Professional Cavity PCB Substrate Manufacturer, we offer Cavity slot PCB and Cavity BGA substrates from 4 layer to 30 laers. High frequency and high speed materials are used to produce such Cavity PCBs.
Cavity PCB Substrate, also known as grooved PCB substrate, is a technology leading innovation in electronic design. Its design features grooves that cleverly accommodate chips and other key components, bringing unique advantages to the board’s performance and application areas.
The uniqueness of Cavity PCB Substrate is first reflected in its innovative design. Compared with traditional flat circuit boards, Cavity PCB Substrate creates a more flexible installation space for various electronic components by adding grooves at the bottom. This design not only improves the integration of the circuit board, but also provides more possibilities for more complex electronic component layouts.
The groove design of Cavity PCB Substrate is not only for aesthetics, but also for careful consideration of heat dissipation performance. By increasing the channels for air circulation, this design effectively improves the heat dissipation effect of the circuit board. Especially in high-density, high-performance electronic equipment, this superior heat dissipation performance has become one of the reasons why Cavity PCB Substrate is so popular.
As electronic products continue to shrink in size and increase in functionality, higher requirements are placed on circuit board size and integration. Through its unique design, Cavity PCB Substrate allows the circuit board to accommodate more electronic components in a smaller size, further improving product integration. This is of great significance for modern electronic equipment that pursues lightweight and thinness.
The design of Cavity PCB Substrate is not only widely used in consumer electronics products, but also finds innovative application scenarios in a series of high-tech fields. From advanced communication equipment to high-performance computers, Cavity PCB Substrate is leading the new trend in electronic engineering and fully utilizing its unique features.
The design of Cavity PCB Substrate, through its unique features, brings new possibilities to electronic engineering. Its grooved design not only meets the challenges of size and integration, but also creates new benchmarks in thermal performance and application fields. As technology continues to advance, we can expect Cavity PCB Substrate to play a more important role in future electronic design.
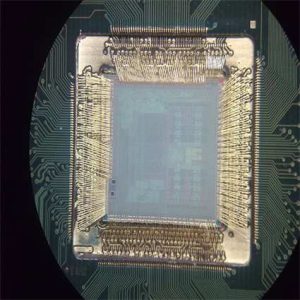
Cavity Packaging Substrate
What types of Cavity PCB Substrate are there?
Cavity PCB substrates have become the favored option for engineers and designers in the field of electronic engineering, thanks to their innovative design. Among these, Ball Grid Array (BGA) and Chip Scale Package (CSP) are prominent choices. Let’s delve into the unique features of these designs to offer readers a comprehensive grasp of the versatility provided by Cavity PCB substrates.
Ball Grid Array (BGA) Design
BGA is one of the most common and widely used designs in Cavity PCB Substrate. Its main features include:
High-density integration is achieved through the use of a Ball Grid Array (BGA) design, employing spherical solder joints positioned at the bottom. This arrangement facilitates a more condensed component layout, leading to a highly integrated circuit. The BGA design also boasts excellent heat dissipation performance, attributed to the even distribution of spherical solder joints. This enhancement effectively addresses the heat dissipation requirements of high-performance electronic equipment. Furthermore, the uniform distribution of solder joints contributes to the robust reliability of the BGA design, enabling it to withstand mechanical stress and vibration with resilience.
Chip Scale Package (CSP) design
CSP is another popular Cavity PCB Substrate design with unique features including:
Compact Size: The design of Small Package (SP) is renowned for its compact dimensions, making it ideal for electronic devices with limited space.
High Performance: Despite its diminutive size, the CSP design can accommodate high-performance chips, ensuring that it meets the demanding performance requirements of advanced electronic devices. This combination of compactness and capability makes CSP an attractive choice for various applications.
Choosing the appropriate Cavity PCB Substrate design for a project requires careful consideration of the project’s specific needs. If high-density integration and effective heat dissipation are paramount, a Ball Grid Array (BGA) design may be more suitable. On the other hand, for projects emphasizing compact size and low power consumption, opting for a CSP design would be a prudent decision.
The various types of Cavity PCB Substrate, especially BGA and CSP designs, provide electronic engineers with more choices. In actual projects, reasonable selection of different types of Cavity PCB Substrate based on project needs and goals will have a positive impact on product performance and reliability. By in-depth understanding of the characteristics of BGA and CSP design, engineers can formulate design strategies more clearly and lay a solid foundation for innovative electronic products.
What are the advantages of Cavity PCB Substrate?
Cavity PCB Substrate achieves a higher level of integration through its unique design by embedding chips and other key components into grooves. Compared with traditional circuit boards, this increase in integration allows electronic devices to accommodate more functional components in a smaller space, providing greater flexibility for product design.
Smaller size
Its grooved design not only improves integration, but also enables Cavity PCB Substrate to achieve smaller size designs. In today’s trend of focusing on thinness, lightness and size, Cavity PCB Substrate’s size advantage makes it shine in the design of compact electronic devices, such as smart handheld devices and wearable technology products.
Excellent cooling performance
The groove structure of Cavity PCB Substrate provides a more convenient channel for heat dissipation of electronic components. This design can effectively reduce the temperature of electronic components and improve the stability and reliability of the device. Especially for high-performance equipment, such as computer servers and graphics processors, excellent heat dissipation performance has become a prominent advantage of Cavity PCB Substrate.
Increased design flexibility
The design of Cavity PCB Substrate allows engineers more flexibility in the layout of electronic components. This design not only provides greater design space, but also allows engineers to optimize board performance more efficiently. Therefore, Cavity PCB Substrate becomes an ideal choice for complex circuit layout and design innovation.
Suitable for high-density layouts
As electronic devices continue to pursue performance, components on circuit boards are becoming more dense. Cavity PCB Substrate provides an ideal platform for high-density layouts through its recessed design.
Cavity PCB substrates have gained widespread popularity in the contemporary design of electronic devices owing to their numerous advantages, including high integration, compact size, outstanding heat dissipation performance, and design flexibility. The innovative design of these substrates opens up new possibilities for electronic engineers, resulting in products that not only excel in performance but also stand out in terms of appearance and size competitiveness. The synergistic impact of these benefits positions Cavity PCB substrates with a promising outlook in the future design of electronic devices.
Why choose Cavity PCB Substrate?
In today’s rapidly developing electronics field, Cavity PCB Substrate is gradually becoming a favored choice among engineers and designers. So, among the many circuit board options, why is Cavity PCB Substrate so highly regarded, and what is so unique about it?
One thing that stands out in the design of Cavity PCB Substrate is its exceptional flexibility. Compared with traditional circuit boards, its special groove design provides engineers with greater design space. This makes it easier to fit more electronic components into a limited space, thereby increasing the overall integration of the board.
The demand for enhanced functionality and reduced size in electronic devices has led to increased expectations for circuit board integration. Cavity PCB Substrate addresses this need by achieving a higher level of integration through a groove design that tightly embeds chips and other components. This innovation results in smaller and lighter designs for modern electronics.
Effective thermal management has always been a critical consideration in electronic device design. The groove structure of Cavity PCB Substrate significantly improves heat dissipation performance. This design facilitates better conduction and dispersion of the generated heat, ensuring that electronic components can maintain an optimal temperature during operation. As a result, Cavity PCB Substrate is particularly favored in high-performance and long-term use equipment.
Cavity PCB Substrate is not limited to applications in specific fields. Its flexibility and high integration make it widely used in multiple industries, such as communication equipment, medical equipment, automotive electronics, etc. Whether you are pursuing miniaturization of smartphones or servers with high performance requirements, Cavity PCB Substrate can meet diverse design needs.
The adoption of Cavity PCB Substrate is not only to cater to market trends, but also because of the advanced technology behind it. What engineers are interested in is not only its external design, but also the technical support it provides for the equipment, allowing electronic products to reach new heights in performance and design.
To sum up, the reason why Cavity PCB Substrate is chosen by more and more engineers and designers lies not only in its unique design flexibility, but also in its higher integration, excellent heat dissipation and adaptability to electronic products. Features suitable for design needs in multiple fields. This innovative choice not only meets the high performance and miniaturization requirements of modern electronic equipment, but also opens up more innovative possibilities for engineers.
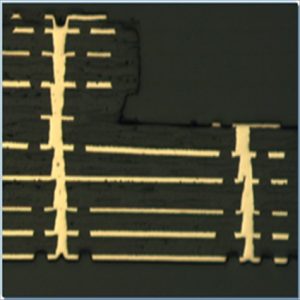
Cavity PCB Substrate
What is the manufacturing process of Cavity PCB Substrate?
Comprehending the manufacturing process of Cavity PCB Substrate is essential for engineers, as it significantly impacts the performance and stability of electronic devices, and plays a pivotal role in bringing innovative designs to fruition. In this exploration, we will delve into the step-by-step manufacturing process of Cavity PCB Substrate, examining the key technologies and processes involved from the motherboard to the bottom layer.
The manufacturing process of Cavity PCB Substrate initiates during the design phase, where engineers meticulously plan the layout of grooves to accommodate diverse chips and components. Utilizing design software is imperative to ensure that the dimensions and shapes of the grooves align with the equipment requirements.
A critical step in the manufacturing process involves selecting suitable materials. The chosen material must possess outstanding electrical conductivity, heat resistance, and mechanical strength to guarantee optimal performance of the Cavity PCB Substrate across various application environments.
An essential aspect of Cavity PCB Substrate manufacturing is the production of printed circuit boards (PCBs). This phase entails imprinting the designed circuit pattern onto the substrate to create a conductive path. For Cavity PCB Substrate, beyond conventional circuits, precision grooves must be intricately crafted on the base plate.
The creation of grooves is a unique step in the Cavity PCB Substrate manufacturing process. This requires high-precision machines and tools to ensure the shape and depth of the grooves meet design requirements. This step, which is not included in traditional circuit board manufacturing, makes Cavity PCB Substrate more complex in structure, but also provides more design space for electronic devices.
Following the manufacturing of the printed circuit board, the next phase involves the precise installation of components such as chips, resistors, capacitors, etc. into the recesses and circuit boards. The installation of components for Cavity PCB Substrate requires elevated technical expertise to ensure that they fit precisely without compromising the structure of the groove, enabling optimal performance.
Once the components are installed, the subsequent crucial steps in the manufacturing process are soldering and encapsulation. Soldering establishes a dependable connection between electronic components and the circuit board, while encapsulation shields the entire circuit from external environmental factors. For Cavity PCB Substrate, the package design must account for the presence of grooves to maintain package integrity and device stability.
The final stage of the manufacturing process involves testing and quality control. Engineers utilize various testing methods to verify that different aspects of the Cavity PCB Substrate meet design specifications, ensuring reliable performance. Any defects discovered during this stage are promptly addressed to uphold the product’s quality standards.
The manufacturing process of Cavity PCB Substrate is a precise and complex project that requires highly professional technology and equipment support. By gaining insight into each step of the process, engineers can better understand what makes Cavity PCB Substrate unique, thereby demonstrating more innovation and utility in electronic device design.
In what application fields is Cavity PCB Substrate widely used?
Cavity PCB Substrate (grooved PCB substrate), as an innovative circuit board technology, has demonstrated excellent performance in different fields, beyond its application in consumer electronics such as mobile phones and computers.
Cavity PCB Substrate is extensively utilized in consumer electronics like mobile phones and computers. Its design attributes, characterized by increased integration and reduced dimensions, contribute to the slimness, lightweight, and enhanced efficiency of electronic devices. In the realm of mobile phones, Cavity PCB Substrate proves instrumental in accommodating diverse chips and components, optimizing internal space utilization, all the while ensuring stability and performance.
In the field of communication equipment, the excellent performance of Cavity PCB Substrate has been fully utilized. Its application in network equipment, base stations and communication modules improves the overall performance of the equipment and signal transmission efficiency. Cavity PCB Substrate is favored in this field because its design can better cope with high-frequency and high-speed communication needs.
In the field of industrial automation, Cavity PCB Substrate has also demonstrated its unique advantages. Its highly integrated design makes industrial control systems and automation equipment more compact while maintaining high performance and stability. This is an important technical support for all types of factory automation and smart manufacturing applications.
The incorporation of Cavity PCB Substrate in medical electronic devices enhances their portability and precision. Its highly integrated design accommodates various sensors, control units, and communication modules, resulting in enhanced reliability and flexibility for medical monitoring and treatment equipment.
In the aerospace sector, where stringent weight and performance requirements prevail, Cavity PCB Substrate’s lightweight design and exceptional performance make it an ideal choice for avionics and satellite applications. Its capability to perform effectively in extreme environments, including space constraints, and its resistance to high temperatures and pressures have garnered widespread recognition.
In addition to its success in consumer electronics, Cavity PCB Substrate plays a pivotal role across diverse industries such as communications, manufacturing, medical, and aerospace. The broadening of its application scope has significantly contributed to technological innovation and the improvement of equipment performance in various industrial sectors.
How to find high quality Cavity PCB Substrate?
Check out their service history, customer testimonials and project cases in the industry. A supplier with extensive experience and a good reputation is usually more likely to provide high quality Cavity PCB Substrate.
Before solidifying a partnership with a supplier, it is wise to request samples for testing. This allows for a visual assessment of the quality and performance of Cavity PCB Substrate. Concurrently, confirm that the supplier’s products have achieved relevant certification standards, such as ISO quality management system certification, to ensure compliance with industry standards.
Obtain detailed information from suppliers about their supply chain management to ensure the timely delivery of high-quality Cavity PCB Substrate. Transparent supply chain management helps mitigate potential production risks.
Balancing cost and product value is crucial, with the importance of choosing a supplier that provides high-quality products slightly outweighing the consideration of cost. Opting for a supplier offering slightly more expensive but superior products is a worthwhile investment. Using low-quality Cavity PCB Substrate can result in production failures and heightened maintenance costs, ultimately overshadowing any initial savings.
Seek recommendations and references from peers, industry experts, or online communities. Insights and advice from other companies provide a comprehensive understanding, aiding informed decision-making.
Ensuring effective communication with suppliers is crucial. Clearly express your requirements and communicate project goals and expectations with vendors. Strong communication builds a solid partnership, guaranteeing project success. By following these recommendations, you can confidently choose a supplier with the ability to provide top-notch Cavity PCB Substrate, establishing a firm foundation for your project.
How to get a quote for Cavity PCB Substrate?
In the development of electronic engineering, Cavity PCB Substrate (grooved PCB substrate) has attracted much attention as an innovative technology. However, before deciding to adopt this emerging technology, it is crucial to understand how to obtain accurate market quotes. This article will discuss how to effectively obtain a quote for Cavity PCB Substrate while ensuring the project budget and plan.
Before setting out to get a quote for Cavity PCB Substrate, you first need to fully understand the project’s needs and specifications. Clarifying key parameters such as required performance indicators, size, number of layers, etc. will provide suppliers with the necessary information to ensure that the quotes they provide are more accurate.
It is recommended to contact multiple Cavity PCB Substrate suppliers to obtain their quotation information. This allows for effective comparison, not just of price, but also of delivery time, quality assurance, after-sales service, etc. Select the supplier that best suits your project needs through extensive comparison.
Some suppliers provide online quotation tools. By entering the key parameters of the project, the system will automatically generate the corresponding quotation. This method is usually faster and allows you to obtain quotes anytime and anywhere for easy comparison and adjustment.
In order to obtain an accurate quote, it is essential to comprehend the prevailing trends and price fluctuations within the Cavity PCB Substrate market. Factors such as the dynamic interplay between supply and demand, variations in raw material prices, and other market dynamics can significantly influence the quoting process. Staying well-informed about these market dynamics is crucial for gaining a deeper understanding of the rationale behind quotations.
When getting a quote, be sure to look carefully for hidden costs and extras. Some suppliers may include some additional charges in their quotations, such as shipping charges, custom tooling charges, etc. Be transparent about these costs to avoid budget overruns later on.
Establishing long-term relationships with suppliers may lead to more favorable offers and support. Through active communication and exchange, not only can the needs of both parties be better understood, but also more flexible business conditions may be obtained.
When obtaining a quote for Cavity PCB Substrate, a wise and prudent approach will lay the foundation for a successful project. By fully understanding project requirements, comparing suppliers, utilizing online tools, understanding market trends, paying attention to hidden costs, and establishing long-term relationships, you can more effectively obtain accurate market quotes and ensure that the project’s budget and plan are properly controlled.
What FAQs need answers to Cavity PCB Substrate?
What types of Cavity PCB Substrates are commonly used, and what are their distinctive features?
Common types of Cavity PCB Substrates include Ball Grid Array (BGA) and Chip Scale Package (CSP). Each type has unique characteristics that cater to specific engineering and design requirements.
Where can one find reputable suppliers and manufacturers of Cavity PCB Substrate?
Locating high-quality suppliers and manufacturers of Cavity PCB Substrate is critical for successful project implementation. This FAQ provides guidance on finding reliable sources for this innovative technology.
How can one obtain accurate quotes for Cavity PCB Substrate?
Before deciding on the adoption of Cavity PCB Substrate, obtaining accurate market quotes is essential. This FAQ section offers guidance on the factors influencing quotes and strategies for obtaining reliable pricing information.
Are there different types of Cavity PCB Substrates?
Indeed, Cavity PCB Substrates come in various types, with Ball Grid Array (BGA) and Chip Scale Package (CSP) being the most common. Each type has its own set of characteristics catering to different requirements.
Why is Cavity PCB Substrate gaining popularity among engineers and designers?
The growing preference for Cavity PCB Substrate can be attributed to its flexibility in design and unique advantages in high-density electronic component layout. Engineers and designers are drawn to its distinctive features in the design landscape.
Can you elaborate on the manufacturing process of Cavity PCB Substrate?
Understanding the manufacturing process of Cavity PCB Substrate is crucial. From mainboards to substrates, the manufacturing process involves key steps, technologies, and processes that contribute to its unique design and functionality.
In which application areas is Cavity PCB Substrate widely used?
Cavity PCB Substrate finds widespread applications not only in consumer electronics like smartphones and computers but also in critical sectors such as communication devices. Explore the diverse application areas where its superior performance shines.
How can one find reputable suppliers for high-quality Cavity PCB Substrate?
For engineers and designers seeking Cavity PCB Substrate, finding reputable suppliers and manufacturers is essential. This section provides guidance on where to look and what factors to consider when selecting a supplier.
How can one obtain accurate quotes for Cavity PCB Substrate?
Before deciding on Cavity PCB Substrate adoption, obtaining accurate market quotes is crucial. Discover tips on how to secure precise quotes, aiding in budgeting and project planning.
What are some common questions regarding Cavity PCB Substrate that need addressing?
Explore a set of common questions surrounding Cavity PCB Substrate, providing insightful answers to help readers gain a deeper understanding and effective application of this innovative technology.
In conclusion, this FAQ section aims to address your queries and enhance your comprehension of Cavity PCB Substrate, offering valuable insights for successful integration into your next-generation electronic product designs.