BT resin substrate manufacturing. we use the BT materials to produce the BGA substrates, Small gap LED PCBs, and other HDI PCBs from 2 layer to 50 layers. High quality are fast shipping time.
In today’s electronic field, BT resin substrate plays an indispensable role as an important part of printed circuit board (PCB) manufacturing. This article aims to deeply explore the manufacturing process of BT resin substrates, from design to production, to provide readers with the opportunity to fully understand this key technology. Whether you are an electronics engineer, manufacturer, or electronics enthusiast, you will gain valuable information from this article to meet the challenges of the ever-evolving electronics industry.
What is a BT resin substrate manufacturing?
BT resin substrate is a highly regarded key material in today’s electronic manufacturing field. Its name comes from the English “Bismaleimide Triazine”, which is a high-performance resin based on polytetraphthalate terephthalate (PTFE). This material is known for its excellent electrical properties and excellent high temperature resistance, and is often widely used in high-frequency, high-speed circuit design.
The unique structure of BT resin substrate gives it many advantages, making it ideal for manufacturing complex PCBs. First of all, it has excellent electrical characteristics, including low dielectric constant and low dielectric loss, which can effectively reduce signal attenuation and crosstalk during signal transmission, thereby improving circuit performance and stability. Secondly, the BT resin substrate can maintain stability in high-temperature environments and has a temperature resistance of over 200 degrees Celsius. It is suitable for application scenarios in various high-temperature environments, such as aerospace, automotive electronics and other fields.
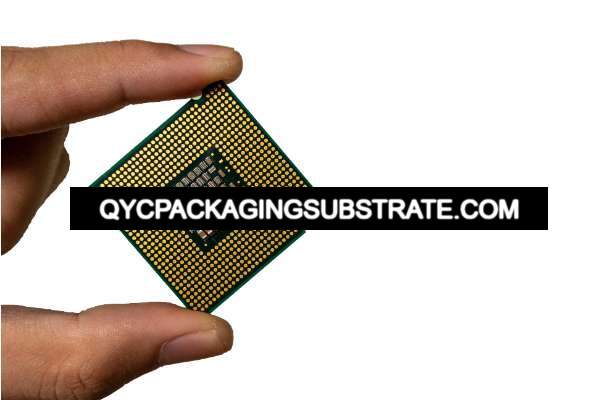
BT resin substrate manufacturing
In addition, BT resin substrate also has excellent mechanical properties and chemical stability, which can resist the erosion of chemical substances and the impact of mechanical stress, ensuring the reliability and stability of the circuit board in various harsh environments. This characteristic makes BT resin substrates widely used not only in high-end fields such as communications, radar, and satellite navigation, but also in many industries such as medical equipment, industrial control, and consumer electronics.
In general, BT resin substrate has become one of the indispensable and important materials in the field of modern electronic manufacturing due to its excellent electrical properties, high temperature resistance and stable and reliable characteristics, providing performance improvement and stability for various electronic equipment. Running provides a solid foundation.
How to Design a BT resin substrate manufacturing?
Designing BT resin substrates is a complex and critical engineering task, which requires engineers to use professional knowledge and skills to convert circuit schematics into achievable physical layouts. The main steps for designing BT resin substrates will be introduced in detail below.
First, the design process begins with the capture of a circuit schematic. At this stage, engineers use software tools such as Altium Designer, Cadence, etc. to convert the circuit schematic diagram into a computer-readable form. These software provide rich component libraries and design tools that enable engineers to select and place various electronic components, such as resistors, capacitors, transistors, etc., to build the required circuit functions.
Next is component layout. In this step, engineers reasonably lay out each electronic component on the PCB board, taking into account the circuit’s functional requirements, signal transmission paths, heat dissipation requirements, and subsequent manufacturing and assembly processes. Good component layout not only improves circuit performance, but also reduces board size and saves costs.
Then there’s the wiring. Wiring is the process of physically wiring the connections between electronic components with wires. In this step, engineers need to consider factors such as signal transmission speed, interference, and signal-to-noise ratio, and adopt appropriate line widths, line spacing, and wiring rules to ensure the stability and reliability of the circuit.
Finally, there is layout optimization. Once component placement and routing are complete, engineers will optimize the entire circuit layout to ensure optimal performance, space utilization, and manufacturability. This may involve adjusting component locations, optimizing signal transmission paths, adding ground and power planes, and other operations to meet design requirements and manufacturing process requirements.
In general, designing a BT resin substrate requires engineers to perform a series of key steps such as component layout, wiring, and layout optimization based on the circuit schematic to achieve circuit functions, optimize performance, and ensure smooth manufacturing and assembly. Through the combination of professional design software and the professional knowledge and skills of engineers, the design of high-quality BT resin substrates will provide a solid foundation for the performance and reliability of electronic products.
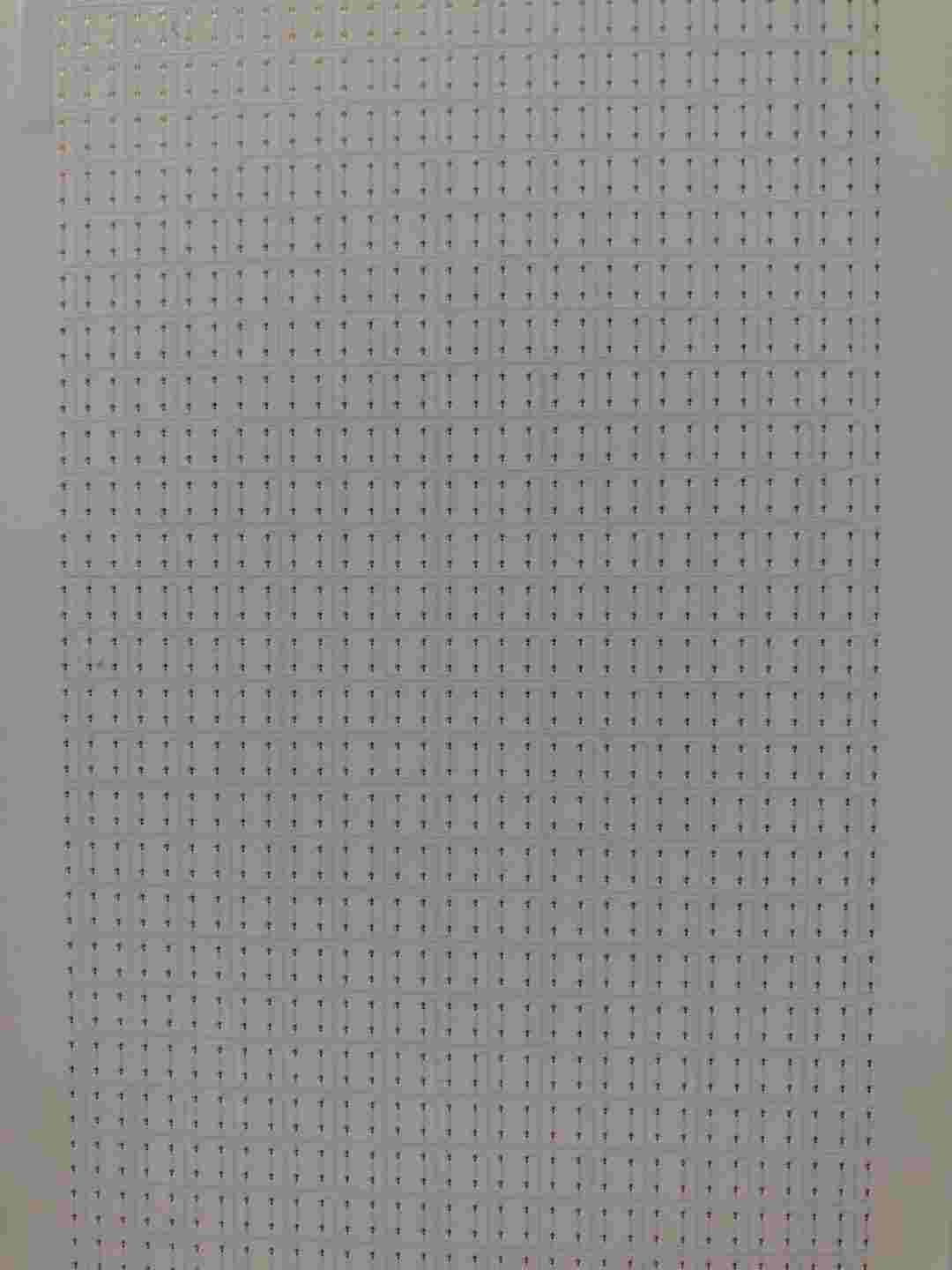
BT LED PCBs
What is the BT resin substrate manufacturing Fabrication Process?
The manufacturing process of BT resin substrates is a precise and complex process involving multiple critical steps to ensure the quality and reliability of the final product. The following is a detailed introduction to the manufacturing process of BT resin substrate:
The first step in manufacturing BT resin substrates is substrate pretreatment. At this stage, substrates of appropriate size and thickness are selected, cleaned and surface prepared. The cleaning process is designed to remove any dirt or grease from the substrate surface and ensure that the substrate surface is flat and ready for subsequent processing steps. Surface treatment can be achieved by mechanical or chemical methods to increase the roughness and surface tension of the substrate surface to provide better adhesion for conductor deposition.
Conductor deposition is one of the key steps in manufacturing BT resin substrates. At this stage, conductor material (usually copper) is deposited on the surface of the substrate to form wires and connection points. Common conductor deposition methods include chemical deposition, electroplating, and physical vapor deposition. These methods can be selected based on specific design requirements and application needs to ensure conductor layer uniformity and adhesion.
Patterning is the process of transferring designed circuit patterns to the surface of a substrate. Patterning is usually achieved using photolithography technology, in which a photosensitizer is coated on the substrate surface and then exposed to ultraviolet light to form a photolithographic pattern according to the designed pattern. Through chemical etching or other removal methods, conductor material in areas not protected by photolithography is removed, forming the desired wire and circuit patterns.
Etching is the process of removing conductive material not covered by photolithography from a substrate using a chemical solution. This step is intended to define the shape and structure of the circuit and ensure good isolation between wires. The etching process typically uses acidic or alkaline solutions, whose chemical composition varies depending on the desired etch rate and the characteristics of the substrate material. Precise control of the etching process is key to ensuring circuit quality and performance.
Solder mask is the process of applying a layer of protective material to the surface of a substrate to protect the circuit and enhance its durability. Solder mask is usually made of polymer materials with good insulation properties and chemical resistance. Solder mask not only prevents the wires from being damaged during use, but also provides an extra layer of protection, making the circuit more stable and reliable.
The last critical step is surface treatment, which processes the surface of the substrate to improve welding performance and corrosion protection. Surface treatments can include chemical treatments, spraying or coating with a layer of metal or alloy materials to increase the surface’s weldability and corrosion resistance. The choice of surface treatment depends on the specific application needs and desired performance specifications.
Through the careful design and execution of the above key steps, the BT resin substrate manufacturing process ensures the quality and reliability of the final product, providing a stable and reliable foundation for various electronic applications.
How to manufacturing a BT resin substrate manufacturing?
The manufacturing process of BT resin substrate is a complex process with precise design and process control, involving multiple key steps. Each step is crucial and affects the quality and performance of the final product.
First, the manufacturing process begins with the substrate preparation stage. At this stage, engineers carefully select substrates of appropriate size and thickness and perform thorough cleaning and surface preparation. This step ensures the surface flatness and cleanliness of the substrate, providing a good foundation for subsequent process steps.
Next comes the conductor deposition stage. At this stage, conductor material (usually copper) is deposited on the surface of the substrate to form wires and connections through chemical or physical methods. These wires will build the circuit pattern in subsequent steps.
This is followed by the patterning process. Through photolithography technology, the designed circuit pattern is transferred to the surface of the substrate. This requires sophisticated photolithography equipment and high-resolution masks to ensure the accuracy and precision of circuit patterns.
Once the pattern has been transferred, the etching stage follows. In this step, a chemical solution is used to remove conductor material not covered by photolithography from the substrate surface, creating the desired wire and circuit patterns. This process requires strict control of etching time and solution concentration to ensure the quality and clarity of the circuit pattern.
Then comes the coating of solder mask. The solder mask is coated on the surface of the substrate to protect the circuit from the external environment and enhance its durability. The solder mask also provides soldering points for easy subsequent assembly and connection.
Finally, there is the surface treatment stage. At this stage, the surface of the substrate is processed to improve its welding performance and corrosion resistance. This may involve chemical treatments, mechanical polishing or other special techniques to ensure the quality and reliability of the substrate surface.
To sum up, the manufacturing process of BT resin substrate is a delicate and complex process that requires a high degree of professional knowledge and strict process control. Each step has a significant impact on the quality and performance of the final product and must therefore be performed and managed to extremely high standards.
How Much Does a BT resin substrate manufacturing Cost?
The cost of BT resin substrate is a complex issue affected by many factors. When considering cost, several factors must be considered, including size, complexity, materials, and quantity.
First of all, size is one of the important factors that determine the cost of BT resin substrate. Generally speaking, larger-sized substrates will require more materials and production resources, so the cost will be relatively higher. In contrast, smaller sized substrates generally cost less. In addition, the size will also affect the production efficiency of the substrate, thereby affecting the overall cost.
Secondly, the complexity of the substrate is also an important consideration. Complex circuit designs may require more layers and finer craftsmanship, which increases manufacturing costs. For example, multilayer board designs may result in higher production costs because they require more layers and complex stacking processes.
Material is another key factor affecting the cost of BT resin substrate. BT resin substrates usually use high-performance materials such as polytetraphthalate terephthalate (PTFE), which are relatively expensive. In addition, conductor materials (such as copper), solder mask materials and surface treatment materials will also have an impact on costs. Choosing high-quality materials can improve substrate performance and reliability, but can also increase manufacturing costs.
Finally, quantity is another important factor affecting the cost of BT resin substrates. Generally speaking, high-volume production can achieve economies of scale, thereby reducing unit costs. Conversely, the cost of low-volume production may be higher due to lower utilization of production equipment and resources.
Taken together, understanding these cost drivers is critical to budgeting and optimizing production expenses. Through reasonable design and production planning, as well as effective management of factors such as size, complexity, materials, and quantity, the cost of BT resin substrates can be minimized and the quality and reliability of the product can be ensured.
What materials are BT resin substrate manufacturing made of?
The manufacturing of BT resin substrates is inseparable from the application of various key materials, which together ensure the performance and reliability of the final product. The following are common key materials used in BT resin substrate manufacturing:
Polytetraphthalate terephthalate (PTFE): One of the core materials of BT resin substrate, it has excellent electrical characteristics and high temperature resistance. As a substrate material, PTFE can provide good dielectric properties and chemical stability, and is suitable for the design needs of high-frequency and high-speed circuits.
Conductor material: Copper is usually used as the conductor material of BT resin substrate. Copper has good electrical conductivity and workability, and can meet the needs of wires and connections in circuits. By depositing copper conductors on the surface of the substrate, circuit connections and signal transmission are achieved.
Solder mask material: In PCB manufacturing, the solder mask layer usually covers the surface of the copper conductor to protect the circuit from the external environment, such as moisture, chemical corrosion, etc. The solder resist material has good insulation and heat resistance, can effectively isolate the circuit and improve the durability and stability of the PCB.
Surface treatment materials: In the final stage of BT resin substrate manufacturing, special treatment is required on the surface of the substrate to improve welding performance and anti-corrosion capabilities. Common surface treatment methods include tin spraying, gold spraying, silver spraying, etc. These treatments can not only enhance the solderability of the conductor surface, but also effectively prevent oxidation and corrosion, ensuring the stability and reliability of circuit connections.
To sum up, there are many types of materials involved in the manufacturing of BT resin substrates, and each material plays a key role in jointly ensuring the performance and quality of BT resin substrates. By rationally selecting and optimizing these materials, high-quality BT resin substrates can be produced that meet the needs of various electronic applications.
Who manufactures BT resin substrate manufacturing?
In the industry of manufacturing BT resin substrates, one of the major manufacturers is our company. As a leading company focusing on the electronics field, we have extensive experience and expertise in the field of BT resin substrate manufacturing. We are committed to providing high-quality, reliable BT resin substrates to meet customers’ needs for circuit board quality and performance.
Our company has advanced production equipment and technical team, able to achieve integrated services from design to production. We strictly control every aspect of the production process to ensure stable and reliable product quality. We focus on technological innovation and quality management, constantly optimize the production process, and improve product performance and production efficiency.
In addition to traditional BT resin substrate manufacturing, we also provide customized solutions to meet customers’ specific design needs and technical requirements. We work closely with our customers to understand their needs and provide them with personalized service and support.
As a reliable BT resin substrate manufacturer, we are committed to providing customers with the highest quality products and services. Whether in the fields of electronic communications, medical equipment or industrial control, we are able to provide customers with satisfactory solutions and provide strong support for the successful launch of their products.
What are 5 qualities of a good customer service?
In the modern business environment, excellent customer service is one of the keys to business success. Here are five qualities of great customer service that help companies build strong relationships with customers and enhance brand value and competitive advantage.
Responding quickly to customer inquiries and concerns is at the heart of excellent customer service. When customers have questions or needs, respond promptly and convey the message that the company cares and values its customers. Through quick response, we establish good communication and trust with customers and enhance customer loyalty to the company.
Excellent customer service is not only about solving customers’ problems, but also showing care and consideration for customers. Use empathy to understand customer needs and emotions and strive to meet customer expectations and requirements. Through sincere care and consideration, we establish emotional connections with customers and promote the formation of long-term cooperative relationships.
Reliability is the cornerstone of quality customer service and an important guarantee for establishing trust between enterprises and customers. Consistently deliver on promises to ensure that the products and services provided meet customer expectations and requirements. By maintaining a high level of reliability, we win the trust and reputation of our customers and enhance our brand image and competitiveness.
Maintaining clear and transparent communication during the service process is one of the keys to excellent customer service. Communicate relevant information to customers in a timely manner, clearly express the company’s position and policies, and eliminate customer doubts and misunderstandings. Through clear communication, we establish a good foundation for communication and cooperation with customers and improve customer satisfaction and loyalty.
Proactively resolving customer issues is an important part of great customer service. In the face of customer complaints and feedback, take timely action to find out the root cause of the problem and solve it to best meet customer needs and expectations. Demonstrate corporate responsibility and responsibility through effective problem solving, and win the respect and trust of customers.
To sum up, the five characteristics of high-quality customer service together form the cornerstone of a good relationship between an enterprise and its customers, help enterprises achieve improvements in customer satisfaction and loyalty, and promote the sustainable development and growth of enterprises. In a fiercely competitive market environment, focusing on high-quality customer service will win broader development space and a better future for the company.
FAQS
What distinguishes BT resin substrate from traditional substrates?
BT resin substrate is made from polyethylene terephthalate (PTFE), offering superior electrical performance and high temperature resistance compared to traditional substrates. It is particularly suitable for high-frequency and high-speed circuit designs.
How long does it take to manufacture BT resin substrates?
The manufacturing time for BT resin substrates varies depending on factors such as complexity, quantity, and supplier lead times. Typically, it ranges from a few days to several weeks.
What are the common challenges in BT resin substrate manufacturing?
Common challenges include ensuring design manufacturability, maintaining tight tolerances, managing material costs, and addressing quality control issues. These challenges require careful attention throughout the manufacturing process to ensure the production of high-quality substrates.
What is the significance of surface treatment in BT resin substrate manufacturing?
Surface treatment is essential in BT resin substrate manufacturing as it protects exposed copper traces from oxidation and provides a solderable surface for component attachment. This ensures reliable electrical connections and enhances the overall performance of the substrate.