High speed mixed dielectric PCB manufacturing. High speed and high frequency mixed dielectric material PCBs Vendor. We offer the mixed dielectric HDI PCB from 4 layer to 50 layers.
In today’s world of electronic engineering, high-speed mixed media PCB manufacturing plays a vital role, becoming the fundamental backbone of almost all electronic devices. High-speed mixed media PCBs not only provide reliable electrical connections, but also meet the stringent requirements of modern electronic equipment for high-speed data transmission and signal integrity. This article will delve into the definition, design and manufacturing process of high-speed mixed media PCB, as well as related costs and materials, aiming to provide engineers and enthusiasts with a comprehensive understanding and guidance.
What is a high-speed mixed media PCB?
High-speed mixed media PCB, as a core component of modern electronic engineering, plays a vital role. It not only provides electrical connections between electronic components, but also provides them with the necessary mechanical support. Specifically, high-speed mixed-media PCBs enable connections and communications between electronic components by etching or “printing” conductive paths on the board surface. These conductive paths are usually made of copper or other conductive materials and are precisely laid out on the surface of the PCB.
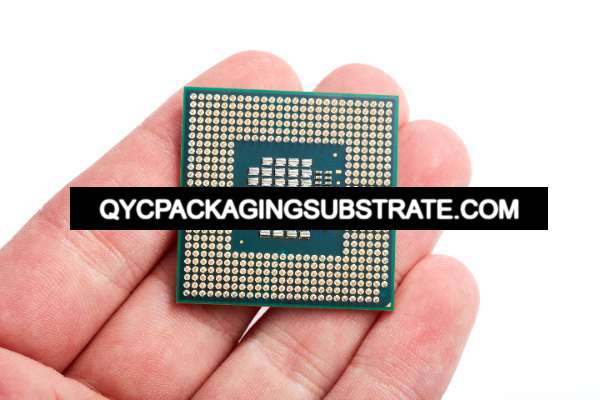
High speed mixed dielectric PCB manufacturing
In high-speed mixed-media PCBs, the key to design is to ensure that signals can be transmitted at high speeds and frequencies while minimizing signal attenuation and distortion. This requires PCB design and manufacturing to comply with strict specifications and standards to ensure circuit performance and reliability. Therefore, during the manufacturing process of high-speed mixed-media PCBs, engineers not only need to consider the layout and connection methods of conductive paths, but also need to select appropriate materials and processes to minimize losses and interference during signal transmission.
In addition to providing electrical connections, high-speed mixed media PCBs also perform the important task of providing mechanical support for electronic components. PCBs are often designed to have specific shapes and sizes to fit a specific device or system. By soldering or plugging electronic components onto the PCB, they can be securely held together to form a complete circuit system.
Overall, high-speed mixed media PCBs play a vital role in modern electronic devices. It is not only a key connector between electronic components, but also provides them with the necessary mechanical support so that various devices and systems can operate properly. Therefore, it is crucial for electronic engineers and manufacturers to understand and master the design and manufacturing technology of high-speed mixed media PCB, which will help them improve circuit performance, reduce costs, and meet evolving market demands.
How to design high-speed mixed media PCB?
Designing high-speed mixed-media PCBs is a challenging task that requires careful planning and execution by engineers in terms of schematic capture, component placement, routing, and layout. This process requires not only a deep understanding of the functional requirements of the circuit, but also the physical characteristics of the PCB, space constraints, and the feasibility of the manufacturing process. Here are the key steps for designing high-speed mixed-media PCBs:
The first step in design is to capture the schematic of the circuit. Engineers need to carefully analyze the circuit’s functional and connection requirements and translate this information into a clear schematic. At this stage, close collaboration with team members and customers is critical to ensure an accurate understanding of circuit requirements.
After the schematic is captured, engineers need to place the various components in the circuit onto the PCB board. This process requires consideration of factors such as interconnections between components, signal transmission paths, and heat distribution. With proper component placement, signal interference and power loss can be minimized, thereby improving circuit performance and stability.
Routing is one of the most critical steps in the design process. Engineers need to connect the placed components with wires and design the best layout plan. During the wiring process, factors such as signal transmission delay, matching impedance, signal stacking, and differential signal transmission need to be considered. By using high-speed wiring technology and reasonable stacking design, signal crosstalk and signal distortion can be effectively reduced, and the anti-interference ability and transmission speed of the circuit can be improved.
Designing high-speed mixed media PCB usually requires the use of professional PCB design software, such as Altium Designer, Cadence Allegro, etc. These software provide a wealth of functions and tools to help engineers with various aspects of schematic design, component placement, wiring and layout. Through these software, engineers can complete design tasks quickly and accurately, and simulate and optimize the design to ensure the best performance and stability of the circuit.
In summary, designing high-speed mixed-media PCBs is a complex and sophisticated job that requires engineers to have extensive experience and expertise in schematic capture, component placement, routing, and layout. Through careful planning and careful execution, engineers can design high-speed mixed-media PCBs with powerful functions and stable performance to meet the high-speed data transmission and signal processing needs of modern electronic products.
What does the high-speed mixed media PCB manufacturing process look like?
The manufacturing process of high-speed mixed-media PCBs is a precise and complex process involving multiple critical steps, each of which has a significant impact on the quality and performance of the final product.
First, the first step in manufacturing high-speed mixed-media PCBs is substrate selection. Substrate selection is critical to PCB performance. Common substrate materials include fiberglass reinforced epoxy resin (FR-4), polytetrafluoroethylene (PTFE), etc. Selecting the appropriate substrate material depends on the circuit design requirements, including operating frequency, thermal stability, mechanical strength and other factors.
Next is the layering process. In this step, multiple stacked substrates are bonded together through a lamination process. Each layer contains conductive and insulating layers, forming the structural framework of the PCB.
Copper patterning is one of the key steps in the manufacturing process. In this step, a conductive pattern is transferred to the substrate surface via photolithography. First, a layer of light-sensitive photoresist is coated on the surface of the substrate, and then mask photolithography is used to expose light to the resist layer to form a conductive pattern. Next, copper is deposited on the conductive pattern through chemical etching or metal evaporation to form a conductive path.
Drilling is another important step in the manufacturing process. In this step, a CNC drill is used to drill holes in the PCB for subsequent installation of electronic components and connecting wires.
Copper plating is to increase conductivity and protect the PCB surface. By immersing the PCB in an electrolyte, a thin layer of copper is plated within the conductive patterns and holes to increase the circuit’s conductivity and corrosion resistance.
Finally, etching is the process of removing unwanted copper material from the PCB surface. In this step, the PCB is immersed in an etching solution, which chemically etches away unwanted copper material so that the conductive pattern is clearly visible.
Through the above series of steps, the final product of high-speed mixed media PCB has complete functionality and assembleability. These PCBs can be used in various high-speed electronic equipment, such as communication equipment, computers, automotive electronics and other fields, providing a solid foundation for the development of modern technology.
How to make high-speed mixed-media PCBs?
Manufacturing high-speed mixed-media PCBs requires a series of precise and meticulous operations, each stage having a significant impact on the quality and reliability of the final product. The following are the key steps in manufacturing high-speed mixed-media PCBs:
The first step in manufacturing a high-speed mixed-media PCB is a preliminary design. At this stage, engineers use professional PCB design software to develop circuit schematics based on circuit requirements and specifications, and determine the layout and routing of components. The quality of this design phase directly affects subsequent manufacturing and performance.
Once the design is complete, the next step is to prepare the substrate. Typically, substrate material selection is based on specific circuit needs and environmental conditions. Commonly used substrate materials for high-speed mixed media PCB include FR-4, Rogers, and high-frequency media. Substrate preparation includes steps such as cleaning, coating and drying to ensure that the substrate surface is flat, clean and adaptable to subsequent processes.
Copper deposition is one of the critical steps in manufacturing high-speed mixed-media PCBs. At this stage, the surface of the substrate is coated with a thin layer of copper to form a conductive layer. Through techniques such as chemical deposition or electroplating, the copper layer is tightly bonded to the surface of the substrate, providing good electrical conductivity for subsequent circuit connections.
Wiring is the process of connecting designed circuits. Engineers use photolithography and etching techniques to form fine patterns of wires and circuits on the copper layer. This process requires highly precise operation and control to ensure that the accuracy and spacing of the wires meet design requirements.
Final inspection is an important step to ensure that manufactured PCBs meet specifications and quality standards. At this stage, the PCB undergoes rigorous visual inspection, electrical performance testing, and functional verification to ensure its stable performance and reliability. Any potential flaws or problems will be promptly discovered and corrected at this stage.
In summary, manufacturing high-speed mixed-media PCBs is a complex and precise process that requires engineers to maintain a high degree of professionalism and meticulous operation at every stage. From design to final inspection, every step is critical and directly affects the performance and reliability of the final product.
What does the high-speed mixed media PCB manufacturing process look like?
The high-speed mixed-media PCB manufacturing process is a complex and precision engineering process designed to ensure high performance and reliability of the final product. Here are the key steps in the process:
During the initial stages of PCB manufacturing, engineers need to select a substrate material suitable for a specific application. For high-speed mixed-media PCBs, materials with excellent dielectric properties and high-frequency characteristics are often chosen, such as fiberglass-reinforced epoxy (FR-4).
Lamination refers to stacking multiple layers of substrates together to form the basic structure of a PCB. In the high-speed mixed media PCB manufacturing process, the stack-up design needs to consider signal integrity and electromagnetic compatibility to ensure stable signal transmission in high-frequency environments.
Copper patterning is the process of transferring a conductive pattern to the surface of a substrate. Using photolithography and etching techniques, engineers can precisely define the location and shape of wires, pads, and other circuit elements to make circuit connections.
Drilling is the process of drilling holes into a PCB to facilitate the connection of wires and components at different levels through the holes. In high-speed mixed-media PCB manufacturing, drilling accuracy and positional relationships are closely related, affecting the performance and reliability of the entire circuit.
Copper plating is to increase the conductivity and corrosion resistance of PCB wires. By depositing copper on the wires and pads, you ensure a stable electrical connection and increase the reliability and durability of your PCB.
Etching is the process of removing unwanted copper material from the PCB surface. Through chemical etching or machining, engineers can precisely define the shape of wires and pads to ensure accurate circuit connections on the PCB.
Together, these critical steps ensure high-speed mixed-media PCB manufacturing quality and performance. By carefully designing and strictly controlling each step, engineers can produce fully functional, reliable and stable PCBs that meet the needs of various high-speed electronic applications.
How to make high-speed mixed-media PCBs?
Manufacturing high-speed mixed-media PCBs requires a series of precision operations to ensure the final product is of excellent quality and reliability. The following are the main stages of the manufacturing process:
Initial Design Conversion: The first step in manufacturing high-speed mixed media PCBs is converting the design files into the format required for production. This involves converting the circuit board’s design drawings into production files for manufacturing, including layout and graphics information. At this stage, ensuring design accuracy and compliance is Critical Substrate Preparation:Next, select an appropriate substrate material and prepare it. This may include cutting the substrate to the required size, cleaning the surface to remove any dirt or impurities, and ensuring the surface is smooth and flat for subsequent processing steps.
Copper deposition: After the substrate is prepared, the surface of the substrate is covered with a layer of copper through chemical or electroplating. This layer of copper will become the conductive layer on the circuit board, providing the connections needed for the circuit.
Pattern production: On a copper-covered substrate, photolithography is used to transfer the design pattern to the substrate surface. This involves covering a substrate with photosensitive resin and then projecting the designed graphics onto the photosensitive resin, forming a pattern of graphics.
Etching: Once the pattern is formed, the unnecessary copper material needs to be etched away from the substrate surface, leaving the desired circuit pattern. This step is typically accomplished using chemical etchants, ensuring high precision and consistency.
Final Inspection: At the final stage of the manufacturing process, the completed PCB is thoroughly inspected and tested. This includes checking circuit continuity, resistance values, insulation properties, and cosmetic quality. Any defects found will be repaired or addressed to ensure the quality of the final product meets standards.
Through precision and meticulous operations, every manufacturing stage is critical to the quality and reliability of high-speed mixed media PCBs, from initial design to final inspection. Only by ensuring that each step is strictly controlled and inspected can we produce high-quality PCB products that meet the requirements.
How much does a high speed mixed media PCB cost?
The cost of high-speed mixed-media PCBs is a complex issue involving many factors. Size, complexity, materials and quantity are the main drivers when considering cost. First, size directly affects the board area and material usage, so larger PCB sizes usually bring higher costs. Additionally, with high-speed mixed-media PCBs, complexity is also an important factor. Complex circuit designs may require more layers, denser wiring, and more special processes, all of which increase manufacturing costs.
Materials also have a significant impact on cost. For high-speed mixed-media PCBs, high-performance substrate materials are often chosen, such as high-frequency media or special low-loss materials, which are inherently more expensive than ordinary FR-4 substrates. In addition, price fluctuations of metal materials such as copper will also affect the final PCB cost.
Quantity is another important cost factor. Typically, producing higher quantities of PCBs reduces unit costs because fixed costs (such as manufacturing setup and engineering expenses) can be spread over more boards. Therefore, unit costs are usually lower for items produced in high volumes.
Understanding these cost drivers is critical to budgeting and optimizing production costs. During the design phase, engineers need to weigh design requirements against cost constraints to ensure functionality and performance are achieved while keeping costs under control. At the same time, working with suppliers and evaluating different materials and production options can help find the most cost-effective solution.
To sum up, the cost of high-speed mixed media PCB is a complex issue affected by many factors. By gaining a deeper understanding of the impact of factors such as size, complexity, materials and quantity on costs, production costs can be better budgeted and optimized to achieve the best balance of costs without sacrificing quality.
What material is PCB made of?
PCB (Printed Circuit Board) is a vital component of modern electronic equipment. They carry electronic components and provide stable electrical connections. PCBs are usually composed of several key materials, including substrate materials, conductive path materials, and insulation protection materials.
First of all, the substrate material is the foundation of the PCB, which provides the support structure for the entire circuit. One of the most common substrate materials is fiberglass reinforced epoxy, also known as FR-4. FR-4 has good mechanical strength and heat resistance and is suitable for most application scenarios. In addition to FR-4, there are other types of substrate materials, such as ceramic substrates and metal substrates, that provide higher performance and stability in specific applications.
Secondly, the conductive paths of the PCB are made of copper. Copper was chosen as the material for the conductive paths because it has good electrical conductivity and mechanical strength, and is relatively easy to process. During the PCB manufacturing process, copper is deposited on the surface of the substrate and chemically etched to form the required conductive pattern.
Finally, the insulating protective layer of the PCB is usually composed of solder film. The solder film covers the surface of the PCB to insulate and protect the conductive path to prevent short circuits and damage to the circuit from the external environment. Solder mask is usually a high temperature resistant polymer material such as polyimide (PI) or polyamide (PA).
In addition to these common materials, modern PCB manufacturing also uses some advanced materials to meet specific design needs. For example, flexible substrates use flexible polyester films as the substrate material, which can be used in applications that require bending or folding. Metal substrates use metal substrates to replace traditional substrate materials, providing better heat dissipation performance and mechanical stability, and are suitable for high-power and high-frequency circuit design.
In summary, PCB material selection is critical to the performance and stability of the circuit. Understanding the characteristics and application scenarios of different materials can help engineers make better choices during the design and manufacturing process, thereby ensuring the performance and reliability of electronic devices.
Who makes PCBs?
The manufacturing of PCBs is a highly specialized and sophisticated process, often undertaken by a range of specialized suppliers and manufacturers. Among these suppliers, some are factories specializing in PCB manufacturing, while others are comprehensive electronic manufacturing service providers.
In the current market, more and more companies tend to cooperate with professional PCB manufacturers to ensure product quality and production efficiency. These manufacturers have advanced equipment and technology, as well as extensive experience, to meet various design requirements and project sizes.
Many companies choose to work with outside PCB manufacturers rather than produce PCBs in-house. This cooperation model helps reduce costs, reduce production time, and ensure product quality and reliability. For these companies, choosing the right PCB manufacturer is crucial.
In our company, our products remain competitive in the market. We have advanced manufacturing equipment, strict quality control system and professional technical team.
What are the 5 qualities of great customer service?
Excellent customer service is crucial in the modern business environment. It is not only a service attitude, but also a key factor in the long-term development of a company and customer loyalty. Here are five key qualities of great customer service:
Responsiveness: Excellent customer service starts with prompt responses to customers. When customers have questions, complaints or needs, timely and effective responses can help build trust and enhance customer satisfaction with the company. By responding quickly to emails, phone calls, or social media messages, businesses can enhance the customer experience by demonstrating that they value their concerns.
Empathy: Empathy is key to understanding and building an emotional connection with your customers. By listening to customers’ needs and feelings, and understanding their pain points and challenges, companies can better meet customer expectations and provide personalized solutions. Showing empathy when interacting with customers can increase customer loyalty to your business and build strong, long-term relationships.
Reliability: Reliability is the cornerstone of customer service and is demonstrated by consistently delivering on promises and commitments made to customers. Whether delivering products, providing services, or solving problems, customers want to be able to rely on the stability and reliability of your business. By maintaining consistent quality standards and service levels, businesses can build credibility and earn the trust and respect of their customers.
Communication: Clear and transparent communication is key to building good customer relationships. Enterprises should ensure smooth communication with customers, convey important information in a timely manner, explain product features and service processes, and provide useful feedback and suggestions. By proactively communicating with customers, companies can eliminate misunderstandings, solve problems, and improve customer satisfaction.
Problem-solving skills: Actively solving customer problems and challenges is the key to quality customer service. Enterprises should establish an effective problem-solving mechanism, respond quickly to customer complaints and feedback, and take appropriate measures to solve problems to ensure customer satisfaction and loyalty. Through the ability to handle problems, companies can not only regain the trust of customers, but also establish a good corporate image and attract more customers’ attention and support.
To sum up, high-quality customer service is not only a corporate responsibility, but also a manifestation of competitive advantage and brand value. Through responsiveness, empathy, reliability, communication and problem solving, businesses can earn the trust and loyalty of their customers and achieve continued business growth and success.
Frequently Asked Questions
What is the significance of impedance control in high-speed mixed dielectric PCB manufacturing?
Impedance control is critical in high-speed mixed dielectric PCB manufacturing as it ensures consistent signal integrity by maintaining the desired electrical characteristics throughout the transmission lines. Precise impedance matching reduces signal distortion, minimizes reflections, and enhances overall system performance, particularly in applications with high data rates or frequency-sensitive components.
How are signal integrity issues addressed in high-speed mixed dielectric PCBs?
Signal integrity issues in high-speed mixed dielectric PCBs are addressed through careful design considerations and layout optimization. Techniques such as controlled impedance routing, differential signaling, proper ground plane design, and minimizing signal discontinuities help mitigate issues like signal reflections, crosstalk, and electromagnetic interference, ensuring reliable data transmission and system operation.
What factors affect the cost of high-speed mixed dielectric PCBs?
The cost of high-speed mixed dielectric PCBs is influenced by various factors, including board size, layer count, complexity of the circuit design, choice of materials, surface finish, and production volume. Additional costs may arise from specialized manufacturing processes, such as impedance control, blind/buried vias, or controlled-depth drilling, which are often required for high-speed applications.
Can high-speed mixed dielectric PCBs be manufactured using environmentally friendly practices?
Yes, high-speed mixed dielectric PCBs can be manufactured using environmentally friendly practices. Initiatives such as using lead-free solder, recycling waste materials, reducing energy consumption during production, and adhering to regulatory standards for hazardous substances contribute to sustainable PCB manufacturing. Additionally , selecting eco-friendly substrate materials and implementing efficient waste management processes to further minimize environmental impact.
How do advancements in PCB manufacturing technology impact high-speed mixed dielectric PCBs?
Advancements in PCB manufacturing technology continually enhance the performance, reliability, and cost-effectiveness of high-speed mixed dielectric PCBs. Innovations such as finer trace widths and spacing, improved materials with lower loss tangents, and advanced fabrication techniques enable higher signal speeds, tighter impedance control, and greater design flexibility, meeting the evolving demands of modern electronic systems.