Aluminum Oxide PCBAL203 PCB Manufacturer.”Aluminum Oxide PCB, or Al2O3 PCB, is crafted by leading manufacturers specializing in advanced ceramic substrates. These PCBs excel in high thermal conductivity and electrical insulation, crucial for demanding electronic applications.
Aluminum Oxide (Al2O3) PCBs, also known as Aluminum Oxide Printed Circuit Boards, are advanced circuit boards that utilize aluminum oxide as the primary substrate material. This unique material offers excellent thermal conductivity, electrical insulation, and mechanical stability, making it ideal for high-performance applications. Aluminum Oxide PCBs are used in various industries, including aerospace, automotive, medical, and consumer electronics, where high reliability and efficiency are paramount.
What is an Aluminum Oxide PCB?
An Aluminum Oxide PCB is a type of printed circuit board that uses aluminum oxide (Al2O3) as its substrate material. Aluminum oxide is a ceramic material known for its exceptional thermal and electrical properties. It provides high thermal conductivity, excellent electrical insulation, and superior mechanical strength, making it suitable for demanding applications where heat dissipation and reliability are critical.
The use of aluminum oxide in PCBs allows for effective thermal management, reducing the risk of overheating and enhancing the performance and lifespan of electronic components. These PCBs are often used in high-power and high-frequency applications where traditional materials like FR4 may not provide adequate performance.
Aluminum Oxide PCB Design Reference Guide
Designing Aluminum Oxide PCBs involves several critical considerations to ensure optimal performance and reliability. The following sections provide an overview of the key aspects involved in the design and application of these substrates.
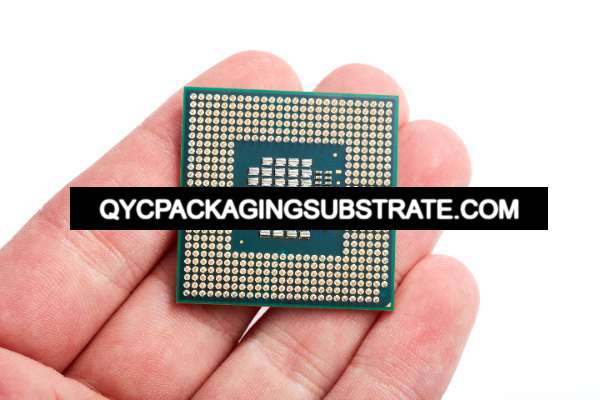
Aluminum Oxide PCBAL203 PCB Manufacturer
The materials used in Aluminum Oxide PCBs are selected for their superior electrical, thermal, and mechanical properties:
Aluminum Oxide (Al2O3): Aluminum oxide is the primary substrate material, offering high thermal conductivity, excellent electrical insulation, and robust mechanical strength. It ensures efficient heat dissipation and reliable performance in high-power applications.
Copper: High-purity copper is used for the conductive layers, providing excellent electrical conductivity and reliability. The thickness of the copper layers is chosen based on the current-carrying requirements and signal integrity considerations.
Dielectric Material: High-performance dielectric materials are used between the copper layers to provide electrical insulation and support high-frequency signal transmission.
Adhesives: Advanced adhesives are used to bond the layers together, ensuring mechanical stability and minimizing signal loss.
Several key considerations must be addressed during the design phase:
Impedance Control: Precise impedance control is essential for maintaining signal integrity, especially at high frequencies. This involves careful design of the signal traces and the use of controlled impedance materials.
Thermal Management: Effective thermal management is crucial for high-performance applications. The design must incorporate thermal vias, heat sinks, or other techniques to efficiently dissipate heat generated by high-power components.
Mechanical Stability: The substrate must provide robust mechanical support to withstand thermal cycling and mechanical stresses during operation.
Reliability: Long-term reliability is ensured through the use of high-quality materials and precise manufacturing processes, preventing issues such as delamination and warping.
What Materials are Used in Aluminum Oxide PCBs?
Materials used in Aluminum Oxide PCBs are selected for their complementary properties to enhance the overall performance of the substrate:
Aluminum Oxide (Al2O3): The primary substrate material, offering high thermal conductivity, excellent electrical insulation, and robust mechanical strength.
Copper: High-purity copper is used for the conductive layers, providing excellent electrical Dielectric Material: High-performance dielectric materials are used between the copper layers to provide electrical insulation and support high-frequency signal transmission.
Adhesives: Advanced adhesives are used to bond the layers together, providing mechanical stability and minimizing signal loss.
What Size are Aluminum Oxide PCBs?
The size of Aluminum Oxide PCBs varies depending on the application and specific design requirements:
Thickness: The overall thickness of Aluminum Oxide PCBs can range from a few hundred micrometers to several millimeters, depending on the number of layers and the application requirements.
Dimensions: The length and width of the substrates are determined by the size of the components and the layout of the system. They can range from small form factors for compact devices to larger substrates for more complex electronic systems.
The Manufacturing Process of Aluminum Oxide PCBs
The manufacturing process of Aluminum Oxide PCBs involves several precise and controlled steps to ensure high quality and performance:
High-quality base materials, such as copper-clad laminates and aluminum oxide substrates, are selected and prepared for processing. The materials are cleaned and treated to remove any impurities and ensure a smooth surface.
The dielectric material is applied to the substrate in multiple layers, with each layer being patterned and cured to form the desired circuit patterns. This process is repeated to build up the required number of layers, ensuring high-density interconnects and excellent electrical performance.
Microvias and through-holes are drilled into the substrate to create electrical connections between the layers. These vias are then plated with copper to ensure reliable electrical conductivity and robust mechanical support.
The substrate surface is finished with a high-precision solder mask to protect the underlying circuitry and provide a smooth surface for component mounting. This step also includes the application of surface finishes, such as ENIG (Electroless Nickel Immersion Gold) or OSP (Organic Solderability Preservative), to enhance solderability and corrosion resistance.
After fabrication, the substrates are assembled with electronic components. Rigorous testing is conducted to ensure that the substrates meet all design specifications and performance requirements. This includes electrical testing, thermal cycling, and mechanical stress testing to verify the reliability and durability of the substrates.
The Application Area of Aluminum Oxide PCBs
Aluminum Oxide PCBs are used in a wide range of high-performance electronic applications:
In consumer electronics, Aluminum Oxide PCBs support high-performance and compact devices such as smartphones, tablets, and wearable technology. The substrates provide the necessary electrical and thermal performance to ensure the reliable operation of these devices.
In medical devices, Aluminum Oxide PCBs support high-frequency signal processing and reliable operation in various diagnostic and therapeutic equipment. These substrates ensure precise and accurate signal transmission, making them ideal for use in imaging systems, monitoring devices, and surgical instruments.
In automotive applications, Aluminum Oxide PCBs are used in various electronic systems, including infotainment, navigation, and advanced driver-assistance systems (ADAS). These substrates offer high reliability and performance, enabling advanced functionalities and efficient operation in automotive environments.
In aerospace and defense applications, Aluminum Oxide PCBs provide robust performance in harsh environments and under extreme conditions. These substrates are used in various aerospace and defense systems, such as radar, communication, and navigation systems, ensuring reliable operation and long-term durability.
In industrial automation, Aluminum Oxide PCBs are used in various control and automation systems. These substrates offer high reliability and performance, enabling advanced functionalities and efficient operation in industrial environments.
What are the Advantages of Aluminum Oxide PCBs?
Aluminum Oxide PCBs offer several advantages that make them indispensable in high-performance electronic applications:
High Thermal Conductivity: Aluminum Oxide PCBs provide efficient heat dissipation, reducing the risk of overheating and enhancing the performance and lifespan of electronic components.
Electrical Insulation: The high dielectric strength of aluminum oxide ensures excellent electrical insulation, preventing short circuits and ensuring reliable operation.
Mechanical Strength: The robust mechanical properties of aluminum oxide provide durable and stable substrates that can withstand thermal cycling and mechanical stresses.
Miniaturization: These substrates enable the integration of complex circuitry in a compact form factor, supporting the trend towards smaller and more powerful electronic devices.
Reliability: Aluminum Oxide PCBs provide long-term reliability through high-quality materials and precise manufacturing processes, ensuring stable operation of electronic devices.
FAQ
What are the key considerations in designing an Aluminum Oxide PCB?
Key considerations include material properties, layer stack-up, impedance control, thermal management, and mechanical stability. The design should ensure optimal electrical performance, efficient heat dissipation, and long-term reliability.
How do Aluminum Oxide PCBs differ from traditional PCBs?
Aluminum Oxide PCBs use aluminum oxide as the substrate material, providing superior thermal conductivity, electrical insulation, and mechanical strength compared to traditional PCBs, which typically use FR4 or other materials.
What is the typical manufacturing process for Aluminum Oxide PCBs?
The process involves material preparation, layer build-up, drilling and plating, surface finishing, and assembly and testing. Each step is carefully controlled to ensure high quality and performance.
What are the main applications of Aluminum Oxide PCBs?
Aluminum Oxide PCBs are used in a wide range of applications, including consumer electronics, medical devices, automotive, aerospace, and industrial automation. They provide advanced functionality and reliability in these demanding environments.