Blind Vias&Buried Vias PCB manufacturing. HDI PCBs, Mixed media laminating PCBs Vendor, we offer Blind Vias&Buried Vias PCB from 4 layer to 50 layers. We will produce such PCB according to the material you require.
In PCB (Printed Circuit Board) manufacturing, blind via and buried via technology play a vital role. Blind and buried via technology can help circuit board designs become more compact and efficient, thereby improving their performance and density. This article will delve into the definitions, design principles, and manufacturing processes of these technologies to provide you with a comprehensive guide to help you better understand and apply blind and buried via technology.
What exactly are blind via and buried via technologies?
Blind via and buried via technologies are advanced processes commonly used in PCB (Printed Circuit Board) manufacturing. They provide more possibilities and flexibility for circuit board design and manufacturing. In traditional double-sided or multi-layer PCBs, holes traverse the entire board thickness, while blind via and buried via technologies allow holes to be formed inside the PCB without completely penetrating the entire board thickness. Blind vias only penetrate one surface, while buried vias are completely covered and do not expose the surface.
The importance of these technologies in PCB design is self-evident. First, they can effectively increase the density of circuit boards. By forming holes inside the PCB, designers can use space more efficiently and make the layout of components on the board more compact. This is especially important for miniaturized and lightweight electronic devices, such as smartphones, tablets, and wearable devices.
Secondly, blind hole and buried hole technology can also improve the performance and reliability of PCB. These techniques can improve the speed and stability of signal transmission by reducing wire lengths on the PCB and reducing crosstalk on the circuit board. In addition, blind holes and buried holes can also reduce the surface area of the circuit board and reduce mutual interference between signal lines, thereby improving the anti-interference ability of the entire circuit system.
In addition, blind via and buried via technology can also simplify the wiring and assembly process of circuit boards. Since the holes do not penetrate the entire thickness of the board, working on both sides of the board during routing and soldering can be avoided, which makes assembly easier and more efficient.
To sum up, blind via and buried via technologies play a vital role in PCB design and manufacturing. They can not only improve the density and performance of circuit boards, but also simplify the wiring and assembly process, providing new opportunities for the design and manufacturing of electronic devices. Production offers more possibilities.
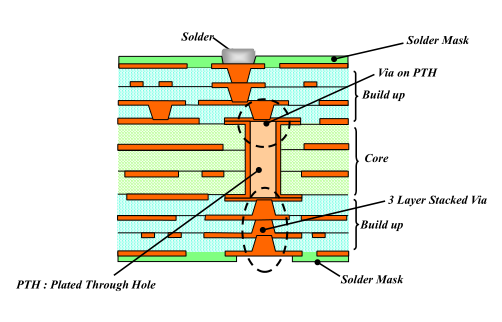
Blind Vias&Buried Vias PCB
How to design a PCB with blind and buried vias?
When designing a PCB with blind and buried vias, there are some key design principles and points to consider. The application of blind via and buried via technology in PCB design aims to improve the density and performance of the circuit board, so every detail in the design process is crucial.
First, let us understand the concepts of blind vias and buried vias. Blind holes are drilled on one side of the PCB surface, but do not completely penetrate the entire board thickness; buried holes are located inside the PCB and are completely covered in the interlayer medium.
When designing PCBs with blind and buried vias, here are some important design principles and points:
Selection of stacked layer thickness: Blind vias and buried vias are commonly used in multi-layer PCB designs. When choosing layer thicknesses, you need to ensure enough space to accommodate blind and buried vias while maintaining PCB stability and performance.
Consider signal integrity: The design of blind and buried vias should consider the integrity of signal transmission. Reasonable layout and lead length can reduce signal attenuation and crosstalk, and improve the performance and stability of the circuit board.
Consider thermal management: In PCB design, especially in high-density PCBs, thermal management must also be considered in the design of blind and buried vias. Through reasonable layout and heat dissipation design, the temperature of the circuit board can be effectively reduced and its working efficiency and reliability can be improved.
Choose the right material: The design of blind and buried vias also needs to consider the selection of materials. Choosing high-quality interlayer dielectric and copper-clad materials can ensure the quality and stability of blind and buried vias, thereby improving the performance of the entire PCB.
Use professional design software: When designing PCBs with blind and buried vias, it is very important to use professional design software. These software usually have rich functions and tools that can help designers accurately layout and design blind and buried vias, ensuring their quality and accuracy.
Conduct appropriate testing and verification: After the design is completed, appropriate testing and verification must be performed to ensure that the design of blind and buried vias meets the expected requirements. Through simulation and actual testing, potential problems can be discovered and solved in time to ensure the quality and stability of PCB.
In summary, designing PCBs with blind and buried vias requires consideration of many factors, including layer thickness selection, signal integrity, thermal management, material selection, design software, and test verification. Only by comprehensively considering these factors can we design PCB products with stable performance and reliable quality.
What is the manufacturing process of blind vias and buried vias?
In PCB (Printed Circuit Board) manufacturing, blind via and buried via technologies are common manufacturing processes, which provide higher density and performance for PCB. The following will provide an overview of the manufacturing process of blind and buried vias and introduce the key steps.
The manufacturing process of blind and buried vias usually includes the following main steps:
Before any drilling begins, the PCB board is surface treated to improve its drilling quality. This may involve surface cleaning, chemical treatment or the application of special coatings to enhance adhesion to the hole walls.
PCB layer alignment is a critical step, especially in multi-layer PCB manufacturing. Precise alignment ensures that blind and buried vias formed between different layers are in the correct location.
Before drilling, optical or mechanical devices are often required to ensure the flatness and stability of the PCB. During the drilling process, a special drill bit is used to drill holes into the PCB board to form the required blind holes or buried holes.
After drilling is completed, the PCB usually needs to be cleaned to remove any remaining chips, dust or oil. The cleaning process can use chemical solvents or aqueous solutions to ensure that the PCB surface is clean.
Before subsequent processes, the PCB surface may need to be specially treated to enhance the adhesion of the hole walls or increase conductivity.
After all manufacturing steps are completed, PCBs usually need to be inspected and verified to ensure that the quality of blind and buried vias meets requirements. This may involve using optical inspection equipment or conducting electrical tests.
In the manufacturing process of blind and buried vias, it is crucial to ensure precision and accuracy at every step. Deviation in any step may lead to quality problems of the PCB board, affecting the performance and reliability of the entire electronic device.
Through the execution of the above key steps, the manufacturing process can ensure that the quality and performance of the PCB board meet the design requirements, thereby meeting the needs of various electronic devices.
Can blind via and buried via technology improve PCB performance and density?
In modern electronic devices, PCB performance and density are critical to overall device performance. As an important step in PCB manufacturing, blind via and buried via technology can indeed significantly improve the performance and density of PCB, and play a key role in reducing the size and weight of circuit boards.
First, let’s explore the advantages of blind via and buried via technology:
Increase PCB density: Blind and buried via technology allows circuit connections to be transferred from one PCB layer to another without going through the entire board thickness. In this way, PCB can achieve higher wiring density, making it possible to accommodate more electronic components and connection lines in a limited space.
Enhance circuit board performance: Through blind hole and buried hole technology, the signal transmission path of the circuit board can be more direct and stable, reducing signal transmission interference and loss, thus improving the performance and reliability of the overall circuit.
Reduce board size and weight: Traditional through-hole connections take up a certain amount of space on the PCB, and will take up more space in multi-layer PCBs. Blind hole and buried hole technology can reduce board thickness, thereby significantly reducing the size and weight of the circuit board while maintaining the same functionality. This is particularly important for thin, light and miniaturized electronic devices.
Through the above advantages, blind via and buried via technology can not only improve the performance and density of PCB, but also meet the needs of modern electronic equipment for miniaturization, lightweight and high performance. Therefore, in PCB design and manufacturing, making full use of blind via and buried via technology will bring significant advantages and competitiveness.
In what fields are blind via and buried via technologies widely used?
In today’s technological field, blind via and buried via technology have become an indispensable part in various fields. Their wide application makes it possible to improve the performance and reduce the size of various electronic devices, mainly involving the following fields:
With the continuous advancement of technology, more and more electronic devices need to accommodate more electronic components in a limited space. Blind hole and buried hole technology can realize the interconnection of multi-layer circuit boards, effectively improving the density and performance of circuit boards. This technology is widely used in various high-density electronic devices, such as smartphones, tablets, laptops, etc. Through blind via and buried via technology, these devices can implement more complex functions in a smaller volume and provide a better user experience.
In modern communication equipment, the requirements for circuit boards are particularly stringent, requiring high-speed data transmission and stability within a limited space. Blind hole and buried hole technology can achieve high-density wiring and connections, improve the speed and stability of signal transmission, thereby ensuring the performance and reliability of communication equipment. This technology is widely used in various communication equipment, including routers, switches, base stations, etc., providing faster and more stable network connections for people’s communications.
With the continuous development of automotive electronic technology, the electronic devices in modern cars are becoming more and more diverse and complex. Blind via and buried via technology have been widely used in the field of automotive electronics, mainly in automotive control systems, in-vehicle entertainment systems, driving assistance systems, etc. Through blind hole and buried hole technology, automotive electronic equipment can maintain stable performance in harsh working environments, improving the safety, comfort and intelligence of the car.
In general, blind hole and buried hole technology have been widely used in the fields of high-density electronic equipment, communication equipment, and automotive electronics, providing the possibility to improve the performance and reduce the size of various electronic equipment, and promote the development of modern technology and progress.
How much does a PCB with blind and buried vias cost?
The application of blind via and buried via technology in PCB manufacturing can improve the density and performance of circuit boards, but it will also affect manufacturing costs. Understanding these cost factors and being able to accurately estimate the cost of PCBs featuring these technologies is critical for manufacturers and designers.
Design evaluation: First, the PCB design needs to be evaluated to determine the number, size, and location of blind holes and buried holes. These design parameters will directly affect manufacturing costs.
Material cost analysis: Cost analysis of required materials, including substrate material, copper thickness, drilling materials, etc. Choosing the right material type and supplier is an important step in reducing costs.
Manufacturing process assessment: Understand the cost impact of different manufacturing processes, including drilling, plating, etching and other processing steps. Choosing appropriate processing technology and process parameters can effectively control costs.
Production scale considerations: Consider the impact of production scale on costs, evaluate the cost difference between mass production and small batch production, and develop a production plan based on market demand and expected sales.
Market research: Conduct market research to understand the PCB market price level and competition to ensure reasonable pricing and maintain competitiveness.
In summary, it is critical for manufacturers and designers to understand the factors that affect the cost of blind and buried via technologies and to be able to accurately estimate the cost of PCBs with these technologies. Through reasonable design and cost control strategies, the best performance and cost-effectiveness of blind and buried via technologies can be achieved.
How to choose the right manufacturer for manufacturing PCBs with blind and buried vias?
When choosing the right manufacturer to manufacture PCBs with blind and buried vias, you need to consider a range of factors to ensure that the manufacturer you choose can meet your needs and provide a high-quality product. Here are some important considerations:
Experience and expertise: First, you should choose a manufacturer with extensive experience and expertise. They should have an in-depth understanding of blind and buried via technology and be able to provide you with professional advice and support.
Technical capabilities: Manufacturers should have advanced production equipment and technology and be able to implement complex blind and buried via designs. Their engineering team should have strong technical capabilities and be able to handle various challenges and provide high-quality solutions.
Quality Control: Quality is one of the key factors in choosing a manufacturer. You should choose a manufacturer with strict quality control processes and certifications to ensure stable and reliable product quality.
Lead time: Production lead time is another important consideration. You want to choose a manufacturer that can deliver on time and is flexible enough to respond to urgent orders.
Customization capabilities: The manufacturer should be able to provide customized solutions based on your specific needs. They should be able to flexibly adapt their production processes to meet your individual requirements.
Customer Service: A good manufacturer should provide excellent customer service, respond promptly to your questions and needs, and provide you with ongoing support and assistance.
Cost-Effectiveness: Finally, you also need to consider cost-effectiveness. While quality is the primary consideration, you should also choose a manufacturer that offers competitive pricing.
All in all, choosing the right manufacturer to manufacture PCBs with blind and buried vias requires a comprehensive consideration of multiple factors, including experience, technical capabilities, quality control, delivery time, customization capabilities, customer service, and cost-effectiveness. By carefully evaluating and comparing the pros and cons of different manufacturers, you can choose the partner that best suits your needs, ensuring your project runs smoothly and achieves the desired results.
What are the key characteristics of great customer service?
Excellent customer service is crucial for PCB manufacturers. Not only does it build and maintain customer relationships, it also increases customer satisfaction and loyalty. Here are the key characteristics of great customer service:
Great customer service starts with a fast, timely response. No matter what questions or needs customers raise, manufacturers should respond as quickly as possible and show concern and attention to their customers. Timely feedback not only solves problems but also demonstrates the manufacturer’s professionalism and focus.
Manufacturers should have extensive expertise and be able to provide customers with accurate and comprehensive solutions. Whether it is about PCB design, material selection or manufacturing process, manufacturers should have sufficient expertise to meet customer needs and provide valuable suggestions and opinions.
Customer needs vary, so manufacturers should be able to provide customized solutions to customers. By gaining a deep understanding of customers’ needs and requirements, manufacturers can provide personalized services and products that meet customer expectations, thereby enhancing customer satisfaction and loyalty.
Good communication is key to building and maintaining customer relationships. Manufacturers should maintain close communication with customers and promptly share information such as project progress, problem solutions, and technology updates. Through effective communication, manufacturers can enhance customer trust and ensure projects run smoothly and meet customer expectations.
Excellent customer service is not only important during the project, but also during the after-sales phase after the project is completed. Manufacturers should provide customers with comprehensive after-sales support, including technical support, maintenance services and problem solving. Through timely and effective after-sales support, manufacturers can increase customer satisfaction and build long-term, strong relationships.
In the highly competitive PCB manufacturing industry, excellent customer service is the key to a manufacturer’s success. Through key features such as timely response, expertise, customized solutions, good communication and after-sales support, manufacturers can meet customer needs, improve customer satisfaction, and achieve sustainable development and growth.
FAQS
What are the cost implications of using blind and buried vias?
Incorporating blind and buried vias into PCB designs can increase manufacturing costs due to the additional complexity involved in the drilling and plating processes. However, the benefits in terms of improved performance and space savings may outweigh the added cost for certain applications.
Are there any limitations or drawbacks to using blind and buried vias?
While blind and buried vias offer significant advantages, they also come with limitations. For example, blind vias may have aspect ratio limitations, and buried vias can make PCB debugging and repair more challenging. Additionally, not all PCB manufacturers may offer blind and buried via capabilities.
How can I ensure the reliability of blind and buried vias in my PCB design?
To ensure the reliability of blind and buried vias, it is important to work closely with experienced PCB designers and manufacturers who have expertise in handling these advanced technologies. Conducting thorough design reviews and testing prototypes can also help identify and mitigate any potential issues early in the process.
Blind Vias&Buried Vias PCB manufacturing
If you encounter issues with blind or buried vias in your PCB design, some common troubleshooting steps include checking for proper drill alignment, verifying plating thickness, and examining the integrity of the via connections using X-ray or other inspection methods.