Embedded cavity PCB manufacturing, Open cavity(slot) on the PCBs, or make the step cavity on the PCBs, Put the IC or other components and parts in the cavity area. we offer Cavity PCBs from 4 layer to 30 layers. We will produce this Cavity PCBs according to the material you require. Such as:High frequency and high speed materials, or mixed media materials.
Revealing the Art of Embedded Cavity PCB Manufacturing: A Comprehensive Guide. In modern electronics, printed circuit boards (PCBs) play an important role, seamlessly integrating electronic components into devices ranging from smartphones to spacecraft. Among many PCB manufacturing technologies, embedded cavity PCB manufacturing stands out for its precise and indispensable process, which provides the possibility of compact, high-performance electronic systems. In this comprehensive guide, we delve into the complexities of embedded cavity PCB manufacturing, revealing its importance in the electronics industry.
What is an embedded cavity PCB?
Embedded cavity PCB, also known as cavity PCB or cavity backplane PCB, is a special printed circuit board design that plays a vital role in electronic devices. With the continuous advancement of modern electronic technology, the needs of electronic equipment have become more and more complex and diverse. Against this background, embedded cavity PCB has become one of the important tools to solve many electronic design challenges.
In this ever-changing electronic field, embedded cavity PCB plays a key bridge role. It is not only a basic structure that supports and connects electronic components, but also an important component to achieve high performance and stable operation of electronic equipment. The design and manufacturing of embedded cavity PCB not only requires superb technology and craftsmanship, but also requires a deep understanding of the overall architecture and functional requirements of the electronic system.
The design of embedded cavity PCB is not limited to simple wiring to connect electronic components, but needs to take into account various factors, such as the stability of signal transmission, suppression of electromagnetic interference, heat dissipation and management, etc. Its special design structure enables embedded cavity PCB to effectively reduce the size and weight of electronic equipment and improve overall performance and reliability.
In the field of modern electronics, embedded cavity PCB has a wide range of applications, covering many industries such as communications, aerospace, medical, and automobiles. Whether used in micro mobile devices or large industrial control systems, embedded cavity PCB plays an irreplaceable role. Its emergence has greatly promoted the development of electronic technology and injected new vitality and power into the scientific and technological progress of human society.
In general, embedded cavity PCB is not only a printed circuit board design, but also one of the important symbols of the development of modern electronic technology. Its unique design and high-performance characteristics make it an indispensable part of many electronic devices, creating a more convenient, efficient and intelligent lifestyle for humans.
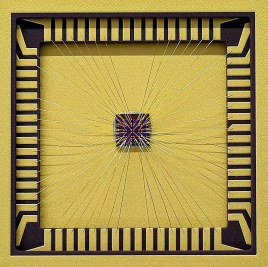
Embedded cavity PCB
How to design embedded cavity PCB?
Designing an embedded cavity PCB is a delicate and complex process that requires multiple critical steps to ensure the quality and performance of the final product. The following are the main steps in designing an embedded cavity PCB:
Requirements analysis: First, the design team needs to communicate with customers to understand their needs and technical specifications. This includes determining the size, shape, and materials of the required embedded cavity as well as the required circuit layout and functionality.
PCB layout planning: Based on the results of the demand analysis, the design team begins to plan the PCB layout. They determine the location, size and shape of the cavity and integrate it into the PCB design. At this stage, positional relationships to other components, signal transmission paths, and thermal management needs need to be considered.
Select the appropriate material: Select the appropriate substrate material based on the design needs and application environment. Commonly used substrate materials include FR-4, high-frequency materials such as Rogers, and ceramic materials. Choosing the right materials is critical to ensuring PCB stability, electrical performance and thermal management.
PCB design software operation: The design team uses professional PCB design software, such as Altium Designer, Cadence Allegro, etc., to convert layout planning into actual PCB design. They place components, draw connections, and precisely embed the size and shape of embedded cavities into the design.
Signal integrity and thermal management considerations: During the design process, the design team must pay close attention to signal integrity and thermal management. They ensure the reliability of signal transmission by optimizing signal paths, reducing signal interference, and adding ground and power planes. At the same time, they must also consider how to effectively dissipate heat to avoid overheating of components in the embedded cavity.
Design verification and optimization: After completing the preliminary design, the design team conducts design verification and optimization. They use simulation simulation and circuit layout analysis tools to evaluate the performance and stability of designs and make necessary modifications and optimizations to meet customer needs and standards requirements.
Generate design files: Finally, the design team generates design files, including PCB layout, component list (BOM), Gerber files, etc. These files will be used in the manufacturing process to ensure that the final embedded cavity PCB meets design specifications and customer requirements.
Designing an embedded cavity PCB is a complex process that takes into account multiple aspects such as circuit design, material selection, thermal management, and mechanical design. Through a strict design process and a professional technical team, we can ensure that the final embedded cavity PCB meets high quality and high performance requirements, providing reliable electronic solutions for various applications.
What is the manufacturing process of embedded cavity PCB?
The manufacturing process of embedded cavity PCB is a precise and complex process involving multiple critical steps to ensure the quality and performance of the final product. The following are the main processes for manufacturing embedded cavity PCB:
Design review and verification: The first step in manufacturing an embedded cavity PCB is to conduct design review and verification. During this phase, engineers carefully review the PCB design to ensure that the size, location, and shape of the cavity are as expected and meet the required functionality and performance requirements. This involves working closely with the design team to ensure the manufacturability and reliability of the design.
Material Selection and Preparation: Before fabricating an embedded cavity PCB, the appropriate substrate material and laminate must be selected. Commonly used substrate materials include FR-4 fiberglass composite materials, Rogers materials and ceramic substrates. The choice of these materials depends on application requirements such as high frequency characteristics, thermal management and mechanical strength. Once the material selection is determined, the corresponding materials need to be prepared for subsequent processing.
Lamination and Molding: One of the key steps in manufacturing embedded cavity PCBs is the lamination and molding process. At this stage, the pre-prepared substrate layers are laminated together with copper foil and pre-copper layers through the action of heat and pressure. This ensures adhesion and consistency between the layers and prepares them for subsequent processing steps.
Cavity Fabrication: Next comes the process of cavity fabrication, which involves using sophisticated tools and equipment to create cavities or cavities in the PCB. This can be achieved through a variety of methods, including laser drilling, controlled depth milling, and mechanical drilling. Engineers must ensure that the size and shape of the cavity are consistent with the design requirements and avoid damage to other parts of the PCB.
Wire and component installation: After completing the cavity fabrication, the next step is the process of mounting the wires and components on the PCB. This involves soldering electronic components to the PCB surface, as well as connecting wires to establish electrical connections. This step requires highly precise operations and skills to ensure correct and reliable assembly.
Testing and Quality Control: Finally, the process of manufacturing embedded cavity PCB also includes the stages of testing and quality control. At this stage, the PCB must undergo rigorous testing to verify that its functionality and performance meet design specifications. At the same time, quality control measures must also be implemented to ensure the consistency and reliability of the final product.
To sum up, manufacturing embedded cavity PCB is a precise and complex process that requires close coordination and precision operation of multiple critical steps. By strictly executing each step and ensuring the effective implementation of quality control, manufacturers can produce embedded cavity PCB products that meet design requirements and have excellent performance.
How to make embedded cavity PCB?
The manufacturing process of embedded cavity PCB is a complex and precise process involving multiple steps and specialized technologies. The production process of embedded cavity PCB will be introduced in detail below.
Design Verification: Before starting to manufacture the embedded cavity PCB, design verification is first required. Engineers use CAD software to verify the circuit board design, including cavity location, size and layout, to ensure it matches specification requirements and intended functionality.
Material preparation: When the production process begins, the appropriate substrate material is prepared. Common substrate materials include FR-4, Rogers or ceramic, the choice of material depends on the PCB’s end use and performance requirements.
Machining the Cavity: The next critical step is to machine the cavity. This typically involves using high-precision processes such as laser drilling or controlled-depth milling to create cavities in the substrate according to design specifications. These cavities can be used to house sensitive components, reduce electromagnetic interference, or improve thermal management.
Wiring layer preparation: Next, prepare the wiring layer. Through chemical treatment or mechanical processing, conductive lines are formed on the surface of the substrate to connect electronic components and complete the circuit design.
Stacking and laminating: After preparing the wiring layers, stack and laminate. This step involves stacking multiple layers together and laminating them under high temperatures and pressures to hold the layers together to form the complete PCB structure.
Plating and surface treatment: Next, proceed to plating and surface treatment. Through the electroplating process, a metal layer is formed in the wires and holes of the PCB, providing a good electrical connection. Then, surface treatment is performed to protect the PCB surface from environmental corrosion and oxidation.
Patterning and Inspection: Finally, pattern and inspect. Design patterns are transferred to the PCB surface using photolithography technology and inspected using automated equipment to ensure each PCB meets design specifications and quality standards.
Finished product testing: After completion of production, the embedded cavity PCB is tested for finished products. This includes functional testing, electrical testing and reliability testing to ensure each PCB works properly and meets customer needs.
Through the above steps, embedded cavity PCB can be produced to provide stable and reliable performance and functions for various electronic devices.
How much does an embedded cavity PCB cost?
The manufacturing of embedded cavity PCB involves many aspects of cost, which directly affect the quality, performance and reliability of the final product. The following are the main cost factors to consider when manufacturing embedded cavity PCBs:
The materials required for the manufacturing of embedded cavity PCBs are an important part of the cost. This includes substrate materials, conductive layers, insulating materials, etc. Choosing high-quality materials that meet design requirements is critical to ensuring product performance. Special materials such as high-frequency materials or metal substrates may also increase costs.
The manufacturing of embedded cavity PCB requires the use of advanced manufacturing equipment and technologies, such as laser drilling, controlled depth milling, lamination, etc. These high-precision processes require a large investment in purchasing and maintaining equipment, as well as experienced technicians to operate and monitor them, thus increasing manufacturing costs.
Manufacturing embedded cavity PCBs requires skilled workers to operate and monitor the production process. These workers need to be trained to master complex manufacturing techniques, and they need to pay corresponding wages and benefits. Labor costs are a non-negligible part of manufacturing costs.
Ensuring the quality of embedded cavity PCB products requires strict quality control. This includes quality inspection of raw materials, quality monitoring of the production process, quality testing of finished products, etc. Establishing a complete quality control system requires a certain amount of capital and manpower, but it can effectively reduce cost losses caused by quality problems.
Companies that manufacture embedded cavity PCBs need to pay certain management and operating costs, including office space rental, equipment maintenance fees, administrative staff salaries, etc. Although these costs are not directly related to product manufacturing, they are necessary for the normal operation of the company and are also included in the manufacturing costs.
In addition to the main cost factors mentioned above, there are some other factors that may affect the manufacturing cost of embedded cavity PCB, such as taxes, transportation costs, market competition, etc.
Taking all the above factors into consideration, the cost of manufacturing embedded cavity PCB will vary depending on the product specifications, complexity, production quantity, and the actual situation of the manufacturer. Although manufacturing costs may be higher, investing in high-quality embedded cavity PCB manufacturing is one of the keys to ensuring product performance and reliability, and will also bring long-term use value and market competitive advantages to customers.
What materials are embedded cavity PCBs made of?
As a special type of printed circuit board, embedded cavity PCB requires specific materials to be selected during its manufacturing process to meet various design requirements and application scenarios. Usually, the material selection of embedded cavity PCB is crucial, which directly affects the performance, stability and reliability of the circuit board.
The substrate material of embedded cavity PCB usually uses high-performance media to ensure that the circuit board can maintain stable performance under various environmental conditions. Common substrate materials include:
FR-4 (fiberglass reinforced epoxy): FR-4 is a widely used substrate material with excellent electrical properties and mechanical strength, making it suitable for most general application scenarios.
Rogers: Rogers materials have higher dielectric constants and lower dielectric losses, making them suitable for high-frequency applications such as wireless communications and radar systems.
Ceramics: Ceramic substrates offer excellent high-temperature performance and dimensional stability, making them suitable for high-temperature, high-frequency and high-power applications.
The conductive layer is an important part of the embedded cavity PCB used to connect electronic components. It is usually made of high-purity metal materials, such as:
Copper: Copper is a common choice for conductive layers, offering good conductivity and processability to meet the needs of most circuit boards.
Gold: In some high-end applications, such as aerospace and medical equipment, the metal layer may use gold as the conductive material to ensure high reliability and long-term stability.
Isolation layers are used to separate different circuit layers and protect circuit boards from the external environment. Commonly used isolation materials include:
Epoxy Resin: Epoxy resin has good insulating properties and chemical resistance, making it suitable for most applications.
Polyimide (PI): PI material has excellent high temperature performance and chemical stability and is suitable for high temperature, high frequency and high pressure applications.
Material selection for embedded cavity PCB depends on specific design requirements, application scenarios and performance needs. Through reasonable selection of materials and careful design, the embedded cavity PCB can be ensured to have excellent electrical performance, thermal management performance and reliability to meet the needs of various complex electronic systems.
Who makes embedded cavity PCBs?
In today’s electronics manufacturing world, the manufacturing of embedded cavity PCBs is becoming increasingly important as they provide an ideal solution for high-performance and miniaturized electronic devices. So, who is making these critical components? Let’s explore it together.
The manufacturing of embedded cavity PCB requires deep technical knowledge and rich experience. Therefore, many professional manufacturers specialize in this field. These manufacturers have advanced equipment and technology and have continuously improved their manufacturing levels through years of practice. They are able to customize various types of embedded cavity PCBs according to customer requirements, ranging from simple designs to highly complex applications.
Companies that manufacture embedded cavity PCBs are often at the forefront of technological innovation. They continuously invest in research and development to explore new materials, processes and technologies to improve product performance and meet evolving market needs. These manufacturers are often industry leaders, and their products and solutions have a wide range of applications in various fields.
At our company, we are proud to have advanced embedded cavity PCB manufacturing capabilities. We have an experienced and skilled team dedicated to providing customers with high-quality, reliable embedded cavity PCB solutions. By introducing the latest manufacturing equipment and processes, we continue to improve production efficiency and product quality to meet the growing needs of our customers.
As an embedded cavity PCB manufacturer, we understand that each customer’s needs are unique. Therefore, we provide flexible customization services and can customize embedded cavity PCBs of various specifications and sizes according to customer requirements. Whether it is small batch production or mass customization, we are able to meet our customers’ needs and provide a full range of support and services for their projects.
The manufacturing of embedded cavity PCB requires a high degree of professional knowledge and technical capabilities, and professional manufacturers are the key to achieving this goal. As a manufacturer of our company, we are committed to providing customers with high-quality, innovative embedded cavity PCB solutions, providing a solid foundation for their project success.
What are the five qualities of great customer service?
In the field of embedded cavity PCB manufacturing, providing excellent customer service is crucial. Here are five key traits that are not only the hallmark of a successful business, but also a key factor in customer satisfaction and loyalty.
Great customer service starts with effective communication. Manufacturers should always keep communication channels open with customers, respond to inquiries and resolve issues in a timely manner. Understanding customer needs and clearly communicating information about order progress, technical details, and any changes helps build trust and ensure both parties are on the same page.
Customers expect quick responses when they need help. Manufacturers shall respond to customer inquiries, requests and complaints as promptly as possible. By establishing efficient customer service teams and response processes, and leveraging modern communications technologies, manufacturers can achieve rapid feedback, thereby increasing customer satisfaction.
In the embedded cavity PCB manufacturing industry, customers often need to rely on the manufacturer’s expertise and advice. Provide an experienced and skilled team that can provide customers with accurate technical support, design suggestions and solutions. By working with customers, manufacturers can better understand their needs and provide them with the best solutions.
Customers want long-term relationships with reliable partners. Manufacturers should aim for reliable delivery and quality, consistently deliver on their promises, and ensure products meet specifications and standards. By building good credibility and word-of-mouth, manufacturers can gain the trust of their customers, which can lead to business growth.
A professional attitude is crucial when interacting with customers. Manufacturers should treat customers with courtesy, respect and patience, actively listening to and understanding their needs and feedback. Providing personalized service, flexible solutions, and demonstrating professionalism with high standards of work quality and ethical behavior will help establish the manufacturer’s image in the minds of customers and enhance customer satisfaction.
Overall, excellent customer service is not only about product quality and technical prowess, but also about building and maintaining relationships between manufacturers and customers. By fully understanding and practicing the above characteristics, manufacturers can stand out in a highly competitive market, win the trust and loyalty of customers, and achieve long-term sustainable development.
Frequently Asked Questions
What are the primary advantages of Embedded Cavity PCBs?
Embedded Cavity PCBs offer several key advantages, including enhanced thermal management, reduced electromagnetic interference (EMI), improved signal integrity, and increased design flexibility. The integration of cavities within the PCB substrate enables efficient heat dissipation, making them ideal for high-power applications and compact electronic devices.
How does Embedded Cavity PCB manufacturing impact thermal management?
The incorporation of cavities in Embedded Cavity PCBs facilitates superior thermal management by providing additional space for heat dissipation. This design feature allows for efficient airflow and heat transfer, thereby preventing overheating and ensuring the reliable operation of electronic components, particularly in demanding environments.
What industries benefit the most from Embedded Cavity PCB technology?
Embedded Cavity PCB technology finds applications across various industries, including aerospace, automotive, telecommunications, medical devices, and consumer electronics. These industries benefit from the enhanced performance, reliability, and miniaturization capabilities offered by Embedded Cavity PCBs, enabling the development of advanced electronic systems with stringent requirements.
Can Embedded Cavity PCBs be customized to accommodate specific design requirements?
Yes, Embedded Cavity PCBs can be customized to meet specific design requirements and application needs. Manufacturers offer flexible design options, allowing for the integration of cavities in various shapes, sizes, and configurations to optimize performance and functionality. Customization options also extend to material selection, layer stack-up, and surface finishes to ensure compatibility with diverse electronic designs.
What considerations should be made when selecting a manufacturer for Embedded Cavity PCBs?
When choosing a manufacturer for Embedded Cavity PCBs, several factors should be considered, including experience, expertise, manufacturing capabilities, quality standards, and customer support. It’s essential to partner with a reputable manufacturer with a proven track record in producing high-quality Embedded Cavity PCBs that meet industry standards and regulatory requirements. Additionally, assessing the manufacturer’s production facilities, technological capabilities, and responsiveness to customer needs can help ensure a successful partnership and satisfactory outcomes.