What is ultra-thin rigid PCB?
Ultra-thin hard PCB Manufacturer. Ultra-thin hard PCB thickness: 3mil, 4mil, 5mil, with FR4 materials, BT core , Rogers core, or other High speed and high frequency material. the 4 layer Ultra-thin hard PCB thickness will be about 7mil~8mil.
Ultra-thin rigid PCB, as a key technology in the modern electronics industry, plays a vital role. It not only has excellent thinness, but also maintains excellent durability and stiffness, providing new possibilities for the design and manufacturing of electronic devices.
In the design of electronic devices, space is often a precious resource. As people’s requirements for device size become increasingly strict, traditional PCB design can no longer meet the needs of modern electronic products. This introduces the concept of ultra-thin rigid PCB. They are designed to be extremely thin, allowing them to be easily embedded into a variety of small devices such as smartphones, tablets and wearables, while still maintaining superior performance.
Ultra-thin rigid PCBs are not just thin, they must also have excellent durability and stiffness. This means that they must be able to withstand a wide range of external pressures and environmental conditions, such as temperature changes, humidity and mechanical stress, in small spaces. Therefore, the design and manufacturing of ultra-thin rigid PCBs must undergo precise processes and rigorous testing to ensure that they can operate reliably under various extreme conditions.
To meet these requirements, ultra-thin rigid PCBs undergo a sophisticated design process. Engineers use advanced software and technology to carefully lay out circuits and use high-performance materials such as FR-4 fiberglass epoxy and high thermal conductivity copper foil to ensure performance and reliability. During the manufacturing process, advanced production equipment and processes are used to precisely control the thickness and quality of the PCB to ensure that it meets the design specifications and can operate stably under various conditions.
Overall, ultra-thin rigid PCBs represent an important innovation in electronics design and manufacturing. Their emergence has brought new possibilities to the development of modern electronic equipment, creating more compact, lightweight and powerful products for us.
How to design ultra-thin rigid PCB?
When designing ultra-thin rigid PCBs, engineers need to be careful and considerate to ensure they achieve optimal performance in a compact space. The design process of ultra-thin rigid PCB and its key aspects will be introduced in detail below:
First, the design team uses professional software, such as Altium Designer, Cadence Allegro, etc., to start planning the circuit layout. These software provide a rich set of features that enable engineers to intuitively lay out electronic components and optimize their placement and connections. At this stage, engineers need to consider factors such as the circuit’s functional requirements, space constraints, and heat distribution.
Secondly, engineers focus on how the circuit is laid out. They focus on arranging components in a compact but efficient space to minimize PCB size. Through precise layout, circuit complexity can be reduced and signal transmission paths optimized, thereby improving circuit performance and reliability.
During the layout process, engineers also need to pay special attention to signal integrity and thermal management. They use simulation tools to simulate and analyze the circuit to ensure that the signal transmission on the PCB is stable and reliable. At the same time, they take measures to effectively disperse and dissipate heat to avoid overheating of the circuit, which can lead to performance degradation or failure.
In addition, the design team must also consider the layered structure and stacking method of the PCB. By rationally selecting the interlayer insulation material and copper foil thickness, the PCB can be made thin while ensuring its hardness and stability.
Finally, after the design is completed, engineers need to conduct rigorous design verification and review. They utilize EDA tools for circuit routing and electrical rule checking to ensure that the design complies with standards and specifications and can meet the product’s performance requirements.
Overall, designing ultra-thin rigid PCBs is a complex and precise job. Through meticulous layout planning, signal integrity and thermal management considerations, engineers can ensure that PCBs achieve optimal performance and reliability in a compact space, thus providing solid technical support for the development of modern electronic equipment.
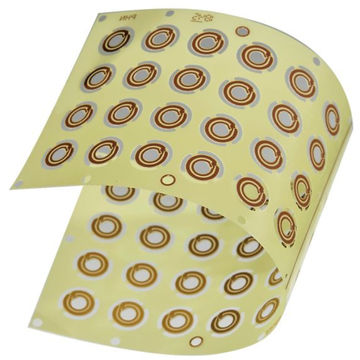
Ultra-thin hard PCB
What is the manufacturing process of ultra-thin rigid PCB?
The manufacturing process of ultra-thin rigid PCB is a precise and complex project involving multiple key steps. Each step is crucial and affects the quality and performance of the final product.
First, the process of manufacturing ultra-thin rigid PCB begins with preparing the substrate material. Usually, the substrate material used is fiberglass reinforced epoxy resin (FR-4), which has good electrical insulation and mechanical strength and is very suitable as the base material of PCB.
Next, layers of copper foil are layered onto the substrate. These copper foil layers will become conductive paths on the PCB, carrying current and signals. Through layer-by-layer stacking, multi-layer PCB design can be realized to meet the needs of complex circuit layouts.
Subsequently, the circuit pattern is etched. This step uses chemical methods or laser technology to remove unnecessary parts of the copper foil from the PCB surface, leaving the desired circuit pattern. This process requires highly precise control to ensure the accuracy and clarity of circuit patterns.
Advanced technologies such as laser drilling may also be used when manufacturing ultra-thin rigid PCBs. Laser drilling can achieve precise hole diameters and locations, providing greater flexibility and precision for component mounting on PCBs. This technology plays a vital role in achieving the required thickness and precision, especially for ultra-thin PCBs.
Strict quality control is indispensable throughout the entire manufacturing process. By using advanced inspection equipment and technology, manufacturers can conduct comprehensive inspections and tests on PCBs to ensure they meet specifications and standards. Any potential defects or issues are promptly discovered and corrected to ensure the quality and reliability of the final product.
In general, manufacturing ultra-thin rigid PCB is a complex and precise process that requires manufacturers to have advanced equipment and technology, as well as a strict quality control system. Only in this way can ultra-thin rigid PCBs with high quality and reliability be produced to meet the continuous improvement of performance and space requirements of modern electronic equipment.
How to make ultra-thin rigid PCB?
The manufacturing of ultra-thin rigid PCB is a precise and complex process that requires professional knowledge and the support of advanced equipment. The following are the key steps and technical points for manufacturing ultra-thin rigid PCB:
Manufacturing the substrate: The first step in manufacturing ultra-thin rigid PCB is to prepare the substrate material. The commonly used substrate material is fiberglass-reinforced epoxy (FR-4), which has excellent electrical insulation and mechanical strength, making it ideal for electronic applications.
Copper foil layer stacking: Copper foil is stacked on the substrate, which is the basis for forming the circuit pattern. The thickness of the copper foil is usually determined based on design requirements and can be precisely controlled during the manufacturing process.
Circuit pattern etching: Use chemical etching or laser etching technology to form the required circuit pattern on the surface of the copper foil. This step requires a high degree of precision to ensure the accuracy and stability of the circuit.
Control thickness: One of the keys to manufacturing ultra-thin rigid PCBs is precise control of the thickness of the substrate and copper layers. Special mechanical equipment presses the substrate and copper foil to the required thickness through processes such as lamination and hot pressing, while ensuring uniformity and reliability.
Quality Control: Strict quality control measures are implemented at every stage of the manufacturing process. From material selection to production processes, strict standards and specifications need to be followed to ensure the highest level of performance and durability of the final product.
Final inspection: After manufacturing is completed, final inspection and testing is performed. This includes visual inspection, dimensional measurements, electrical performance testing, etc. to ensure the product meets specifications and customer needs.
Through the above precise and systematic manufacturing process, ultra-thin rigid PCBs can be produced, providing key support and foundation for modern electronic equipment. These PCBs not only have excellent performance and stability, but can also meet the needs of various complex applications and promote the continuous development and innovation of electronic technology.
How Much Does a Ultra Thin Rigid PCB Cost?
When it comes to cost considerations for ultra-thin rigid PCBs, we must realize that their manufacturing costs vary depending on a variety of factors. First, size is one of the main factors that affects cost. Smaller size ultra-thin rigid PCBs usually require more precise machining processes and higher production costs because of higher technical requirements for arranging circuits in limited space. In contrast, although larger-sized PCBs may require more materials, their manufacturing costs may be lower because their production processes are relatively simple.
Secondly, the complexity of PCB also directly affects the cost. Complex circuit designs require more layers and more complex process flows, which increases manufacturing costs. For example, if the PCB requires multi-layer stacking, blind vias, buried vias or special materials, the corresponding manufacturing costs will increase.
Finally, order quantity is also an important factor affecting costs. Typically, mass production reduces the cost per PCB because the cost of running the production equipment can be spread over more products. But for small batches or custom orders, production costs may increase as production lines need to be adjusted to suit different requirements.
Although ultra-thin rigid PCBs may incur higher manufacturing costs due to their specialized characteristics, the space savings and performance improvements they provide often justify the investment. First, the compact design of ultra-thin rigid PCBs makes them suitable for applications with extremely high space requirements, such as smartphones, tablets, and portable medical equipment. Secondly, because ultra-thin rigid PCB has a higher integration level and optimized circuit layout, its performance is often more reliable and stable, thereby reducing equipment maintenance costs and failure rates, and bringing a better experience to users.
So while ultra-thin rigid PCBs may be slightly more expensive in terms of initial investment, the investment is often worth it when considering the advantages in space savings and performance improvements, as well as long-term reliability and stability. When selecting a PCB supplier, businesses should weigh a variety of factors, including cost, quality and delivery time, to ensure they choose the solution that best suits their needs.
What materials are used in ultra-thin rigid PCB?
When designing and manufacturing ultra-thin rigid PCBs, choosing the right materials is critical, as these materials directly affect the performance and reliability of the PCB. Here are some high-quality materials commonly used for ultra-thin rigid PCBs:
FR-4 fiberglass epoxy resin: FR-4 fiberglass epoxy resin is one of the most common substrate materials and one of the preferred materials for manufacturing ultra-thin rigid PCBs. It has excellent electrical insulation and mechanical strength, allowing it to maintain stability and reliability under various environmental conditions.
Copper foil: Copper is the main conductive material in ultra-thin rigid PCB. Copper has good electrical and thermal conductivity and can effectively transmit current and dissipate heat, thereby ensuring the performance stability of the PCB. In addition, copper has high corrosion resistance and can resist common chemicals and environmental influences, extending the life of the PCB.
Prepreg: Prepreg is a fiberglass-impregnated epoxy resin material used to bond copper foil to substrates. It has excellent adhesion and thermal stability, ensuring good adhesion between PCB layers and improving the mechanical strength and heat resistance of PCB.
Copper-clad foil: Copper-clad foil is a material that covers a layer of copper on the surface of a PCB and is used to form circuit patterns and conductive paths. It has good conductivity and processability, can meet the requirements of complex circuit layout, and improves the signal transmission performance and anti-interference ability of PCB.
Solder Mask: Solder Mask is a protective layer covering the surface of PCB to prevent short circuit and oxidation during soldering, while improving the appearance quality and durability of PCB. It is usually made of epoxy resin, which has good chemical and heat resistance.
To sum up, the materials used in ultra-thin rigid PCB manufacturing cover many aspects such as substrate materials, conductive materials, adhesive materials and protective materials, among which FR-4 fiberglass epoxy resin and copper are the most common and important materials, which together ensure the excellent performance and reliability of ultra-thin rigid PCBs.
What are 5 qualities of a good customer service?
In today’s highly competitive business environment, excellent customer service is crucial when choosing an ultra-thin rigid PCB manufacturer. Here are five key qualities that can help ensure your experience with your manufacturer is smooth and satisfying:
Response speed is one of the important indicators for measuring a manufacturer’s customer service level. When you make inquiries or ask questions to the manufacturer, they should be able to respond promptly with accurate and detailed information. A manufacturer that can respond quickly and solve problems can help you avoid unnecessary delays and increase productivity.
Reliability means that a manufacturer is able to deliver high-quality products on time and is able to fulfill all of its commitments. When choosing a manufacturer, you should look at their production capabilities, delivery record, and customer feedback and reviews to ensure they are trustworthy.
Manufacturing ultra-thin rigid PCBs requires highly specialized knowledge and skills. A quality manufacturer will have the experience and expertise to understand and meet your specific needs. They should be able to provide technical support and advice to help you optimize your design and resolve issues that may arise.
In an ever-changing market environment, flexibility is an important advantage for manufacturers. A quality manufacturer should be able to adapt to changes in your needs and provide you with customized solutions. They should be able to flexibly adjust production plans to meet your schedule and requirements.
Transparency is the basis for building trust and good working relationships. Manufacturers should be transparent about prices, delivery times, product specifications, etc. and provide you with timely updates and progress reports. By keeping communication open and transparent, manufacturers can ensure you always have a clear understanding of the progress of your project.
In general, choosing an ultra-thin rigid PCB manufacturer with good customer service characteristics is the key to ensuring a smooth and successful cooperation. By looking at aspects such as responsiveness, reliability, expertise, flexibility and transparency, you can choose a partner you can trust to drive your project to a successful conclusion.
FAQs
What is the typical thickness of an ultra-thin rigid PCB?
The thickness of ultra-thin rigid PCBs often depends on the specific application requirements. Generally speaking, they can be very thin, ranging from 0.2 mm to 0.8 mm in thickness. For some special applications, even thinner PCBs can be produced. Designers will choose the appropriate thickness based on the space constraints of the device and the stress and environmental conditions the circuit board will need to withstand.
Can ultra-thin rigid PCBs withstand harsh environmental conditions?
Yes, ultra-thin rigid PCBs are designed and manufactured to withstand a variety of harsh environmental conditions. They have excellent resistance to temperature, moisture and mechanical stress and can operate reliably in extreme temperatures, humidity and vibration environments. In addition, ultra-thin rigid PCBs usually use high-quality materials and manufacturing processes to ensure their stability and reliability, providing excellent performance even under harsh conditions.
How long is the production cycle of ultra-thin rigid PCB?
The production cycle of ultra-thin rigid PCB depends on several factors, including order volume, design complexity and manufacturer’s production capabilities. Typically, it takes several weeks from order confirmation to delivery. For urgent orders or special requirements, manufacturers may provide expedited services to shorten the production cycle. When selecting a manufacturer, one should consider its production capabilities and delivery times to ensure that orders can be completed in a timely manner.
How is the cost of ultra-thin rigid PCB calculated?
The cost of ultra-thin rigid PCB is affected by many factors, including board size, number of layers, thickness, material, surface treatment, etc. In addition, the order volume will also affect the cost. Generally speaking, the unit price of bulk orders will be lower. When requesting quotes from manufacturers, provide as detailed specifications and requirements as possible so they can give you an accurate quote. While ultra-thin rigid PCBs may be slightly more expensive than regular PCBs, their unique properties and advantages can often offset the cost difference.
How to choose a suitable ultra-thin rigid PCB manufacturer?
Choosing the right ultra-thin rigid PCB manufacturer is crucial. First, make sure the manufacturer has the experience and expertise to meet your specific needs. Secondly, it is necessary to inspect the manufacturer’s production equipment and quality control system to ensure that it can provide high-quality products. Additionally, pay attention to the manufacturer’s service levels, including delivery times, customer support, and after-sales service. By comprehensively considering these factors, choosing a manufacturer with good reputation and excellent quality can provide you with stable and reliable ultra-thin rigid PCB products and services.