We are a professional IC package substrate producer, we mainly produce ultra-small trace and spacing IC packaging substrate and HDI PCBs.
The material selection for flip chip package substrates holds significant importance. In flip chip packaging, various materials, such as organic substrates, ceramics, and silicon, are commonly utilized, each presenting distinct advantages and drawbacks. Organic substrates are known for their cost-effectiveness and lightweight properties but may have limitations in terms of thermal performance. Ceramics, renowned for their outstanding thermal conductivity and reliability, are of high quality but come with a premium price. Conversely, silicon substrates offer a cost-effective solution while striking a favorable balance between performance and affordability, rendering them a preferred choice in the industry. The material composition is a critical consideration directly influencing the functionality and cost-effectiveness of flip chip packaging.
As the electronics industry continues to develop, emerging materials and trends will also be discussed to help readers understand future IC packaging substrate material innovations. By gaining an in-depth understanding of these material options, readers will be able to better understand the design and performance of electronic devices and make informed decisions when selecting packaging substrate materials suitable for their projects.
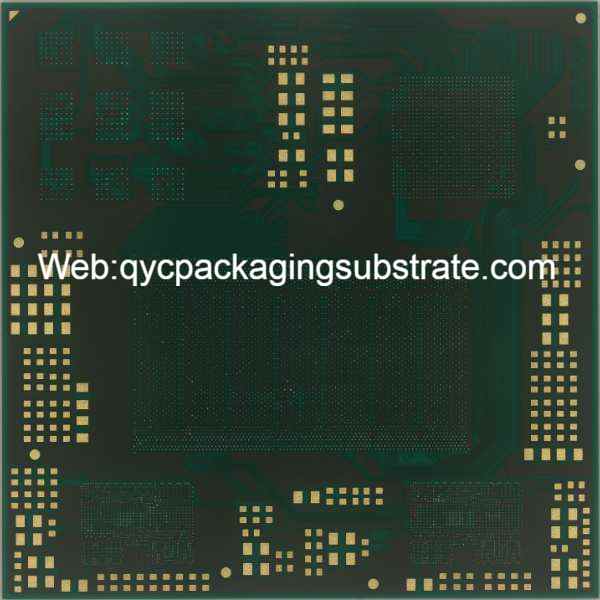
IC package substrate material
The Importance of IC Package Substrate Materials
The selection of materials holds a crucial and far-reaching significance in IC packaging. It serves as a linchpin, exerting direct influence over the package’s performance while also significantly shaping the reliability and cost-efficiency of electronic equipment. In this segment, we embark on a comprehensive exploration of how material selection influences packaging performance, underscoring the critical importance of choosing the appropriate materials tailored to specific applications.
Discuss the impact of material selection on packaging performance
The performance of an Integrated Circuit (IC) package hinges on a careful selection of materials with diverse physical, electrical, and thermal properties. Each material possesses its unique attributes in terms of thermal conductivity, dielectric constant, mechanical strength, and thermal resistance, all of which exert a direct influence on heat dissipation capacity, signal transmission speed, and structural stability of the package.
For instance, let’s consider thermal performance. Conversely, materials with inadequate thermal conductivity or high thermal resistance may lead to chip overheating, resulting in reduced performance and a shorter lifespan.
In the realm of electronic equipment, signal transmission speed is another critical factor. The selection of a material boasting a low dielectric constant can mitigate signal transmission delays, thereby accelerating the device’s response time. Furthermore, the mechanical strength of the chosen material is a vital consideration, as it holds a substantial sway over the package’s reliability and durability.
The need for appropriate material selection
When selecting IC packaging substrate materials, the specific needs of the application need to be carefully considered. Different applications may require different performance characteristics. For example, high-speed communications equipment may require materials with low dielectric constant and high thermal conductivity, while military equipment may place greater emphasis on mechanical strength and durability.
Therefore, appropriate material selection is a key factor in ensuring package performance and reliability. The wrong choice can result in reduced performance, increased failure rates and higher maintenance costs. Therefore, it is crucial to ensure appropriate material selection during the IC packaging process.
In summary, material selection has a profound impact on the performance and reliability of IC packages. Understanding the properties of different materials to meet specific application needs and adhering to appropriate material selection will help ensure superior performance and long-term reliability of electronic devices.
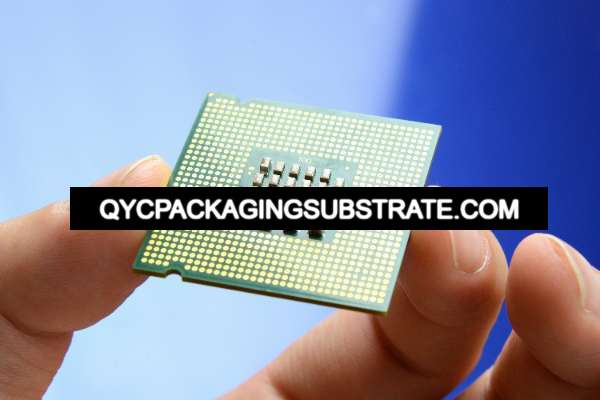
IC package substrate material
The most common IC packaging substrate materials
In the field of IC packaging, FR-4 and high-density interconnect (HDI) are the two most common material choices, each with unique characteristics and a wide range of applications.
FR-4(Flame Retardant-4)
FR-4 is a widely used fiberglass reinforced composite material known for its excellent electrical insulation properties. Its features include:
Electrical performance: FR-4 substrate has good insulation and can effectively isolate circuits and prevent interference between electronic components.
FR-4 is widely used in standard electronic equipment such as PCB manufacturing, communication equipment and consumer electronics. Its excellent insulating properties and mechanical strength make it the first choice for many electronic applications.
High Density Interconnect (HDI)
HDI substrate is an advanced technology used to meet the needs of modern electronic devices for higher performance and compact size. Its features include:
High density: HDI substrate uses fine lines and stacked layer design, which can accommodate more components in a relatively small area and provide higher circuit density.
Multi-layer design: HDI substrates can have multiple layers, making them very useful in the design of complex circuits.
Micro Lines: HDI allows the use of micro lines, providing higher signal speeds and performance.
Overall, FR-4 and HDI are the two most common IC packaging substrate materials, and they each play a key role in different types of applications. Selecting the appropriate material depends on the requirements of the specific application, including electrical performance, mechanical strength and space constraints. When selecting materials, these properties need to be weighed to meet the performance needs of the electronic device.
Key factors in material selection
There are several key factors to consider when selecting the appropriate IC packaging substrate material. These factors directly impact cost, performance and reliability. In this section, we’ll dive into these factors and provide suggestions on how to make trade-offs when choosing materials.
Cost-Effectiveness: Cost is often one of the first considerations in material selection. Different materials have different prices, and when a project has a limited budget, choosing the most cost-effective material is crucial.
Performance requirements: Different applications require different performance characteristics.
For instance, in high-speed communications equipment, the demand is for materials with minimal signal transmission losses, while high-frequency applications necessitate materials with low dielectric constants. Consequently, it becomes paramount to ensure that the chosen materials align with the specific performance prerequisites.
Reliability: The Dependability Factor
The reliability of a material stands as a paramount determinant in gauging its appropriateness for a given application. In certain contexts like aerospace or medical devices, material reliability takes center stage, significantly influencing the longevity and safety of the end product.Environmental requirements: Certain applications require materials to be corrosion-resistant or resistant to high temperatures. Environmental requirements will influence the choice of materials to ensure they perform well in harsh conditions.
Advice on how to make trade-offs when choosing
Clearly Define Performance Requirements: Before selecting materials, clearly defining the performance requirements of your project is key. This will help you focus on the most important properties when selecting materials.
Compare cost and performance: Conduct a cost-performance analysis to determine the most economical material that will meet performance needs. Sometimes, high-performance materials may not be the most economical option.
Consider future upgradeability: As technology continues to evolve, it’s also important that materials are upgradeable. Choosing materials that can adapt to future changes in performance needs may reduce long-term costs.
Conduct experiments and tests: Before final selection of materials, conduct experiments and tests to verify their performance and reliability. This will help reduce potential risks.
Consult an Expert: If you are unsure about material selection, consult a professional materials engineer or supplier who can provide you with valuable advice.
Balancing cost, performance and reliability is a complex task when selecting IC packaging substrate materials. However, clearly defining requirements, comparing the properties of different materials, considering future upgradeability, and working with a professional will help ensure that the best material is selected for your specific application.
Emerging Materials and Trends
Discuss emerging IC packaging substrate materials and future trends
As the electronics field continues to evolve, emerging IC packaging substrate materials and trends are shaping future packaging technologies. One emerging material that has attracted much attention is flexible substrate material, such as polyimide (PI) film. These flexible substrates are lightweight, thin, bend-resistant and highly reliable, making them suitable for mobile devices, wearable technology and foldable electronics.
Another emerging trend is material selection based on environmental protection and sustainability. Organic substrate materials, such as biopolymers and degradable materials, are receiving increasing attention. Not only do these materials reduce reliance on harmful chemicals, they also help reduce waste and lower your carbon footprint, thus complying with environmental regulations.
Impact of innovation on material selection
Innovation has always been the driving force in the IC packaging field. The emergence and adoption of new materials is critical to innovation. They give products greater design freedom, enabling the creation of novel electronic devices and solutions. Innovation also involves continuous improvements in materials processes and manufacturing techniques to ensure higher performance and reliability.
Innovations in material selection also have a positive impact on sustainability. By using environmentally friendly and biodegradable materials, the electronics industry can reduce its reliance on harmful chemicals, generate less waste, and use resources more efficiently during production. This innovation helps drive sustainable practices in electronics, allowing us to better meet future needs.
In short, emerging IC packaging substrate materials and trends not only change the face of packaging technology, but also promote the continuous development of the electronic field. The impact of innovation on material selection will continue to lead us towards a more sustainable and environmentally friendly future. Therefore, when selecting IC packaging substrate materials, it is important to pay close attention to these emerging materials and trends to ensure product competitiveness and sustainability.
Full text overview
In the field of modern electronics, the selection of IC packaging substrate materials is crucial.
IC packaging substrate is one of the core components of electronic equipment. It connects and supports chips, circuits and other key elements. Different applications require different performance characteristics, such as high frequency, high speed, thermal stability, etc. Correct material selection therefore ensures system performance and reliability.
FR-4 and high-density interconnect (HDI) are the two most common IC packaging substrate materials. They have their own advantages in different application fields. FR-4 is suitable for applications with general performance requirements, while HDI excels in high-density, high-performance environments. Understanding the properties and application scenarios of these materials can help engineers better select the appropriate materials to meet project needs.
Additionally, we explore key factors in material selection, including cost, performance, and reliability.
Finally, we highlight the impact of emerging materials and trends on IC packaging substrate material selection.
In summary, the selection of IC packaging substrate materials is a key factor in the success of electronic projects. When selecting materials, engineers should be thoughtful and make informed decisions based on performance and application needs, while also paying close attention to emerging materials and trends to ensure their projects can keep up with changing technology developments. By carefully selecting materials, we can ensure the performance and reliability of electronic systems and drive continued advancement in the field of electronics.