Ultrathin BGA Package Substrates Manufacturer . the Package Substrate will be made with Showa Denko and Ajinomoto High speed materials.
As electronic devices become increasingly refined and functional, ultra-thin BGA (Ball Grid Array) packaging substrates have emerged as a key technology. These packaging substrates, with their extremely thin design and high-density connection methods, provide the possibility for performance improvement and volume compression of electronic devices. This article will deeply explore the characteristics, manufacturing process and application fields of ultra-thin BGA packaging substrates, aiming to reveal its importance in the design of modern electronic devices and its key role in electronic products such as smartphones, tablets, and laptops.
What are Ultrathin BGA Package Substrates?
Ultra-thin BGA packaging substrate is one of the key technologies that attracts much attention in today’s electronic field. It is a packaging solution based on printed circuit board (PCB) technology, which is unique in its extremely thin thickness and high-density solder ball array. This design allows electronic devices to achieve more compact packaging structures while maintaining reliable electrical connections.
Compared with traditional packaging solutions, one of the biggest advantages of ultra-thin BGA packaging substrates is its extreme thinness. By using advanced process and material technologies, manufacturers are able to control substrate thickness to extremely low ranges, even down to hundreds of microns or less. This ultra-thin design not only makes electronic devices thinner and lighter, but also helps improve their heat dissipation performance, thereby better meeting the dual needs of modern consumer electronics for volume and performance.
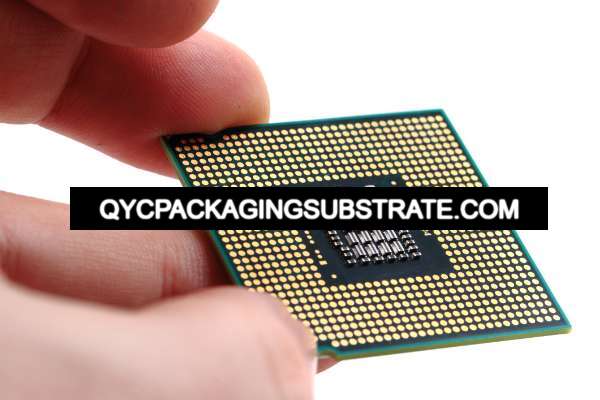
Ultrathin BGA Package Substrates Manufacturer
In addition, the ultra-thin BGA packaging substrate also has a high-density solder ball array, which means that more connection points can be accommodated in a limited space, thereby enabling more complex circuit designs. This is especially important for high-performance applications such as smartphones, tablets, drones and other devices that need to process large amounts of data and signals.
Overall, the ultra-thin BGA packaging substrate not only provides reliable electrical connections, but also provides an ideal solution for various high-performance applications through its compact packaging structure. Its wide application in electronic device design marks the continuous advancement of electronic technology in the direction of thinner, lighter and higher performance.
Ultrathin BGA Package Substrates design Reference Guide.
In modern electronic equipment, the design of ultra-thin BGA Package Substrates (Ultra-thin BGA Package Substrates) is crucial. This guide will provide you with important guidance on ultra-thin BGA package substrate design to help you make the most of this critical technology.
Design Principles
The design of ultra-thin BGA packaging substrates should take into account factors such as circuit layout, laminate structure, signal integrity and heat dissipation. During the design process, good signal transmission paths and electrical connections need to be ensured while maintaining package compactness and stability.
Material selection
Selecting the appropriate substrate material is critical to the performance of ultra-thin BGA package substrates. Commonly used substrate materials include FR-4, high-frequency materials and ceramic substrates. Each material has its specific electrical characteristics and mechanical strength and needs to be selected according to specific application requirements.
Packaging technology
The packaging technology of ultra-thin BGA packaging substrate includes solder ball connection, metallized holes and micro-lenses. When selecting packaging technology, factors such as signal transmission stability, heat dissipation performance, and manufacturing costs need to be considered to ensure optimal performance and reliability.
Thermal management
Due to the compact structure and high integration level of ultra-thin BGA package substrates, heat dissipation becomes an important consideration in the design process. Effective thermal management solutions can improve the working stability and life of the device and reduce the impact of temperature on electronic components.
Signal integrity
Maintaining signal integrity is one of the key challenges in ultra-thin BGA package substrate design. Through reasonable wiring planning, signal layer separation and regional coverage, signal crosstalk and timing distortion can be reduced to ensure reliable signal transmission.
Manufacturing process
The manufacturing process of ultra-thin BGA packaging substrates requires highly precise processing equipment and advanced process control. From board pretreatment to electroplating and encapsulation, each step requires strict control and fine adjustment to ensure the quality and stability of the final product.
Ultra-thin BGA packaging substrates are widely used in high-performance electronic products such as smartphones, tablets, and portable medical equipment. Its compact packaging structure and excellent performance make it an ideal choice for thin and light design and high-speed data transmission.
By following the above design guidelines, you can effectively design and optimize ultra-thin BGA packaging substrates, improve the performance and competitiveness of electronic products, and achieve wider applications and commercial success.
What material is used in Ultrathin BGA Package Substrates?
Ultra-thin BGA packaging substrate is an important part of modern electronic device design, and its material selection is crucial. The following are the materials commonly used for ultra-thin BGA packaging substrates and their characteristics:
Substrate material
Ultra-thin BGA packaging substrates usually use high-performance substrate materials such as polyimide (PI) and polytetrafluoroethylene (PTFE). These materials have excellent mechanical strength, thermal stability and chemical resistance, and can meet the requirements of high-density wiring and compact packaging.
Conductive layer
In ultra-thin BGA packaging substrates, copper foil is usually used as the conductive layer. Copper foil has good electrical conductivity and processability, enabling complex circuit wiring and ensuring good signal transmission.
Filler
In order to improve the flatness and surface smoothness of ultra-thin BGA packaging substrates, filler materials are often used to fill the wire gaps. Filling materials usually use materials such as epoxy resin or polyamide, which have excellent adhesion and high temperature resistance.
Solder ball
The solder ball of the ultra-thin BGA packaging substrate is the key component connecting the chip and the packaging substrate. Solder balls are usually made of tin alloy, which has good soldering performance and mechanical strength, ensuring stable electrical connection and reliable packaging structure.
Surface coating
In order to improve the corrosion resistance and welding performance of ultra-thin BGA packaging substrates, the surface of the conductive layer is often coated with a layer of metal or alloy, such as nickel, gold, silver, etc. These surface coatings effectively protect the conductive layers and provide good solder contact.
To sum up, the material selection of ultra-thin BGA packaging substrate is crucial to ensure circuit performance, packaging reliability and product quality. By selecting appropriate materials and carrying out precise process control, ultra-thin BGA packaging substrates with high performance and high reliability can be realized, promoting the development of electronic device design in the direction of thinner, lighter and higher performance.
What size are Ultrathin BGA Package Substrates?
Ultra-thin BGA packaging substrates are known for their compact design and high-density solder ball array, providing important solutions for the design of modern electronic devices. The size of these packaging substrates is often affected by a variety of factors, including application requirements, device size and manufacturing technology.
In practical applications, the size of ultra-thin BGA packaging substrates usually has a certain degree of flexibility to adapt to different device designs and performance requirements. Nonetheless, we can provide some general guidance:
Package area
The area of ultra-thin BGA packaging substrates is usually relatively small to accommodate the compact design requirements of modern electronic equipment. Nonetheless, its area can be adjusted to the requirements of the specific application, ranging from a few square millimeters to several square centimeters.
Thickness
Ultra-thin BGA packaging substrates are known for their thin designs, with thicknesses typically ranging from tens to hundreds of microns. This ultra-thin design not only helps reduce the overall device size, but also improves board flexibility and thermal performance.
Solder ball spacing
The solder ball spacing determines the soldering density and electrical connection performance of the ultra-thin BGA package substrate. Typically, the solder ball spacing is adjusted according to the power requirements of the device and the requirements of the soldering process to ensure a stable soldering connection and reliable electrical performance.
Number of layers
Ultra-thin BGA packaging substrates can use multi-layer designs to provide more signal pins and circuit connections. Typically, the number of layers can be adjusted based on the functional complexity and performance requirements of the device, ranging from two layers to multiple layers.
Overall, the size of ultra-thin BGA packaging substrates can be customized according to specific application requirements to achieve optimal performance and packaging effects. Whether used in smartphones, tablets or other electronic devices, ultra-thin BGA packaging substrates provide high-performance, compact and reliable solutions.
The Manufacturer Process of Ultrathin BGA Package Substrates.
The manufacturing process of ultra-thin BGA packaging substrates is a complex and precise process that combines advanced process and material technologies to ensure that the final product meets the requirements of high-performance electronic equipment. The following are the main steps of the ultra-thin BGA package substrate manufacturing process:
Substrate design
The first step in the manufacturing process is substrate design. This involves determining the size, hierarchy, and wiring layout of the substrate. Designers must consider electrical performance, thermal management, packaging density and other factors to ensure that the final packaging substrate meets the expected functional and performance requirements.
Laminated
During the lamination process, layers of film or resin are pressed together to create a multilayer structure. These layers can include substrates, dielectric layers, copper foil, etc., and are stacked according to design needs. The lamination process requires high temperatures and pressure to ensure adhesion and bonding quality between the layers.
Copper plating
After lamination is completed, the surface of the substrate needs to be covered with copper foil to form a conductive path. This is usually achieved through a copper plating process, in which a chemical solution coated with copper ions is deposited onto the substrate surface and an electrical current forms a conductive copper layer. The thickness and uniformity of the copper layer are critical to the performance of the circuit board.
Final packaging
Once the fabrication and copper foil covering of the substrate is complete, the final packaging process follows. This involves mounting electronic components (such as chips, resistors, capacitors, etc.) onto a substrate and securing them using soldering or other connection techniques. The package substrate may then go through testing and quality control processes to ensure it meets specifications and performance requirements.
The manufacturing process of ultra-thin BGA packaging substrates requires precise control and highly automated production lines to ensure product quality and consistency. Material selection, process parameters and equipment accuracy all have a significant impact on the performance and reliability of the final product. Through continuous technological innovation and process improvement, the manufacturing process of ultra-thin BGA packaging substrates will continue to be improved to meet the growing needs of the electronics market.
The Application area of Ultrathin BGA Package Substrates.
As an important component in the design of modern electronic equipment, ultra-thin BGA packaging substrate plays a key role in many fields. Its excellent electrical performance and compact packaging structure make it ideal for a variety of high-performance and thin and light designs.
The smartphone industry is a typical representative of ultra-thin BGA packaging substrate applications. As mobile phone functions continue to expand and performance improves, the requirements for packaging technology are becoming higher and higher. The ultra-thin BGA packaging substrate can not only meet the compact size requirements of mobile phones, but also provide stable electrical connections, allowing mobile phones to reach a higher level in terms of performance and appearance.
The tablet and notebook computer fields also benefit from the application of ultra-thin BGA packaging substrates. Consumer demands for mobile devices are increasingly inclined to be thin, light and high-performance, and ultra-thin BGA packaging substrates are one of the key technologies to achieve this goal. It ensures stable and reliable device performance while keeping the circuit board compact.
As an emerging application field, drones also widely use ultra-thin BGA packaging substrates. Drones have very strict requirements on volume and weight, and the thinness and lightness of the ultra-thin BGA packaging substrate make it an ideal choice. At the same time, its excellent electrical performance also ensures the stability and reliability of the drone during flight.
In general, the wide application of ultra-thin BGA packaging substrates in electronic devices such as smartphones, tablets, laptops, and drones not only improves the performance and stability of the products, but also promotes the trend of electronic products becoming thinner and lighter. high-performance development.
What are the advantages of Ultrathin BGA Package Substrates?
Ultra-thin BGA Package Substrates are an important part of modern electronic device design, and their advantages are self-evident. Compared with traditional packaging solutions, they present a series of eye-catching features, with significant improvements from volume to performance.
First, one of the biggest advantages of ultra-thin BGA packaging substrates is their compact size. With the continuous pursuit of thinner, lighter and more portable electronic devices, ultra-thin BGA packaging substrates have become the first choice for various high-end electronic devices due to their thin characteristics. Compared with traditional packaging solutions, they can achieve a more compact design in size, bringing more space to the lightweight and portability of electronic products.
Secondly, the light weight of the ultra-thin BGA packaging substrate is also an advantage that cannot be ignored. Due to the use of thin and light materials and structural designs, these packaging substrates can effectively reduce the overall weight of electronic devices while ensuring strength and stability, further enhancing the portability and use convenience of the device.
In addition to the advantages in size and weight, the ultra-thin BGA packaging substrate also has excellent transmission speed. Using advanced wiring technology and high-frequency signal transmission design, these substrates can achieve faster and more stable data transmission, providing a solid foundation for improving the performance of electronic equipment.
In addition, the ultra-thin BGA packaging substrate also has good heat dissipation performance. Through optimized design and material selection, these substrates can effectively disperse and remove the heat generated by the device, maintain the stability and reliability of the device during high-load operation, and extend the service life of the device.
To sum up, the ultra-thin BGA packaging substrate provides a reliable solution for performance improvement and volume compression of electronic devices with its many advantages such as small size, light weight, fast transmission speed and good heat dissipation performance. In an increasingly competitive electronics market, they will surely become an important driving force in promoting innovation and technological progress.
FAQ
How reliable is the ultra-thin BGA packaging substrate?
The ultra-thin BGA packaging substrate undergoes strict design and manufacturing processes and has excellent reliability. Its solder ball array provides a robust electrical connection, and its compact package helps reduce mechanical stress between devices, thereby improving overall reliability.
Is the maintenance of ultra-thin BGA package substrate complicated?
Under normal circumstances, the maintenance of ultra-thin BGA package substrates is not complicated. Due to their compact design, special tools and techniques are required to repair them, so maintenance is usually the responsibility of professional technicians or the equipment manufacturer.
What is the impact of ultra-thin BGA packaging substrates on the environment?
The ultra-thin BGA packaging substrate uses environmentally friendly materials and processes during the manufacturing process, and due to its compact design, the volume and weight of the device can be reduced, thereby reducing the consumption of resources. However, when disposing, correct treatment and recycling need to be carried out in accordance with local environmental regulations to reduce the impact on the environment.
What is the heat dissipation performance of ultra-thin BGA package substrate?
Ultra-thin BGA package substrates generally have better heat dissipation performance, mainly due to their compact design and the heat dissipation characteristics of the solder ball array. In addition, technologies such as additional radiators or heat pipes can be used during design to further improve the heat dissipation effect to meet the heat dissipation needs of high-performance electronic devices.