Semiconductor BGA substrate manufacture. extra small bump pitch with 100um, extra small trace and spacing are 9um. we also can make the BGA substrate with ultrathin base materials.
Within the ever-evolving realm of semiconductor design, Ball Grid Array (BGA) substrates have emerged as indispensable components, playing a vital role in facilitating the installation and interconnection of electronic elements. This segment aims to delve into the distinctive characteristics of BGA substrates and shed light on their pivotal role in semiconductor packaging.
BGA substrates represent a pivotal component in semiconductor devices, meticulously crafted to offer an efficient method for packaging chips. The distinctive arrangement of a spherical grid enables secure mounting of electronic components on the substrate, establishing reliable electrical connections through these spherical connection points. The design of BGA substrates is meticulously tailored to accommodate the requirements for compact layouts and high integration in electronic devices, establishing a robust technical foundation for contemporary semiconductor design.
Within the realm of semiconductor packaging, BGA substrates function as a crucial link between the chip and the motherboard. Their role extends beyond mere mechanical support, encompassing exceptional performance in electrical connections. Leveraging carefully planned layouts and advanced manufacturing technologies, BGA substrates achieve steadfast fixation of electronic components and foster highly dense electrical connections. This capability not only enhances the overall performance but also facilitates the reduction of the size of semiconductor devices.
The basic nature of the BGA substrate lies in its structure and arrangement, which directly affects the effect of the entire semiconductor package. Its spherical grid arrangement not only increases the density of electrical connections, but also effectively solves thermal management challenges. This makes BGA substrates an indispensable component of modern high-performance electronic devices.
Overall, BGA substrate plays a central role in semiconductor design. It provides a solid foundation for the installation and connection of electronic components. Through its unique design and highly integrated features, semiconductor equipment has made great progress in performance and space utilization. As modern electronic devices pursue smaller, stronger, and higher performance, the design and application of BGA substrates will continue to play a decisive role.
What types of BGA substrates are there?
Within the complex domain of semiconductor engineering, Ball Grid Array (BGA) substrates emerge as prominent elements distinguished by their diversity and unique designs. Let’s delve into an exploration of various BGA substrates, unveiling different types of High-Density Interconnect (HDI), organic substrates, and more. Each variant bestows distinctive characteristics upon semiconductor designs, catering to specific engineering requirements.
High-Density Interconnect (HDI) Substrate
HDI substrates shine as gems within the BGA substrate family, renowned for their exceptional high-density wiring. Utilizing fine lines and interconnect holes, HDI substrates facilitate increased component integration within confined spaces, delivering superior performance to semiconductor designs.
Organic Substrate
Organic substrates hold a significant position in the BGA substrate family tree. Crafted using organic resin materials as the primary substrate body, this type of substrate offers greater flexibility in the manufacturing process and can accommodate diverse sizes and shapes in design. Its outstanding electrical properties and processability make it a preferred choice for numerous semiconductor applications.
Hard substrate vs soft substrate
In the classification of BGA substrates, hard substrates and soft substrates are the two main branches. Rigid substrates are known for their rigidity and stability and are suitable for applications with high physical environmental requirements. Relatively speaking, soft substrates are more flexible and suitable for curved or bent designs, such as flexible electronic devices.
Radio frequency (RF) BGA substrate
In response to the needs of radio frequency applications, RF BGA substrates emerged as the times require. This type of substrate is designed with the particularities of high-frequency signal transmission in mind, ensuring excellent performance in fields such as wireless communications and radar.
Rigid-flexible hybrid substrate
Delving into the realm of diverse BGA substrates unveils distinctive attributes associated with each type, presenting a plethora of options for semiconductor design. Whether the objective is achieving high-density interconnection, flexibility, or optimizing RF performance, the BGA substrate family has evolved into an indispensable component in semiconductor engineering, owing to its remarkable diversity. In this era of relentless innovation, a comprehensive understanding and adept utilization of the various BGA substrate types promise to open up expansive avenues for semiconductor design, fostering broader development opportunities.
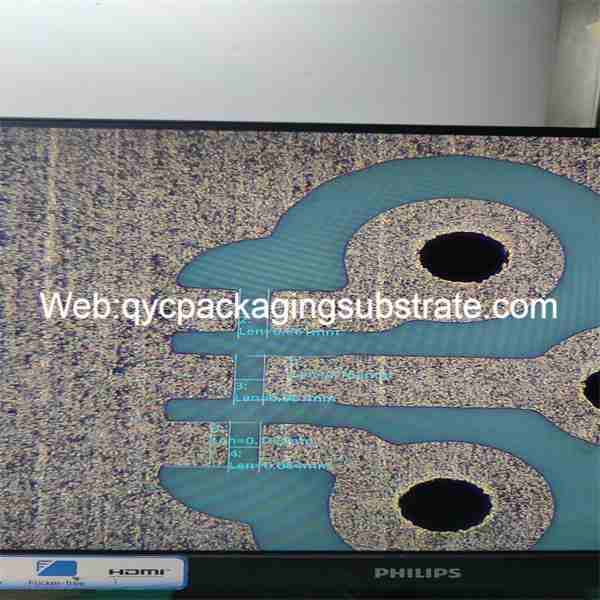
Semiconductor BGA substrate quote
What are the advantages of BGA substrate?
The BGA (Ball Grid Array) substrate stands out as a fundamental element in contemporary semiconductor design, making significant strides in the realm of semiconductor engineering due to its numerous advantages. Offering enhanced electrical performance and effective thermal management, BGA substrates contribute distinct added value to the overall performance of semiconductor devices.
Sublimation of electrical performance
A significant advantage of BGA substrates is their superior electrical performance. Through unique layout and design, the BGA substrate effectively reduces the resistance and inductance of the circuit and improves the transmission efficiency of electrical performance. This means that under the same conditions, electronic devices on BGA substrates can transmit signals faster, thus performing well in high-performance applications.
Superb application of thermal management
In semiconductor engineering, effective thermal management is imperative. The Ball Grid Array (BGA) substrate stands out for its superior thermal management features in semiconductor devices, thanks to its advanced heat dissipation design. The spherical grid array layout efficiently disperses heat, preventing localized overheating and ensuring sustained stable performance during extended operational periods.
Compact size, optimal space
As electronic equipment develops toward miniaturization, BGA substrates have become a valuable choice in semiconductor design due to their compact size. Compared with traditional packaging, BGA substrates can achieve higher device integration, making the circuit board simpler and optimizing overall space utilization. This is crucial for modern electronic devices that are thin, portable and highly integrated.
Improved reliability
The welding technique utilized in Ball Grid Array (BGA) substrates ensures a consistent distribution of solder joints, effectively reducing the risk of stress concentration. This significantly enhances the reliability and stability of semiconductor devices, particularly when exposed to fluctuating temperatures and diverse environmental conditions.
BGA substrates are purposefully engineered to seamlessly integrate with state-of-the-art manufacturing technologies and materials, including High-Density Interconnect (HDI) technology. This adaptability enables BGA substrates to meet the dynamic requirements of semiconductor engineering, offering a reliable foundation for the production of cutting-edge electronic devices.
In summary, the notable advantages of BGA substrates in semiconductor engineering extend beyond improvements in electrical performance and thermal management. Their innovative design, reliable welding methods, and compatibility with advanced technologies infuse a new level of vitality into the design and manufacturing processes of electronic devices. This innovative force is poised to propel the forefront of semiconductor engineering, laying a robust foundation for the ongoing development of future electronic technology.
Why choose BGA substrate?
In the rapidly evolving semiconductor market, the selection of an optimal solution for intricate electronic designs holds paramount importance. Ball Grid Array (BGA) substrates have prominently emerged in this competitive arena, garnering preference among engineers due to their superior performance, efficient space utilization, and adaptability to cutting-edge technologies.
The excellent performance of BGA substrates is one of the key factors in its leadership in the industry. With its ball-shaped arrangement of pins, BGA enables a more compact layout and provides shorter interconnect paths, thereby reducing signal transmission delays. This design helps improve the circuit’s operating speed and stability, making BGA stand out in high-frequency and high-performance applications.
In today’s increasingly miniaturized electronic devices, space is a critical consideration. Compared with traditional chip packaging, BGA substrate provides greater design flexibility with its compact packaging form. By enabling more interconnections in a limited space, BGA substrates help achieve more compact and lightweight product designs, which is an advantage that cannot be ignored, especially for mobile devices and embedded systems.
As technology advances rapidly, the semiconductor industry needs solutions that can adapt to emerging technologies and standards. BGA substrates better adapt to advanced packaging technologies and manufacturing processes through their design flexibility. For example, high-density interconnect (HDI) BGA substrates support more layers and enable more complex circuit designs, thereby meeting the needs of modern electronic devices for high integration and advanced functions.
In the automotive industry, the application of BGA substrates in vehicle electronic control units (ECUs) is an obvious example. Since automotive electronics need to operate stably in extreme environments, BGA substrates successfully meet the challenges in this field through their short interconnect paths and excellent thermal management capabilities. In comparison, other chip packaging formats may not provide sufficient performance and stability.
To sum up, the reason why BGA substrate has become a leader in the field of semiconductor design is because of its excellent performance, space optimization and technical adaptability. Through flexible design, compact layout and advanced manufacturing processes, BGA substrates have surpassed other semiconductor solutions in many application scenarios, providing innovative design options for electronic engineers.
How to make BGA substrate?
The manufacturing of BGA (Ball Grid Array) substrates is a key link in semiconductor engineering. Its complex process involves the production of motherboards and substrates, revealing important steps, materials used, and advanced technologies in the semiconductor field. The following is an in-depth introduction to the essentials of motherboard and substrate manufacturing.
Subtractive and additive processes in semiconductor manufacturing:
During the subtractive process of motherboard manufacturing, precision is paramount as the motherboard is intricately carved out of the original substrate through cutting and engraving. Advanced manufacturing equipment is employed to guarantee that the motherboard’s size and shape align with the design specifications.
In contrast, the additive process involves incrementally adding layers of diverse materials to construct a multi-layered structure for the motherboard. This layering approach not only facilitates higher circuit density but also enhances the overall performance and complexity of the circuit board by stacking layers upon layers.
Critical to motherboard manufacturing is the integration of advanced materials and technologies to ensure the semiconductor devices’ high performance and stability. Utilization of high-performance conductive materials, insulating materials, and advanced printing technologies is widespread, contributing to improved conductivity, insulation, and overall durability of the motherboard.
At the core of substrate manufacturing is the development of high-density interconnect technology to enable more compact circuit layouts. This includes the use of fine lines and advanced printing technology to accommodate more electronic components in a limited space and improve the integration of circuit boards.
BGA substrates, integral to the semiconductor manufacturing process, rely on crucial materials such as FR-4 (fiberglass reinforced epoxy resin) and polyimide. FR-4, as the primary substrate material, boasts commendable mechanical and electrical properties. Simultaneously, polyimide is employed to facilitate high-density interconnections, ensuring swift signal transmission.
The selection and application of these materials necessitate a careful balance between cost considerations and manufacturing feasibility while upholding performance standards. This dual focus forms the bedrock for BGA substrate manufacturing.
The precision art of BGA substrate manufacturing in semiconductor engineering demands advanced technology and state-of-the-art equipment. A profound understanding of the pivotal steps in motherboard and substrate production enhances our appreciation of the indispensable role BGA substrates play in supporting the performance and fostering innovation in electronic equipment.
What are the application fields of BGA substrates?
The Ball Grid Array (BGA) substrate has undergone significant evolution and emerged as a crucial element in semiconductor technology, demonstrating remarkable versatility and adaptability across diverse industries. Its extensive adoption, spanning from consumer electronics to automotive and medical devices, highlights its pivotal role in various applications.
The precise performance and sleek design of contemporary devices like smartphones, tablets, and digital cameras owe their existence to the high integration and dense interconnection facilitated by BGA substrates. The stability and outstanding electrical properties of BGA substrates emerge as crucial elements propelling innovation in consumer electronics.
Within the automotive industry, BGA substrates are reshaping vehicle electronic systems. The modern automobile incorporates a growing array of electronic components, spanning engine control units, safety systems, and entertainment systems. The high-density interconnection and reliability inherent in BGA substrates ensure seamless collaboration among these systems, delivering a safer and more intelligent driving experience for motorists.
In the medical field, BGA substrates have also demonstrated their key role in precision medical equipment. From pacemakers to medical imaging equipment, these devices require highly reliable electronic components, and the superior performance and compact design of BGA substrates make them ideal for these devices. Its excellent thermal management characteristics ensure long-term stable operation of the equipment and meet the stringent requirements for high quality and reliability in the medical field.
The successful application of BGA substrates in diverse industries is evidenced by actual cases. For instance, in the realm of smart home devices, the remarkable integration capabilities of BGA substrates contribute to the creation of smaller and more intelligent devices. In aerospace, the preference for BGA substrates is driven by their lightweight design and high-performance features, making them the primary choice for avionics equipment.
In summary, BGA substrates have transcended the limitations of conventional semiconductor technology, serving as a driving force for innovation across diverse sectors. Their flexibility and versatility find application in consumer electronics, automotive technology, and medical devices, positioning them as a crucial component in the ongoing revolution of semiconductor technology. As technology progresses, BGA substrates are expected to remain at the forefront, leading the transformation of semiconductor technology and guiding industries towards a future marked by intelligence, efficiency, and reliability.
Where to find semiconductor BGA substrate?
The swift progression of the semiconductor industry has firmly established BGA (Ball Grid Array) substrates as essential elements in contemporary electronic designs. The crucial factor for project success lies in the careful selection of a dependable and top-notch semiconductor BGA substrate supplier. Shared below are essential insights to steer you towards a reputable provider of these advanced substrates.
Firstly, prioritize manufacturers and distributors with a stellar reputation in the semiconductor field. Collaborating with an industry leader ensures access to proven, high-quality BGA substrates. Thoroughly examine the track record and standing of potential partners to confirm their alignment with your project requirements.
As a dedicated supplier of semiconductor BGA substrates, our company is committed to delivering exceptional products and services. By engaging directly with us, you can leverage our expertise and experience to acquire a tailored, high-performance BGA substrate aligned with the specific needs of your project.
As a supplier, we offer comprehensive insights to elucidate the factors influencing pricing. From substrate type to complexity, we elucidate the variables affecting your quote, empowering you to make well-informed decisions.
Collaborating with our company extends beyond mere procurement; it represents an opportunity to harness our resources, technical support, and customer service. Our commitment lies in fostering enduring relationships, ensuring robust support and assistance throughout the project lifecycle.
Recognizing the unique requirements of every project, our role as a semiconductor BGA substrate supplier involves delivering customized solutions tailored to your specific design and performance standards. Partnering with us ensures the acquisition of a BGA substrate fully aligned with your project specifications.
In the quest for semiconductor BGA substrates, the choice of a trustworthy supplier is pivotal. As your collaborative partner, our company pledges to furnish superior products, in-depth industry insights, and comprehensive support to guarantee the success of your project. Feel free to reach out and let us collectively drive innovation and foster the evolution of semiconductor technology.
Quotation of semiconductor BGA substrate
In the realm of semiconductor engineering, the BGA (Ball Grid Array) substrate holds a pivotal position, furnishing robust support for the functionality and effectiveness of electronic devices. Nonetheless, for semiconductor engineers and designers, acquiring a precise comprehension of BGA substrate pricing is crucial to guarantee project success. This article will delve deeply into the fundamental factors influencing the quotation of semiconductor BGA substrates, examining the diverse pricing variables that demand thoughtful consideration for making informed decisions.
Different types of substrates differ in material cost, manufacturing difficulty, and performance characteristics. High-density interconnect (HDI) substrates may have higher manufacturing costs than traditional organic substrates, but their advantages in miniaturization and high performance may bring more value to projects.
The complexity of BGA substrates is one of the important factors affecting pricing. Complex circuit layouts, multi-layer interconnections and advanced manufacturing techniques often result in a more cumbersome manufacturing process, driving up costs. When budgeting for a BGA substrate project, the potential impact of design complexity on pricing must be fully considered.
Production quantity is another key factor that determines the unit price of BGA substrates. Generally speaking, high-volume production helps spread fixed costs, thereby reducing the cost of a single substrate. However, small-scale production may result in higher unit prices. When choosing the appropriate production quantity, you need to balance the budget requirements and actual needs of the project.
The use of BGA substrates involves a variety of materials, including FR-4 and polyimide. The choice of material will directly affect the cost and determine the performance of the substrate to a certain extent. At the same time, materials that meet quality standards ensure the stability and reliability of the project, but may also increase the overall cost.
As manufacturing technology continues to advance, new production methods and processes may affect the pricing of BGA substrates. Adopting advanced manufacturing technologies may increase efficiency, but the costs of initial investment and technology conversion also need to be considered. Therefore, the choice of manufacturing technology requires a thorough assessment of its long-term impact on the total project cost.
By delving into the above considerations, semiconductor engineers and designers can better understand the logic behind the quotation of semiconductor BGA substrates. They can make more informed choices about pricing variables based on substrate type, complexity and production quantity when developing project budgets and developing procurement strategies. Such smart choices not only help control costs, but also help ensure the high performance and reliability of BGA substrates, thereby driving the success of semiconductor engineering projects.
Frequently Asked Questions
What factors influence the pricing of Semiconductor BGA Substrate quotes?
Understand the variables affecting the cost, including substrate type, complexity, and production volumes. This knowledge empowers individuals and businesses to budget effectively for their semiconductor projects.
What distinguishes BGA Substrates from other semiconductor solutions?
BGA Substrates offer a unique set of advantages, such as enhanced electrical performance, efficient thermal management, and space optimization. These attributes set them apart in the competitive semiconductor landscape.
Why should one choose BGA Substrates over other semiconductor solutions?
BGA Substrates stand out in terms of performance, space optimization, and adaptability to cutting-edge technologies, making them a superior choice in certain semiconductor applications.
Can you elaborate on the manufacturing process of BGA Substrates?
The manufacturing process involves intricate steps, including motherboard production with subtractive and additive processes, utilization of advanced materials, and substrate manufacturing techniques for high-density interconnects.
What factors influence Semiconductor BGA Substrate quotes?
Semiconductor BGA Substrate quotes may vary based on substrate type, complexity, and production volumes. Understanding these variables is crucial for making informed decisions regarding project costs.
Are Semiconductor BGA Substrates customizable to specific project requirements?
Yes, Semiconductor BGA Substrates offer customization options to meet specific project requirements, providing flexibility for diverse semiconductor applications.