Ultrathin BGA Substrates Manufacturer.As a manufacturer specializing in ultrathin BGA substrates, our expertise lies in crafting intricate electronic components with unparalleled precision. Through cutting-edge technology and meticulous craftsmanship, we engineer substrates that embody the epitome of thinness without compromising on durability or performance. Each substrate undergoes rigorous quality assurance, ensuring flawless functionality in diverse applications ranging from consumer electronics to aerospace systems. With a commitment to innovation and excellence, we stand as leaders in the industry, delivering solutions that redefine the possibilities of electronic engineering.
As a key technological innovation in the field of modern electronics, ultra-thin BGA substrate plays an indispensable role in high-performance electronic devices and systems. Its design and application are developing rapidly and have been widely used in various industries. Its ultra-thin design and high-density layout provide new possibilities for lightweight and high-performance electronic products, injecting new vitality into the continuous progress and innovation of technology.
What are Ultrathin BGA Substrates?
Ultra-thin BGA substrate is an innovative electronic component that provides important support for the thinness and high performance of modern electronic devices. This substrate uses non-conductive materials, such as polyimide, to make an extremely thin planar structure, and its surface is covered with tiny solder ball arrays (BGA). These tiny solder balls are used to connect chips, electronic components and other devices to enable high-density circuit layouts and the assembly of complex electronic systems.
One of the characteristics of ultra-thin BGA substrate is its ultra-thin design. Due to the use of very thin substrate materials and the small size and spacing of solder balls, ultra-thin BGA substrates are thinner and lighter than traditional circuit boards. This makes them ideal for lightweight electronic devices such as smartphones, tablets, wearables, etc., which have strict size and weight requirements.
Another outstanding feature is the high-density layout of the ultra-thin BGA substrate. Through the precise arrangement of tiny solder balls, ultra-thin BGA substrates can connect more electronic components in a limited space, thereby improving circuit integration and performance. This high-density layout provides greater design flexibility and functional scalability for high-performance systems, making it possible to innovate and upgrade electronic products.
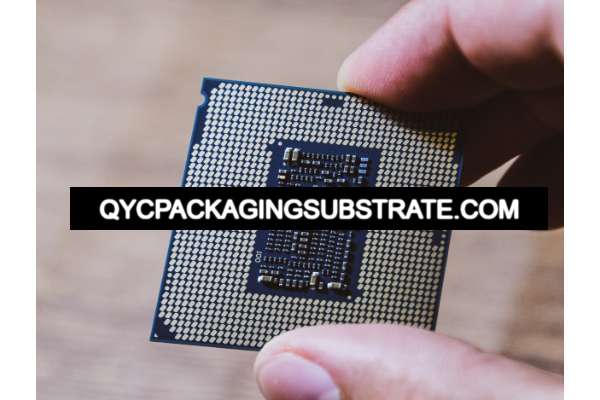
Ultrathin BGA Substrates Manufacturer
Since the design and manufacturing process of ultra-thin BGA substrates requires precise processes and advanced technology, they generally have high stability and reliability. This makes them widely used in application scenarios that require extremely high circuit performance and reliability, such as medical diagnostic equipment, industrial control systems, aerospace equipment, etc.
In general, the emergence of ultra-thin BGA substrates has brought important technological breakthroughs and innovations to the electronic field, providing more possibilities for the design and manufacturing of various electronic devices. With the continuous advancement of technology and the expansion of application scope, ultra-thin BGA substrates will continue to play an important role in promoting the development of the electronic industry in the direction of thinner, lighter and higher performance.
Ultrathin BGA Substrates design Reference Guide.
The design of ultra-thin BGA substrates (Ultra-Thin Ball Grid Array Substrates) is a complex and critical task that requires comprehensive consideration of multiple factors to ensure the performance and reliability of the final product. Here are some key points and reference guides for ultra-thin BGA substrate design:
Substrate material selection
Selecting the appropriate substrate material is crucial for the design of ultra-thin BGA substrates. Common substrate materials include polyimide (PI), polyamide amide (PAI), and aramid. These materials have excellent thermal properties, mechanical properties and chemical stability, and can meet the requirements of ultra-thin BGA substrates for lightweight, high density and high reliability.
Laminated design
The lamination design of ultra-thin BGA substrates needs to take into account factors such as wiring density, signal integrity and thermal management. Through reasonable lamination design, the optimal layout of the circuit and signal transmission path can be achieved, while the thickness and weight of the circuit board can be effectively controlled to ensure the stability and reliability of the product.
Circuit design
In the circuit design of ultra-thin BGA substrates, factors such as signal integrity, electromagnetic compatibility, and power consumption need to be considered. Reasonable line design can reduce signal crosstalk and noise interference, improve the anti-interference ability and stability of the circuit, thereby ensuring product performance and reliability.
Solder ball mounting
Solder ball installation on ultra-thin BGA substrates requires precise control of parameters such as soldering temperature, time and pressure to ensure soldering quality and reliability. At the same time, it is also necessary to consider the thermal stress impact of the welding process on the substrate and components, and take corresponding measures for thermal management and protection.
Final test
After the ultra-thin BGA substrate design is completed, strict final testing is required to verify the product’s performance and reliability. Test items include electrical testing, mechanical testing and environmental testing to ensure that the product can work stably under various conditions and have long-term reliability.
In summary, ultra-thin BGA substrate design is a complex and critical task that requires comprehensive consideration of multiple factors such as material selection, lamination design, circuit design, solder ball installation and final testing. Through reasonable design and precision manufacturing, the high performance, high reliability and long-term stability of ultra-thin BGA substrates can be achieved to meet the needs and challenges of various application fields.
What material is used in Ultrathin BGA Substrates?
The material selection of ultra-thin BGA substrate plays a vital role in its performance and application. Typically, ultra-thin BGA substrates are made of materials with a range of properties, including excellent electrical properties, high strength, high temperature resistance, and ultra-thin thickness. The following are some materials commonly used for ultra-thin BGA substrates:
Polyimide (PI)
Polyimide is a high-performance polymer material with excellent thermal stability, mechanical strength and chemical stability. Due to its high-temperature stability and ultra-thin characteristics, polyimide is often used as the base material for ultra-thin BGA substrates. It is able to withstand temperature changes in high-temperature welding processes and working environments while providing reliable electrical performance.
Polyamide ester (PEI)
Polyamide ester is another high-performance polymer material commonly used in ultra-thin BGA substrates. It has excellent properties similar to polyimide, including high strength, high temperature resistance and chemical stability. Polyamide esters are often used in applications requiring greater mechanical strength and rigidity.
Polyamide (PPA)
Polyamide is a type of high-performance polymer material with excellent heat resistance and mechanical properties. Their application in ultra-thin BGA substrates is usually to meet the requirements for high temperature resistance and high strength. The polyamide resin base material maintains stability in high temperature environments and provides reliable circuit support.
Metal substrate
In addition to polymer materials, metal substrates are also widely used in some special ultra-thin BGA substrates. Metal substrates have good heat dissipation performance and mechanical strength, and are suitable for some applications that require high thermal management. Common metal substrates include aluminum substrates and copper substrates.
Other materials
In addition to the above materials, there are some other special materials that can also be used for ultra-thin BGA substrates to meet specific application needs. For example, ceramic substrates have excellent high temperature resistance and electrical properties and are suitable for applications in some special high temperature environments.
In summary, the material selection of ultra-thin BGA substrate is crucial to its performance and application. Different materials have different characteristics and application ranges. Design engineers need to select appropriate materials based on specific application needs and performance requirements to ensure the stability, reliability and performance of ultra-thin BGA substrates.
What size are Ultrathin BGA Substrates?
The size of ultra-thin BGA substrates allows flexibility and diversity due to their special designs and applications. Typically, the size of ultra-thin BGA substrates can be customized according to specific application requirements. They can be very small, suitable for miniature electronic devices, or larger, used in high-performance systems.
For miniature electronic devices, such as smart watches, headphones, smart glasses, etc., the size of ultra-thin BGA substrates is usually very small. These devices have strict size and weight requirements, so the ultra-thin BGA substrate needs to be designed small enough to fit into the compact space layout of the device. These small ultra-thin BGA substrates may only be a few millimeters to tens of millimeters in size, but they are still able to provide high-density circuit layout and reliable electrical connections.
For high-performance systems, such as computer servers, network equipment, industrial control systems, etc., ultra-thin BGA substrates may be larger. These systems usually need to process large amounts of data and complex computing tasks, so ultra-thin BGA substrates need to have more circuit layers and larger sizes to accommodate more electronic components and connection lines. These large ultra-thin BGA substrates may reach dimensions of tens of centimeters or more, but they can still maintain ultra-thin design and high integration characteristics.
In summary, ultra-thin BGA substrates are available in a wide range of sizes and can be customized according to specific application needs. Whether it is micro electronic devices or high-performance systems, ultra-thin BGA substrates can provide high-density circuit layout, reliable electrical connections and excellent performance, providing important support for the design and manufacturing of various electronic products.
The Manufacturer Process of Ultrathin BGA Substrates.
The design and manufacturing of ultra-thin BGA substrates is a complex and precise process that requires advanced processes and technologies to ensure product quality and performance. In this process, every step is crucial and affects the stability, reliability and performance of the final product.
First, the choice of substrate material is crucial. Ultra-thin BGA substrates usually use high-performance non-conductive materials, such as polyimide (PI) or polytetrafluoroethylene (PTFE), to ensure that they have sufficient mechanical strength and thermal stability. Material selection should take into account circuit design requirements, as well as the environmental conditions and usage needs of the final product.
Next comes the lamination process, where the various layers of the multi-layer substrate are combined into a whole. This step requires precise control of temperature, pressure and time to ensure a strong bond between the different layers and that the overall thickness is within design specifications.
Circuit design is a key link in the manufacturing of ultra-thin BGA substrates. Design engineers need to consider factors such as circuit layout compactness, signal integrity, and electromagnetic compatibility, while minimizing line length and interlayer coupling to improve circuit performance and stability.
Solder ball mounting is the process of precisely mounting tiny solder balls on the surface of a substrate. This step requires high-precision equipment and delicate operating techniques to ensure that the connection between the solder balls and the chip pins is firm and reliable, and that the soldering process does not damage the substrate or electronic components.
Finally, there is the final test, which performs functional testing and performance verification on the ultra-thin BGA substrate to ensure that it meets the design specifications and customer requirements. The testing process involves many aspects such as electrical testing, thermal environment testing, reliability testing, etc., and requires comprehensive and precise testing methods and equipment.
In general, the design and manufacturing of ultra-thin BGA substrates requires multi-disciplinary collaboration, involving professional knowledge in materials science, electronic engineering, machining, process technology and other fields. Only through precise process control and advanced technical means can we produce ultra-thin BGA substrates that are stable, reliable, and have excellent performance, providing strong support for the development and application of modern electronic products.
The Application area of Ultrathin BGA Substrates.
Ultra-thin BGA substrates are widely used in today’s electronics field and play a key role in multiple industries. First, they are commonly found in consumer electronics such as smartphones and tablets. These devices have very strict requirements on volume and weight, and the compact design and highly integrated circuit layout of the ultra-thin BGA substrate enable these devices to achieve a thinner and lighter appearance while maintaining high performance.
In addition to consumer electronics, ultra-thin BGA substrates are also widely used in portable electronic devices. For example, portable audio players, handheld game consoles, camcorders and other products all use ultra-thin BGA substrates. These devices need to deliver outstanding performance and functionality while maintaining portability, and ultra-thin BGA substrates are key to achieving this goal.
In the field of medical diagnostic equipment, ultra-thin BGA substrates also play an important role. High-precision equipment such as medical imaging equipment and portable monitoring equipment require stable and reliable circuit support to ensure accurate data collection and processing. The ultra-thin BGA substrate’s high level of integration and excellent electrical performance make it ideal for these devices.
In addition, ultra-thin BGA substrates are also widely used in industrial control systems and other fields. Industrial automation equipment has extremely high requirements for stability, durability and high performance, and ultra-thin BGA substrates can meet these requirements and maintain good working conditions in extreme environments.
In general, ultra-thin BGA substrates play an important role in various fields, providing key support for the lightweight and high performance of modern electronic products. With the continuous advancement of technology and the continuous expansion of application fields, ultra-thin BGA substrates will continue to play an important role and inject new vitality into the development of the electronics industry.
What are the advantages of Ultrathin BGA Substrates?
The advantages of ultra-thin BGA substrates are not only reflected in its ultra-thin design and high-density layout, but also in its excellent electrical performance, thermal stability and reliability. These advantages make it outstanding in various complex applications.
First of all, the ultra-thin design of ultra-thin BGA substrate makes electronic devices thinner, lighter and more portable. Compared with traditional circuit boards, ultra-thin BGA substrates can achieve a more compact design and save space, making electronic products smaller in size and easier to carry. This is particularly important for portable electronic devices such as smartphones, tablets and wearable devices, making them more lightweight and comfortable and improving the user experience.
Secondly, the ultra-thin BGA substrate adopts a high-density layout, providing higher circuit integration and performance. In a limited space, ultra-thin BGA substrates can accommodate more electronic components and connection lines, achieving more complex functions and more powerful performance. This provides a broad space for functional expansion and performance improvement of electronic products, meeting users’ needs for rich functions and high performance.
In addition, the ultra-thin BGA substrate has good electrical properties. Through precise design and manufacturing processes, ultra-thin BGA substrates can achieve stable electrical characteristics, including low power consumption, low signal distortion and high signal-to-noise ratio, ensuring stable operation of electronic products and high-quality signal transmission.
In terms of thermal stability, the ultra-thin BGA substrate uses high-quality materials and advanced heat dissipation design, which can effectively disperse and conduct heat, maintain the normal operating temperature of electronic equipment, and improve the stability and reliability of the system. This is especially important for high-performance equipment and long-running application scenarios, and can effectively prevent performance degradation and failures caused by overheating.
To sum up, ultra-thin BGA substrate has significant advantages in ultra-thin design, high-density layout, electrical performance, thermal stability and reliability, etc., making it outstanding in various complex applications and becoming a popular choice for modern electronics. An indispensable and critical component of the product. With the continuous development of technology and the expansion of application scope, ultra-thin BGA substrates will continue to play an important role in promoting the continuous progress and innovation of the electronics industry.
FAQ
What are the considerations in material selection for ultra-thin BGA substrates?
The material selection of ultra-thin BGA substrate is crucial because the material properties directly affect its performance and stability. Considerations include the material’s thermal stability, mechanical strength, electrical properties and compatibility with other components. Commonly used materials include polyimide (PI) and fiberglass reinforced epoxy resin (FR4).
What are the special requirements for the welding process of ultra-thin BGA substrate?
Due to the design characteristics of ultra-thin BGA substrates, the welding process requires higher precision and control. The temperature and time during the soldering process require precise control to avoid damage or failure to the substrate and solder joints.
How to deal with thermal management of ultra-thin BGA substrate?
Due to the compact design of ultra-thin BGA substrates, thermal management is an important consideration. Effective thermal design can be achieved by adding a thermal layer to the substrate, optimizing the layout, and selecting appropriate thermal materials. In addition, considering high-power applications, substrate materials with better thermal conductivity can also be considered.
How to ensure the reliability of ultra-thin BGA substrate?
The reliability of ultra-thin BGA substrates is closely related to its manufacturing quality. Precise manufacturing processes, strict quality control and reasonable design are key factors to ensure the reliability of ultra-thin BGA substrates. Taking factors such as environmental conditions, stress distribution, and life testing into account during the design phase are also important measures to ensure reliability.
How to control the cost of ultra-thin BGA substrate?
Although the design and manufacturing process of ultra-thin BGA substrates is relatively complex, costs can be effectively controlled by optimizing design, improving production efficiency, and rationally selecting materials. In addition, establishing good cooperative relationships with suppliers, conducting bulk purchases, and conducting timely cost analysis are also important means to reduce costs.