Flip Chip Package Substrate Firm we have produced the best samllest bump pitch with 100um, the best smallest trace are 9um. and the smallest gap are 9um. most of the design are 15um to 30um trace and spacing.
In the ever-evolving field of PCB engineering, flip chip packaging substrates have become the focus of attention with their unique position. As a PCB engineer with ten years of practical experience, an in-depth study of this technology started a fascinating journey into the core of modern electronic packaging.
Flip chip packaging substrate, as one of the cutting-edge technologies of electronic packaging, plays a key bridge role.
Flip chip packaging substrates have demonstrated excellent performance in dealing with high-density interconnect (HDI) and other advanced packaging requirements, making them an indispensable choice for electronic engineers.
From a structural point of view, the flip chip packaging substrate usually consists of a multi-layer structure, including a base material, a conductor layer, an insulating layer and a metal layer. This sophisticated yet compact design makes it ideal for compact space and complex circuitry requirements in advanced electronic equipment.
In terms of production technology, improved HDI manufacturing technology and innovative semi-additive manufacturing technology have further promoted the evolution of flipped chip packaging substrates. These advanced manufacturing processes provide greater precision and controllability in the fabrication of substrates, ensuring higher performance in small-sized devices while still maintaining excellent stability.
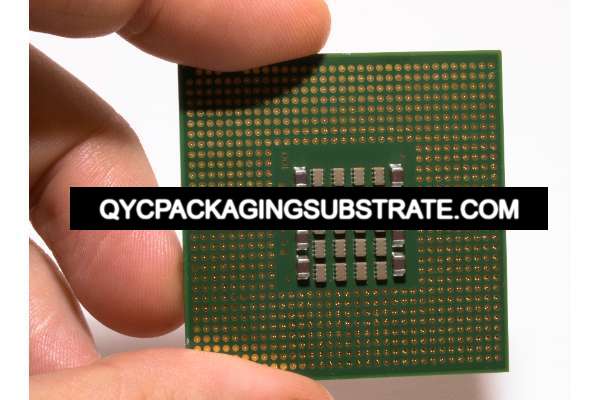
Flip Chip Package Substrate
Overall, flipped chip packaging substrates represent the pinnacle of continuous technological innovation in the field of PCB engineering. In-depth study of this field not only helps understand its critical role in modern electronic devices, but also provides engineers with the opportunity to expand their design and manufacturing skills. In this evolving field, flipped chip packaging substrates will continue to lead the way in future electronic packaging technology.
What is the key function of flipping the chip packaging substrate?
In the vast ocean of modern electronic packaging, the flipped chip packaging substrate is a bright pearl, carrying the complex electrical and mechanical connections between the semiconductor chip and the package. As a PCB engineer with ten years of hands-on experience, digging into the core capabilities of flip chip packaging substrates will reveal a fascinating world of electronic engineering.
The core function of flipping the chip packaging substrate is to provide a solid foundation for the chip mounting process. This is not just a simple task, but a sophisticated engineering art that involves the electrical and mechanical connections between semiconductor chips and packages.
First, let’s focus on this solid foundation. In the design of the flipped chip packaging substrate, engineers focused on ensuring that it has sufficient strength and stability. Such a solid foundation can not only withstand complex working environments and challenges, but also provide a safe habitat for the chip.
Critical electrical connections are another mission of flipping the chip packaging substrate. Through carefully designed electrical connection structures, the substrate becomes a bridge for information transmission between the semiconductor chip and the package. This connection not only requires efficient signal transmission, but also takes into account the optimization of electrical performance to ensure system reliability and stability.
Mechanical connections are an integral part of flipping the chip packaging substrate. Through ingenious design, engineers ensure that the substrate can firmly accommodate the chip while ensuring that no mechanical displacement occurs during operation of the device. This solid mechanical connection is key to long-term system operation and provides a reliable foundation for equipment performance.
Overall, the core function of flip chip packaging substrate is to play a key role in the electronic packaging arena. It is not only a solid foundation for semiconductor chips, but also an exquisite engineering of electrical and mechanical connections. By in-depth understanding and application of this technology, we can better promote the development of electronic engineering and create more advanced, efficient and reliable electronic systems.
What are the different types of flip chip packaging substrates?
In the field of PCB engineering, the diversity of flip chip packaging substrates not only meets different engineering needs, but also provides flexibility and innovation for various application scenarios. The types of these substrates vary based on their focus and use, primarily including high-density interconnect (HDI) and materials customized for specific functions.
High-density interconnect (HDI) substrate is an important type of flip chip packaging, and its design focuses on achieving higher density interconnection in a limited space. This substrate uses advanced process technology, including micro-circuit, micro-hole and complex stacked structure, to meet the needs of modern electronic equipment for small, lightweight and high performance. The unique design of HDI substrate makes it an ideal choice for portable electronic devices such as mobile phones and tablet computers.
Conversely, there is a distinct focus on flip chip packaging substrates tailored for specific functionalities. These substrates are intricately designed to cater to the unique requirements of specific applications, incorporating an array of specialty materials and processes to address diverse engineering challenges. For instance, in high-frequency applications, specialized dielectric materials may be essential to ensure the stability of signal transmission. Similarly, applications operating in high-temperature environments may demand the use of temperature-resistant materials to guarantee stability and reliability.
This diversity of substrate types ensures that suitable solutions can be found in the electronics industry, whether in communications, medical, automotive or industrial control fields. Engineers can select the appropriate type of flip chip packaging substrate based on their specific needs to achieve optimal performance and reliability in their designs.
Overall, these different types of flip chip packaging substrates demonstrate flexibility and versatility in PCB engineering. By in-depth knowledge and understanding of these different types of substrates, engineers can better cope with challenges in different fields and promote the continuous development of electronic technology.
How to distinguish packaging substrate and IC packaging technology? What are the classifications of chip packaging technology?
In today’s rapidly developing electronics field, it is crucial for engineers to have a deep understanding of the classification of chip packaging technologies. This understanding spans the spectrum from traditional packaging methods to innovative flip-chip technologies, and engineers are tasked with skillfully selecting the right technology for a specific application to ensure optimal performance.
Traditional packaging method
Conventional packaging methods represent one of the earliest approaches to chip packaging technology. This technique entails the placement of a chip onto a substrate, followed by the utilization of wires to establish connections between the chip and the substrate. While these packaging methods are straightforward and well-suited for specific applications with low power and frequency requirements, their limitations become increasingly evident as electronic devices strive for enhanced performance and compact design.
Advanced flip chip technology
Flip chip technology represents the forefront of modern chip packaging. In this technology, chips are mounted upside down on a substrate, with electrical connections made through slightly bent metal connections. This upside-down configuration provides a shorter signal propagation path, which reduces signal latency and significantly improves performance. Flip-chip technology also manages heat more efficiently because the chip is in direct contact with the cooling system, helping to lower temperatures and improve stability.
Diversified flip chip technology classification
Within flip chip technology, there are various classifications, including:
Ball Grid Array (BGA): Uses spherical solder joints to connect chips and substrates, providing higher connection density and better heat dissipation performance.
Chip-scale packaging (CSP): The chip is directly packaged on it, which reduces the size and weight of the package and is suitable for small mobile devices.
2.5D and 3D packaging: These technologies introduce multiple chip layers, enabling more compact designs and higher performance, but also create more complex manufacturing and thermal challenges.
For engineers, selecting the appropriate packaging technology depends on the requirements of the specific application. In computer systems pursuing high performance, 3D packaging may be chosen to integrate multiple processors. In thin and light mobile devices, CSP may be preferred to reduce volume and weight. When making decisions, engineers need to weigh factors such as performance, cost, cooling effectiveness and manufacturing feasibility.
What are the differences between flipped chip packaging substrates and traditional PCBs?
In the evolution of PCB engineering, flip chip packaging substrates and traditional PCBs exhibit a series of key differences that impact the design and performance of electronic systems. Although they are similar in some respects, the two technologies differ significantly in structure, application, and performance.
Basic structure and materials
The flip chip packaging substrate is different from traditional PCB in basic structure and materials. Flip chip packaging substrates usually use more advanced materials to adapt to advanced chip packaging technology. This difference can be reflected in the manufacturing process of the substrate, especially in the preparation of high-density interconnect (HDI) substrates, where more compact and lightweight designs are achieved through more refined material selection and process control.
Introduction of substrate-like PCB (SLP)
Substrate-like PCB (SLP) is one of the important innovations in modern electronic system design, and flipping chip packaging substrates makes it easier to integrate with this innovation. Compared to traditional PCBs, SLP has a higher level of integration and a smaller form factor, making it ideal for compact electronic devices. The combination of flip chip packaging substrate and SLP provides more flexible design options for electronic systems and supports smaller devices.
Advantages of High Density Interconnect (HDI) Substrates
High-density interconnect (HDI) substrates play a key role in modern electronic devices, and flip chip packaging substrates are more suitable for this trend. Compared with traditional PCBs, HDI substrates have more layers, more compact wiring, and smaller apertures, providing more connection options for high-performance electronic systems. This gives flip chip packaging substrates an advantage under high-density wiring requirements, providing more flexible design solutions.
Different orientations in motherboard design
The motherboard is the core of the electronic system, and flipping the chip packaging substrate presents different orientations in the motherboard design. Due to its advanced packaging technology, flipping the chip packaging substrate enables more compact and higher-performance motherboard designs, providing more computing and processing capabilities for advanced electronic devices.
What are the main structures and production technologies for flipping chip packaging substrates?
As one of the cutting-edge technologies of modern PCB engineering, Flip Chip Package Substrate has demonstrated outstanding innovation in its core structure and production technology. A deep understanding of the underlying structure of this technology and the production process behind it is crucial to understanding its unique value in the field of electronic packaging.
Core structure
The core structure of the flip-chip package substrate is designed to enable reliable connection and optimized performance between the semiconductor chip and package. Key components include high-density interconnect (HDI) technology, which provides a more compact layout for chips, and innovative substrate designs to accommodate the needs of advanced electronic devices. This design allows the chip to be flipped and mounted directly on the substrate, minimizing the path for electrical signal transmission, thus improving overall performance.
Improved HDI manufacturing technology
Improvements in high-density interconnect technology have driven the manufacturing of flip chip packaging substrates. By implementing finer lines and higher-density connections on the substrate, improved HDI manufacturing technology provides greater flexibility and room for performance upgrades. This enables smaller, lighter electronic devices while increasing the speed and reliability of signal transmission.
Innovative semi-additive manufacturing technology
Semi-additive manufacturing technology holds a significant position in the fabrication of flip chip packaging substrates. It enables the meticulous addition of necessary metal layers onto the substrate’s surface, elevating the precision and controllability of the connections. Beyond simplifying the manufacturing process, this technology concurrently trims production costs, rendering it more competitively advantageous.
By combining improved HDI manufacturing technology and semi-additive manufacturing technology, flip chip packaging substrates have made significant progress in modern substrate production. This combination of advanced structure and production technology brings more compact, efficient and reliable solutions to the electronics industry, helping to promote the continuous development of PCB engineering.
Frequently Asked Questions (FAQs) for Flipping Chip Package Substrates
When exploring the esoteric world of flipped chip packaging substrates, engineers and enthusiasts often encounter a series of questions. Below are answers to some key questions designed to provide readers with a clear understanding of the important aspects of flipping chip packaging substrates.
What is a flip chip packaging substrate and how is it different from a traditional PCB?
The flip chip packaging substrate is a critical component in integrated circuit assembly, providing a solid foundation for the chip. Compared with traditional PCBs, its main difference is its focus on achieving more efficient chip connections and heat dissipation to improve the performance and reliability of integrated circuits.
What are the main advantages of flipping the chip packaging substrate?
The main advantage of this substrate is that it provides a shorter electrical connection path to the chip, increases signal transmission speed, and accommodates more connections on the same chip area. In addition, flip chip technology also has excellent heat dissipation performance, helping to maintain the stability of the integrated circuit.
What are the different types of flip chip packaging substrates and what applications are they suitable for?
Flip chip packaging substrates are available in diverse types and are suitable for various application scenarios. High-density interconnect (HDI) substrates are available for applications requiring higher connection density, while other materials and designs are tailored to meet different engineering needs.
What are the key innovations in production technology for flipped chip packaging substrates?
The production technology of substrates has undergone several key innovations. Improved HDI manufacturing technology improves performance by enhancing interconnect density, while improved semi-additive manufacturing technology introduces greater precision and efficiency into substrate manufacturing. The continuous evolution of these technologies is driving the development of flipped chip packaging substrates.
What is the future trend of flipping chip packaging substrates in electronic engineering?
In the future, flipped chip packaging substrates will continue to develop and play a more important role in electronic engineering. As technology continues to advance, we can expect more advanced, higher-performance flip chip packaging substrates to support innovative electronic devices and systems.