Ultrathin IC Package Substrates Manufacturer.An ultrathin IC package substrates manufacturer specializes in creating extremely thin, high-performance substrates used in integrated circuit packaging. These advanced substrates support miniaturization and enhanced functionality in electronic devices, providing crucial connectivity and reliability. The manufacturer employs cutting-edge technology and precision engineering to meet the demanding requirements of the semiconductor industry, ensuring optimal performance and efficiency in a variety of applications.
Ultrathin IC package substrates (Ultrathin IC Package Substrates) are one of the focuses of electronic equipment design. As electronic products increasingly pursue thinner, lighter and higher performance, they are gradually emerging. These substrates not only make modern electronic devices lighter, they also provide greater flexibility and reliability while maintaining performance. Their emergence has brought new possibilities to the design of electronic products and promoted the development of electronic products in the direction of thinner, lighter and higher performance. With the continuous advancement of technology, ultra-thin IC packaging substrates will become an indispensable key component in the design of electronic equipment, opening a new chapter for future electronic equipment design.
What are Ultrathin IC Package Substrates?
Ultra-thin IC packaging substrate is a specially designed printed circuit board (PCB) whose thickness is usually between tens to hundreds of microns. Compared with traditional PCB, ultra-thin IC packaging substrate is thinner and lighter, but still has good electrical performance and mechanical strength. This substrate is commonly used in high-end electronic devices such as smartphones, tablets, and portable electronics.
In today’s electronic product market, consumers’ consistent pursuit of products that are light, thin, and short is their pursuit. Ultra-thin IC packaging substrates are a key part of electronic device design, allowing devices to be thinner, lighter and more portable without losing performance. Its specially designed thickness makes it shine in a variety of high-tech applications.
First of all, the thickness of ultra-thin IC packaging substrates is usually between tens to hundreds of microns, which is much thinner than the thickness of traditional PCBs. This ultra-thin design allows electronic devices to become lighter and easier to carry and use while maintaining performance. Especially for portable devices such as smartphones, ultra-thin IC packaging substrates can provide them with more design space, making the overall device more fashionable and portable.
Secondly, despite being ultra-thin, ultra-thin IC packaging substrates still maintain good electrical performance and mechanical strength. High-performance materials and advanced process technology are used in the design and manufacturing process to ensure the stability and reliability of the substrate. This enables ultra-thin IC packaging substrates to meet the performance and reliability requirements of high-end electronic devices, not only enabling complex functions but also providing a long-lasting use experience.
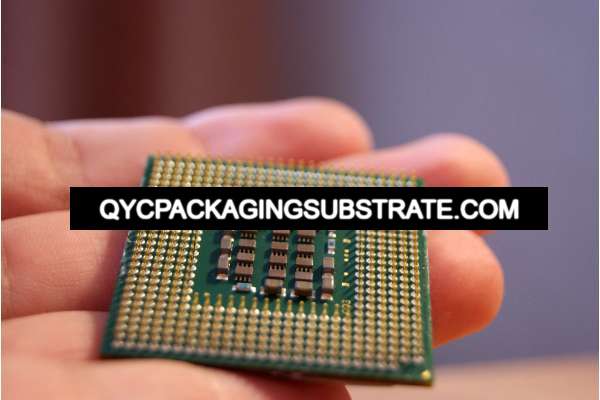
Ultrathin IC Package Substrates Manufacturer
Finally, ultra-thin IC packaging substrates are widely used in various high-end electronic devices. From smartphones to tablets, from wearable devices to medical devices, ultra-thin IC packaging substrates play an important role. They provide the possibility of thin and light design for these devices, promoting the development of electronic products in a more portable and fashionable direction.
In general, the emergence of ultra-thin IC packaging substrates not only makes the design of electronic devices more flexible and diverse, but also brings consumers a more convenient and efficient use experience. With the continuous development and innovation of technology, it is believed that ultra-thin IC packaging substrates will play an increasingly important role in future electronic device design and become a key component of electronic products.
Ultrathin IC Package Substrates design Reference Guide.
The design of ultrathin IC package substrates (Ultrathin IC Package Substrates) is a crucial part of electronic equipment manufacturing. Good design can ensure that the substrate is thin and light while maintaining stable electrical performance and mechanical strength. The following are key factors to consider when designing ultra-thin IC packaging substrates:
Design planning
Before starting the design, the overall requirements and functionality of the circuit need to be clear. Considering the application scenarios of ultra-thin IC packaging substrates, such as smartphones, tablets, etc., design planning should focus on lightweight and compactness.
Material selection
Choosing the right materials is critical to the performance of ultra-thin IC packaging substrates. Common materials include polyimide (PI) and polytetrafluoroethylene (PTFE), which have excellent high temperature resistance and mechanical strength and are suitable for the design of ultra-thin substrates.
Component layout
On ultra-thin IC packaging substrates, component layout is critical. A reasonable layout can not only optimize the performance of the circuit, but also improve the integration of on-board components, reduce the board area, and achieve a thinner and lighter design.
Signal integrity
When routing and connecting components, special attention needs to be paid to maintaining good signal integrity. Using appropriate wiring techniques and stack-up design can minimize signal interference and crosstalk and ensure circuit stability and reliability.
Thermal management
Due to the thin thickness of ultra-thin IC packaging substrates, thermal management is an important design consideration. Reasonable heat dissipation design and thermal conduction path planning can effectively improve the heat dissipation efficiency of the circuit and ensure long-term stable operation of the equipment.
Check and verify
After the design is completed, be sure to conduct strict Design Rule Checks (DRC) and Electrical Rules Checks (ERC). Through these inspections, potential design problems can be discovered and repaired in a timely manner to ensure that the design complies with code requirements.
Generate Gerber files
Finally, Gerber files and drilling files suitable for manufacturing are generated. Ensure documentation is accurate and communicate fully with manufacturers to ensure the manufacturing process runs smoothly.
Through the above design reference guide, you can better plan and implement the design of ultra-thin IC packaging substrates, providing a solid foundation for thinner, lighter and higher-performance electronic devices.
What material is used in Ultrathin IC Package Substrates?
The material selection of ultra-thin IC packaging substrate is crucial and directly affects its performance and application range. Usually, ultra-thin IC packaging substrates use some special high-performance materials to meet the requirements for thinness, high-density wiring and good electrical performance.
Polyimide (PI) is a common ultra-thin IC packaging substrate material. It has excellent mechanical strength and thermal stability, allowing it to maintain stable performance over a wide temperature range. PI materials also have good electrical insulation properties and chemical stability, and are suitable for the manufacturing of high-density, high-speed circuits.
In addition to polyimide, polytetrafluoroethylene (PTFE) is also a commonly used ultra-thin IC packaging substrate material. PTFE has a low dielectric constant and low dielectric loss, making it excellent in high-frequency applications. At the same time, PTFE material also has excellent high temperature resistance and chemical stability, and is suitable for use in electronic equipment requiring high frequency and high temperature environments.
In addition, flexible substrates are also one of the important materials for ultra-thin IC packaging substrates. Flexible substrates usually use polyimide or polyester films, which are highly flexible and bendable and can adapt to complex mechanical structures and shapes. They are commonly used in electronic devices that need to be bent or folded.
In general, the material selection of ultra-thin IC packaging substrates needs to comprehensively consider its requirements in terms of thin and light design, electrical performance and reliability. Different application scenarios may require different material combinations to achieve optimal performance and reliability. With the continuous development of technology, it is believed that there will be more applications of new materials in the future, promoting further innovation and development of ultra-thin IC packaging substrates in electronic device design.
What size are Ultrathin IC Package Substrates?
Ultrathin IC Package Substrates play an increasingly important role in the design of electronic devices. Their sizes vary depending on application requirements, and they have a certain degree of flexibility and customization. These substrates are often extremely thin in thickness, but can be adjusted in length and width to meet specific design requirements.
Generally speaking, the size range of ultra-thin IC packaging substrates is relatively wide, ranging from a few millimeters to tens of centimeters. For mobile devices and portable electronic products, such as smartphones, tablets, etc., smaller size ultra-thin IC packaging substrates are usually required to adapt to the compact design and light portability requirements of the device. These substrates may have lengths and widths ranging from tens of millimeters to a hundred millimeters, while maintaining extremely thin thickness to ensure a thin and light design of the device.
For some applications such as industrial equipment and medical devices, larger ultra-thin IC packaging substrates may be required to accommodate more electronic components and complex circuit designs. The size of these substrates may reach tens of centimeters or more, but still maintain a thin thickness to meet the device’s space constraints and lightweight design requirements.
It should be noted that the size of ultra-thin IC packaging substrate is not only affected by application requirements, but also limited by the manufacturing process. When designing ultra-thin IC packaging substrates, the mechanical strength of the material, cost-effectiveness, and feasibility of the manufacturing process need to be taken into consideration to ensure that the final product not only meets the design requirements but also has good manufacturability and reliability.
In general, the size of ultra-thin IC packaging substrates is determined according to specific application needs and design requirements. While maintaining extreme thinness, the length and width can be flexibly adjusted to meet the design and functional requirements of different devices.
The Manufacturer Process of Ultrathin IC Package Substrates.
The manufacturing process of ultra-thin IC packaging substrates is a precise and complex project that requires superb technology and advanced equipment. The manufacturing process of ultra-thin IC packaging substrates will be introduced in detail below.
First, the manufacturing process begins with the selection of materials. Ultra-thin IC packaging substrates usually use high-performance plastic materials such as polyimide (PI) or polytetrafluoroethylene (PTFE). These materials have excellent thermal properties, mechanical strength and chemical stability, making them ideal for manufacturing ultra-thin circuit boards.
Next is the preparation of the processing technology. Advanced micro-machining technology is applied in the manufacturing process of ultra-thin IC packaging substrates. These include laser cutting, chemical etching and other processes to ensure the flatness and dimensional accuracy of the substrate. These processing techniques not only enable substrates to be made very thin, but also maintain their structural stability and reliability.
This is followed by pattern transfer and circuit production. The circuit pattern is transferred to the substrate surface through sophisticated pattern transfer technology. This requires the use of photolithography and chemical etching processes to ensure that the circuit pattern is accurately transferred to the substrate and maintains its integrity and accuracy.
This is followed by metallization and surface treatment. After the circuit pattern is completed, the substrate needs to be metallized, usually using a nickel-metalization process or other metallization processes, to increase its conductivity and corrosion resistance. At the same time, solder mask and silk screen layers may also be applied to the surface of the substrate to protect the circuit and provide better appearance and identification.
Finally comes testing and inspection. At the final stage of the manufacturing process, ultra-thin IC packaging substrates require rigorous testing and inspection to ensure that their quality and performance meet design requirements. This includes electrical testing, visual inspection and dimensional measurements to ensure each substrate meets high standards of quality.
Through the above manufacturing process, ultra-thin IC packaging substrates can be produced, providing reliable support for the thinning and high-performance of modern electronic devices.
The Application area of Ultrathin IC Package Substrates.
Ultra-thin IC packaging substrates are widely used in the field of electronic equipment. Its thinness, lightness and high performance have brought revolutionary changes to product design in many fields. The following is the application range of ultra-thin IC packaging substrates in smartphones, wearable devices and medical devices:
Smartphones and Tablets
Ultra-thin IC packaging substrates provide important support for the design of smartphones and tablets. As these devices increasingly focus on thinness, lightness and portability, ultra-thin IC packaging substrates have become a necessary component. Its thin and light design makes the device lighter and improves the user’s carrying comfort. It also provides more space for the internal layout of the device, allowing designers to arrange components and circuits more freely, thus improving the overall performance of the device. and reliability.
Wearable device
With the rapid development of wearable technology, ultra-thin IC packaging substrates also play an important role in wearable devices. For example, products such as smart watches, smart glasses, and health monitors all need to integrate as many functions and sensors as possible within a limited space. The thin and light design of ultra-thin IC packaging substrates makes these devices more comfortable and lightweight, without placing unnecessary burden on users, while also ensuring the performance and functional integrity of the devices.
Medical instruments
In the field of medical devices, ultra-thin IC packaging substrates are increasingly used. For example, blood glucose meters, heart rate monitors, portable medical imaging equipment, etc. all need to be lightweight, portable and high-performance to meet the needs of medical staff and patients. Ultra-thin IC packaging substrates can realize miniaturization and portability of medical equipment, making medical monitoring more convenient, while also reducing the cost of equipment and improving the utilization efficiency of medical resources.
In summary, the application of ultra-thin IC packaging substrates in fields such as smartphones, wearable devices, and medical devices not only meets the needs for thinner, lighter, and higher-performance products, but also provides a broader scope for product innovation and development. space. With the continuous advancement of technology and the continuous expansion of application scenarios, ultra-thin IC packaging substrates will continue to play an important role in the field of electronic equipment, promoting the progress and development of the industry.
What are the advantages of Ultrathin IC Package Substrates?
Ultra-thin IC packaging substrates have many advantages over traditional PCBs. These advantages not only make electronic devices more portable and efficient, but also improve the overall user experience. The following are several significant advantages of ultra-thin IC packaging substrates:
Thin and light design
One of the distinctive features of ultra-thin IC packaging substrates is their thin and lightweight design. Due to the use of advanced materials and manufacturing processes, these substrates are lighter than traditional PCBs and can significantly reduce the weight of electronic devices. This thin and light design not only makes the device more portable and convenient for users to carry around, but also improves the appearance and aesthetics of the device to a certain extent.
High performance
Despite their thin thickness, ultra-thin IC packaging substrates are still able to provide excellent electrical performance and signal transmission characteristics. Through advanced material selection and process control, these substrates ensure stable signal transmission and good circuit connections, thereby ensuring high-performance operation of the device. Whether it is data transmission or power consumption control, ultra-thin IC packaging substrates can meet high-demand application scenarios.
Flexibility
The design flexibility of ultra-thin IC packaging substrates is another outstanding advantage. Thanks to advanced manufacturing processes, these substrates can be designed into various shapes and sizes to meet the design needs of different electronic devices. Whether it is bending, folding or complex curved surfaces, ultra-thin IC packaging substrates can be flexibly adapted to provide more possibilities for device design.
Reliability
After professional design and manufacturing processes, ultra-thin IC packaging substrates have high reliability and durability. These substrates undergo strict quality control and testing and are capable of stable operation in various harsh environments. Whether in high temperature, high humidity, high pressure or vibration environments, ultra-thin IC packaging substrates can maintain stable electrical performance and ensure stable operation of the equipment for a long time.
In summary, ultra-thin IC packaging substrates have become an indispensable key technology in the design of modern electronic equipment due to their many advantages such as thin and light design, high performance, flexibility and reliability, providing a basis for making electronic products lighter and more efficient. It also provides strong support for the development of electronic equipment in the future and opens up a broader space for the development of electronic equipment in the future.
FAQ
What is an ultra-thin IC packaging substrate?
Ultra-thin IC packaging substrate is a specially designed printed circuit board (PCB) whose thickness is usually between tens to hundreds of microns. Compared with traditional PCBs, this substrate is thinner and lighter, but still has excellent electrical properties and mechanical strength, and is widely used in smartphones, tablets and other portable electronic devices.
What materials does ultra-thin IC packaging substrate consist of?
Common ultra-thin IC packaging substrate materials include high-performance plastics such as polyimide (PI), polytetrafluoroethylene (PTFE), and other thin composite materials. These materials have excellent electrical insulation properties, heat resistance and mechanical strength, ensuring that the substrate can still work stably under extreme conditions.
What are the main manufacturing processes for ultra-thin IC packaging substrates?
Manufacturing ultra-thin IC packaging substrates requires the use of advanced microfabrication technologies, including laser cutting, chemical etching and lamination processes. Laser cutting ensures high-precision shape processing, while chemical etching is used for detailed circuit patterning. The lamination process stacks multiple thin layers of materials to form the final ultra-thin substrate structure.
What are the manufacturing costs of ultra-thin IC packaging substrates?
The manufacturing cost of ultra-thin IC packaging substrates is usually slightly higher than that of traditional PCBs, but as the production process matures and large-scale production advances, its costs will gradually decrease. Many high-end electronics manufacturers believe this additional cost is worth it, given its unique advantages in performance and design.