Ceramic PCB Substrates Manufacturing. Ceramic materials PCBs, and Ceramic package substrates Vendor. we produce the Ceramic boards from 1 layer to 20 layers.
In the ever-changing world of electronics manufacturing, ceramic PCB substrates have become a game-changing technology, delivering unparalleled performance and reliability. Industries ranging from aerospace to telecommunications are increasingly turning to ceramic PCB substrates to meet their stringent requirements. In this comprehensive guide, we dive into the intricacies of ceramic PCB substrate manufacturing, discussing its processes, materials, cost considerations, and more.
What is a ceramic PCB substrate?
In the field of modern electronic manufacturing, ceramic PCB substrates represent an innovative technology that provides new solutions for the performance and reliability of electronic devices. Compared with traditional PCBs based on organic materials, ceramic PCB substrates utilize high-purity ceramic materials, such as aluminum oxide (Al2O3) or aluminum nitride (AlN), as a carrier for the substrate. These ceramic materials have excellent thermal conductivity, mechanical strength and electrical insulation properties, allowing ceramic PCBs to perform well in high power, high frequency circuits and harsh environments.
The manufacturing process of ceramic PCB substrates involves precision craftsmanship and advanced technology. First, high-purity ceramic powder is mixed with binders and additives to form a slurry, which is then shaped and processed to form sheets of the desired size and surface finish. Next, conductive metal lines and holes are deposited on the surface of the substrate through screen printing or other deposition techniques to form the circuit layout. Subsequently, after multiple high-temperature sinterings in the kiln, the ceramic substrate is densified, and the metal circuits are sintered to form a solid electrical connection. Finally, surface treatments such as metallization, solder film coating, and surface shaping are performed to improve solderability and ease of component installation.
The advantage of ceramic PCB substrates is their excellent performance and reliability. Because ceramic materials have excellent thermal conductivity, ceramic PCBs can effectively disperse heat and reduce the operating temperature of electronic components, thus improving the performance and life of the device. In addition, ceramic PCBs have high mechanical strength, good pressure resistance, and are not easily affected by external environmental factors, so they have excellent stability and reliability in harsh working environments. This makes ceramic PCBs the preferred solution in fields such as aerospace, communications, and medical, especially for applications with demanding performance requirements and harsh working environments.
What factors need to be considered when designing ceramic PCBs?
When designing a ceramic PCB, several factors need to be considered to ensure the performance and reliability of the final product. First, designers must have a deep understanding of the properties and limitations of the ceramic materials used. Ceramic materials often have excellent thermal conductivity, mechanical strength, and electrical insulation properties, but may also present specific molding difficulties or size limitations. Therefore, the design must weigh these factors and select the appropriate ceramic material to meet the requirements of the specific application.
Secondly, circuit layout is crucial in ceramic PCB design. Optimized circuit layout can minimize signal interference, crosstalk and electromagnetic interference, thereby improving circuit stability and performance. During the design process, designers need to consider signal transmission paths, power distribution, ground and power plane layout, as well as the location and connection of components. Proper circuit layout can reduce the power consumption of ceramic PCBs, improve signal integrity, and ensure stable operation of the circuit in high-frequency and high-temperature environments.
In addition, manufacturing constraints are also one of the important factors to consider when designing ceramic PCBs. The manufacturing process of ceramic PCBs may be subject to some limitations, such as the difficulty of molding ceramic materials, processing accuracy requirements and the feasibility of subsequent processes. Therefore, designers need to consider various constraints in the manufacturing process during the design stage, and reduce manufacturing costs and improve production efficiency through reasonable design and optimization. For example, methods such as avoiding designing structures that are too small or complex, choosing sizes and shapes suitable for ceramic processing, and adopting standardized manufacturing processes can effectively deal with manufacturing constraints.
In summary, designing ceramic PCBs requires comprehensive consideration of material properties, circuit layout, and manufacturing constraints. Only by fully understanding and effectively coping with these factors can we design ceramic PCBs with excellent performance, reliability and stability to meet various high-demand application needs.
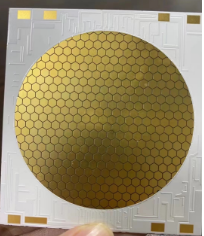
Ceramic PCB
What is the manufacturing process for ceramic PCBs?
The manufacturing process of ceramic PCB (Printed Circuit Board) is a complex and precise process, involving precise control of multiple links and highly professional technology. Let’s dive into the various steps of this process:
The first step in manufacturing a ceramic PCB is substrate preparation. High-purity ceramic powder, such as aluminum oxide (Al2O3) or aluminum nitride (AlN), is usually used, mixed with additives to form a slurry. The slurry is then poured into a mold and pressed or cast to form a preliminary ceramic substrate.
Print on the surface of the ceramic substrate. Conductive metal lines and vias are printed on the surface of the substrate through screen printing technology or other deposition technologies. These conductive traces form the PCB’s electrical connections and provide connection points for electronic components.
The printed ceramic PCB substrate needs to undergo multiple sintering processes. During the sintering process, the substrate is exposed to a high temperature environment and subjected to multiple heating and cooling cycles. This helps burn out the binder in the substrate while encouraging the ceramic particles to combine into a dense structure. At the same time, the metal particles in the conductive lines will also be sintered to ensure the stability of the electrical connection.
Post-sintered ceramic PCB substrates may undergo surface treatments to improve their corrosion resistance and solderability. This may include steps such as metallization, pad coverage, and surface profiling. These treatments make the PCB easier to solder electronic components and improve its stability in harsh environments.
After ceramic PCB manufacturing is completed, strict inspection and testing is required to ensure quality meets requirements. This includes visual inspection, electrical testing, dimensional measurements and possibly environmental durability testing. Only PCBs that pass all inspections and tests can be considered qualified products.
Finally, the ceramic PCB is protected with appropriate packaging and ready for shipment. This may involve anti-static packaging, moisture-proof packaging or other customized packaging methods to ensure that the product reaches the customer safely during transportation.
Overall, the manufacturing process of ceramic PCBs requires a high degree of process technology and strict quality control to ensure that the final product has excellent performance and reliability and meets customer needs and expectations.
What are the material and cost considerations for ceramic PCBs?
When designing and manufacturing ceramic PCBs, choosing the right materials and considering cost factors are critical. The following are factors to be aware of in this regard:
Selecting the appropriate ceramic material is a critical step. Commonly used materials include aluminum oxide (Al2O3) and aluminum nitride (AlN). Aluminum oxide has good insulation properties and lower cost, and is suitable for applications with low general performance requirements; aluminum nitride has higher thermal conductivity and mechanical strength, and is suitable for high-power, high-frequency circuits and harsh environmental conditions.
Because ceramic PCBs have excellent thermal conductivity properties, thermal management needs to be considered during design. Effective thermal design can improve circuit performance and reliability while extending device life.
The size and thickness of ceramic PCBs are critical to circuit design and performance. Through reasonable size and thickness selection, circuit stability and reliability can be achieved.
When designing a PCB, you need to ensure that the selected materials match the circuit layout and application environment. For example, for high-frequency circuits, materials with lower dielectric losses and stable dielectric constants need to be selected.
Optimizing circuit layout is an important step in ensuring ceramic PCB performance and reliability. Proper layout can reduce signal interference, improve signal integrity, and ensure circuit stability and reliability.
Given the unique nature of ceramic PCB manufacturing, manufacturing constraints need to be fully considered. For example, ceramic materials are difficult to process and require special processing equipment and process technology; in addition, temperature and time need to be strictly controlled during the sintering process to ensure product quality.
The cost of ceramic PCBs is usually higher, mainly affected by the following factors:
In summary, selecting appropriate materials, optimizing circuit design, considering manufacturing constraints, and managing costs appropriately are important considerations when designing and manufacturing ceramic PCBs.
Who are the major manufacturers of ceramic PCBs?
In the ceramic PCB market, some major manufacturers are leading the industry and providing high-quality products and services to customers. Among them, our company (company name), as one of the leaders in the industry, adheres to excellent quality and innovative spirit and is committed to meeting the diverse needs of customers.
As one of the leading manufacturers of ceramic PCBs, we have advanced production facilities and technical teams to offer a wide range of ceramic PCB solutions covering various application areas. Our manufacturing process strictly follows industry standards to ensure stable and reliable product quality.
Our ceramic PCBs have higher thermal conductivity, greater mechanical strength and superior electrical insulation properties compared to traditional FR-4 boards, making them excellent in high power and high frequency applications. Our products are highly customizable to meet customer-specific design requirements, resulting in higher performance and reliability.
As a manufacturer with extensive experience, we understand our customers’ pursuit of quality and reliability. Therefore, we adopt strict quality control measures and strictly control every aspect from raw material procurement to production and manufacturing to ensure the excellent quality of each ceramic PCB.
In addition to product quality, we also focus on communication and cooperation with customers. Our team upholds an open, transparent and positive working attitude, always listens to customers’ needs and feedback, and provides customers with professional technical support and thoughtful after-sales service.
In today’s fierce competition in the ceramic PCB market, our company will continue to adhere to the concept of “quality first, service first”, continuously improve product quality and service levels, and work with customers to create a better future.
How to provide excellent customer service?
In the field of ceramic PCB manufacturing, providing excellent customer service is crucial, which is not only related to customer satisfaction, but also directly affects the long-term stability of the partnership. Here’s how to achieve great customer service:
During the ceramic PCB manufacturing process, it is crucial to ensure clear and transparent communication with your customers. This includes clearly understanding customer needs and requirements, providing customers with detailed product information and progress updates, and responding promptly to customer inquiries and questions. By establishing open and honest channels of communication, a foundation of trust and collaboration can be built.
Customers often expect quick responses when needed, especially in emergencies. Therefore, promptly responding to customer emails, phone calls, or online inquiries is key to providing excellent customer service. Establishing an efficient customer service team to ensure that questions and needs raised by customers can be handled in a timely manner is an important step in ensuring customer satisfaction.
During the ceramic PCB manufacturing process, customers may encounter various technical challenges or questions. Therefore, providing professional technical support is an important part of excellent customer service. This includes dispatching experienced engineers and technicians to provide customers with customized solutions, solve technical problems, and provide relevant training and guidance to help customers realize the full potential of the product.
After the delivery of ceramic PCB products, quality after-sales service is also crucial. This includes promptly handling customer complaints and issues, providing product repair and replacement services, as well as conducting regular customer satisfaction surveys, collecting customer feedback and continuously improving product and service quality. By proactively paying attention to customer needs and feedback and establishing a good after-sales service system, customer satisfaction and loyalty can be improved.
In general, providing high-quality customer service is not only a basic requirement to meet customer needs, but also the key to establishing long-term cooperative relationships and establishing a good reputation for the company. Through clear communication, quick response, professional technical support and thoughtful after-sales service, ceramic PCB manufacturing companies can win the trust and support of customers, maintain competitive advantages, and achieve sustainable development.
Frequently Asked Questions
What factors influence the cost of Ceramic PCB Substrates?
The cost of Ceramic PCB Substrates is influenced by various factors, including material selection, complexity of design, and manufacturing volume. Ceramic materials such as alumina or aluminum nitride tend to be more expensive compared to traditional organic substrates due to their superior properties and specialized manufacturing processes. Additionally, intricate designs with densely packed components or high-density interconnects may incur higher manufacturing costs. Furthermore, economies of scale play a significant role, with larger production volumes generally resulting in lower per-unit costs. Overall, careful consideration of material options, design complexity, and production volume is essential in determining the cost-effectiveness of Ceramic PCB Substrates for specific applications.
How do I select the right manufacturer for Ceramic PCB Substrates?
Selecting the right manufacturer for Ceramic PCB Substrates is crucial to ensuring product quality, reliability, and timely delivery. When choosing a manufacturer, consider factors such as expertise in ceramic materials, advanced manufacturing capabilities, and a track record of delivering high-quality products. Look for manufacturers with extensive experience in ceramic substrate fabrication and a proven track record of serving industries such as aerospace, telecommunications, and automotive. Additionally, inquire about the manufacturer’s quality control processes, certifications, and adherence to industry standards. Collaborating with a reputable manufacturer that prioritizes customer satisfaction and offers comprehensive technical support can significantly enhance the success of your Ceramic PCB projects.
What are the advantages of Ceramic PCB Substrates over traditional materials?
Ceramic PCB Substrates offer several advantages over traditional materials such as FR-4. Firstly, they exhibit significantly higher thermal conductivity, allowing for efficient dissipation of heat generated by electronic components. This property makes Ceramic PCBs particularly well-suited for high-power applications where thermal management is critical. Additionally, ceramics provide excellent mechanical strength and dimensional stability, ensuring reliability in harsh operating conditions. Moreover, Ceramic PCBs offer superior electrical insulation properties, reducing the risk of signal interference and short circuits. Overall, these advantages contribute to enhanced performance and longevity of electronic devices utilizing Ceramic PCB Substrates.