Embedded slot PCB manufacturing. Embedded Cavity PCB will made with Depth control cavity(slot). or multiple cavity on the PCBs. We specialize in the production of this kind of depth control slot PCB.
In today’s digital era, the rapid development of electronic equipment cannot be separated from the critical support of embedded slot PCB. As a core component of electronic equipment, embedded slot PCB achieves functionality and performance optimization of electronic equipment through its precision design and manufacturing. This article will conduct an in-depth study of the manufacturing process of embedded slot PCB, from design to finished product, and provide you with a detailed introduction to the implementation principles and application methods of this key technology.
What is an embedded slot PCB?
Embedded slot PCB (Printed Circuit Board) is a specially designed printed circuit board, which is characterized by a slot structure on the surface or inner layer for embedding specific components or connectors. This design is to meet the needs of modern electronic devices for high integration and compact size. Compared with traditional flat circuit boards, embedded slot PCBs can achieve higher device density and more flexible designs while maintaining performance.
The structure of the embedded slot PCB consists of a multi-layer printed circuit board in which the interlayer or surface layer is precisely processed into a slot structure. These grooves can come in different shapes and sizes, customized to the requirements of a specific application. The presence of the slots allows components to be embedded inside the circuit board, thereby increasing the functionality and flexibility of the circuit board while keeping the overall size compact.
Embedded slot PCB plays an important role in various electronic devices. For example, embedded slot PCB technology is widely used in smartphones, tablets, medical equipment, industrial control systems and other fields. These devices often require highly integrated circuit boards to meet complex functional requirements and space constraints. Embedded slot PCBs effectively meet these requirements and provide critical support for device performance and reliability.
Designing and manufacturing embedded slot PCBs presents some unique challenges. First, designers need to accurately calculate and plan the location and dimensions of the slots to ensure that the components will fit accurately and not affect the overall performance of the board. Secondly, the manufacturing process requires the use of advanced processing technology and equipment to ensure the accuracy and surface quality of the grooves. These challenges require designers and manufacturers to work closely together to ensure the quality and reliability of the final product.
In short, embedded slot PCB is a printed circuit board with a special design and structure. Its slot structure provides important support for the highly integrated and compact design of electronic equipment. In the ever-evolving electronics industry, embedded slot PCB technology will continue to play an important role and bring more innovation and possibilities to various application fields.
How to design an embedded slot PCB?
The design of embedded slot PCB is a complex process that takes into account many factors, which directly affects the performance and functionality of electronic equipment. When designing an embedded slot PCB, engineers need to carefully consider various key factors to ensure that the quality and performance of the final product meet expectations.
Component layout is one of the first considerations in embedded slot PCB design. Reasonable component layout can maximize the space utilization of the circuit board, ensure short circuits between circuits and reduce electromagnetic interference. Engineers need to carefully arrange the location and orientation of individual components based on circuit functionality and size requirements.
Circuit tracing refers to the design of wires or traces connecting electronic components. In embedded slot PCB, designers need to pay special attention to the layout and path of traces to ensure the stability and reliability of signal transmission. Carefully designed circuit traces can minimize signal attenuation and crosstalk, improving circuit performance.
The location and size of the slot have a significant impact on the functionality and appearance of the embedded slot PCB. Designers need to reasonably arrange the position and size of the slots according to the size and shape of the internal components of the slots to ensure that the internal components can be perfectly embedded in them without affecting the stability and reliability of the overall circuit.
When designing an embedded slot PCB, thermal management is an important factor that cannot be ignored. Since embedded slot PCBs often operate in space-constrained environments, effective thermal management measures need to be taken to prevent circuit overheating, which can lead to performance degradation or damage. Designers can optimize thermal management through proper thermal design, material selection, and circuit layout.
Finally, the design of embedded slot PCB also needs to consider its adaptability under different environmental conditions. Designers need to choose materials and processes that meet the requirements of specific application scenarios to ensure that the embedded slot PCB can work stably under various extreme temperatures, humidity and pressure, and has good shock resistance and dustproof performance.
In summary, key factors in embedded slot PCB design include component layout, circuit traceability, slot location and size, thermal management, and environmental suitability. By fully considering these factors, designers can create high-performance, high-reliability embedded slot PCBs to meet the needs of various application scenarios.
What is the process of manufacturing an embedded slot PCB?
The process of manufacturing embedded slot PCBs involves multiple complex steps, from design to final product, requiring precision craftsmanship and strict control. The manufacturing process of embedded slot PCB will be introduced in detail below:
In the process of manufacturing embedded slot PCB, the first step is the design stage. The design team uses professional PCB design software, such as Altium Designer or Cadence Allegro, to draw the PCB layout and circuit connection diagrams based on the needs and specifications provided by the customer. At this stage, key factors such as component layout, slot location and size, and circuit tracing are focused to ensure the accuracy and feasibility of the design.
After completing the design, the next step in the manufacturing process is to prepare the raw materials. Usually, the substrate material of PCB is FR-4 glass fiber reinforced epoxy resin. In addition, other materials are required, such as copper foil, glue, etc. These raw materials undergo stringent quality checks before being used for manufacturing.
Graphicalization is to convert the designed PCB drawings into the graphical files required in the actual manufacturing process. This step is usually completed by specialized software, which generates corresponding graphical files based on the design drawings to facilitate the implementation of subsequent manufacturing processes.
During the printing process, the graphic file is transferred to the PCB substrate. This process uses layer-by-layer coverage and photolithography technology to print the designed patterns and circuit graphics onto the PCB substrate, and uses acid etching or alkali etching technology to remove unnecessary copper foil to form the required circuit pattern.
After printing is completed, the PCB substrate needs to be gold-plated to improve its conductivity and corrosion resistance. Gold plating processes such as HASL (Hot Air Solder Leveling) or ENIG (Electroless Nickel Immersion Gold) are usually used to protect the PCB surface through the gold plating layer.
The final step is to mount the electronic components onto the PCB to form the final embedded slot PCB product. This process, called plug-in assembly, requires soldering various components to the PCB through automated equipment or manual operations, and conducting necessary testing and quality inspections.
Through the above steps, the manufacturing process of embedded slot PCB from design to finished product is completed. The entire process involves multiple professional technologies and equipment and requires strict control and supervision to ensure that the quality and performance of the final product meet customer requirements.
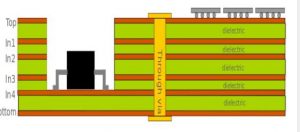
Embedded Slot PCB
How much does it cost to manufacture an embedded slot PCB?
Manufacturing embedded slot PCB involves costs in many aspects, including design, materials, manufacturing processes, labor costs, etc. Understanding these cost factors is critical to developing a budget and ensuring project success.
First, design cost is one of the primary considerations in manufacturing embedded slot PCBs. Professional PCB design requires experienced engineers and advanced design software, which will increase design costs. Complex design requirements may require more design hours and resources, increasing costs.
Secondly, material cost is an important part of manufacturing embedded slot PCB. The price of common PCB materials such as FR-4 fiberglass reinforced epoxy resin depends on factors such as thickness, number of layers, and special requirements. In addition to the substrate material, there is also the cost of surface treatment materials (such as metal plating) and embedded components.
Manufacturing processes also have an impact on costs. Different manufacturing processes may require different equipment and techniques, affecting costs. For example, high-precision hole milling and laser cutting technology may increase manufacturing costs, but can improve production efficiency and quality.
Labor costs are another important aspect. Manufacturing embedded slot PCBs requires skilled operators and technicians to operate the equipment, monitor the production process and control quality. Their wages and training costs directly impact manufacturing costs.
In addition to these direct costs, there are also indirect costs to consider, such as equipment maintenance, transportation costs and market competition, which may have an impact on manufacturing costs.
Taking the above factors into consideration, the cost of manufacturing embedded slot PCB can be adjusted according to the requirements and budget of the specific project. Generally speaking, custom embedded slot PCBs cost more, but can provide better performance and solutions suitable for specific applications. Therefore, when formulating a budget, it is necessary to comprehensively consider aspects such as design requirements, material selection, manufacturing processes, and labor costs to ensure the successful implementation of the project.
What materials are used in embedded slot PCB?
As a specially designed printed circuit board, embedded slot PCB uses a variety of materials in its manufacturing process. Each material has specific characteristics and functions, providing important support for the performance and reliability of the circuit board.
The substrate material of embedded slot PCB usually uses FR-4 glass fiber reinforced epoxy resin. This material has excellent electrical and mechanical properties to meet the requirements of most applications. The advantages of FR-4 substrate include high temperature resistance, moisture resistance and high mechanical strength, making it suitable for use in various environmental conditions.
The conductive layer is the core part of the embedded slot PCB, and copper is usually used as the conductive material. Copper has good electrical conductivity and mechanical properties. During the PCB manufacturing process, it is usually covered in the form of thin copper foil on the surface of the substrate to form circuit connection lines and soldering surfaces.
The surface treatment of embedded slot PCB plays a key role in soldering and connection. Common surface treatment materials include:
HASL (Hot Air Solder Leveling): Through tin immersion and hot air blowing, a tin layer is formed on the soldering surface, providing good soldering performance and corrosion resistance.
ENIG (Electroless Nickel Immersion Gold): The copper layer is first plated with nickel and then gold to form a protective layer on the metal surface to improve welding performance and surface flatness.
Embedded slot PCB usually requires packaging devices and filling slots. The packaging material plays an important role in the protection and stability of the circuit board. Common packaging materials include epoxy resin, polyimide (PI), etc. These materials have good high temperature resistance and mechanical strength, which can protect the device and provide reliable support.
In addition to the above core materials, manufacturing embedded slot PCB also requires some auxiliary materials, such as solder paste, insulation layer, filling material, etc. These materials play a supporting role in the manufacturing process, ensuring the integrity and performance of the circuit board.
To sum up, the manufacturing of embedded slot PCB involves the selection and application of multiple materials that work together on different parts of the circuit board to ensure its performance and reliability. Choosing the right material combination is one of the keys to manufacturing high-quality embedded slot PCBs.
Who makes embedded slot PCBs?
In modern electronics manufacturing, the manufacturing of embedded slot PCBs is a precise and complex task that requires experienced manufacturers to ensure product quality and performance. In our company, we have an experienced team responsible for embedded slot PCB manufacturing. At the same time, we also cooperate with some excellent suppliers to jointly ensure the high quality and reliability of our products.
Our manufacturing team consists of a group of professional engineers and technicians with many years of experience. They have deep industry knowledge and technical capabilities, and have extensive experience in the field of embedded slot PCB manufacturing. From design review to monitoring of the production process, our team always ensures product quality with a high degree of professionalism and rigor.
In addition to our own manufacturing team, we also work with some excellent suppliers to provide us with the necessary materials and equipment. These suppliers have undergone strict screening and evaluation and have reliable supply capabilities and high-quality products. They work closely with us to ensure the product’s production process runs smoothly and provide the required support and service in a timely manner.
Our cooperative relationships with our suppliers are based on the principles of mutual trust and win-win. By working closely with them, we are able to jointly respond to market challenges, meet customer needs, and continuously improve product quality and technical levels. We firmly believe that through continuous efforts and innovation, we will be able to provide customers with better quality embedded slot PCB products, bringing greater value and competitive advantage to their applications.
Overall, our company is jointly responsible for manufacturing high-quality embedded slot PCB products through the expertise of our in-house team and close collaboration with our suppliers. We are committed to providing reliable solutions to our customers and establishing long-term and stable cooperative relationships with them.
What are the characteristics of great customer service?
Excellent customer service is the cornerstone of any successful business. It is not just about meeting customer needs, but also the process of creating value and providing pleasant experiences for customers. Here are a few key characteristics that define great customer service:
Great customer service starts with good communication. This means understanding customer needs, opinions and feedback and being able to communicate information clearly and in a timely manner. Through active listening and effective communication, you can build a trusting relationship with your customers.
Responding promptly when customers have questions or needs is critical. Quick response demonstrates respect and attention to customers, helps improve customer satisfaction and enhances customer loyalty.
Excellent customer service requires empathy, the ability to understand customers’ needs and feelings, and providing reasonable support and assistance based on the actual situation. Compassion can bring companies closer to their customers and build closer relationships.
Reliability is one of the key characteristics of customer service. Customers want to be able to rely on companies to provide stable, consistent service, whether it’s product quality or after-sales support. Only through reliable performance can a business win the trust and trust of its customers.
Excellent customer service requires professionalism, including deep product knowledge, problem-solving skills, and a courteous and respectful attitude toward customers. Professionalism is not only reflected in technical level, but also includes comprehensive understanding and satisfaction of customer needs.
To sum up, excellent customer service is not only the process of meeting customer needs, but also the key to establishing a good relationship with customers. Through good communication, responsiveness, compassion, reliability and professionalism, businesses can enhance their customer experience, become more competitive and achieve long-term business success.
FAQs
What are Embedded Slot PCBs used for?
Embedded Slot PCBs find applications in various electronic devices, including smartphones, tablets, industrial control systems, etc. They are particularly suitable for applications where space is limited or stringent performance requirements exist.
What is the typical design cycle for Embedded Slot PCBs?
The design cycle for Embedded Slot PCBs varies depending on the complexity of the design and the required specifications. Generally, the design cycle can range from a few weeks to several months.
How do I choose the right manufacturer for Embedded Slot PCBs?
Choosing the right manufacturer for Embedded Slot PCBs requires consideration of several factors. It’s essential to evaluate the manufacturer’s experience, technological capabilities, quality control systems, and customer service levels. Additionally, examining past projects and customer reviews can provide valuable insights into the manufacturer’s capabilities.
What materials are commonly used in Embedded Slot PCBs?
Embedded Slot PCBs typically utilize FR-4 glass-reinforced epoxy resin as the substrate material due to its excellent electrical and mechanical properties. Surface treatments such as HASL (Hot Air Solder Leveling) or ENIG (Electroless Nickel Immersion Gold) are commonly employed to enhance solderability and reliability.
What are the key challenges in manufacturing Embedded Slot PCBs?
Manufacturing Embedded Slot PCBs presents several challenges, including precise routing and milling of slots, ensuring dimensional accuracy, maintaining signal integrity, and achieving uniform plating thickness. Overcoming these challenges requires advanced equipment, meticulous process control, and skilled personnel.
How can I optimize the cost of manufacturing Embedded Slot PCBs?
Optimizing the cost of manufacturing Embedded Slot PCBs involves various strategies, including design simplification, material selection optimization, process optimization, and bulk purchasing. Collaborating closely with the PCB manufacturer and leveraging their expertise can also help identify cost-saving opportunities.