CPU Ball Package Substrates Manufacturer . the Package Substrate will be made with Showa Denko and Ajinomoto High speed materials.or other.
In modern electronic equipment, CPU Ball Package Substrates are a key component to ensure efficient operation of the equipment. These substrates are precision manufactured to provide stable support and connectivity to the central processing unit (CPU). This article will delve into the important role of CPU ball packaging substrates, manufacturing processes, and their indispensability in various application fields.
What are CPU Ball Package Substrates?
CPU Ball Package Substrates are an indispensable and key component of modern electronic equipment. They provide a solid connection between the central processing unit (CPU) and the motherboard, providing the necessary support for the device to run efficiently.
These substrates usually use fiberglass reinforced epoxy resin (FR-4) as the base material. This material has good mechanical properties and heat resistance and is very suitable as a substrate material for electronic devices. The surface of the substrate is covered with metal balls, usually made of a tin-lead alloy. These metal balls act as connectors, connecting the CPU to corresponding contact points on the motherboard.
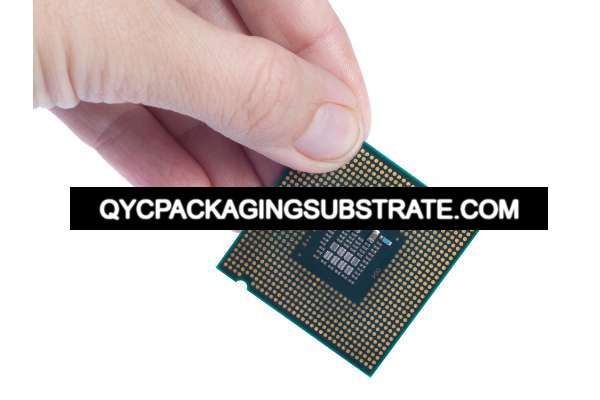
CPU Ball Package Substrates Manufacturer
Designing CPU ball packaging substrates requires precise processes and strict quality control. The wiring layout of the substrate must be precisely designed to ensure stable electrical connections and minimize signal interference. In addition, thermal management of the substrate is also very important, especially in high-performance CPU applications. By designing a reasonable heat dissipation structure and selecting appropriate materials, the temperature of the CPU can be effectively reduced and the stability and reliability of the device can be ensured.
In general, CPU ball packaging substrate is a crucial component in modern electronic equipment. Not only do they provide a stable electrical connection, they also help to effectively manage the heat of the CPU, ensuring efficient operation and stability of the device. In the ever-evolving field of electronic technology, the importance of CPU ball packaging substrates will continue to increase, providing strong support for various application scenarios.
CPU Ball Package Substrates design Reference Guide.
When designing a CPU ball packaging substrate, engineers need to consider multiple key factors to ensure that the final product has excellent performance and reliability. Here is a brief overview of some important considerations:
Wiring layout
Good wiring layout is the key to CPU ball package substrate design. Engineers need to consider the length of signal transmission paths, minimization of interference and crosstalk, and appropriate separation between signal lines and power and ground lines. By optimizing the wiring layout, signal delays and distortions can be minimized and system performance improved.
Material selection
When selecting substrate materials, engineers need to consider factors such as electrical performance, thermal conductivity and mechanical strength. Commonly used substrate materials include FR-4, high-frequency materials, and metal substrates. Correct selection of materials ensures good electrical properties and stable structural performance of the substrate.
Thermal management
The CPU ball package substrate generates a lot of heat during operation, so good thermal management is crucial. Engineers need to design effective heat dissipation structures, such as heat sinks, heat dissipation holes, etc., to ensure that the temperature of the CPU and surrounding components remains within a safe range. In addition, selecting appropriate heat dissipation materials and heat dissipation methods is also a key step.
Design Reference Guide
Provides valuable advice and best practices to help engineers avoid common mistakes and problems during the design process. By following the guidelines in the Design Reference Guide, engineers can ensure that the CPU ball package substrate design meets requirements and delivers excellent performance and reliability. To sum up, detailed design reference guide is one of the keys to designing high-quality CPU ball packaging substrate, and it is also one of the important guarantees to ensure the smooth operation of electronic equipment.
What material is used in CPU Ball Package Substrates?
CPU ball packaging substrate is a key component in modern electronic equipment, and its material selection is crucial. Materials must be highly reliable and durable without compromising stability, thermal conductivity and electrical performance. The following are commonly used materials for CPU ball packaging substrates:
FR-4 (fiberglass reinforced epoxy resin)
FR-4 is one of the most common substrate materials and has excellent mechanical strength and temperature resistance. It has good insulation properties and can effectively prevent electrical short circuits. It is one of the ideal choices for CPU ball packaging substrates.
Metal ball
As a medium connecting the CPU and the motherboard, metal balls are usually made of tin-lead alloy. These small metal balls provide a stable electrical connection when connected and have good thermal conductivity to help dissipate heat effectively.
Copper foil
In the manufacturing process of CPU ball packaging substrate, copper foil is used as the material of the conductive layer. Copper has good electrical conductivity and processability, which can ensure the stability and reliability of the circuit.
Solder paste
Solder paste is one of the key materials connecting the CPU and the motherboard, and is usually composed of solder alloy. Solder paste has good wettability and fluidity, and can form stable solder joints during the soldering process to ensure the reliability of electrical connections.
Organic packaging materials
In addition to the material of the substrate itself, organic packaging materials are also an important component of the CPU ball packaging substrate. These materials are typically high-temperature resistant resins used to encapsulate and protect circuit components, ensuring their long-term stable operation.
To sum up, the materials used in the CPU ball packaging substrate must have a high degree of stability, thermal conductivity and electrical properties to ensure the reliability and performance of electronic devices. By rationally selecting materials and strictly controlling the manufacturing process, CPU ball packaging substrates can meet the needs of various application fields and provide solid support for the development of modern electronic technology.
What size are CPU Ball Package Substrates?
The size of the CPU ball packaging substrate is usually affected by multiple factors, including the design requirements of the specific device, CPU packaging type, and application scenarios. Although CPU ball packaging substrates exist in various sizes, generally speaking, they are designed to achieve high integration and compact layout in modern electronic devices.
In large systems such as personal computers and servers, the size of the CPU ball package substrate is usually larger to accommodate more circuit components and connections. These substrates may have dimensions from a few inches to a dozen inches to meet the needs of high-performance computing and data processing. At the same time, they may also contain multiple CPU packages to achieve parallel computing and multi-core processing functions.
In mobile devices and embedded systems, the size of the CPU ball packaging substrate is usually smaller due to space constraints. These substrates may only be a few centimeters to a few inches in size, but still need to provide stable electrical connections and excellent performance. Therefore, when designing these substrates, engineers need to pay special attention to layout compactness and thermal management effects to ensure that the device’s performance requirements are met and the size is minimized.
In general, CPU ball packaging substrates come in a wide range of sizes and can be customized according to specific application needs. Whether it’s a large server or a small smartphone, the right substrate size is needed to support its functionality and performance. Therefore, when designing and manufacturing CPU ball packaging substrates, multiple factors need to be considered to ensure that the final product meets the requirements of the device and has excellent performance and reliability.
The Manufacturer Process of CPU Ball Package Substrates.
The manufacturing process of CPU ball packaging substrate is a precise and complex process, which involves multiple key steps. Each step is crucial and requires precise operation and strict quality control to ensure the stability and reliability of the final product. sex.
The first is material pretreatment. Before manufacturing the CPU ball packaging substrate, various raw materials need to go through a strict pre-processing process. This includes steps such as cleaning the substrate material, removing surface oxides, and applying solder mask ink to ensure that subsequent processes can proceed smoothly and achieve the desired results.
Next is printing the solder mask and conductive pattern. The printed solder mask is to protect the substrate surface from short circuits caused by soldering, while the conductive pattern is to form circuit connections. These patterns need to be accurately formed on the surface of the substrate through a special printing process to ensure that subsequent electrical connections can proceed smoothly.
Etching is another critical step in the manufacturing process. After the conductive pattern is formed, excess metal material needs to be etched away from the substrate surface to form precise circuit connections. This process requires precision chemical etching technology and strict control parameters to ensure the accuracy and consistency of etching.
Next is the ball joint. This is a key step in the electrical connection between the CPU ball package substrate and the CPU. In this process, special equipment and processes are used to form tiny metal balls on the surface of the substrate for reliable connection with the CPU. The accuracy and stability of this step directly affects the performance and reliability of the final product.
The last step is inspection. Strict quality inspections are required at all stages of the manufacturing process to ensure that products meet requirements. After manufacturing is completed, terminal inspection is also required, including visual inspection, electrical testing, etc., to ensure that the stability and reliability of the product reach the expected level.
To sum up, the manufacturing process of CPU ball packaging substrate involves multiple key steps, each step requiring precise operation and strict quality control. Only by ensuring that each step is correct can the final product have stability and reliability and meet the performance and quality requirements of modern electronic equipment.
The Application area of CPU Ball Package Substrates.
CPU ball packaging substrate plays a vital role in modern electronic equipment and is widely used in various fields, including personal computers, smartphones, industrial control systems, etc. These substrates provide stable electrical connections and excellent performance for these devices, becoming an integral part of modern electronic technology.
In the field of personal computers, the CPU ball packaging substrate is an important connection bridge between the CPU and the motherboard. Through high-quality substrate design and manufacturing, personal computers can achieve efficient data transmission and processing, providing users with a smooth experience.
Smartphones are another important application field. For such small, high-performance devices, the stability and reliability of the CPU ball packaging substrate are particularly critical. These substrates not only need to meet the requirements of small size and lightweight, but also need to have excellent thermal management performance to ensure that mobile phones do not have performance problems under long-term high-load use.
In industrial control systems, the CPU ball package substrate is responsible for processing data and controlling equipment. These substrates need to have high stability and anti-interference capabilities to ensure the normal operation of industrial equipment and ensure the stability and efficiency of the production line.
In addition to the above fields, CPU ball packaging substrates are also widely used in automotive electronics, communication equipment, medical equipment and other fields. Whether it is ordinary consumer electronics or high-end professional equipment, these key substrates are inseparable. Therefore, the CPU ball packaging substrate is not only an essential component of modern electronic equipment, but also an important driving force for technological progress and industrial development.
What are the advantages of CPU Ball Package Substrates?
Compared with traditional welding technology, CPU ball packaging substrate has significant advantages in the design and manufacturing of electronic equipment. First, they provide greater reliability. Because the CPU ball package substrates are connected by metal balls instead of traditional soldering, they have a more stable electrical connection. Metal ball connections are less susceptible to external vibrations or temperature changes, greatly reducing the risk of component discontinuities and extending the life of the equipment.
Secondly, the CPU ball packaging substrate has excellent thermal management capabilities. In high-performance electronic devices, the heat generated by the CPU is a key challenge. Traditional soldering techniques can cause heat to concentrate around the solder joint, increasing the risk of heat loss and temperature rise. The CPU ball-type packaging substrate is connected through metal balls, which effectively disperses heat and improves heat dissipation efficiency, thus maintaining the stable operation of the CPU.
In addition, the design of the CPU ball package substrate is more compact. Traditional soldering techniques usually require additional space to arrange solder joints and connection lines, limiting the overall size and layout of electronic devices. The CPU spherical packaging substrate adopts spherical connection, which can achieve stable connection in a smaller space, making the device design more flexible, the overall size smaller, and suitable for a wider range of application scenarios.
Therefore, these advantages make CPU ball packaging substrates the first choice for many electronic devices. Whether it is a personal computer, a smartphone or an industrial control system, the performance, reliability and flexibility of the device can be improved by using CPU ball packaging substrates to meet the growing market demand. The technological progress of CPU ball packaging substrates will continue to promote the development of electronic equipment and bring people a more intelligent, convenient and efficient life experience.
FAQ
What is the difference between CPU ball packaging substrate and traditional soldering technology?
Traditional soldering technology usually uses solder to directly connect electronic components and substrates, while the CPU ball packaging substrate uses more advanced ball connection technology. This spherical connection provides higher connection density and more stable connection quality, while also improving thermal management efficiency. In contrast, traditional welding technology may suffer from problems such as poor welding and thermal expansion mismatch.
How to ensure the stability of the spherical connection of the CPU ball package substrate?
The ball connection of the CPU ball package substrate uses precision-made metal balls, which can provide strong mechanical support and electrical connection. During the manufacturing process, ball joints undergo strict quality control and inspection to ensure the stability and reliability of each connection point. In addition, the design of the spherical connection also takes factors such as thermal expansion into account to maintain a stable connection at different temperatures.
What are the advantages of CPU ball packaging substrate in terms of thermal management?
The CPU ball package substrate connects the CPU to the motherboard through a ball connection. This design can conduct heat more effectively and achieve optimized thermal management. The larger contact area between the metal ball and the substrate can transfer heat to the radiator or other heat dissipation devices faster, thereby improving the CPU’s working efficiency and extending its service life. In addition, the design of the spherical connection can also reduce the impact of thermal expansion on the connection quality and maintain connection stability.