Antenna Cavity PCBs Manufacturer.As a leading Antenna Cavity PCBs manufacturer, we specialize in designing and producing high-precision PCBs with integrated antenna cavities for advanced wireless communication systems. Our state-of-the-art manufacturing process ensures superior signal integrity, reduced interference, and enhanced performance, making us the preferred choice for cutting-edge applications in telecommunications, aerospace, and IoT industries.
Antenna cavity PCBs (Printed Circuit Boards) are specialized circuit boards designed for high-frequency applications where precision and performance are critical. These PCBs are used in applications such as telecommunications, radar systems, and wireless communication devices, where they provide excellent signal integrity and efficient radiation characteristics. The unique design and materials used in antenna cavity PCBs enable them to meet the stringent requirements of these advanced technologies.
What is an Antenna Cavity PCB?
An antenna cavity PCB is a type of printed circuit board that incorporates cavities or recesses within its structure to house antenna elements and other high-frequency components. These cavities are designed to enhance the performance of the antenna by providing a controlled environment that minimizes signal loss and interference. The use of cavities allows for better control of the electromagnetic fields, resulting in improved radiation patterns and overall antenna efficiency.
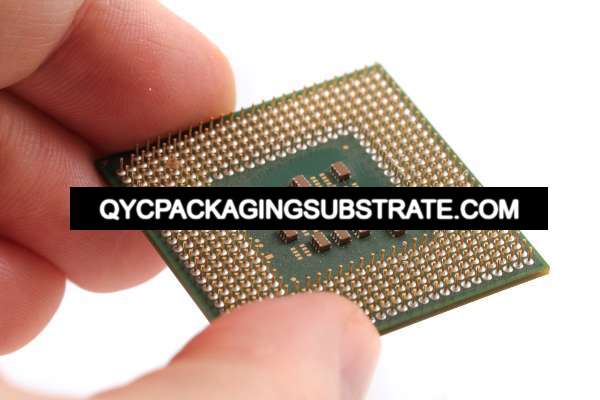
Antenna Cavity PCBs Manufacturer
Antenna cavity PCBs are typically made from materials with low dielectric loss and high thermal stability to ensure reliable performance at high frequencies. Common materials used include Rogers, Taconic, and PTFE (Polytetrafluoroethylene)-based laminates. These materials help maintain signal integrity and reduce losses, making them ideal for high-frequency applications.
Antenna Cavity PCB Design Reference Guide
Designing an antenna cavity PCB involves several critical considerations to ensure optimal performance and reliability. The following sections outline the key aspects of antenna cavity PCB design.
The choice of materials is crucial for the performance of antenna cavity PCBs. Key materials include:
Rogers Laminates: Known for their low dielectric loss and high thermal stability, Rogers laminates are widely used in high-frequency applications.
Taconic Laminates: These materials offer excellent performance in terms of dielectric properties and thermal stability, making them suitable for high-frequency and high-power applications.
PTFE-Based Laminates: PTFE-based materials provide low dielectric loss and stable performance over a wide range of frequencies and temperatures.
Metallic Layers: Conductive metals such as copper are used for creating the signal traces and antenna elements. These layers must be carefully selected and applied to maintain adhesion and conductivity.
What Materials are Used in Antenna Cavity PCBs?
Materials used in antenna cavity PCBs are selected for their complementary properties to enhance the overall performance of the substrate:
Rogers Laminates: Provide low dielectric loss and high thermal stability, making them ideal for high-frequency applications.
Taconic Laminates: Offer excellent performance in terms of dielectric properties and thermal stability.
PTFE-Based Laminates: Provide low dielectric loss and stable performance over a wide range of frequencies and temperatures.
Copper: Used for creating the signal traces and antenna elements, copper provides excellent electrical conductivity and reliability.
Dielectric Filling Materials: Used to fill the cavities, dielectric materials help control the electromagnetic properties and improve performance.
What Size are Antenna Cavity PCBs?
The size of antenna cavity PCBs varies depending on the application and specific design requirements:
Thickness: The thickness of antenna cavity PCBs can range from a few hundred micrometers to several millimeters, depending on the thermal and mechanical requirements.
Dimensions: The length and width of the PCBs are determined by the size of the components and the layout of the system. They can range from small form factors for compact devices to larger substrates for complex electronic systems.
The Manufacturing Process of Antenna Cavity PCBs
The manufacturing process of antenna cavity PCBs involves several precise and controlled steps to ensure high quality and performance:
High-quality laminates and metal sheets are selected and prepared for processing. The materials are cleaned and treated to remove any impurities and ensure a smooth surface.
The cavities and holes are drilled or routed into the PCB using precision machinery. This step ensures that the cavities meet the specific size and shape requirements of the design.
The layers of the PCB are laminated together using heat and pressure. This step ensures that the layers are bonded together securely and that the cavities are properly formed.
Conductive layers are deposited onto the PCB using techniques such as sputtering, electroplating, or screen printing. These layers form the electrical pathways and antenna elements required for the specific application.
After fabrication, the PCB is assembled with any necessary components and connectors. Rigorous testing is conducted to ensure that the PCB meets all design specifications and performance requirements. This includes testing for signal integrity, electromagnetic compatibility, and mechanical stability.
The Application Area of Antenna Cavity PCBs
Antenna cavity PCBs are used in a wide range of high-performance applications:
In telecommunications, antenna cavity PCBs are used in base stations, repeaters, and other communication infrastructure. These PCBs provide reliable and efficient performance in high-frequency communication systems.
In radar systems, antenna cavity PCBs are used in both military and civilian applications. These PCBs provide precise control of the electromagnetic fields, ensuring accurate and reliable radar performance.
In wireless communication devices, antenna cavity PCBs are used in smartphones, tablets, and other portable devices. These PCBs provide efficient radiation characteristics and reliable performance in compact form factors.
In aerospace applications, antenna cavity PCBs are used in satellite communication systems and other high-frequency applications. These PCBs provide robust performance in harsh environments and under extreme conditions.
In the automotive industry, antenna cavity PCBs are used in advanced driver-assistance systems (ADAS) and other communication and radar systems. These PCBs provide reliable and efficient performance in demanding automotive environments.
What are the Advantages of Antenna Cavity PCBs?
Antenna cavity PCBs offer several advantages that make them indispensable in high-performance applications:
High Signal Integrity: Antenna cavity PCBs provide excellent signal integrity, minimizing signal loss and interference.
Efficient Radiation Characteristics: The use of cavities allows for better control of the electromagnetic fields, resulting in improved radiation patterns and overall antenna efficiency.
Thermal Management: Antenna cavity PCBs provide efficient thermal management, dissipating heat effectively and maintaining the performance of high-power components.
Mechanical Stability: Antenna cavity PCBs offer robust mechanical support, withstanding thermal cycling and mechanical stresses during operation.
Versatility: Antenna cavity PCBs can be used in a wide range of applications, from telecommunications to aerospace and automotive systems.
FAQ
What are the key considerations in designing an antenna cavity PCB?
Key considerations include material selection for thermal and electrical performance, cavity design for optimal antenna performance, layer stack-up for thermal management and electrical routing, and ensuring mechanical stability and reliability.
How do antenna cavity PCBs differ from other PCB types?
Antenna cavity PCBs incorporate cavities within their structure to enhance the performance of the antenna elements. This provides better control of the electromagnetic fields, resulting in improved signal integrity and radiation characteristics compared to standard PCBs.
What is the typical manufacturing process for antenna cavity PCBs?
The process involves material preparation, drilling and routing, layer lamination, metallization, and rigorous assembly and testing to ensure high quality and performance.
What are the main applications of antenna cavity PCBs?
Antenna cavity PCBs are used in telecommunications, radar systems, wireless communication devices, aerospace, and automotive applications, providing advanced functionality and reliability in high-frequency environments.