Glass Package Substrates Manufacturer. Advanced semiconductor glass packaging substrate manufacturer, we offer the Advanced Glass Substrates with high quality,The finished glass substrate will be more flat, have a high temperature effect, and last longer.
In modern electronic equipment, printed circuit boards (PCBs) play an irreplaceable role. However, with the continuous advancement of technology, a key type of PCB, the glass packaging substrate, has gradually become the focus of the electronics industry. As a senior PCB engineer, I know the importance of understanding the processes behind glass packaging substrate manufacturers. This not only ensures product quality and performance, but also helps promote innovation and development in the electronics industry.
What is a glass packaging substrate?
When it comes to the manufacturing of electronic devices, glass packaging substrates are a topic of great concern. These substrates are high-performance electronic substrates based on glass substrates that have a series of excellent properties and are therefore widely used in various high-demand fields.
First, glass packaging substrates are often used in high-frequency, high-speed, and high-density applications. This means they are capable of performing well in scenarios that require fast signal transmission and complex circuit layouts. Whether it is servers in data centers, communication equipment or medical diagnostic equipment, glass packaging substrates can meet their high-performance needs.
Second, glass packaging substrates excel in electrical performance. The glass substrate itself has excellent insulation properties, which can effectively isolate circuits and reduce signal interference. In addition, the dielectric constant and dielectric loss angle of the glass packaging substrate are very stable, ensuring the accuracy and stability of signal transmission.
In addition to electrical properties, glass packaging substrates also have excellent thermal properties. Glass materials have good thermal conductivity and can effectively dissipate heat and maintain a stable operating temperature of electronic devices. This is critical for high-power-density electronic devices to prevent overheating damage and performance degradation.
Most importantly, glass packaging substrates offer reliability. Glass substrates are less susceptible to environmental conditions such as moisture, heat and chemicals. This allows the glass packaging substrate to maintain stable performance in harsh environments and ensures long-term reliable operation of the equipment.
To sum up, the glass packaging substrate is a powerful and reliable electronic substrate that is suitable for various high-performance and high-demand application fields. Their excellent electrical properties, thermal properties and reliability make them an integral part of modern electronic device manufacturing.
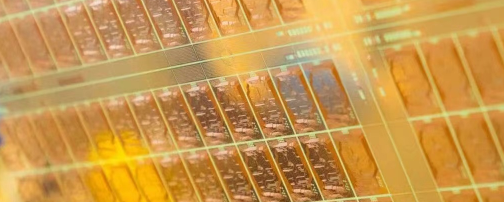
Glass Package Substrates
How to design glass packaging substrate?
Designing a glass packaging substrate is a comprehensive engineering task that requires consideration of many factors to ensure the performance and reliability of the final product. Here are a few key factors to consider when designing glass packaging substrates:
Circuit Layout: Good circuit layout is the key to a successful design. Engineers need to carefully plan component placement to minimize signal path length and cross-talk. By rationally laying out circuit components, signal delay and power consumption can be reduced and system performance improved.
Interlayer connection: Glass packaging substrates usually have multi-layer structures, and appropriate interlayer connection solutions need to be designed. Engineers need to consider factors such as signal transmission paths, power consumption distribution, and thermal management to ensure the stability and reliability of inter-layer connections.
Power management: Effective power management is key to designing high-performance glass packaging substrates. Engineers need to evaluate the power consumption requirements of the system and design appropriate power supply networks and power management circuits to ensure stable operation of the circuit and minimize energy loss.
EMI/RFI Suppression: Electromagnetic interference (EMI) and radio frequency interference (RFI) can negatively affect circuit performance. When designing glass packaging substrates, engineers need to take measures to reduce the circuit’s sensitivity to external interference, and add filters and shielding structures when necessary to ensure the stability and reliability of the circuit.
To effectively solve the above problems, engineers often utilize advanced design software and simulation tools. These tools help engineers perform circuit simulation and analysis to optimize routing, signal integrity and power distribution to ensure design accuracy and reliability. Working closely with suppliers and manufacturers, engineers also receive advice on material selection, manufacturing processes and technical support to ensure the final product meets customer needs and standards.
What is the manufacturing process of glass packaging substrates?
The manufacturing process of glass packaging substrates is a complex and precise process that requires multiple critical steps to complete. These steps are detailed below:
Material preparation: First, manufacturers need to select high-quality glass substrates and other necessary materials, such as metallization materials and dielectric materials. The selection of glass substrate is crucial because it directly affects the electrical performance, thermal performance and reliability of the substrate.
Graphic design: After the material preparation is completed, the engineer converts the circuit graphic design into a CAD file. This step is the foundation of the entire manufacturing process and requires precise design and layout to ensure circuit performance and stability.
Graphic transfer: Next, the CAD file is transferred to the substrate surface using photolithography technology. Photolithography is a high-precision pattern transfer method by projecting a CAD file onto a photosensitive coating and then using chemical processing to transfer the pattern to the substrate surface.
Deposition: Once the pattern transfer is completed, metal or other materials need to be deposited on the surface of the substrate to form the circuit pattern. This is usually achieved through techniques such as chemical vapor deposition (CVD) or physical vapor deposition (PVD). The deposited material will fill the voids in the pattern and form electrical connections.
Etching: After deposition is completed, chemical or mechanical methods need to be used to remove unnecessary materials to form the final circuit pattern. This step is called etching, and techniques such as etching fluids or lasers are usually used to remove excess material, leaving the desired circuit structure.
Inspection and testing: Finally, manufactured substrates undergo rigorous inspection and testing to ensure they meet specifications and quality requirements. This includes visual inspection, dimensional measurements, electrical testing and reliability testing, etc. Only substrates that pass these inspections and tests can be considered qualified and enter subsequent assembly and production processes.
Throughout the manufacturing process, strict quality control and process monitoring are crucial to ensure the performance and reliability of the final product. The manufacturing of glass packaging substrates requires highly specialized equipment and technology, and only professionally trained and experienced staff can complete this task.
How much does a glass packaging substrate cost?
As an important part of the electronics industry, the cost of glass packaging substrates is affected by many factors, including manufacturing processes, material selection, specification requirements, and order quantity. A deeper understanding of the impact of these factors on cost will help customers better understand the pricing mechanism of glass packaging substrates.
The manufacturing process of glass packaging substrates directly affects the cost level. For example, glass packaging substrates produced using advanced processes and equipment tend to have a higher cost, but can also provide higher performance and reliability. In contrast, traditional manufacturing processes, while less expensive, may limit product performance and functionality.
Material is one of the key factors in the cost of glass packaging substrates. Different substrate materials, metallization materials, dielectric materials and solder materials will all have an impact on costs. For example, high-quality substrate materials and metallization materials tend to be more expensive but provide better electrical and thermal performance, thereby increasing the cost of the product.
Customer specifications for glass packaging substrates will also affect cost levels. Customized and high-performance products often require additional processes and materials, resulting in relatively higher costs. In contrast, standard-sized products cost less but may not meet customer-specific needs and requirements.
Order quantity is one of the important factors affecting the cost of glass packaging substrates. Generally speaking, mass production can reduce the cost of unit products because production costs can be effectively amortized through economies of scale. On the contrary, the cost of small batch production is relatively high because the production efficiency is low and the economic benefits of scale cannot be achieved.
To sum up, the cost of glass packaging substrates is affected by a variety of factors, including manufacturing process, material selection, specification requirements and order quantity. Generally speaking, the cost of customized and high-performance products is higher, while the cost of mass-produced products with standard specifications is relatively low. Therefore, when customers choose glass packaging substrates, they should comprehensively consider various factors and choose the product that best suits their needs.
What is the material of the glass packaging substrate?
In the manufacturing process of glass packaging substrates, the materials used play a vital role in their performance and reliability. The following are key materials commonly found in glass packaging substrates:
Glass substrate: Glass substrate is the basic material for glass packaging substrates. It is usually produced using special processes and has excellent flatness and surface quality. The choice of glass substrate depends on the application requirements. Common glass materials include borosilicate glass, quartz glass, etc.
Metalized materials: Metalized materials are mainly used to form a conductive layer on the surface of glass substrates. Commonly used metals include copper and silver. These metals have good electrical conductivity and corrosion resistance, ensuring the stability and reliability of circuits.
Dielectric Materials: Dielectric materials are used to fill the gaps between conductive layers to prevent short circuits between the conductive layers and provide insulating properties. Polyimide film is a commonly used dielectric material with excellent heat resistance and mechanical strength, and can meet the requirements of high temperature and high frequency environments.
Solder: Solder is used to connect electronic components to glass packaging substrates. It is usually a metal alloy, such as tin-lead alloy or lead-free solder. Good solder can ensure the stability and reliability of the welding connection while reducing resistance and power consumption.
These materials play a key role in the manufacturing process of glass packaging substrates, and their selection and processing have a significant impact on the quality and performance of the final product. By rationally selecting and optimizing these materials, glass packaging substrates can meet the requirements of various complex application environments, providing a solid foundation for performance improvement and reliable operation of electronic devices.
Who manufactures glass packaging substrates?
The manufacturing of glass packaging substrates not only requires highly specialized technology and equipment, but also requires reliable manufacturers to ensure product quality and supply reliability. In the glass packaging substrate industry, supplier selection is crucial, and as a professional glass packaging substrate manufacturer, we are committed to providing customers with excellent products and services.
Our company is a PCB manufacturer with many years of experience, dedicated to producing high-performance, high-reliability glass packaging substrates. We have advanced production equipment and technical team to meet the different needs and requirements of our customers. As a comprehensive PCB supplier, we provide a full range of services from design to production to ensure that our customers’ projects can proceed smoothly and achieve expected goals.
Our glass packaging substrate products have the following features:
High-Quality Materials: We use high-quality glass substrates and metallized materials to ensure the product has excellent electrical and thermal properties.
Advanced process: We introduce advanced manufacturing processes and equipment, including photolithography, deposition, etching and other processes to ensure the accuracy and stability of product manufacturing.
Strict quality control: We implement a strict quality management system and strictly control and inspect every aspect from raw material procurement to production and manufacturing to ensure stable and reliable product quality.
Customized services: We provide customized solutions, designing and producing according to customers’ specific needs and requirements, ensuring that the products meet customer expectations.
Timely delivery: We have efficient production capacity and supply chain management system, which can deliver customer orders in time to meet customers’ production needs.
As one of the leaders in the glass packaging substrate industry, we are committed to providing customers with the highest quality products and services, and growing and developing together with them. If you have any questions or needs about our products and services, please feel free to contact us and we will serve you wholeheartedly!
What are the 5 qualities of great customer service?
Excellent customer service is crucial for PCB manufacturers. Here are 5 qualities of great customer service:
Respond quickly: As a PCB manufacturer, it is crucial to respond quickly to customer inquiries and questions. Respond to customers’ emails, phone calls or online messages in a timely manner to ensure that customers receive the support and solutions they need as soon as possible. This not only shows respect and concern for customers, but also helps to establish good communication and cooperation.
Expertise: Excellent customer service requires PCB manufacturers to have extensive industry experience and expertise. Customers may face a variety of technical and process challenges, and they need to be able to rely on manufacturers to provide accurate, effective advice and technical support. Therefore, the manufacturer’s team should be professionally trained and possess in-depth technical knowledge in understanding and applying circuit board manufacturing.
Customized services: Customer needs vary, so providing customized solutions is one of the important attributes of good customer service. PCB manufacturers should be able to provide personalized product design and manufacturing services based on customers’ specific needs. Whether it’s special materials, specific processes or custom sizes, manufacturers should actively listen to their customers’ needs and strive to provide solutions that meet their requirements and expectations.
Quality Assurance: Another key attribute of great customer service is strict assurance of product quality. PCB manufacturers should establish a sound quality management system to strictly control the quality of each link from raw material procurement to production and manufacturing to final delivery. By using advanced testing equipment and technology, manufacturers can ensure that product quality is stable and reliable and meets customer requirements and standards.
After-sales support: Excellent customer service is not only about service during the sales process, but also includes after-sales support and service. Once the product is delivered, the manufacturer should provide comprehensive after-sales support, including technical training, repair and maintenance, and problem solving. Customers may encounter various problems during use, and they need to be able to get help and support in a timely manner to ensure the normal operation of the product and customer satisfaction.
To sum up, excellent customer service is crucial for PCB manufacturers. Through attributes such as responsiveness, expertise, customized services, quality assurance and after-sales support, manufacturers are able to build long-term and stable customer relationships and achieve win-win development. Therefore, PCB manufacturers should continue to improve their service levels to meet the growing needs and expectations of customers.
FAQs
What application areas are glass packaging substrates suitable for?
Glass packaging substrates are widely used in many application fields. They are particularly suitable for high-frequency, high-speed, and high-density electronic applications, such as 5G communication equipment, medical diagnostic instruments, aerospace navigation systems, etc. Because glass substrates have excellent electrical properties and stability, they are widely used in fields that require high performance and reliability.
What is the maximum size of a glass packaging substrate?
The size of glass packaging substrates is usually limited by manufacturing processes and equipment. Generally speaking, the maximum size of the glass packaging substrate can reach tens of centimeters or even larger. However, it should be noted that as the size increases, so does the manufacturing complexity and cost.
How long is the production cycle of glass packaging substrates?
The production cycle of glass packaging substrates usually depends on multiple factors, including order quantity, specification requirements and manufacturing processes. In general, the production cycle of customized glass packaging substrates may be longer than that of standard products. Typically, the production lead time can be anywhere from a few days to a few weeks, depending on the customer’s needs and the manufacturer’s production capabilities.
What are the advantages of glass packaging substrates compared with traditional FR4 substrates?
Glass packaging substrates have many advantages over traditional FR4 substrates. First, glass substrates have higher glass transition temperatures and thermal stability, allowing them to operate at higher temperatures without failure. Secondly, the glass packaging substrate has better dimensional stability and surface flatness, which is beneficial to the wiring and assembly of precision circuits. In addition, the dielectric constant and loss factor of the glass substrate are relatively low, enabling better signal transmission performance and anti-interference capabilities.
How do manufacturers of glass packaging substrates ensure product quality?
Manufacturers of glass packaging substrates usually adopt strict quality control measures to ensure stable and reliable product quality. These measures include raw material inspection, production process control, finished product inspection and product certification. Manufacturers will establish quality management systems based on international standards and customer requirements, and verify their quality management levels through certificates such as ISO certification. In addition, manufacturers will continue to improve processes and technologies to improve product quality and production efficiency.