Ultrathin LED PCB Manufacturer. We can produce 2 layer Ultrathin hard PCB thickness with 3MIL(75um), 4mil(100um), 5mil(127um). if you want do make 4 layer Ultrathin hard PCB,the finished thickness will be about 7mil or 8mil.We will produce PCB according to the thickness you require.
In today’s digital world, the manufacturing of Ultrathin LED Ultrathin LED PCB (Printed Circuit Board) is becoming increasingly important. These Ultrathin LED PCBs are at the core of many innovative technologies, such as LED lighting and electronic devices. With the continuous development of LED technology and the expansion of application scope, the demand for Ultrathin LED Ultrathin LED PCB with high performance, thinness and excellent thermal conductivity is also growing. This article will take you deep into the world of Ultrathin LED Ultrathin LED PCB manufacturers, from basic concepts to manufacturing processes, to applications and benefits, to unveil this key technology area.
What is Ultrathin LED PCB?
Ultrathin LED PCBs are an essential part of the modern LED lighting industry, providing lighting designers and manufacturers with endless possibilities for innovation. These specially designed printed circuit boards (PCBs) are carefully manufactured to enable lighter and thinner LED lighting solutions. Compared with traditional PCBs, Ultrathin LED PCBs are not only more compact in size, but also have significant advantages in thermal conductivity and electrical characteristics.
Thin design and lightweight construction
One of the key features of Ultrathin LED PCB is its extremely thin design. This thin structure makes LED lighting equipment more portable and enables flexible installation and layout in more application scenarios. Whether it is indoor lighting, outdoor landscape lighting or automotive lighting, Ultrathin LED PCB can meet designers’ needs for lightweight and provide products with higher portability and aesthetics.
Excellent thermal conductivity
In LED lighting applications, thermal management is a crucial consideration. Ultrathin LED PCB uses high-quality thermally conductive materials and designs to effectively conduct and disperse the heat generated by the LED, thereby extending the life of the LED and improving performance stability. This excellent thermal conductivity not only ensures that the LED maintains a stable operating temperature during long-term use, but also reduces the heat loss of the lighting system and improves energy efficiency.
Excellent electrical characteristics
In addition to thermal conductivity properties, Ultrathin LED PCB also has excellent electrical properties, providing a reliable foundation for the stable operation of LED lighting systems. Through precise circuit design and high-quality material selection, they ensure stable and reliable electrical connections between LED modules while minimizing line impedance and signal attenuation.
Industry preferred choice
Due to its superior design and performance features, Ultrathin LED PCB has become the preferred choice in the LED lighting industry. Whether for home lighting, commercial lighting, or industrial lighting, manufacturers can rely on these advanced PCB solutions to achieve innovative design and high-efficiency output of luminaires.
In the ever-evolving LED lighting market, Ultrathin LED PCB has shown its unlimited potential and broad application prospects. As one of the key driving forces of LED lighting technology, they bring more flexible and sustainable solutions to future lighting designs. As technology continues to advance and the market continues to develop, we can look forward to seeing more innovations and breakthroughs, bringing new miracles to the LED lighting industry.
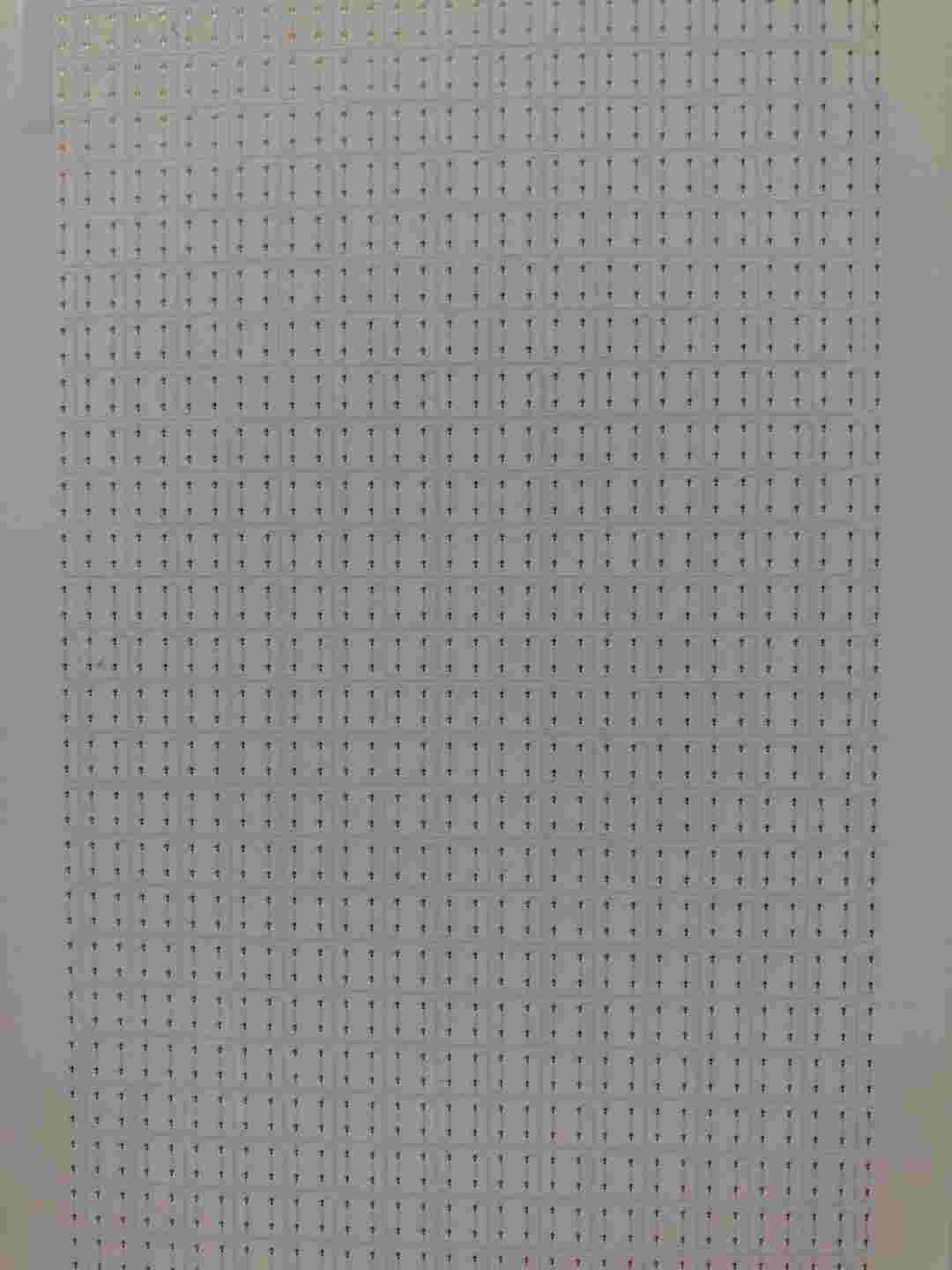
Ultrathin LED PCB
Ultrathin LED PCB design Reference Guide.
The design of Ultrathin LED PCB is crucial, as it directly affects the performance and reliability of LED lighting products. When designing Ultrathin LED PCB, there are several key factors to consider, including layout, thermal conductivity, electrical characteristics, and mechanical strength. Here are some key factors that should be considered when designing Ultrathin LED PCB:
Layout design
When designing Ultrathin LED PCB, layout design is a crucial step. Good layout design can optimize PCB performance and stability to the greatest extent. First of all, the location and connection method of LED devices need to be reasonably arranged to ensure even distribution of light sources and maximize the use of PCB space. Secondly, power and signal lines need to be properly arranged to minimize electromagnetic interference (EMI) and ensure the stability of signal transmission.
Thermal design
Since LED devices generate a large amount of heat during operation, thermal conductivity design is crucial for Ultrathin LED PCB. The use of high thermal conductivity materials and reasonable heat dissipation structures should be considered in the design to effectively transfer heat from the LED device to the PCB surface and dissipate the heat to the surrounding environment through a heat sink or heat sink. In addition, special materials such as metal substrates or aluminum substrates can also be used to improve the thermal conductivity of PCBs.
Electrical Characteristics Design
When designing Ultrathin LED PCB, electrical characteristics need to be considered, including resistance, capacitance, inductance and signal transmission. Proper selection of materials and layout can minimize electrical losses and ensure the stability and reliability of signal transmission. In addition, electrical features such as circuit protection and overload protection should also be considered to ensure the safety and stability of the LED lighting system.
Mechanical strength design
Ultrathin LED PCB usually needs to be used in complex environments, so mechanical strength design is also crucial. The thickness, material and structure of the PCB should be considered in the design to ensure that it has sufficient mechanical strength and vibration resistance to withstand the influence of the external environment and maintain long-term stable operation.
To sum up, designing Ultrathin LED PCB is a complex and important task that requires comprehensive consideration of factors such as layout, thermal conductivity, electrical characteristics, and mechanical strength. Only by fully considering these factors during the design process and selecting appropriate materials and technologies can we design a high-performance, high-reliability Ultrathin LED PCB to meet the needs and requirements of LED lighting products.
What material is used in Ultrathin LED PCB?
The design and manufacturing of Ultrathin LED PCBs (Printed Circuit Boards) requires the use of a range of high-performance materials to ensure their reliability and performance in LED lighting systems. The following are common key materials:
FR-4
FR-4 is a glass fiber reinforced epoxy resin material and one of the most commonly used substrates in PCB manufacturing. It has excellent insulation properties, mechanical strength and heat resistance and is suitable for applications in a variety of environmental conditions. In Ultrathin LED PCB manufacturing, FR-4 is often used as a substrate material to provide good mechanical support and electrical isolation for the PCB.
Metal substrate
A metal substrate is a PCB with a metal substrate, usually an aluminum substrate or a copper substrate. These substrates have excellent thermal conductivity and can effectively dissipate heat, reduce the operating temperature of the LED lighting system, and improve its performance and life. Aluminum substrates are often used in scenarios that require lightweight design, while copper substrates are more suitable for situations that require higher thermal conductivity.
Special thermal conductive materials
In addition to substrate materials, Ultrathin LED PCB manufacturing may also use special thermal conductive materials, such as copper foil, aluminum foil or silicone. These materials are used as the thermal conductive layer of the PCB to help effectively conduct the heat generated by the LED to the PCB surface and further dissipate it into the surrounding environment. This helps keep the operating temperature of the LED components within a safe range and prevents overheating damage.
The performance and reliability of Ultrathin LED PCBs are directly affected by the materials used in the manufacturing process. Selecting appropriate materials can ensure that the PCB has good thermal conductivity and mechanical strength to meet the requirements of the LED lighting system. Therefore, when choosing an Ultrathin LED PCB manufacturer, it is important to pay attention to its material selection and manufacturing process to ensure the quality and performance of the final product.
The selection and application of these key materials provide a solid foundation for the design and manufacturing of Ultrathin LED PCB, making it an important part of the LED lighting industry.
What size are Ultrathin LED PCB?
In the world of LED lighting technology, size is not just a number, but directly affects the performance, functionality and application range of the product. For Ultrathin LED PCB (Printed Circuit Board), size is one of the crucial factors. These PCBs are often used in compact LED lighting devices such as LED lamps, light strips, backlight modules, etc., so their size must fit perfectly with the shape and size of the device.
Generally speaking, the design of LED lighting equipment needs to take into account space constraints, so Ultrathin LED PCBs usually need to be smaller and thinner. When manufacturers design and produce Ultrathin LED PCB, they will customize the size of the PCB according to the specific requirements of customers. This means that customers can require PCBs to have specific lengths, widths and thicknesses based on their product’s design needs and application scenarios to ensure optimal performance and fit.
One of the main benefits of custom PCB sizing is the ability to ensure a perfect match between the PCB and other components. In LED lighting equipment, PCB usually needs to be closely integrated with LED chips, heat sinks, lenses and other components to achieve good heat dissipation and optical performance. By customizing the dimensions, manufacturers can ensure optimal spacing and connections between the PCB and other components, thereby improving overall system performance and reliability.
In addition, customizing the PCB size can also increase product flexibility and customizability. Different LED lighting applications may require PCBs of different shapes and sizes to meet different design needs and installation spaces. Manufacturers can adjust the PCB size and layout according to customer requirements to achieve the best design effect and provide customized solutions.
To sum up, the size of Ultrathin LED PCB is an important issue that manufacturers and customers are concerned about. By customizing the size, you can ensure a perfect fit between the PCB and the LED lighting equipment, improving the performance, functionality and reliability of the product to meet the needs of different application scenarios. When choosing an Ultrathin LED PCB manufacturer, customers should value the manufacturer’s customization capabilities and technical strength to ensure the best solution.
The Manufacturer Process of Ultrathin LED PCB.
The manufacturing process of Ultrathin LED PCB is a precise and complex process that requires multiple critical steps to ensure the quality and performance of the final product. Each step is detailed below:
Design
The first step in manufacturing Ultrathin LED PCB is to design it. Design engineers use CAD (computer-aided design) software to create the layout of the PCB, including wire routing, the location and connections of electrical components, etc. During the design process, factors such as the size, layer, and thermal conductivity of the PCB must be taken into consideration to ensure that the final PCB can meet the requirements of the LED lighting system.
Printing
After the design is completed, the PCB layout will be printed onto the substrate. Wire routes are usually chemically printed onto a fiberglass substrate (FR-4) or a metal substrate to form the desired circuit. The printing process requires precise control of temperature, pressure and time to ensure the quality and accuracy of printed circuits.
Plating
After printing is completed, the PCB needs to go through a plating process to increase the thickness and corrosion resistance of the metal wires. This usually involves immersing the PCB in a solution containing metal ions and applying an electric current, causing the metal ions to deposit a uniformly thick metal coating on the wires.
Drilling
Drilling holes in PCBs are used to mount electronic components and connect wire routes at different levels. The drilling process requires precise control of hole diameter and location to ensure component installation and connection accuracy. Modern PCB manufacturing often uses laser drilling technology, which allows for greater precision and efficiency.
Assemble
After drilling is completed, the PCB will be assembled into the final LED lighting product. This includes installing LED chips, capacitors, resistors and other necessary electronic components, as well as connecting external power and control circuits. The assembly process requires a high degree of precision and expertise to ensure that each component is installed correctly and the circuits are connected correctly.
Test
The last critical step is rigorous testing of the manufactured PCB. Testing usually includes electrical testing, functional testing and reliability testing. Manufacturers use advanced testing equipment and technology to ensure each PCB meets industry standards and customer requirements. Only PCBs that pass the test can be considered as qualified products and can be delivered to customers for use.
The manufacturing process of Ultrathin LED PCB is a complex and precise process that requires the precise execution of multiple critical steps. Manufacturers utilize advanced production equipment and technology to ensure the quality and stability of PCBs, and strictly implement quality control standards to ensure that the final product can meet industry standards and customer needs.
The Application area of Ultrathin LED PCB.
Ultrathin LED PCB (Printed Circuit Board), as a key component, has a wide range of applications in the field of LED lighting. Their design flexibility and high performance make them ideal for a variety of LED lighting products, covering multiple industries and application scenarios.
Indoor lighting
In terms of indoor lighting, Ultrathin LED PCB’s thin design and high-efficiency features make them the first choice for indoor lighting fixtures. Whether it is home lighting, commercial office spaces or public buildings, Ultrathin LED PCB can provide uniform and soft light while being energy-saving and durable.
Outdoor lighting
In outdoor environments, LED lighting needs to withstand harsher climatic conditions and environmental impacts. The high degree of weather resistance and water resistance of Ultrathin LED PCBs makes them ideal for outdoor lighting products such as street lights, landscape lighting, and security lighting. Their stability and long life allow them to perform well in a variety of outdoor applications.
Automotive lighting
With the continuous development of automotive technology, LED lighting is increasingly used in automotive lighting systems. Ultrathin LED PCB can be designed into various shapes and sizes to accommodate the complex structure and space constraints of automotive lamps. They provide bright, energy-saving automotive headlights, rear lights, turn signals and interior lighting, improving driving safety and comfort.
Display
LED display screens have become an important means of displaying information in various occasions, such as indoor and outdoor billboards, conference displays, stage backgrounds, etc. The high degree of integration and flexible design of Ultrathin LED PCBs makes them a key component of LED displays. They provide high-resolution, high-brightness and high-contrast displays that attract the eye and convey information.
Backlight module
LCD displays and panels require backlight modules to provide light sources to display clear images and text. As the core component of the backlight module, Ultrathin LED PCB can provide uniform backlight and ensure high-quality display effects of the monitor. Its ultra-thin design and high-efficiency features make products such as LCD TVs, computer monitors, and mobile device screens thinner, lighter, and more energy-efficient.
To sum up, Ultrathin LED PCB plays a key role in various LED lighting products, including indoor lighting, outdoor lighting, automotive lighting, display screens and backlight modules. Their high performance and reliability make them the first choice in many industries, driving the continuous innovation and development of LED technology.
What are the advantages of Ultrathin LED PCB?
Ultrathin LED PCB (Printed Circuit Board) has attracted much attention in today’s LED lighting field, and its unique advantages make it an ideal choice for many applications. Ultrathin LED PCB has many advantages compared to traditional LED PCB, which we will explore in detail below.
First of all, Ultrathin LED PCB is lighter and thinner than traditional LED PCB. This thin and light design allows them to be easily integrated into a variety of compact LED lighting fixtures, saving space and improving the overall performance of the product.
Secondly, Ultrathin LED PCB has higher thermal conductivity. LED lighting systems have strict heat dissipation requirements, and the special materials and designs used in Ultrathin LED PCB can effectively conduct heat to the surrounding environment, maintain the stable operating temperature of the LED, extend its life and improve performance.
In addition, Ultrathin LED PCB has better electrical characteristics, including lower resistance, better signal transmission and higher circuit stability. These characteristics ensure that LED lighting systems can work in a reliable and stable manner while reducing energy consumption and maintenance costs.
In addition, Ultrathin LED PCB can also provide higher integration and more flexible design options. Manufacturers can customize the shape, size and layout of PCBs according to customer requirements to meet the needs of different application scenarios. This flexibility makes Ultrathin LED PCB suitable for a variety of LED lighting products, from indoor lighting to automotive lighting, from display screens to backlight modules.
In summary, Ultrathin LED PCB has obvious advantages in terms of thin and light design, high thermal conductivity, superior electrical characteristics, and flexible design options, making it the preferred solution in the field of LED lighting. As LED technology continues to develop and its application scope expands, Ultrathin LED PCB will continue to play its important role in promoting progress and innovation in the LED lighting industry.
FAQ
How to ensure the quality of Ultrathin LED PCB?
Manufacturers typically implement strict quality control measures, including raw material inspection, production process control, finished product testing, and final acceptance. In addition, they may also hold relevant quality certifications, such as ISO 9001, to ensure product quality meets standards.
What environmental conditions are Ultrathin LED PCB suitable for?
Ultrathin LED PCB is usually able to adapt to different environmental conditions such as indoor and outdoor as well as high and low temperatures. However, in extreme environments, such as high temperature or high humidity environments, special designs or materials may be required to ensure PCB stability and reliability.
What is the difference between Ultrathin LED PCB and traditional LED PCB?
Ultrathin LED PCB is thinner and lighter than traditional LED PCB, and has higher thermal conductivity and better electrical characteristics. They are often used in applications that have strict requirements on PCB size and weight, such as ultra-thin LED lamps and mobile devices.
What is the maximum size of Ultrathin LED PCB?
The maximum size of Ultrathin LED PCB depends on the manufacturer’s production capacity and customer demand. Generally, manufacturers can customize PCBs in various sizes according to customer requirements to meet different application needs.