the device and their overall weight reduction.
Rigid-flexible substrate
Rigid-Flex Substrates combine the advantages of rigid and flexible substrates, providing mechanical support for the rigid part and allowing flexible layout of the flexible part in a limited space. This substrate type is commonly used in complex electronic devices such as advanced smartphones, aerospace electronic systems, and military equipment that require reliable operation in harsh environments.
High Density Interconnect Substrate
High-Density Interconnect (HDI Substrates) achieve higher circuit density and smaller package size through tiny vias and precise wire design. HDI substrates are widely used in high-end electronic products that require high performance and small size, such as 5G communication equipment, high-performance computers, and advanced automotive electronic systems.
Metal core substrate
Metal Core Substrates use metal materials (such as aluminum, copper) as the core substrate and have excellent heat dissipation performance and mechanical strength. This type of substrate is commonly used in high-power LED lighting, power conversion equipment and some high-power electronic devices. A significant advantage of metal core substrates is their effective thermal management capabilities, which can extend the service life and stability of electronic devices.
Ceramic substrate
Ceramic Substrates are made of ceramic materials such as aluminum oxide (Al2O3) and aluminum nitride (AlN), which have high thermal conductivity and excellent electrical insulation properties. This type of substrate is often used in applications requiring high frequency, high temperature and high reliability, such as aerospace, military electronics and high-power microwave devices. Ceramic substrates are characterized by high temperature resistance and corrosion resistance, making them suitable for use in extreme environments.
The diversity of ultra-small packaging substrates enables them to meet the specific needs of different fields and applications. From consumer electronics to industrial automation, from medical equipment to military electronics, each type of substrate has its unique advantages and applicable scenarios. Understanding these substrate types and their characteristics can help select the most appropriate solution during the design and manufacturing process, improving the performance and reliability of electronic products.
The continuous innovation and development of ultra-small packaging substrates will continue to promote the advancement of electronic technology and meet more complex and demanding application needs in the future. I hope that through the introduction of this article, you can have a deeper understanding of ultra-small packaging substrates and find the best solutions in practical applications.
The advantages of Ultra-small Size Package Substrates
As electronic equipment increasingly develops towards miniaturization, lightweight and high performance, the application of ultra-small size package substrates (Ultra-small Size Package Substrates) has become more and more widespread. These substrates offer significant advantages in meeting the needs of modern electronics. The following are the main advantages of ultra-small packaging substrates:
Compact size and lightweight design
One of the biggest advantages of ultra-small packaging substrates is their ability to significantly reduce the size and weight of electronic products. Modern electronic devices, such as smartphones, wearable devices, and miniature sensors, have extremely strict size and weight requirements. By using ultra-small packaging substrates, these devices can be smaller and lighter without sacrificing functionality. This compact design not only improves the product’s portability, but also enhances the user experience.
High-density integration and optimized design
Ultra-small packaging substrates allow higher density component integration, allowing more functions to be packaged in a limited space. This is especially important for electronic devices that require high performance and functionality. For example, in smartphones and other portable devices, the use of ultra-small packaging substrates can integrate more functional modules such as cameras, sensors and wireless communication modules while keeping the device size small. This high-density integration not only improves device performance but also provides designers with more design flexibility.
Improved signal integrity and electrical performance
The design and manufacturing process of the ultra-small package substrate is optimized to ensure optimal signal integrity and electrical performance. Because these substrates usually use high-quality materials and precise manufacturing processes, they can effectively reduce electromagnetic interference and signal loss, thereby improving the speed and reliability of signal transmission. This is particularly critical in high-speed data transmission and high-frequency applications, such as 5G communications equipment and high-speed computers.
Superior thermal management performance
In high-performance electronic devices, thermal management is a critical issue. The ultra-small packaging substrate uses advanced materials and designs to effectively manage and dissipate heat. This not only helps extend the life of electronic components but also improves the overall performance of the device. For example, by integrating thermally conductive materials into the substrate, heat can be quickly and efficiently conducted away from the heating element to avoid overheating problems.
High reliability and productivity
Ultra-small packaging substrates have high reliability due to their precise manufacturing processes and strict quality control. Standardized design and production processes reduce errors during assembly, ensuring consistency and reliability for each substrate. In addition, these substrates are suitable for mass production, significantly reducing production costs and improving production efficiency. This is particularly important for consumer electronics products that require mass production.
Environmental protection and sustainability
Many ultra-small packaging substrates use environmentally friendly materials and processes to reduce environmental impact. For example, the use of lead-free soldering technology and recyclable substrate materials not only complies with environmental regulations, but also contributes to the sustainable development of the enterprise. This environmental advantage makes ultra-small packaging substrates even more attractive in modern electronics manufacturing.
In summary, ultra-small packaging substrates have become indispensable components in the design and manufacturing of modern electronic equipment due to their compact size, high-density integration, excellent signal and thermal management performance, high reliability, and environmentally friendly characteristics. With the continuous advancement of technology, ultra-small packaging substrates will play a key role in more fields and promote the innovation and development of electronic products.
How to Design a Ultra-small Size Package Substrates?
Designing ultra-small size package substrates (Ultra-small Size Package Substrates) is a complex and precise task that requires comprehensive consideration of multiple factors to ensure the functionality, reliability and manufacturability of the final product. Below are detailed steps and key considerations for designing ultra-small package substrates.
Determine design needs
Before the design begins, the design requirements and specifications of the product must first be clarified. This includes determining the size, shape, thickness of the substrate and the type and number of electronic components that need to be supported. Additionally, the operating environment, operating temperature range, and electrical performance requirements such as signal integrity and power management need to be considered.
Choose the right material
Material selection is a critical step in designing ultra-small packaging substrates. Commonly used materials include FR4 (fiberglass reinforced epoxy), ceramic, polyimide and metal core substrates. FR4 is the most common choice, but for applications requiring high thermal conductivity and high frequency performance, ceramic and metal core substrates may be more suitable. Material selection should be based on performance requirements, cost considerations, and manufacturing feasibility.
Design circuit diagram
Circuit diagram design is the core part of PCB design. Using professional design software such as Altium Designer, Cadence Allegro, or Eagle, create detailed drawings of all electronic components and their electrical connections. Circuit diagrams should be as concise and free of redundancy as possible to optimize space utilization and reduce signal interference.
Component layout
Component layout directly affects the performance and manufacturability of ultra-small package substrates. When laying out components, ensure that there is sufficient distance between components to avoid signal crosstalk and heat build-up. In addition, the functional relationship of components should also be considered and related components should be placed as close as possible to shorten the signal path and improve electrical performance.
Trace design
Trace design is a critical step in ensuring signal integrity and power distribution. When designing wiring, consider the shortest path for signal transmission, and avoid sharp turns and right-angle wiring to reduce signal reflection and interference. For high-speed signals, differential pairs and characteristic impedance matching techniques should be used. In addition, special attention should be paid to the design of power and ground wires to ensure good power integrity and noise suppression.
Cascading design
Layer Stackup determines the number of layers of the substrate and the functional distribution of each layer. For ultra-small packaging substrates, multi-layer designs are often used to make full use of limited space. A typical stacked design includes a signal layer, a power layer, and a ground layer, and each layer is connected through vias (Via). Proper stacking design helps reduce electromagnetic interference (EMI) and improves the reliability of signal transmission.
Thermal management design
Thermal management is critical to ensuring the reliability of ultra-small packaging substrates. Appropriate heat dissipation paths and thermal vias should be designed, and heat sinks or thermal pads should be placed where needed to effectively dissipate the heat generated by the components. In addition, the thermal conductivity of the material is also an important factor affecting the thermal management effect.
Design verification and optimization
After completing the preliminary design, the design needs to be simulated and verified, and professional EDA tools are used to analyze and optimize the electrical performance, thermal performance and mechanical strength. Through repeated iterations, potential issues in the design are identified and improvements made to ensure the final design meets all specifications and requirements.
Manufacturing and testing
After the design is completed, the design files (such as Gerber files) are handed over to the manufacturer for production. After manufacturing is completed, the finished product needs to undergo rigorous functional and reliability testing to ensure that its performance meets expectations. Common testing methods include electrical testing (such as short circuit and open circuit testing), environmental testing (such as high and low temperature testing) and mechanical strength testing.
Through the above steps and considerations, designing an ultra-small packaging substrate can not only meet the miniaturization and high-performance needs of modern electronic devices, but also ensure product reliability and manufacturability. Designers need to continuously learn and apply the latest technologies and tools to cope with changing market needs and technical challenges.
Why use ceramic Ultra-small Size Package Substrates over other boards?
In the design and manufacturing of modern electronic equipment, ultra-small size package substrates (Ultra-small Size Package Substrates) play a vital role. As technology continues to advance, material selection becomes even more important. Due to its unique advantages, ceramic substrates have gradually become the preferred material for ultra-small packaging substrates. Here are some of the key advantages of ceramic ultra-small packaging substrates over other types of substrates.
Ceramic materials have excellent thermal conductivity and can dissipate heat quickly and effectively. This is particularly important in high-power and high-density electronic applications such as power amplifiers, LED lighting, and high-frequency communications equipment. Compared with traditional FR4 materials, ceramic substrates perform better at dissipating heat, extending component life and improving device reliability.
The ceramic substrate has excellent electrical insulation properties and low dielectric constant, ensuring the integrity and stability of signals during high-speed transmission. This is particularly critical for high-frequency, high-speed electronic applications, such as RF (radio frequency) and microwave communications equipment. Low loss and high insulation enable ceramic substrates to support higher operating frequencies and faster data transmission speeds.
The mechanical strength and environmental resistance of ceramic materials enable them to perform well in harsh working environments. They are able to withstand high temperatures, chemical corrosion and mechanical shock, making them suitable for demanding applications such as aerospace, automotive electronics and industrial automation. In contrast, traditional substrates often perform poorly under these extreme conditions, affecting the long-term stability and safety of the device.
The processing accuracy and stability of ceramic substrates enable them to achieve smaller sizes and higher integration, which is suitable for the miniaturization trend of modern electronic products. Ceramic materials can support multi-layer structures and achieve efficient integration of complex circuits through fine wiring and high-density component installation. This makes ceramic ultra-small packaging substrates ideal for small, high-performance products such as mobile devices, wearable devices and advanced sensors.
Due to its excellent thermal, electrical, and mechanical properties, ceramic substrates are widely recognized for their reliability and stability in long-term use. Their high durability allows them to maintain excellent performance in high-stress and high-temperature environments, significantly reducing equipment maintenance and replacement costs, and improving the reliability and economic benefits of the overall system.
Ceramic materials are relatively environmentally friendly, do not contain harmful substances, and have less impact on the environment during the production process. In addition, the long life and high reliability of ceramic substrates reduce the generation of electronic waste and meet the requirements of modern environmental protection and sustainable development.
To sum up, ceramic ultra-small packaging substrates have become an ideal choice for the design and manufacturing of modern electronic equipment due to their superior thermal properties, electrical properties, high mechanical strength, environmental resistance, high-density assembly capabilities, long life and environmental protection characteristics. With the continuous advancement of technology, ceramic substrates will play an important role in more demanding applications, promoting the development of electronic products towards higher performance, smaller size and higher reliability.
What is the Ultra-small Size Package Substrates Fabrication Process?
The manufacturing process of Ultra-small Size Package Substrates is a highly precise and complex process that requires multi-step fine control and advanced technology to ensure the performance and reliability of the final product. The manufacturing process of ultra-small packaging substrates will be introduced in detail below.
The first step in the manufacturing process is to prepare the substrate material. Commonly used substrate materials include fiberglass reinforced epoxy (FR4), ceramics, polyimide, and metal core substrates. Choosing the right material is key as it directly affects the electrical and mechanical properties of the substrate.
For multi-layer substrates, layer alignment and lamination are critical steps. The circuit patterns on each layer need to be precisely aligned to ensure proper electrical connections. The lamination process is usually carried out under high temperature and pressure, so that the layers are tightly combined to form a strong whole.
Once the substrate material is prepared and laminated, the next step is to etch or print the conductive paths. Etching usually uses chemical methods to remove the unprotected copper layer to form the desired circuit pattern. Printing uses screen printing or other advanced printing technologies to print conductive ink directly on the substrate. This step determines the accuracy and reliability of the circuit.
After the wires are etched or printed, holes need to be drilled into the substrate to install electronic components and achieve interlayer connections. Modern manufacturing techniques often use laser drilling or mechanical drilling to ensure high precision in the location and size of holes. These holes will be used for subsequent plating and component soldering.
In order to create a conductive path within the drilled hole, electroplating and hole metallization are required. Through an electroplating process, conductive materials (such as copper) are deposited on the walls of the holes to ensure electrical connections between layers. This step is especially important for multilayer substrates because it directly affects the overall electrical performance.
After electroplating is completed, a solder mask needs to be applied to the substrate. A soldering mask is a protective layer that covers areas that do not require soldering to prevent short circuits or other electrical problems during subsequent soldering. Solder masks are typically applied via screen printing or spraying techniques and then UV cured.
In order to improve the weldability and corrosion resistance of the substrate, surface treatment is required. Common surface treatment methods include hot air leveling (HASL), electroless nickel gold plating (ENIG) and organic solder shielding film (OSP). These treatments ensure that the substrate maintains good electrical performance and soldering reliability over long periods of use.
The final step is to assemble the electronic components onto the substrate. This step typically uses automated equipment for precise component placement and soldering. Surface mount technology (SMT) and through hole technology (THT) are the most commonly used assembly methods. Through reflow soldering or wave soldering, the components are firmly fixed to the substrate to form a complete circuit.
After all manufacturing steps are completed, strict testing and quality control are essential. Including electrical testing, functional testing and environmental testing to ensure that each substrate meets design requirements and quality standards.
Through the fine control and optimization of the above-mentioned multiple steps, ultra-small packaging substrates can achieve high precision, high reliability and high performance to meet the growing needs of modern electronic equipment. This complex manufacturing process not only reflects the application of advanced technology, but also provides a solid foundation for the development of future electronic products.
The application of ceramic Ultra-small Size Package Substrates
Ceramic ultra-small packaging substrate is a key component favored in the modern electronics industry and plays an important role in various high-tech fields. Compared with traditional substrate materials, such as fiberglass reinforced epoxy resin (FR4), ceramic substrates have better performance and characteristics, making them widely used in some special fields.
Due to the excellent high-temperature resistance of ceramic materials, ceramic ultra-small packaging substrates are often used in electronic devices that need to work in high-temperature environments. For example, electronic control systems in high-temperature environments such as rocket engine control systems and automobile engine control units in the aerospace field require substrates that can operate stably in high-temperature environments, and ceramic substrates are ideal for meeting this demand.
Ceramic materials have excellent corrosion resistance and can resist erosion by corrosive media such as acids and alkalis. Therefore, in some special environments, such as marine exploration equipment, chemical equipment, etc., it is necessary to use electronic equipment with corrosion resistance, and ceramic ultra-small packaging substrates can provide stable and reliable electrical connections to ensure the long-term stability of equipment in harsh environments. run.
The low dielectric constant and low loss tangent of ceramic substrates enable excellent performance in high-frequency circuits. Therefore, in applications such as communications, radar systems, and radio frequency modules that require processing of high-frequency signals, ceramic ultra-small packaging substrates have become the material of choice. Its excellent high-frequency characteristics can ensure the stability and accuracy of signal transmission, thus improving the performance of the entire system.
In the fields of medical devices and biosensors, extremely high requirements are placed on the biocompatibility and stability of materials. Due to the characteristics of its inorganic materials, ceramic ultra-small packaging substrates have excellent biocompatibility and chemical stability, and can meet the stringent requirements for material performance of medical equipment and biosensors.
In summary, ceramic ultra-small packaging substrates have broad application prospects in the fields of high temperature, corrosion, high frequency and medical treatment. They provide reliable basic support for electronic equipment in various special environments and promote the development and development of modern electronic technology. application. With the continuous progress and innovation of science and technology, it is believed that ceramic ultra-small packaging substrates will show their huge potential and value in more fields.
FAQs
What is the difference between ultra-small packaging substrates and traditional packaging substrates?
Traditional packaging substrates are often larger and thicker and are suitable for general electronic devices. The ultra-small packaging substrate is designed for lightweight and miniaturization, so it is smaller and more compact. In addition, ultra-small packaging substrates often use advanced materials and manufacturing processes to meet high performance and high reliability requirements.
What factors need to be considered in the design of ultra-small packaging substrates?
The design of ultra-small packaging substrates requires consideration of many factors, including but not limited to: layout and arrangement of electronic components, wire path planning, signal integrity, thermal management, EMI/EMC (electromagnetic interference and electromagnetic compatibility), etc. Designers need to consider these factors to ensure the performance and reliability of the final product.
What application scenarios are ultra-small packaging substrates suitable for?
Ultra-small packaging substrates are widely used in various high-tech fields, including portable consumer electronics (such as smartphones, tablets, headphones), medical equipment (such as medical monitoring instruments, health trackers), industrial control systems (such as sensors, automation equipment), drones, smart wearable devices, etc. The small size and high performance of these substrates make them ideal for these areas.
Is the manufacturing process of ultra-small packaging substrate complex?
The manufacturing process of ultra-small packaging substrates may be more complex than traditional packaging substrates because higher precision and more advanced technology are required to achieve tiny sizes and high-density layouts. Every step in the manufacturing process requires strict control to ensure the quality and performance of the final product.
What about thermal management of ultra-small packaging substrates?
Since ultra-small packaging substrates often integrate a large number of electronic components into a very small space, thermal management is an important consideration. Designers usually use thermal design, thermal path planning, thermal conductive material selection and other methods to effectively manage and disperse heat to ensure the stability and reliability of the equipment under high load and long-term operation.