Ceramic package substrate Manufacturer. Ceramic series package substrate and Ceramic PCBs. We produce ultra-thin, ultra-thick or ultra-small pitch ceramic PCBs from 1 layer to 20 layers.
Ceramic packaging substrates are a key component in the electronics industry manufactured from ceramic materials to support and connect microscopic electronic components. This material has a range of excellent properties that make it ideal for many high-performance electronics.
First, ceramic packaging substrates have good thermal conductivity. In electronic devices, efficient heat dissipation is crucial, and ceramic materials can effectively conduct heat and help maintain stable performance of the device.
Secondly, ceramic materials have excellent electrical insulation properties. This means that on the circuit board, the ceramic packaging substrate can effectively prevent electrical faults and short circuits, improving the safety and stability of the device.
In addition, ceramic packaging substrates also have excellent mechanical strength and can withstand complex working environments and stresses. This enables ceramic packaging substrates to perform well in a variety of demanding industrial applications, such as automotive electronics, communication equipment, industrial control systems, etc.
In general, ceramic packaging substrates provide reliable support and guarantee for high-performance electronic products through its excellent properties such as thermal conductivity, electrical insulation and mechanical strength. In the electronics industry, selecting the appropriate ceramic packaging substrate is an important step to ensure device performance and stability.
What are the types of ceramic packaging substrates?
As an important part of the electronics industry, ceramic packaging substrates have various types, and each type plays a unique role in different application scenarios. The following are several common ceramic packaging substrate types:
Multilayer ceramic substrate, namely multilayer ceramic capacitor (MLCC), is a packaging substrate made of multiple layers of ceramic sheets laminated. This type of substrate has the characteristics of high density, high performance, and high reliability, and is widely used in power management, signal processing, filtering and other fields of electronic products.
Aluminum oxide ceramic substrate is a packaging substrate made of alumina as the base material. It has good insulation performance, thermal conductivity and mechanical strength. This kind of substrate is commonly used in high-frequency circuits, power modules, optoelectronic devices and other fields, and is suitable for harsh environments such as high temperature and high pressure.
Aluminum nitride ceramic substrate is made of aluminum nitride ceramic material, which has excellent thermal conductivity, mechanical strength and high temperature resistance. This kind of substrate is often used for heat dissipation and packaging of high-power electronic devices and semiconductor devices, and can effectively improve the performance and reliability of the device.
The above are only a few common types of ceramic packaging substrates. In addition, there are many other types of ceramic substrates, such as alumina ceramic substrates, silicon nitride ceramic substrates, etc. Each type has its own unique characteristics. Features and application scenarios.
In general, it is crucial to choose the type of ceramic packaging substrate that suits your own needs. Only with an in-depth understanding of the characteristics and advantages of various types can you make a wise choice and provide the best solution for the design and manufacturing of electronic products. .
What are the advantages of ceramic packaging substrates?
As a key component in the electronics industry, ceramic packaging substrates have many advantages over other materials. These advantages make them popular in the electronics field.
First, ceramic packaging substrates have excellent thermal conductivity properties. This material conducts heat quickly and efficiently to a heat sink or the surrounding environment, helping to maintain a stable operating temperature for electronic devices. In high-performance electronic devices, good thermal conductivity can effectively reduce heat accumulation, extend the service life of the device, and improve its performance.
Secondly, ceramic packaging substrates have a high degree of mechanical strength and can withstand complex working environments and stresses. This characteristic allows the ceramic packaging substrate to maintain stability in the face of vibration, impact or other external forces, thereby effectively protecting the internal electronic components and improving the reliability and durability of the device.
In addition, ceramic packaging substrates have excellent electrical insulation properties and can effectively prevent electrical faults and short circuits. In high voltage or high frequency applications, good electrical insulation can effectively reduce the failure rate of electronic equipment and improve the stability and safety of the system.
Finally, ceramic packaging substrates have good chemical stability and can resist corrosion from chemicals and high-temperature environments. This enables the ceramic packaging substrate to maintain stable performance under various harsh working conditions and is suitable for a wide range of application scenarios, including automotive electronics, communication equipment, medical equipment and other fields.
To sum up, ceramic packaging substrates have become the preferred material for many electronic products due to their excellent thermal conductivity, high mechanical strength, electrical insulation and good chemical stability. In the continuously developing electronics industry, ceramic packaging substrates will continue to play an important role, providing strong support for the performance improvement and stable operation of various electronic equipment.
What is the manufacturing process of ceramic packaging substrates?
The manufacturing process of ceramic packaging substrates is a precise and complex process that covers multiple critical steps to ensure that the final product has excellent thermal conductivity, electrical insulation and mechanical strength.
First, the process of manufacturing ceramic packaging substrates begins with the material preparation stage. At this stage, it is crucial to select the appropriate ceramic material, usually high-purity ceramic powder. These ceramic powders are mixed and processed to form blanks with specific properties, which provide the basis for subsequent processes.
Secondly, printed circuits are one of the important links in manufacturing ceramic packaging substrates. At this stage, printing technology is used to print conductive materials (such as silver paste) on the surface of the ceramic substrate to form circuit lines and pads. The accuracy and quality of this step directly affects the performance and stability of the final product.
Finishing is the last critical step in the manufacturing process. At this stage, the ceramic substrate goes through multiple processes such as sintering, surface treatment and inspection, and finally forms the finished packaging substrate. The sintering process is the core link in manufacturing ceramic packaging substrates. Through high-temperature sintering, ceramic materials are combined into a dense structure, improving their mechanical strength and electrical insulation properties. Surface treatment includes cleaning, smoothing and other processes to ensure the flatness and smoothness of the substrate surface. Finally, through strict testing and quality control, we ensure that our products meet specifications and meet customer expectations.
In general, the manufacturing process of ceramic packaging substrates requires precise equipment and process control to ensure that the product has excellent thermal conductivity, electrical insulation and mechanical strength. These technical challenges require manufacturers to have advanced manufacturing technology and rich experience to meet the growing market demand.
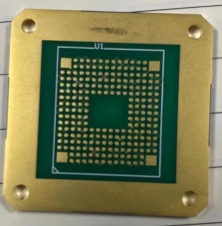
Ceramic package substrate
In what fields are ceramic packaging substrates widely used?
As a key component widely used in the electronics industry, ceramic packaging substrate plays an important role in various fields. The following are the applications of ceramic packaging substrates in different fields:
Automotive electronics is an important application field for ceramic packaging substrates. In modern automobiles, more and more electronic components are widely used, such as engine control units (ECU), anti-lock braking systems (ABS), in-car entertainment systems, etc. Ceramic packaging substrates have good high temperature resistance and vibration resistance, can adapt to the complex working environment of automobiles, and provide reliable support for automobile electronic systems.
In the field of communications, ceramic packaging substrates are widely used in key equipment such as wireless base stations and communication network equipment. These devices need to be highly stable and reliable to ensure the normal operation of the communication network. The excellent electrical insulation and high temperature resistance of ceramic packaging substrates make them ideal for communication equipment.
Industrial control systems cover many fields such as industrial automation, robotics, and sensor systems, and many of these devices and components require the use of packaging substrates. Ceramic packaging substrates have good high temperature resistance, corrosion resistance and mechanical strength. They are suitable for control systems in various industrial environments and provide reliable support for industrial automation and intelligent manufacturing.
In the medical industry, ceramic packaging substrates are widely used in medical diagnostic equipment, treatment equipment, implantable medical devices, etc. These devices have extremely high requirements for stability and accuracy. Ceramic packaging substrates can provide good electrical insulation and high mechanical strength to ensure the reliability and safety of medical equipment.
In the military and aerospace fields, the requirements for electronic equipment are more stringent, requiring high stability, high temperature resistance, radiation resistance and other characteristics. Ceramic packaging substrates are widely used in these fields due to their excellent performance, providing reliable support for military communications, navigation systems, satellites and other equipment.
In summary, ceramic packaging substrates are widely used in automotive electronics, communication equipment, industrial control systems, medical equipment, military aerospace and other fields, providing stable and reliable basic support for various electronic equipment.
Where to find ceramic packaging substrates?
As an important part of the electronics industry, ceramic packaging substrates can be purchased through multiple channels. First of all, professional electronic component markets are an ideal choice. These markets usually provide ceramic packaging substrates of various specifications and models for customers to choose and purchase. By searching and comparing in these markets, customers can easily find products that meet their needs.
In addition, online electronic parts suppliers are also a common way to purchase ceramic packaging substrates. Many electronic parts suppliers provide a wide range of product selections on their websites, and customers can browse and purchase the required ceramic packaging substrates through online platforms. Buying online is not only convenient and fast, but you can also enjoy a wider product selection and competitive price advantages.
In addition, it is also a common way to directly contact the ceramic packaging substrate manufacturer for customized procurement. By communicating directly with the manufacturer, customers can receive more customized service and support, ensuring that the products they purchase fully meet their specific needs and requirements. Manufacturers often provide technical support, sample production, and tailor-made solutions to provide customers with a full range of services and support.
As a supplier, our company also provides ceramic packaging substrates of various specifications and models. Customers can purchase and consult through our official website or directly contact our sales team. We are committed to providing customers with high-quality products and excellent services to meet their diverse needs and requirements.
To sum up, ceramic packaging substrates can be customized and purchased in professional electronic component markets, online electronic parts suppliers, and directly contact manufacturers. No matter which method is used, customers can easily obtain the products they need and receive corresponding technical support and services.
How is the quotation of ceramic packaging substrate determined?
The quotation of ceramic packaging substrates is a key consideration in the electronics industry. Its price is affected by many factors, from material cost to manufacturing process to customization requirements, which will all have an impact on the final price.
First of all, material cost is one of the important factors in determining the price of ceramic packaging substrates. The selection of ceramic materials directly affects the manufacturing cost. Different types of ceramic materials have different price levels, and market prices will also fluctuate with changes in supply and demand.
Secondly, the manufacturing process will also have a significant impact on the price. High-precision manufacturing processes and advanced production equipment can improve production efficiency, but they will also increase manufacturing costs. For example, the use of advanced printed circuit technology or special processing techniques may result in increased costs.
In addition, customers’ customization requirements are also one of the important factors affecting the quotation. Custom production to a customer’s specific needs may require additional engineering and adjustments, and these additional services and efforts will be reflected in the quote.
Customers can request a quotation from the ceramic packaging substrate manufacturer, and usually the manufacturer will determine the final quotation based on the customer’s specific needs and order volume. Customers can compare and choose after receiving quotes from different manufacturers to find the supplier that best suits their needs.
In general, the price of ceramic packaging substrates is the result of a comprehensive consideration of multiple factors. Customers should comprehensively consider price, quality, service and other aspects when choosing a supplier to ensure that they receive the most valuable products and services.
Ceramic Package Substrate Frequently Asked Questions (FAQS)
What are the advantages of ceramic package substrates compared to other materials?
Ceramic package substrates offer several advantages over alternative materials. They possess excellent thermal conductivity, superior mechanical strength, high electrical insulation, and robust chemical stability. These properties make them particularly suitable for demanding electronic applications.
How long does it take to manufacture ceramic package substrates?
The manufacturing time for ceramic package substrates varies depending on factors such as the complexity of the design, the required specifications, and the production volume. Generally, the process involves several stages, including material preparation, circuit printing, processing, and finishing, which collectively determine the production timeline.
How can one choose the right ceramic package substrate manufacturer?
Selecting a suitable ceramic package substrate manufacturer involves considering several factors such as the company’s reputation, experience in the industry, technological capabilities, quality assurance measures, customization options, and customer support services. Conducting thorough research and evaluating multiple manufacturers based on these criteria can help in making an informed decision.
In what temperature environments can ceramic package substrates be used?
Ceramic package substrates exhibit excellent thermal performance, allowing them to operate effectively across a wide range of temperature environments. They can withstand both high and low temperatures, making them suitable for applications in automotive electronics, telecommunications, industrial controls, medical devices, aerospace, and other demanding sectors.
What is the thermal dissipation capability of ceramic package substrates?
Ceramic package substrates possess outstanding thermal dissipation properties due to their high thermal conductivity. They efficiently dissipate heat generated by electronic components, ensuring optimal performance and reliability of the overall system. The specific thermal dissipation capability may vary depending on factors such as substrate design, material composition, and application requirements.