Multilayer ceramic PCB manufacturing. Ceramic PCB and ceramic package substrates Vendor. We offer ceramic boards from 1 layer to 22 layers.
Multilayer ceramic printed circuit boards (PCBs) are a core component of today’s electronics field, undertaking the important task of connecting and supporting various components of electronic equipment. It is crucial for engineers and electronics enthusiasts to understand the manufacturing process, materials and costs of multilayer ceramic PCBs, as well as master their design methods. By deeply understanding the characteristics and processes of multilayer ceramic PCBs, we can better apply its advantages and promote the development of electronic technology.
What is a multilayer ceramic PCB?
Multilayer ceramic PCB (Printed Circuit Board) is a printed circuit board that forms multi-layer conductive paths on a ceramic substrate. Multilayer ceramic PCBs offer a range of significant advantages over traditional fiberglass-reinforced epoxy (FR-4)-based PCBs, making them ideal for many high-performance electronic applications.
First of all, one of the biggest features of multilayer ceramic PCB is its excellent temperature stability. Ceramic substrates exhibit excellent stability and tolerance in high-temperature environments and are not easily affected by temperature changes. This makes multilayer ceramic PCB particularly suitable for electronic equipment in high-temperature environments, such as automotive electronics, aerospace and other fields.
Secondly, multilayer ceramic PCB has excellent electrical properties. The dielectric constant of the ceramic substrate is lower, the signal transmission speed is faster, and the signal loss is smaller, thereby improving the performance and stability of the circuit. This excellent electrical property makes multilayer ceramic PCB the first choice for high-frequency and high-speed electronic equipment.
In addition, multi-layer ceramic PCBs also have excellent mechanical strength and durability. The ceramic material itself has high hardness and pressure resistance, and can effectively resist the impact and vibration of the external environment, thus protecting the components on the circuit board from damage.
In addition to the above characteristics, multi-layer ceramic PCBs also have good chemical resistance and corrosion resistance, and can maintain stable performance in harsh working environments. This gives it unique advantages in some special application scenarios, such as chemical equipment, medical equipment and other fields.
In summary, multilayer ceramic PCBs play an important role in many high-performance electronic applications due to their excellent temperature stability, excellent electrical properties, excellent mechanical strength and durability, as well as good chemical resistance and corrosion resistance. important role. With the continuous advancement of technology and the continuous expansion of application fields, multi-layer ceramic PCB will play a more important role in future development.
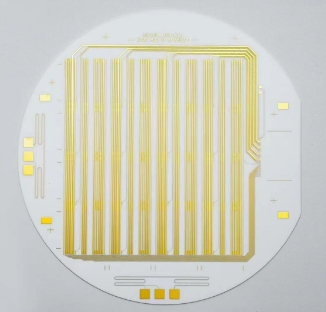
Multilayer ceramic PCB
How to design multilayer ceramic PCB?
Designing a multi-layer ceramic PCB is a complex and precise job, requiring engineers to make full use of professional software for schematic capture, component placement, routing and layout design. These software not only provide intuitive interfaces and powerful functions, but also help engineers consider key factors such as functionality, space utilization and manufacturability during the design process.
First, engineers use software to capture the schematic diagram and convert the circuit schematic diagram into a visual circuit diagram. At this stage, they can add and connect various components, such as resistors, capacitors, transistors, etc., to build a complete circuit structure. Through schematic capture, engineers can clearly understand the functions and connection relationships of the circuit, laying the foundation for subsequent layout and wiring.
Next is the component layout stage, where engineers place various components reasonably on the PCB board. In this process, they need to consider the distance between components, mutual interference, and the overall layout structure to ensure the stability and performance of the circuit. Professional software provides a wealth of layout tools and functions to help engineers achieve the best component layout solution.
Routing is one of the key steps in designing multilayer ceramic PCBs. Engineers need to implement the circuit connections in the schematic diagram on the PCB board through wires or copper foil. Through the automatic wiring and manual adjustment functions provided by the software, engineers can efficiently complete the wiring of complex circuits. During the wiring process, they need to consider factors such as signal transmission speed, power loss, and impedance matching to ensure the stability and performance of the circuit.
Finally, engineers optimize the layout, taking into account the actual manufacturing process of the PCB board. They need to adjust component locations and routing paths to minimize manufacturing costs and increase production efficiency. Through the visualization tools and simulation analysis provided by the software, engineers can quickly evaluate the advantages and disadvantages of different layout solutions and choose the best design solution.
To sum up, designing multi-layer ceramic PCB requires engineers to make full use of professional software for schematic capture, component layout, wiring and layout design. Through reasonable layout and wiring solutions, engineers can optimize circuit functions and improve the performance and reliability of PCB boards.
What is the manufacturing process of multilayer ceramic PCB?
The multilayer ceramic PCB manufacturing process is a complex and precise process involving multiple key steps. Each step is crucial and has a direct impact on the quality and reliability of the finished product.
First, the first step in manufacturing a multilayer ceramic PCB is to select a suitable substrate material. Ceramic substrates are usually made of materials such as aluminum oxide, aluminum nitride or zirconium oxide, which have good high temperature resistance and mechanical strength and are suitable for high-performance electronic applications.
Next is the layer stacking stage. In this step, the selected ceramic substrates are cut to the required size and stacked into a multi-layer structure according to the design requirements. The accuracy of the layup is crucial for subsequent processing and assembly.
This is followed by the Ceramic Lamination process. In this step, the multi-layer ceramic substrate is placed under high temperature and pressure, and the layers are tightly combined through pressing and sintering to form an integrated multi-layer structure. This ensures the stability and mechanical strength of the PCB.
Shaping is the next step, where the ceramic substrate is machined into the desired shape and size. This may involve machining processes such as cutting, grinding and drilling to meet design requirements and dimensional specifications.
Soldering is one of the key steps in connecting electronic components to multilayer ceramic PCBs. Through surface mounting technology (SMT) or plug-in mounting technology (Through-Hole Technology, THT), electronic components are precisely mounted on the surface or through-holes of the PCB and fixed by soldering.
Drilling is used to create through holes and pads on the PCB. These holes are used for the pins of electronic components to pass through and connect to the circuit. The precise location and size of the drilled holes are critical to the correct function of the circuit.
The last is the Final Inspection stage. In this step, the manufactured multi-layer ceramic PCB will undergo strict quality control and inspection to ensure that it meets the design specifications and quality standards. This may include visual inspection, electrical performance testing and reliability verification, etc.
In general, the manufacturing process of multi-layer ceramic PCB requires a high level of technology and craftsmanship. Precise execution and strict quality control are the keys to ensuring the quality and reliability of the finished product. Through careful design and execution of these critical steps, manufacturers are able to produce high-quality multilayer ceramic PCB products suitable for a variety of high-performance electronic applications.
How much does a multilayer ceramic PCB cost?
The cost of multilayer ceramic PCBs varies based on factors such as size, complexity, materials, and quantity. For engineers and production teams, understanding these cost drivers is critical for budget planning and optimization of production costs.
First of all, the size of multi-layer ceramic PCB is one of the important factors affecting the cost. Larger PCB sizes require more substrate material and wire length, so the cost increases accordingly. Additionally, complex designs may require more layers and fine wiring, further increasing manufacturing costs.
Secondly, the complexity of PCB also affects the cost. Complex circuit designs may require more layers and subtle wiring to meet the functionality and performance requirements of electronic devices. This complexity increases process and material costs in the manufacturing process.
The choice of materials will also directly affect the cost of multilayer ceramic PCBs. Materials such as high-quality ceramic substrates, high-quality copper wires, and reliable pads often increase costs, but they also increase PCB performance and reliability.
Finally, production quantity has a significant impact on costs. Generally speaking, high-volume production can achieve economies of scale and reduce the manufacturing cost of each PCB. Conversely, low-volume production or custom orders may result in increased costs because more manpower and resources are required to adjust the production process.
Therefore, for the design and manufacturing process of multi-layer ceramic PCBs, engineers and manufacturers need to comprehensively consider the above factors and make informed decisions based on project needs and budget. By optimizing design, material selection and production processes, they can minimize costs while ensuring product quality and performance meet expected levels.
What materials are used in multilayer ceramic PCBs?
Multilayer ceramic PCB (Printed Circuit Board) is an electronic component that forms multi-layer conductive paths on a ceramic substrate. This PCB consists of multiple alternating stacks of insulating and conductive layers, using ceramic as the substrate to achieve higher temperature stability and reliability. When manufacturing multi-layer ceramic PCBs, the materials used are crucial, and below we will introduce these key materials in detail.
Ceramic substrate is one of the key materials for manufacturing multi-layer ceramic PCB. It is usually made of ceramic materials such as aluminum oxide (Alumina) or aluminum nitride (Aluminum Nitride). These materials have excellent thermal conductivity and mechanical strength, which can effectively disperse the heat generated in the circuit and improve the stability and reliability of the circuit. In addition, ceramic substrates also have good insulation properties and can effectively prevent short circuits and leakage between circuits.
Copper conductive layers are another important component in multilayer ceramic PCBs. It is located on the surface of the ceramic substrate and forms a conductive path through processes such as chemical deposition or electroplating. Copper has good electrical conductivity and welding properties, can effectively transmit electric current, and firmly connect with electronic components. In multilayer ceramic PCBs, multiple copper conductive layers are often used to enable the design and routing of complex circuits.
Soldering pads are key components for connecting electronic components on multilayer ceramic PCBs. It is located on the surface of the copper conductive layer and is used to solder the pins or solder balls of electronic components. The pad is usually made of gold-plated or tin-plated copper material, which has good electrical conductivity and corrosion resistance, ensuring a stable and reliable soldering connection. In high-temperature environments, the pads can effectively resist oxidation and inter-metal diffusion, maintaining the stability and reliability of the welded joints.
To sum up, multi-layer ceramic PCB usually uses materials such as ceramic substrate, copper conductive layer and pad. These materials have excellent thermal conductivity, electrical properties and high temperature resistance, making them suitable for high-performance electronic applications. By rationally selecting and designing these materials, stable and reliable operation of multi-layer ceramic PCBs can be achieved to meet the needs of various high-performance electronic devices.
Who will make the multilayer ceramic PCB?
The manufacturing of multilayer ceramic PCBs is a complex and precise process that requires experienced manufacturers to ensure quality and reliability. In the current market, there are many professional PCB manufacturers offering multi-layer ceramic PCB manufacturing services, and some of these suppliers can even provide customized solutions to meet customers’ specific technical and performance requirements.
For many companies, choosing the right supplier is crucial. In this regard, our company proudly offers multi-layer ceramic PCB manufacturing services, building on years of experience and superior technical prowess. As a professional PCB manufacturer, our company is committed to providing customers with high-quality, high-performance multi-layer ceramic PCBs and is known for its excellent customer service.
The company has advanced production equipment and technical teams that can meet the manufacturing needs of various complex circuit boards. We focus on process control and quality management, and adopt strict production processes and inspection standards to ensure that every multi-layer ceramic PCB can meet customer expectations.
In addition to its technical prowess, the company is known for its flexible production capabilities and fast delivery times. We are able to provide customized solutions according to customer needs and complete order delivery in the shortest possible time, saving customers valuable time and costs.
At our company, customer satisfaction is always our goal. Our professional team will track the order progress throughout the entire process and respond to customer needs and feedback in a timely manner to ensure that customers receive the best service experience.
To sum up, as a professional PCB manufacturer, our company has the technology and experience required to manufacture multi-layer ceramic PCBs. We are committed to providing customers with high-quality, high-performance products to meet the needs and expectations of different customers. We look forward to cooperating with customers from all walks of life to jointly promote the development and application of electronic technology.
What are the 5 qualities of great customer service?
Excellent customer service is one of the keys to a successful business. In a highly competitive market, by providing excellent customer service, companies can build a good brand reputation and win the trust and loyalty of customers. Here are five important qualities of great customer service:
Being able to respond promptly and effectively to customer inquiries and concerns is the foundation of excellent customer service. Customers expect timely support and solutions when they need help or have questions. Therefore, responding quickly to customer needs not only improves customer satisfaction, but also strengthens the relationship between the customer and the business.
Empathy is key to understanding your customers’ needs. Excellent customer service is not just about providing solutions, it is about making customers feel respected and cared for through compassion and understanding. Listening to customers’ problems and concerns and actively working to help them solve them can enhance customers’ trust and loyalty to the company.
In customer relationships, reliability is crucial. Consistently delivering on promises and commitments to customers can establish a company’s credibility and enhance customers’ trust in the company. Customers expect to be able to rely on businesses to provide stable and reliable services, so reliability is one of the important attributes of good customer service.
Clear and transparent communication is key to building good customer relationships. Maintaining good communication with customers throughout the service process ensures that customers understand the progress of the service and provide timely feedback. Effective communication not only avoids misunderstandings and dissatisfaction, but also enhances customer trust and satisfaction with your business.
Proactive problem solving is at the heart of great customer service. Customers may encounter various problems and challenges, and it is the business’s responsibility to try its best to solve these problems and ensure customer satisfaction. Through flexible solutions and ongoing support, companies can earn the respect and trust of their customers, leading to long-term relationships.
Overall, great customer service is an integral part of a successful business. Through traits such as responsiveness, empathy, reliability, communication, and problem-solving, businesses can build a strong brand image, win the trust and loyalty of their customers, and achieve sustained growth and development.
Frequently Asked Questions
What are the benefits of using multilayer ceramic PCBs compared to traditional FR-4 PCBs?
Multilayer ceramic PCBs offer several advantages over traditional FR-4 PCBs. They provide higher temperature stability, improved electrical performance, and enhanced reliability, making them ideal for high-frequency and high-power applications. Additionally, multilayer ceramic PCBs exhibit excellent thermal conductivity, allowing for efficient heat dissipation and enabling the design of compact and reliable electronic systems.
How do you ensure the manufacturability of multilayer ceramic PCB designs?
Ensuring the manufacturability of multilayer ceramic PCB designs involves collaborating closely with PCB manufacturers and adhering to design guidelines tailored to ceramic substrates. Design considerations such as minimum trace widths, minimum annular ring sizes, and appropriate layer stackups are critical to facilitating the fabrication process and achieving high-quality results.
Can multilayer ceramic PCBs be used in harsh environments?
Yes, multilayer ceramic PCBs are well-suited for harsh environments due to their rugged construction and excellent thermal and mechanical properties. They offer superior resistance to temperature extremes, moisture, chemicals, and mechanical stress compared to conventional PCB materials, making them suitable for aerospace, automotive, military, and industrial applications where reliability is paramount.
What are the key factors influencing the cost of multilayer ceramic PCBs?
The cost of multilayer ceramic PCBs is influenced by various factors, including board size, layer count, material quality, surface finish, and production volume. Larger board sizes, higher layer counts, and advanced materials typically result in higher manufacturing costs. Additionally, factors such as assembly complexity, lead time requirements, and supplier capabilities can impact overall costs.