Ceramic package substrate Firm. We use advanced Msap and Sap technology to produce High multilayer interconnection Ceramic package substrates from 4 to 20 layers.
Ceramic packaging substrates are essential components in modern PCB design, facilitating the connection and placement of electronic elements. Crafted from advanced ceramic materials, they offer heightened reliability and performance in demanding operational settings, making them indispensable in electronic device engineering.
Within PCBs, ceramic packaging substrates serve a critical role in linking diverse electronic components, ranging from microprocessors to integrated circuits. They provide a robust foundation for component mounting, ensuring precise positioning and functionality across the circuit board.
Ceramic packaging substrates offer significant advantages over traditional materials like FR-4, particularly in industries requiring high reliability and durability such as aerospace, automotive electronics, and medical equipment. Their superior thermal conductivity and mechanical strength ensure stability even in extreme conditions, while excellent electrical insulation properties minimize signal interference and enhance circuit stability. Additionally, ceramics excel in dissipating heat, effectively managing temperatures to maintain optimal electronic device performance.
In summary, ceramic packaging substrates are indispensable in modern PCB engineering due to their superior performance in connecting and installing electronic components, as well as their stability and reliability in harsh environments. With ongoing technological advancements and the expanding range of application fields, ceramic packaging substrates will continue to be pivotal, offering electronic engineers more innovative possibilities.
What types of ceramic packaging substrates are there?
Ceramic packaging substrates play a crucial role in PCB engineering, offering a variety of types customized to meet diverse design needs across industries. These substrates, ranging from aluminum oxide (Al2O3) to aluminum nitride (AlN), each offer distinct performance traits.
Alumina (Al2O3) substrates are extensively employed owing to their outstanding mechanical strength and electrical insulation properties. They are especially suitable for applications in high-temperature environments like automotive electronics and industrial control systems, where thermal stability is critical.
They are favored for high-power electronic devices and see extensive use in RF modules, power amplifiers, and optoelectronic devices. AlN substrates facilitate efficient thermal management while maintaining superior electrical performance.
Aluminum Borate (AlB) substrates, characterized by low dielectric constant and outstanding dimensional stability, cater to the production of high-frequency and microwave circuits. Playing a pivotal role in communication systems, radar technology, and satellite applications, AlB substrates ensure signal transmission stability and reliability.
Zirconia (ZrO2) substrates, known for their robust strength, remarkable resistance to wear, and stability against chemical corrosion, are extensively utilized in electronic devices designed to function in challenging environments, including high temperatures and corrosive atmospheres. Widely employed in aerospace, petrochemical, and medical equipment, these substrates play a crucial role in enhancing the reliability and longevity of equipment operating under extreme conditions.
These distinct ceramic packaging substrates offer electronic design engineers a myriad of choices to address the diverse design needs of various application scenarios. Whether in high-temperature and high-pressure industrial settings or communication systems demanding exceptional signal stability, ceramic packaging substrates play a pivotal role in fostering continuous innovation and advancement in electronic technology.
What are the advantages of ceramic packaging substrates?
Ceramic packaging substrates offer a multitude of advantages in PCB engineering, spanning from their material characteristics to performance enhancements. Primarily, they excel in thermal conductivity, efficiently dissipating heat to prevent component overheating and thereby enhancing overall performance and reliability of electronic devices. Additionally, their high strength and durability ensure stable operation even in harsh environmental conditions like high temperature and humidity, bolstering long-term reliability. Furthermore, their superior electrical insulation properties minimize signal loss and interference, particularly beneficial in high-frequency and high-power applications, ensuring stable and accurate signal transmission. Lastly, their compatibility with such demanding applications, be it in communication, medical, or automotive electronics, further augments performance, making ceramic packaging substrates indispensable in modern PCB engineering. Overall, they provide a solid foundation for enhancing electronic equipment performance and ensuring stable operation.
Why choose ceramic packaging substrate?
Ceramic packaging substrates have gained significant attention as a preferred choice for cutting-edge electronic designs, surpassing traditional materials like FR-4 and organic substrates. Their appeal lies in several key advantages.
Firstly, ceramic packaging substrates demonstrate exceptional temperature resistance, making them well-suited for extreme environments. Unlike traditional organic substrates, ceramics maintain stability across a broader temperature range, ensuring optimal performance from very low to extremely high temperatures. This characteristic is particularly valuable for applications in challenging conditions.
Ceramic substrates demonstrate remarkable durability in challenging environments, such as those with high humidity, corrosion, or pollution. They maintain consistent electrical properties and mechanical strength, resisting the detrimental impact of external factors. This reliability ensures the prolonged stability of electronic devices, even in harsh conditions.
Moreover, ceramic packaging substrates excel in high-frequency operations, making them suitable for scenarios involving frequent switching and high-speed data transmission. With a low dielectric constant and low loss factor, ceramics effectively minimize signal transmission losses and distortion, ensuring clear and stable signals. This makes them an ideal foundation for the design of high-frequency electronic equipment.
In conclusion, the superior temperature resistance, environmental durability, and high-frequency capabilities make ceramic packaging substrates the material of choice for cutting-edge electronic designs. In the contemporary pursuit of electronic equipment stability, reliability, and performance, opting for ceramic substrates is undoubtedly a wise decision, providing a solid foundation for the successful application of electronic products.
What is the manufacturing process of ceramic packaging substrates?
The manufacturing process of ceramic packaging substrates is a meticulous and intricate procedure designed to guarantee optimal performance and reliability of the final product. It comprises several crucial stages:
Material Preparation: The process commences with the meticulous preparation of suitable ceramic materials, such as aluminum oxide (Al2O3) or aluminum nitride (AlN), chosen for their exceptional thermal conductivity and electrical insulation properties. Substrates are precisely cut, polished, and cleaned to attain a smooth, impurity-free surface.
Layer Printing or Deposition: Conductive and insulating layers are either printed onto or deposited onto the ceramic substrate. The conductive layer typically employs a metal film or ceramic conductive material to establish circuit connection points. Simultaneously, the insulating layer is applied to isolate the conductive layer, thus preventing short circuits and interference between circuits.
Sintering: After printing or deposition, the ceramic substrate undergoes a sintering process. This entails subjecting the substrate to high temperatures, where the ceramic materials crystallize and densify, enhancing their mechanical strength and thermal conductivity. Additionally, the sintering process cures the conductive and insulating layers, ensuring a robust bond with the substrate.
Finally, ceramic packaging substrates need to be precision machined and finished to meet strict specifications and dimensional requirements. This includes processes such as cutting, drilling, polishing and surface treatment to ensure consistent quality and geometry for each substrate. Precision machining also involves forming tiny circuit structures and apertures on substrates to suit specific application needs.
The manufacturing process of ceramic packaging substrates is characterized by high technological intensity and stringent controls. It demands precision craftsmanship and advanced equipment. Through meticulous design and precision processing, ceramic packaging substrates can deliver exceptional performance and reliability, catering to the requirements of various high-end electronic devices.
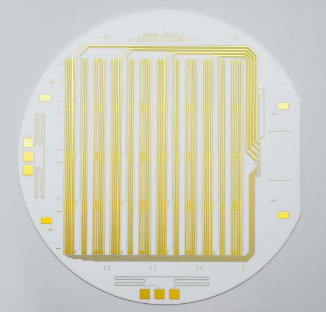
Ceramic packaging substrate
What are the applications of ceramic packaging substrates?
Ceramic packaging substrates are essential in various industries including aerospace, automotive, telecommunications, medical, and computing due to their exceptional resistance to high temperatures and reliability. In aerospace and defense sectors, they play a crucial role in safeguarding critical electronic components such as spacecraft and missile systems.In automotive applications, these substrates are vital for power modules and sensors due to their high strength and thermal conductivity, ensuring stable electronic system operation under extreme conditions. They are extensively employed in telecommunications for network equipment and base stations, leveraging their high-frequency characteristics for efficient data transmission. In the medical realm, ceramic substrates are preferred for their biocompatibility and stability, serving in various medical sensors and implantable devices. Additionally, they play a crucial role in high-performance computing and data centers, where their superior thermal and electrical properties support the demands of advanced processing tasks. Overall, ceramic packaging substrates offer promising prospects for technological innovation and development across diverse sectors, driving progress in aerospace, automotive, telecommunications, medical, and computing industries.
Where to find high quality ceramic packaging substrates?
As a supplier, our primary focus is on partnering with reputable manufacturers and distributors to source top-notch ceramic packaging substrates. We are dedicated to delivering materials of exceptional quality, characterized by superior thermal conductivity, mechanical strength, and electrical insulation properties, meeting the diverse demands of various application environments.
Our product range encompasses a comprehensive selection of substrate sizes and thicknesses, addressing a spectrum of design requirements from ultra-thin configurations to high-power applications. Furthermore, our specialized customization service team is poised to adapt ceramic packaging substrates to precise specifications, including size, shape, and functional requirements. We are equipped to handle both mass production and small batch orders to ensure flexibility and responsiveness to our clients’ needs.
In essence, we pledge to be your dependable partner, delivering top-notch ceramic packaging substrates alongside comprehensive technical support and personalized services. Get in touch with us today, and let’s collaborate to forge outstanding electronic products together.
What is the quotation of ceramic packaging substrate?
Before delving into the quotation of ceramic packaging substrates, it’s crucial to grasp the various factors influencing their prices.
More intricate designs and processing requirements necessitate greater investments in labor, technology, and resources, thereby escalating production costs.
Output: Production volume directly impacts pricing. Generally, higher-volume production tends to lower unit costs, while lower-volume production may result in higher unit prices.
Customization Requirements: Specialized customization demands, such as specific dimensions, unique processing needs, or tailored electrical characteristics, can elevate production expenses and consequently influence the final quotation.
To procure an accurate quotation for ceramic packaging substrates and make informed decisions, it’s advisable for readers to engage reputable suppliers for consultation and pricing. These suppliers typically offer comprehensive technical support and personalized solutions tailored to customers’ specific requirements. Through communication and comparison across multiple suppliers, customers can gain deeper insights into the market dynamics and select the ceramic packaging substrate product aligning best with their needs and budget.
Common problem
Where can one find high-quality Ceramic Package Substrates?
Guide readers on sourcing reliable Ceramic Package Substrates from reputable manufacturers and distributors. Emphasize considerations such as material purity, substrate size, thickness, and customization options to meet specific project requirements.
What factors influence Ceramic Package Substrate quotes?
Provide insights into the cost considerations affecting quotes, including substrate material, complexity, production volume, and customization requirements. Enable readers to make informed decisions by obtaining quotes from trusted suppliers.
What are the common concerns addressed in Ceramic Package Substrate FAQs?
Address common queries related to Ceramic Package Substrates, covering topics such as compatibility, reliability, thermal management, and design considerations. Offer comprehensive answers to dispel uncertainties and guide readers toward successful implementation.
How are Ceramic Package Substrate quotes determined?
Ceramic Package Substrate quotes are influenced by factors such as substrate material, complexity, volume, and customization requirements. Obtaining quotes from trusted suppliers ensures informed decision-making.
Where can I source high-quality Ceramic Package Substrates?
Reputable manufacturers and distributors specialize in providing high-quality Ceramic Package Substrates tailored to specific project requirements. Consider factors such as material purity, substrate size, thickness, and customization options when selecting a supplier.