Aviation Substrate Manufacturer. High frequency and high speed materials Aerospace PCB, Satellite PCB or Military PCBs. We offer IPC Class III PCBs from 2 layer to 50 layers.
In the field of modern aviation, the continuous development of technology has always been the engine driving the industry forward. Aviation Substrate, as an important part of the flight system, is gradually becoming one of the keys to realizing flight technology innovation. This article will comprehensively explore the definition, design guidelines, materials, manufacturing processes, application areas, advantages, and FAQs of aerospace substrates to help you gain a deeper understanding of this critical aerospace technology.
What is Aviation Substrate?
Aviation Substrate, as an important part of the avionics system, plays a vital role driven by modern aviation technology. But, to most people, what exactly is an aerospace substrate? Let’s dig a little deeper.
Aerospace substrate is a basic material used in avionics systems. Its main function is to carry various electronic components and provide electrical connections. This means that the aviation substrate is not just a simple circuit board, but an indispensable core component in the electronic system. The structure of aerospace substrates typically consists of multiple layers of composite materials that are carefully selected and combined to ensure reliable operation of avionics systems in extreme environments.
Generally speaking, aerospace substrates need to have excellent performance characteristics, including high temperature resistance, impact resistance, and corrosion resistance. This is because avionics systems are often exposed to extreme working environments, such as high altitude temperatures, airborne vibrations, etc. Therefore, aviation substrates must be able to maintain stable electrical connections under these harsh conditions to ensure flight safety and system reliability.
When designing aerospace substrates, engineers typically select appropriate materials and layout solutions based on specific application requirements. They need to take into account the special requirements of the flight environment and take appropriate measures to ensure the performance and reliability of aerospace substrates. In addition, aerospace substrates are often smaller in size to accommodate the compact space layout of avionics equipment.
Overall, aerospace substrates play a crucial role in modern aerospace technology. It is not only the basic material of avionics systems, but also a key guarantee for flight safety and performance. Through continuous innovation and optimization, aviation substrates will continue to play a key role in driving the aviation field towards a safer, more efficient and smarter future.
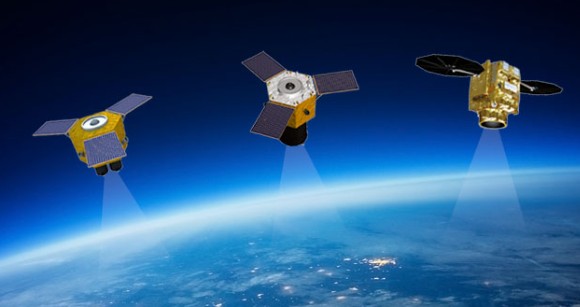
Aviation Substrate
Aviation Substrate design Reference Guide.
Designing an aerospace substrate is a crucial part of an avionics system as it must maintain reliability and stability in the harsh flight environment. In this design reference guide, we will focus on how to consider special flight environment requirements during the design process to ensure that aerospace substrates can operate normally under conditions such as high temperature, high pressure, vibration, etc.
Choosing Materials for Aerospace Applications
First, designers need to select high-performance materials suitable for aerospace applications. These materials must be able to withstand extreme temperatures and pressures and have excellent mechanical strength and corrosion resistance. Commonly used aviation substrate materials include polyimide (PI), polytetrafluoroethylene (PTFE), etc., which can maintain stability in high-temperature environments and have good electrical properties.
Special layout and connection methods
Secondly, designers need to adopt special layout and connection methods to ensure that the aerospace substrate can remain stable under vibration and impact. This may involve adopting a more compact layout with less spacing between components to reduce the impact of vibration on the circuit. In addition, using appropriate connection methods, such as welding or crimping, can ensure the stability and reliability of the connection.
Consider environmental requirements
Finally, the special requirements of the flight environment, such as high temperature and high pressure, must be fully considered during the design process. Designers need to ensure that aerospace substrates can function properly under these extreme conditions and will not suffer performance degradation or failure due to environmental factors. This may require special thermal designs to ensure the board does not overheat, and the selection of high-temperature-resistant materials to protect the electronic components.
To sum up, designing aerospace substrates requires comprehensive consideration of multiple factors such as material selection, layout design, and environmental requirements. Only after fully considering these factors can we design an aerospace substrate that can operate stably in harsh flight environments and provide solid support for the development of flight technology.
What material is used in Aviation Substrate?
As the core component of avionics systems, the choice of materials for aviation substrates is crucial. When facing the extreme challenges of the flight environment, aviation substrates need to have excellent performance and reliability to ensure flight safety and system stability. Therefore, aerospace substrates usually use high-performance composite materials, such as polyimide (PI) and polytetrafluoroethylene (PTFE).
Polyimide (PI)
Polyimide is a polymer material with extremely high temperature stability and mechanical strength. It has excellent high temperature resistance and maintains stable electrical and mechanical properties under extreme temperature conditions. This makes PI one of the ideal choices for aerospace substrates, which can work in high temperature environments for a long time without failure.
Polytetrafluoroethylene (PTFE)
Polytetrafluoroethylene (PTFE) is a material with excellent chemical resistance and a low coefficient of friction. It not only has excellent corrosion resistance, but also has excellent insulation properties and high temperature resistance. In avionics systems, PTFE is widely used in aviation substrates to ensure reliable operation of the system in harsh environments.
These high-performance composite materials not only have excellent properties such as high temperature resistance, chemical corrosion resistance and mechanical strength, but can also meet the stringent requirements for material stability and reliability of avionics systems. Their application gives aerospace substrates strong environmental resistance, allowing avionics systems to operate stably under various extreme conditions.
To sum up, the high-performance composite materials used in aerospace substrates, such as polyimide (PI) and polytetrafluoroethylene (PTFE), have excellent performance and reliability, and provide important support for the stable operation of avionics systems. Assure. As aviation technology continues to develop, we can look forward to the application of more innovative materials to further enhance the performance and functionality of aviation substrates and promote continued progress in the aviation field.
What size are Aviation Substrate?
Aerospace substrates come in a variety of sizes, depending on the specific needs and design specifications of the application. In avionics equipment, especially in flight control systems, communication systems and navigation systems, aviation substrates are widely used, so their size must adapt to the compact space layout and special functional requirements of the equipment.
Typically, aerospace substrates are smaller in size. This is to ensure that it can fit into the limited space inside the aircraft and be easily integrated into various flight electronics. Despite its small size, aviation substrates still need to ensure that they can accommodate enough electronic components and complex circuit layouts within space constraints to meet the requirements of various functions of the aircraft.
In practical applications, the size of the aerospace substrate can be customized according to the specific aircraft type and functional requirements. For example, a small drone may require a smaller sized substrate to fit within its compact fuselage space, while a large airliner may require a larger sized substrate to accommodate more electronic components and complex circuit designs.
In addition to size, the thickness of the aerospace substrate is also an important factor to consider. Since the weight and aerodynamics of an aircraft place stringent demands on its performance, the thickness of the substrate often requires a balance between lightweight and structural strength.
In general, the size of the aerospace substrate is customized based on the design and functional requirements of the aircraft. Whether it is a small drone or a large passenger aircraft, aviation substrates play a key role, providing stable and reliable electronic support for various functions of the aircraft. With the continuous development of avionics technology and the improvement of aircraft performance, the size and performance of aviation substrates will continue to be iterated and optimized to adapt to the needs and challenges of the future aviation field.
The Manufacturer Process of Aviation Substrate.
The manufacturing of aerospace substrates is a precise and complex process involving multiple steps and strict quality control to ensure that the final product meets high standards of quality and performance requirements. Below we will take an in-depth look at the manufacturing process of aerospace substrates and reveal its mysteries and subtleties.
Raw material preparation
The first step in manufacturing aerospace substrates is to prepare raw materials. High-performance composite materials, such as polyimide (PI) and polytetrafluoroethylene (PTFE), are commonly used substrate materials. These materials undergo rigorous quality inspection and testing to ensure they meet the requirements of aerospace applications.
Laminated
During the lamination process, multi-layer substrates are stacked with interlayer dielectric layers such as conductive layers and insulating layers, and high temperature and high pressure are applied to bond them together. The key to this step is to ensure that the bond between each layer is strong and that the entire substrate structure is flat and stable.
Drilling
Drilling is to form holes on the aviation substrate for wire connection and component installation. These holes need to be accurately positioned and processed to ensure the accuracy and reliability of circuit connections. High-precision CNC drilling machines and drilling processes are the key to ensuring hole quality.
Chemical processing
During the chemical processing process, the surface of the aerospace substrate may be cleaned, copper plated, gold plated, etc. to enhance its conductivity and corrosion resistance. These chemical treatments require strict control of various parameters to ensure that the treatment results meet the requirements and do not affect the performance and stability of the substrate.
Printing
Printing is to print necessary logos, patterns, text and other information on the surface of the aviation substrate. These prints need to be clearly visible and durable so that they can be accurately read and identified during flight. The printing process requires sophisticated equipment and high-quality inks to ensure that the printing effect meets standard requirements.
The manufacturing process of aerospace substrates requires strict quality control and precise process operations to ensure that the final product has excellent performance and reliability. Only by striving for excellence in every step can we produce high-quality substrates that meet the requirements of avionics systems and provide reliable guarantee for the continuous development of flight technology.
The Application area of Aviation Substrate.
As the core component of avionics systems, aviation substrates play a key role in all aspects. They are not only carriers for connecting and supporting electronic components, but also an important guarantee for flight safety and performance. The following are the specific applications of aerospace substrates in different application fields:
Flight control system
Aviation substrates play a vital role in flight control systems. They carry key components such as flight controllers, sensors, and actuators, and are responsible for transmitting control signals to realize the aircraft’s attitude control, heading adjustment and other functions. The stability and reliability of aviation substrates are crucial to the normal operation of flight control systems.
Communication Systems
In modern aviation communication systems, aviation substrates undertake important tasks such as signal processing, data transmission, and spectrum management. They work with components such as communication modules and antenna systems to achieve efficient communication between the aircraft, ground stations, and other aircraft. The high performance and stability of aviation substrates ensure the smooth flow of communication systems and provide guarantee for flight safety and information exchange.
Navigation System
Aviation substrates play a key role in navigation systems, providing positioning, navigation, map display and other functional support for aircraft. They work together with GPS receivers, inertial measurement units (IMU), map databases and other equipment to ensure that the aircraft can accurately determine its position, plan its route, and achieve safe and efficient flight. The high precision and reliability of aviation substrates are crucial to the performance of navigation systems and directly affect the navigation safety and accuracy of aircraft.
To sum up, aviation substrates play an irreplaceable role in various aspects such as flight control systems, communication systems, and navigation systems. They not only connect and support key electronic components, but also provide a reliable foundation for the normal operation of avionics equipment. With the continuous development and innovation of aviation technology, aviation substrates will continue to play a key role in promoting the field of avionics towards a safer, more efficient and smarter future.
What are the advantages of Aviation Substrate?
As a core component of avionics systems, aviation substrates have a series of significant advantages, making them an ideal choice for flight safety and reliable performance.
High temperature tolerance
Aviation substrates often face extreme temperature conditions during flight, such as high air pressure and high engine temperatures. Therefore, aerospace substrates must have excellent high temperature tolerance and be able to work stably in high temperature environments without being damaged. Aerospace substrates made of high-performance materials can withstand temperatures up to over 200°C, ensuring reliable operation of flight electronics under various extreme conditions.
Corrosion resistance
Various corrosive factors exist in the aviation environment, such as humidity, chemicals and salt spray. These corrosive factors can cause severe damage to electronic equipment, affecting its performance and lifespan. Aviation substrates have excellent corrosion resistance and can resist the erosion of corrosive substances, maintain good electrical connections and performance stability, thereby extending the service life of aviation electronic equipment.
High mechanical strength
During flight, avionics equipment may be affected by external forces such as mechanical shock, vibration, and pressure. In order to ensure flight safety and equipment stability, aviation substrates must have good mechanical strength, be able to withstand external impact and vibration, and maintain stable structure and connection status. Aerospace substrates made of high-performance composite materials have excellent mechanical strength and can maintain stability and reliability in harsh flight environments.
Ideal for aerospace substrates
Aerospace substrates are ideal for avionics systems due to their high temperature tolerance, corrosion resistance and high mechanical strength. Aerospace substrates play an integral role in flight safety and performance reliability. It can work stably in various harsh environments, ensure flight safety, and provide reliable support for the continuous progress and development of aviation technology.
In summary, the advantages of aviation substrates are obvious and will continue to promote the development of avionics technology and provide a solid foundation for the safety and reliability of future flights.
FAQ
What is the lifespan of aerospace substrates in flight electronics systems?
The life of aerospace substrates depends on multiple factors, including material selection, design quality, working environment, etc. Generally speaking, well designed and maintained aerospace substrates can last for many years in flight electronics systems, but regular inspection and maintenance are still key to maintaining system stability and reliability.
What is the cost of aerospace substrates?
The cost of aerospace substrates depends on multiple factors, including material selection, manufacturing process, dimensional complexity, etc. Compared with general electronic substrates, the cost of aerospace substrates is usually higher because they require the use of more high-temperature-resistant, high-performance materials and need to comply with more stringent aviation safety standards.
What types of aircraft can aerospace substrates be used for?
Aviation substrates are suitable for various types of aircraft, including commercial airliners, military aircraft, drones, rockets, etc. Whether for civil aviation or military use, aviation substrates are an indispensable and key component of flight electronic systems.
What is the difference between aerospace substrates and ordinary electronic substrates?
Compared with ordinary electronic substrates, aerospace substrates have obvious differences in material selection, process requirements and performance indicators. Aviation substrates usually use high-performance composite materials with higher high temperature resistance, corrosion resistance and mechanical strength to meet the harsh requirements of the flight environment.
What is the life cycle of aerospace substrates?
The life cycle of aerospace substrates depends on multiple factors, including material quality, manufacturing processes, environmental conditions, etc. Generally speaking, aerospace substrates under good design and quality control can have a long service life and continuously support the operation of flight electronic systems.