Semiconductor Wire Bond Substrate Manufacturer. High speed and high frequency material packaging substrate manufacturing. The base materials will be used with BT base materials, Rogers Base materials, High tg FR4 base, ABF base materials. and other more types base materials.
Wire bond substrates are vital elements within the realm of Printed Circuit Boards (PCBs), serving a crucial function in enabling dependable connections among electronic components. Tailored for accommodating and interlinking diverse elements such as chips, resistors, and capacitors, these substrates leverage wire bonding techniques to establish robust connections. This involves employing metal wires to connect chip pins to electrodes on the substrate, thereby ensuring consistent electrical transmission.
Beyond just facilitating current and signal transmission, Wire Bond Substrates efficiently conduct heat to the substrate, contributing to the maintenance of a stable operating temperature for the connected components. Positioned at the forefront of PCB innovation, these substrates enable seamless electrical connections, serving as a foundational element for the performance and reliability of a broad spectrum of electronic devices.
Whether integrated into consumer electronics, communication equipment, or industrial control systems, Wire Bond Substrates are instrumental in propelling the development and advancement of modern technology. In summary, they are a pivotal PCB component that establishes secure connections between electronic components and the PCB through wire bonding technology, ensuring both reliable electrical and thermal connections for the optimal functionality of diverse electronic devices.
What are the types of Wire Bond Substrates?
Its compatibility with standard packaging and encapsulation techniques further enhances its appeal for various electronic devices.
Gold wire bonding, on the other hand, utilizes gold wire for creating bonds. It offers superior conductivity and stability compared to aluminum wire bonding, making it ideal for applications demanding high performance, especially in compact designs and high-frequency scenarios. This makes gold wire bonding a preferred choice for critical electronic components.
Copper Wire Bonding
Copper wire bonding, a newer variant, utilizes copper wire for bonding. It boasts higher electrical and thermal conductivity compared to aluminum and gold wire bonding. This makes it suitable for applications demanding enhanced electrothermal performance, with added benefits of lower resistance and improved soldering performance, ideal for advanced electronic products.
In summary, Wire Bond Substrates come in various types, each with distinct features catering to different design requirements and industry applications. Understanding the characteristics of each type empowers electronics engineers and designers to select the most suitable substrate for their projects, thereby enhancing electronic product design and manufacturing capabilities.
What are the advantages of Wire Bond Substrates?
Wire Bond Substrates offer notable advantages in the design and manufacture of contemporary electronic devices, contributing significantly to enhanced device performance and reliability. These substrates excel in several key areas, profoundly impacting electronic devices:
Superior Electrical Conductivity
Wire Bond Substrates boast outstanding electrical conductivity, facilitating efficient current transmission and minimizing resistive losses. This feature enables faster and more stable signal transmission within electronic devices, consequently elevating overall device performance.
Effective Thermal Dissipation
Wire Bond Substrates exhibit commendable thermal dissipation properties, efficiently conducting and dispersing heat generated by the device. Particularly crucial for high-power electronic equipment, this attribute aids in reducing operating temperatures, prolonging equipment lifespan, and sustaining consistent performance levels.
By virtue of these qualities, Wire Bond Substrates significantly enhance the functionality and reliability of electronic devices in modern manufacturing processes.
Compatibility with high frequency applications
Wire Bond Substrates have excellent high-frequency characteristics and can maintain stable signal transmission and electrical performance at high frequencies. This makes them ideal for wireless communications, radar systems and other high-frequency applications, providing reliable performance support for devices.
Combining these benefits, Wire Bond Substrates greatly enhance the performance and dependability of electronic devices. They enhance signal transmission speed and stability, lower device temperatures, prolong device lifespan, and excel in high-frequency applications. Consequently, choosing appropriate Wire Bond Substrates is pivotal for designing and manufacturing top-tier electronic devices with exceptional performance and reliability.
Why Choose Wire Bond Substrates?
In today’s rapidly developing electronics field, Wire Bond Substrates, as an advanced PCB technology, shows obvious advantages in signal integrity, miniaturization capabilities and cost-effectiveness, making it the first choice for electronic design. The following is a detailed analysis of the advantages of Wire Bond Substrates over traditional PCBs and applicable scenarios:
Improved signal integrity
Wire Bond Substrates excel in signal integrity. Compared to traditional PCBs, Wire Bond Substrates can better maintain signal stability and accuracy in high-frequency applications. Its excellent conductivity and low transmission losses make it ideal for processing complex signals and data. In scenarios that require high-performance communication and data transmission, Wire Bond Substrates can better meet the system’s signal quality requirements.
Advantages of miniaturization capabilities
Wire Bond Substrates has demonstrated exceptional capabilities in miniaturized designs. Due to the high precision of their manufacturing process, Wire Bond Substrates allow the integration of more components in a limited space, resulting in a compact design of the device. This is a crucial advantage as modern electronic devices increasingly focus on being thin, light and compact. In applications that require miniaturization and lightweight, Wire Bond Substrates are clearly more competitive.
Cost-benefit considerations
From an economic perspective, Wire Bond Substrates also performs well in terms of manufacturing costs and overall cost. Its highly automated production process reduces production costs, while its miniaturized design saves the use of raw materials. At large-scale production, Wire Bond Substrates is better able to achieve economies of scale and thus offer more competitive prices. For cost-effective projects, Wire Bond Substrates is a smart choice.
Wide range of applicable scenarios
The advantages of Wire Bond Substrates are not limited to a specific field, but show broad adaptability in various application scenarios. Whether in communications equipment, automotive electronics, medical equipment or consumer electronics, Wire Bond Substrates provide superior performance and meet the various electronic design requirements of different industries. Their versatility makes Wire Bond Substrates ideal for many projects.
Taken together, the signal integrity, miniaturization capabilities, and cost-effectiveness of Wire Bond Substrates make them a popular choice in today’s electronic designs. While pursuing high performance, miniaturization and economic efficiency, choosing Wire Bond Substrates will provide reliable support for the successful implementation of the project.
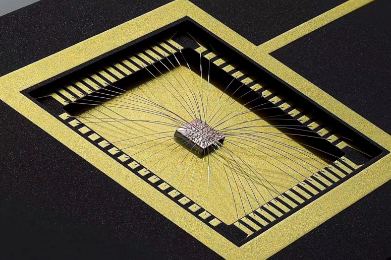
Wire Bond Substrate
How are Wire Bond Substrates made?
The manufacturing process for Wire Bond Substrates is intricate and sophisticated, encompassing several critical steps and advanced technologies to guarantee the quality and performance of the end product. This process involves two primary aspects: substrate manufacturing and bonding technology, both of which are discussed in detail below.
The manufacturing of substrates is the first step in the Wire Bond Substrates manufacturing process, and its quality and characteristics directly affect the performance and stability of the entire product. The following are the main processes of substrate manufacturing:
Manufacturers employ specialized materials like ceramics and laminates to meet diverse application requirements, emphasizing qualities such as mechanical strength, thermal conductivity, and high-temperature resistance. The substrate manufacturing process incorporates precision techniques such as cutting, drilling, and surface treatment to ensure adherence to specified size and surface flatness criteria.
Critical to substrate production is lamination technology for multi-layer boards, wherein different material layers are stacked and firmly bonded through a high-temperature, high-pressure process according to design specifications. The bonding technology, a pivotal step in connecting chips and substrates, significantly influences the quality and stability of electronic components.
Modern Wire Bond Substrate manufacturing processes favor automated bonding procedures for enhanced efficiency and precision. Automation systems facilitate accurate bonding operations, thereby improving both production efficiency and product quality. The selection of appropriate bonding materials, such as aluminum, gold, or copper wire, plays a crucial role during the bonding process. The choice is contingent upon specific application needs, considering varying electrical and thermal conductivity properties associated with each material.
In summary, the Wire Bond Substrate manufacturing process encompasses substrate production and bonding technology. Through meticulous precision processing and the integration of advanced techniques, manufacturers can deliver high-quality, high-performance products tailored to the demands of the electronics industry, thereby supporting its continued development.
What are the application areas for Wire Bond Substrates?
Wire Bond Substrates are integral components in PCB engineering, finding extensive application across various industries. They are notably utilized in telecommunications for producing equipment like routers, switches, and base stations, ensuring robust electrical performance crucial for stable network operations. In aerospace, these substrates are employed in crafting lightweight yet dependable control, communication, and navigation systems for aircraft. Automotive electronics benefit from their ability to withstand extreme conditions, supporting the development of ECUs, driver assistance systems, and in-car entertainment, ensuring the reliability of vehicle electronics. Within medical device manufacturing, Wire Bond Substrates enable the creation of precise and reliable diagnostic, therapeutic, and monitoring equipment essential for healthcare. Moreover, they extend their utility to industrial control, energy management, consumer electronics, and military applications, owing to their versatility and adaptability. In summary, Wire Bond Substrates serve as foundational elements across telecommunications, aerospace, automotive, medical, and various other industries, underpinning the design and production of electronic systems and contributing to the advancement of technology.
Where to find reliable Wire Bond Substrate manufacturers?
When seeking a dependable Wire Bond Substrate manufacturer, selecting a trustworthy supplier is paramount. As your partner, we recognize your exacting standards for suppliers. Here are key considerations in your search:
Quality and Reliability: Give precedence to the manufacturer’s quality control system and proven track record for reliability. This assessment should encompass quality management procedures, inspection tools, testing methodologies, and past project achievements.
As a leading manufacturer of Wire Bond Substrates, we assure you of the following:
Industry Certifications: We possess various industry certifications, including ISO 9001 and ISO 14001, ensuring that our products adhere to global quality standards and environmental management requirements.
Production Capacity: With cutting-edge production facilities, advanced technology, and a skilled team, we can efficiently meet your customized requirements and guarantee timely deliveries.
Quality & Reliability: Our commitment is to deliver Wire Bond Substrates of the highest quality and reliability. Rigorous quality control processes and comprehensive testing ensure that our products consistently meet the highest standards.
Choosing us as your Wire Bond Substrate manufacturer means entrusting your needs to a professional and dependable partner, dedicated to delivering top-notch products and services.
How is the quote for Wire Bond Substrate determined?
When selecting a Wire Bond Substrate, it’s crucial to grasp the key determinants influencing its pricing. The quoted price isn’t solely dictated by factors like substrate material, design intricacy, and production volume needs, but also influenced by market dynamics and the manufacturer’s pricing approach. Below, we delve into these factors to empower readers in their project decisions.
Substrate material stands out as a primary influencer of Wire Bond Substrate quotations. Material choice significantly impacts cost and performance attributes. For instance, opting for a ceramic substrate may incur higher costs compared to selecting a laminate (FR-4); however, ceramics offer superior performance and reliability in high-temperature and high-frequency environments.
The design complexity of Wire Bond Substrate directly affects manufacturing costs. More complex designs usually mean more production steps, more man-hours and higher costs. For example, if the design requires a special stack-up structure or tiny wiring, the production process will be more complex, driving up costs.
The pricing of Wire Bond Substrate is influenced by several factors. Firstly, production volume plays a significant role, with higher volumes generally leading to lower costs per substrate due to spreading fixed costs. Conversely, low-volume production tends to result in higher unit costs as fixed costs are distributed over fewer products. Market dynamics, including supply and demand, also impact prices.Additionally, pricing strategies employed by manufacturers directly influence quotes. Vendors may adopt different pricing models and profit margins, resulting in variations in substrate prices. In summary, the quotation of Wire Bond Substrate is influenced by substrate material, design complexity, production volume, market dynamics, and manufacturer pricing strategies. Understanding these factors helps stakeholders make informed decisions balancing design objectives and cost considerations for their projects.
Frequently Asked Questions
Where can I find reputable Wire Bond Substrate manufacturers?
Reliable Wire Bond Substrate manufacturers can be found through industry directories, trade associations, and online platforms, ensuring adherence to quality standards and efficient production capabilities.
How are Wire Bond Substrate quotes determined?
Wire Bond Substrate quotes vary based on factors such as substrate material, complexity of design, and production volume requirements, with manufacturers providing customized quotes to meet specific project needs.
Where can one find reliable Wire Bond Substrate manufacturers?
Reliable Wire Bond Substrate manufacturers can be found through considerations of industry certifications, production capabilities, and a track record for quality and reliability. Reputable sources and industry networks are valuable in making informed choices.
What factors influence the quotes for Wire Bond Substrates?
Wire Bond Substrate quotes are influenced by factors such as substrate material, design complexity, and production volume requirements. Understanding these factors helps in making cost-effective decisions for specific projects.
Are Wire Bond Substrates compatible with high-frequency applications?
Wire Bond Substrates exhibit excellent compatibility with high-frequency applications. Their design and materials make them suitable for applications where efficient signal transmission and integrity are crucial.
What are the key considerations when selecting Wire Bond Substrates for a project?
Key considerations include the specific requirements of the project, industry standards, and the desired performance characteristics. Collaboration with experienced engineers and manufacturers can aid in making informed decisions.
In conclusion, these FAQs aim to provide clarity on common queries surrounding Wire Bond Substrates. Understanding the intricacies of these substrates is essential for engineers and designers seeking optimal solutions for their electronic design and manufacturing endeavors.