Aluminum Nitride PCB (AlN PCB) manufacturing. We offer ALN ceramic PCBs from 1 layer to 20 layers. or 3D ceramic substrates.
Is the manufacturing of AlN PCB a complex and precise process? Does it require deep expertise and technology? Can we delve into the AlN PCB manufacturing process, and the important topics related to it? The manufacturing of aluminum nitride PCB (AlN PCB) is a complex and precise process that requires in-depth expertise and technology. In the modern electronics industry, AlN PCB has attracted much attention due to its excellent thermal conductivity and high-frequency characteristics. In this article, we will take an in-depth look at the AlN PCB manufacturing process, and the important topics related to it.
What is Aluminum Nitride PCB (AlN PCB)?
Aluminum nitride PCB (AlN PCB) is a special type of printed circuit board (Printed Circuit Board), which is significantly different from traditional glass fiber composite PCB. The base material of AlN PCB is aluminum nitride ceramic, which gives it excellent thermal conductivity and high-frequency characteristics. In contrast, common fiberglass PCBs may have limited performance in high-temperature and high-frequency environments, while AlN PCBs are able to maintain stability under these extreme conditions.
The manufacturing process of aluminum nitride PCB includes selecting high-purity aluminum nitride ceramic powder and forming the substrate through processes such as molding and sintering. Then, a thin layer of copper foil is applied to the surface of the substrate to provide conductivity. Next, photolithography technology is used to transfer the designed circuit pattern to the surface of the copper foil, and chemical etching is used to remove the uncovered portion of the copper foil to form the required circuit pattern. A layer of metal (usually nickel/gold) is deposited over the circuit pattern to protect the copper foil and improve soldering properties. Finally, holes are drilled into the PCB using laser or mechanical drilling techniques, and metal inserts are inserted where necessary to provide connections.
Overall, aluminum nitride PCB is widely used in high power density and high frequency electronic applications due to its unique materials and manufacturing processes. Its excellent performance and stability make AlN PCB an ideal choice for fields such as radio frequency (RF) modules, microwave communications, power amplifiers, etc.
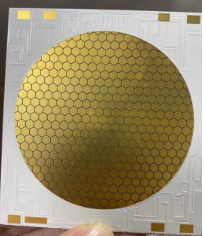
Aluminum Nitride PCB
How to design aluminum nitride PCB (AlN PCB)?
When designing aluminum nitride PCBs, multiple factors need to be considered to ensure the final product has excellent performance and reliability. The key factors in designing aluminum nitride PCBs are detailed below:
Thermal Management: Aluminum nitride PCBs are favored for their excellent thermal conductivity, but effective thermal management still needs to be taken into account during the design process. This includes identifying thermal solutions such as thermal pads, heat sinks or cooling fans to ensure efficient heat transfer away from the PCB in high power density applications.
High-frequency characteristics: Considering the application of aluminum nitride PCB in high-frequency circuits, designers must pay special attention to the optimization of circuit layout and signal transmission paths. Reasonable wiring rules and ground wire design can reduce signal interference and transmission loss, thereby improving the high-frequency performance of the circuit.
Material selection: Choosing the right substrate material is critical for designing aluminum nitride PCBs. In addition to aluminum nitride ceramics as the substrate material, the choice of coated metal layers and other laminate materials also need to be considered to meet the specific requirements of the circuit.
Laminated structure: A proper laminated structure can provide the required electrical performance and mechanical strength. During the design process, the number and sequence of laminates need to be carefully selected and placement of embedded components considered to achieve optimal performance and reliability.
Protection and Encapsulation: When designing an aluminum nitride PCB, the environmental conditions of the circuit and the physical and chemical damage it may suffer need to be taken into consideration. Appropriate protective measures and packaging technology can protect the circuit from external interference and damage and extend the service life of the PCB.
Testing and verification: After the design is completed, rigorous testing and verification must be performed to ensure that the PCB meets specifications and performance requirements. This includes electrical testing, thermal testing, mechanical testing, etc., as well as verification of high-frequency characteristics and thermal performance.
To sum up, designing aluminum nitride PCB requires comprehensive consideration of thermal management, high-frequency characteristics, material selection, laminate structure, protection and packaging, and test verification. Only by fully considering these factors and combining professional knowledge and experience can we design aluminum nitride PCB products with excellent performance, reliability and stability.
What is the manufacturing process of aluminum nitride PCB (AlN PCB)?
As we explore the manufacturing process of Aluminum Nitride PCB (AlN PCB), we will gain an in-depth understanding of its complex and precise process, which covers multiple critical steps to ensure that the performance and quality of the final product are as expected.
As the base material of AlN PCB, aluminum nitride ceramics first need to prepare high-purity AlN ceramic powder. These powders undergo specific shaping and sintering processes to form substrates with the required dimensions and properties. The key to the substrate preparation stage is to ensure that the substrate has a uniform structure and stable performance.
Coat a thin layer of copper foil on the surface of the AlN substrate. The purpose of this step is to provide electrical conductivity so that the AlN PCB can efficiently transmit current and signals.
The designed circuit pattern is transferred to the surface of the copper foil through photolithography technology. This involves covering the copper foil with photosensitive resin or photoresist, which is then exposed and developed to form the desired circuit pattern.
Chemical etching is used to remove the uncovered portion of the copper foil to form the desired circuit pattern. This step leaves only the required wires and connections on the board.
A layer of metal (usually nickel/gold) is deposited over the circuit pattern to protect the copper foil and improve soldering properties. The metallization layer also helps protect the copper foil from environmental corrosion.
Laser or mechanical drilling techniques are used to drill holes into the PCB and metal inserts are inserted where necessary to provide connections. These holes and jacks are important for assembling electronic components and connecting circuits.
Manufactured AlN PCBs are subject to rigorous testing and quality control to ensure they meet specifications and standards. These tests include electrical tests, reliability tests, and thermal performance tests to ensure that AlN PCBs exhibit good performance and reliability in practical applications.
Through these key steps, aluminum nitride PCB (AlN PCB) can be precisely manufactured with excellent thermal conductivity and high-frequency characteristics, making it suitable for various high-performance electronic applications.
How much does aluminum nitride PCB (AlN PCB) cost to manufacture?
do you know? The cost of manufacturing aluminum nitride PCB (AlN PCB) is affected by many factors. When discussing aluminum nitride PCB manufacturing costs, here are key factors to consider:
First, aluminum nitride ceramics are relatively expensive as substrate materials for AlN PCBs. High-purity aluminum nitride ceramic powders are more expensive and require precise control during the molding and sintering processes, which also increases manufacturing costs.
Secondly, the manufacturing process of AlN PCB is relatively complex, involving multiple steps and highly technical production equipment. These steps include substrate preparation, copper foil coating, patterning, etching, metallization, drilling and jacking, etc. Each step requires professional technology and precision equipment support, further increasing manufacturing costs.
In addition, AlN PCB is usually used in high-performance, high-frequency electronic applications, so the requirements for manufacturing processes and quality control are also higher. This means that manufacturers need to invest more manpower, time and resources to ensure that products meet customer requirements and standards, thus increasing manufacturing costs.
In addition, customer customization needs will also affect the manufacturing cost of AlN PCB. Different customers may have different requirements, such as special laminate structures, specific material requirements, or special surface treatments, which can increase manufacturing costs.
In summary, although the manufacturing cost of aluminum nitride PCB is relatively high, its excellent performance and applicability make it of great value in specific fields. For those applications seeking high performance and reliability, the cost of manufacturing an AlN PCB is worth the investment.
What material is aluminum nitride PCB (AlN PCB) made of?
Aluminum nitride PCB (AlN PCB) is a special type of printed circuit board whose material composition is different from traditional FR-4 or other common circuit boards. Understanding the material composition of aluminum nitride PCBs is critical to understanding their superior performance.
First, let’s understand the substrate material of aluminum nitride PCB. Different from traditional glass fiber composite materials, the substrate of aluminum nitride PCB uses aluminum nitride ceramics as the main material. Aluminum nitride ceramics have extremely high thermal conductivity and excellent dimensional stability, making them ideal for high-performance PCBs. This ceramic material conducts heat efficiently, helping to maintain circuit board stability and reliability in high power density and high frequency environments.
In addition to the substrate material, aluminum nitride PCB also involves other important material components. The surface of the aluminum nitride ceramic substrate is often coated with a thin layer of metal, usually copper foil. Copper foil provides the PCB’s electrical conductivity and serves as the basis for the circuit. In addition, in order to protect the copper foil and improve its welding performance, a layer of metal is usually deposited on the surface of the copper foil, most commonly nickel/gold.
In general, the material composition of aluminum nitride PCB includes aluminum nitride ceramic as the substrate material, and surface-coated copper foil and other metal layers. These materials exhibit excellent performance and stability in high-temperature, high-frequency and high-power environments, making aluminum nitride PCBs the first choice for many high-end electronic applications.
With a deeper understanding of the material makeup of aluminum nitride PCBs, we can better understand its importance and advantages in high-performance electronic applications. This combination of material options makes aluminum nitride PCBs ideal for applications targeting high power density and high frequency requirements.
Who makes Aluminum Nitride PCB (AlN PCB)?
In the field of aluminum nitride PCB (AlN PCB) manufacturing, professional PCB manufacturers play a key role. These manufacturers have extensive experience and advanced technical equipment to meet customers’ needs for high-performance PCBs and provide high-quality customized solutions. As you mentioned, the manufacturer may be your company.
Manufacturers of aluminum nitride PCBs usually have professional teams who are well versed in the characteristics, design requirements and manufacturing processes of AlN PCBs. By working closely with customers, manufacturers are able to understand their needs and provide targeted solutions. This includes full support from design consultation to production and manufacturing, to quality control and after-sales service.
As an aluminum nitride PCB manufacturer, the company may have advanced production equipment and processes to ensure the production of high-quality PCB products that meet specifications. In addition, they may continue to invest in R&D and innovation to keep up with the latest trends and technologies in the industry and provide customers with more competitive solutions.
In addition to technical capabilities and production capabilities, the manufacturer’s reputation and service level are also crucial. Excellent manufacturers will uphold the principle of integrity, establish long-term and stable cooperative relationships with customers, and strive to provide customers with excellent service experience.
Overall, as an aluminum nitride PCB manufacturer, the company may be one of the leaders in the industry, providing customers with high-performance, high-quality AlN PCB products through unremitting efforts and continuous innovation, and contributing to customer success and success. development contribution.
What are the five qualities of great customer service?
When it comes to great customer service, there are a few key traits that are essential. These qualities not only ensure customer satisfaction but also help businesses build a good reputation and increase customer loyalty. Here are five key attributes of great customer service:
Great customer service starts with proactive communication. This means not only responding promptly to customer inquiries and questions, but also proactively communicating with customers to understand their needs and expectations. Proactive communication builds trust and makes customers feel like their needs are valued.
Every client is unique, so providing personalized care and solutions is critical. Good customer service should provide customized services based on the customer’s needs and preferences. By understanding a customer’s background, history, and preferences, businesses can better meet customer expectations and build long-term relationships.
Excellent customer service requires staff to have professional knowledge and skills and be able to provide customers with accurate and timely help and advice. From product knowledge to problem-solving skills, professionalism is a key factor in ensuring customer trust and satisfaction.
Businesses need to be flexible and adaptable to different customer needs and situations. Great customer service should be able to be flexible and make changes based on customer feedback and requests. This flexibility is not only reflected during the service process, but also when solving problems and handling complaints.
Continuous improvement is key to ensuring that the quality of customer service continues to improve. Companies should constantly collect customer feedback and make improvements and adjustments based on feedback. Through continuous improvement, companies can better meet customer needs and maintain a competitive advantage.
In conclusion, great customer service is one of the cornerstones of building a successful business. Through proactive communication, personalized care, professionalism and professionalism, flexibility and adaptability, and continuous improvement, businesses can build great customer relationships and achieve long-term business success.
Frequently Asked Questions
What are the key advantages of Aluminum Nitride PCBs (AlN PCBs) compared to traditional PCBs?
Aluminum Nitride PCBs offer several advantages over traditional PCBs. Firstly, they have excellent thermal conductivity properties, making them suitable for high-power applications where heat dissipation is critical. Additionally, AlN PCBs exhibit high-frequency characteristics, making them ideal for use in microwave communication systems and RF modules. Moreover, their robustness and reliability in harsh operating environments make them preferred choices in demanding applications.
How does the cost of manufacturing Aluminum Nitride PCBs (AlN PCBs) compare to traditional PCBs?
Manufacturing Aluminum Nitride PCBs typically incurs higher costs compared to traditional PCBs. This is primarily due to the specialized materials and fabrication processes involved in AlN PCB manufacturing. The high-purity aluminum nitride ceramic substrate and additional processing steps contribute to increased production expenses. However, the superior performance and reliability of AlN PCBs often justify the higher cost, especially in applications requiring exceptional thermal management and high-frequency performance.
Can Aluminum Nitride PCBs (AlN PCBs) be used in consumer electronics applications?
While Aluminum Nitride PCBs offer exceptional thermal conductivity and high-frequency characteristics, they are generally not commonly used in consumer electronics applications due to their higher cost compared to traditional PCBs. Consumer electronics typically prioritize cost-effectiveness and mass production scalability, which may not align with the specialized requirements and higher expenses associated with AlN PCBs. However, in niche consumer products where thermal management and high-frequency performance are critical, AlN PCBs may find limited use.
Are there any limitations or challenges associated with Aluminum Nitride PCBs (AlN PCBs)?
Although Aluminum Nitride PCBs offer superior thermal conductivity and high-frequency performance, they come with certain limitations and challenges. One challenge is the relatively high cost of materials and manufacturing processes compared to traditional PCBs, which may restrict their widespread adoption in cost-sensitive applications. Additionally, AlN PCBs may pose challenges in terms of compatibility with standard assembly processes and the availability of specialized manufacturing facilities equipped for handling ceramic substrates.