IC Packaging Substrate Producer. the Package Substrate will be made with BT materials, Rogers materials, High TG FR4 Base, Showa Denko and Ajinomoto High speed materials. or other types high speed materials and high frequency materials.
In the realm of modern electronics, the significance of IC packaging substrates cannot be overstated. These diminutive yet pivotal components serve as the linchpin of integrated circuit (IC) packaging, exerting a profound influence not only on the performance and reliability of electronic devices but also on the continuous evolution of the entire electronics industry. This article delves deeply into the realm of IC packaging substrates, underscoring their indispensable role in electronic devices.
IC packaging substrates operate as the central nervous system of contemporary electronic devices, bearing the crucial responsibilities of ICs while providing essential support and connectivity. They act as the conduit linking diverse components within electronic devices, facilitating data transmission, signal processing, and power distribution. Consequently, the design and performance of IC packaging substrates wield direct influence over the overall device’s functionality.
Beyond providing physical support for IC interconnection, IC substrates achieve connections between various functional elements through high-density wiring technologies. They also assume a pivotal role in thermal management, ensuring that ICs maintain optimal operating temperatures, thereby enhancing both performance and reliability. Moreover, the reliability and durability of IC substrates are paramount for the sustained operation of electronic devices over the long term.
In the subsequent sections, this article will embark on an extensive exploration of the various types of IC substrates, delving into their distinctive characteristics and their extensive spectrum of applications across the electronics industry. Furthermore, it will delve into forthcoming trends in IC substrates, shedding light on how innovation and sustainability practices are propelling advancements in the field of electronics. A comprehensive understanding of IC packaging substrates will deepen our appreciation of their pivotal role in modern technology.
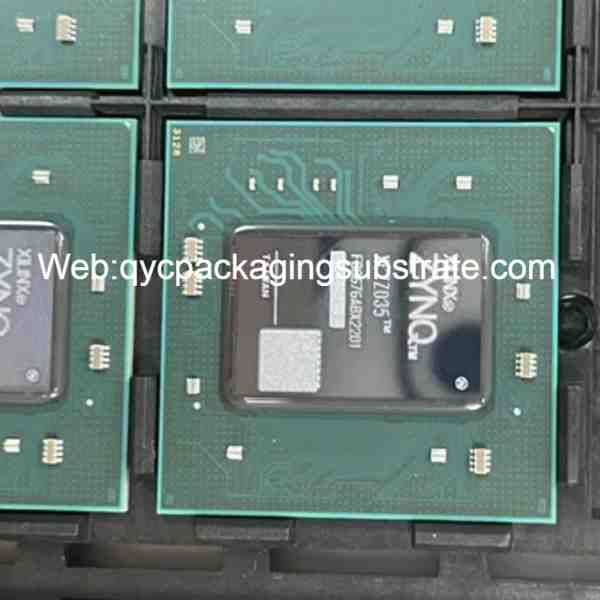
IC packaging substrates
What is an IC substrate?
In the realm of contemporary electronics, IC substrates assume a pivotal and indispensable role. These substrates are fundamental components of electronic devices, offering support and connectivity to integrated circuits (ICs) while playing a crucial part in the overall circuitry. Let’s delve into the fundamental concepts of IC substrates and their critical significance in IC packaging.
An IC substrate serves as a platform housing circuits and interconnecting components. It is typically fabricated from insulating materials, including printed circuit boards (PCBs) or other suitable options. These substrates feature layers of copper foil, which serve the purpose of establishing circuit connections and facilitating signal transmission. IC substrate designs can encompass multiple layers to cater to the demands of intricate circuitry and intricate connection requirements.
Key role in IC packaging
IC substrates serve as foundational components within the IC packaging process, serving a pivotal role in connecting IC chips to other essential electronic elements such as resistors, capacitors, inductors, as well as power and signal transmission lines. The precision and quality of these connections are of paramount importance, bearing a profound impact on circuit performance and reliability.
Furthermore, IC substrates assume a crucial function in the realm of thermal management. In the context of contemporary integrated circuits, which often generate substantial heat, IC substrate design must prioritize the facilitation of efficient heat conduction and dissipation solutions. This is indispensable to ensure that IC chips can operate at peak performance without succumbing to overheating issues.
Moreover, IC substrates fulfill a pivotal role in providing robust physical support and protection for the circuit. Typically designed to be compact and resilient, they act as a safeguard, shielding the IC chip from potential damage caused by mechanical stress and environmental factors.
In summation, IC substrates stand as indispensable components in the realm of modern electronics. They deliver vital connectivity, adeptly manage thermal considerations, and provide the essential physical support, all the while exerting a profound influence on the performance and reliability of electronic devices. An in-depth comprehension of IC substrate design and application is not only fundamental for grasping the operational principles of electronic devices but also holds substantial significance in propelling the continuous evolution of the electronic field.
Type of IC substrate
Here are some common IC substrate types along with their characteristics and application areas:
BGA (Ball Grid Array) board
BGA substrate is a common type of IC packaging substrate that uses a ball grid arrangement to connect the IC to the printed circuit board (PCB). Features of BGA substrate include:
High-density connections: The ball grid arrangement of the BGA substrate provides high-density connections, making it suitable for highly integrated ICs.
Good heat dissipation performance: Due to smaller connection points, the BGA substrate has better heat dissipation performance and is suitable for high-performance ICs.
Reliability: The solder connections to the BGA substrate are very reliable and resistant to vibration and temperature changes.
BGA substrates are widely used in electronic equipment manufacturing, communication technology, computer hardware and other fields.
FCBGA (Flip Chip Ball Grid Array) board
FCBGA substrate is an advanced IC packaging substrate type that uses flip chip technology to connect the IC to the PCB. Features of FCBGA substrate include:
Highly Integrated: FCBGA allows more connection points and smaller spacing, supporting highly integrated ICs.
Excellent thermal management: With shorter interconnect distances, FCBGA provides excellent thermal management performance for high-performance ICs.
Signal integrity: FCBGA substrate can reduce the time delay of signal transmission and help improve signal integrity.
FCBGA substrates are widely used in high-performance computing, network equipment and communication systems.
CSP (Chip Scale Package) board
The CSP substrate is a small IC packaging substrate that is comparable in size to the chip itself. Features of CSP substrates include:
Small size: CSP substrate is very small, suitable for compact devices and mobile devices.
Lightweight: Due to its small size, CSP substrates are very lightweight and suitable for portable devices.
Cost-Effective Manufacturing: The production costs for CSP substrates are notably economical, rendering them ideal for large-scale manufacturing operations.
Versatile Application: CSP substrates find extensive utility in a range of portable electronic products, including mobile phones, digital cameras, and wearable devices.
Diverse IC Substrate Types: Various IC substrate types exhibit distinct characteristics and application domains, tailored to cater to the varied requirements of different electronic devices.
These are some common IC substrate types, each type has unique characteristics and application areas to meet the needs of different electronic devices.
The key role of IC packaging substrate
IC packaging substrates play a vital role in the modern electronics industry, offering a high degree of versatility and diversity, with every aspect ranging from high-density wiring technology to thermal management and performance optimization to reliability and durability. Have a profound impact on the performance and reliability of electronic equipment.
High Density Cabling Technology
High-density wiring technology stands as a fundamental element in the contemporary design of electronic devices. It facilitates the interconnection of a greater number of electronic components and circuits within confined spaces, thereby yielding heightened performance and expanded functionality. The imperative for high-density wiring is driven by the ever-increasing need for modern electronic devices to be compact and lightweight. Achieving high-density wiring in IC packaging substrates is accomplished through multifaceted means, including multi-layer design, intricate and space-efficient circuit layout, and precise interconnection techniques. This not only elevates the performance of electronic devices but also reduces their physical footprint, rendering them more suitable for a diverse array of applications.
Thermal management and performance optimization
Efficient thermal management has consistently posed a significant challenge in the realm of electronic device design. In the modern landscape, electronic components and IC chips frequently operate at elevated temperatures, and excessive heat can result in performance deterioration, component failure, or a shortened operational lifespan. To address these thermal concerns, IC packaging substrates are strategically engineered to facilitate the effective management and dissipation of heat. They achieve this through the incorporation of thermal heat dissipation layers, thermally conductive materials, and heat dissipation structures, thereby ensuring that the device operates within an acceptable temperature range. This not only enhances equipment performance but also extends its operational life while simultaneously reducing the incidence of failures.
Reliability and durability
The reliability of connections is critical to the proper functioning of electronic devices. The IC packaging substrate uses high-quality interconnection technology to ensure that the connections between various components are strong and reliable and not easily disconnected or damaged. This ensures that the equipment remains highly reliable in a variety of application environments. In addition, the materials and designs of IC packaging substrates take durability into account and can withstand shock, vibration and temperature changes, ensuring that the device can operate normally under harsh conditions.
In essence, IC packaging substrates offer indispensable support for the contemporary design and production of electronic devices. They achieve this through high-density wiring techniques, adept thermal management, performance enhancement, and the fortification of reliability and durability. These pivotal functions are integral in addressing the demands of the ever-expanding electronics market, guaranteeing that equipment can operate at peak performance across a multitude of applications, thereby playing a pivotal role in advancing the electronics industry.
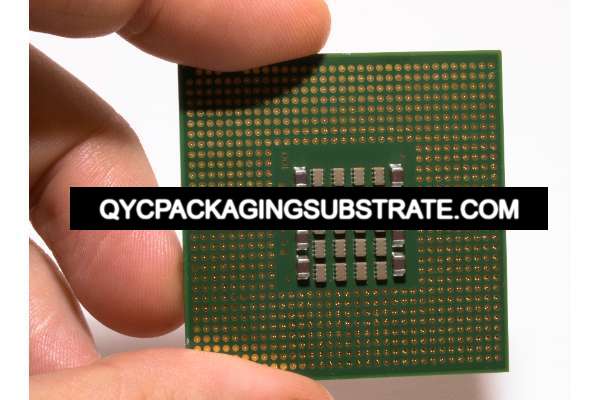
IC packaging substrates
Application of IC substrate in electronic industry
The following will introduce in detail the application cases of IC substrates in electronic equipment manufacturing, communication technology, military and aerospace fields.
Electronic equipment manufacturing
Through high-density wiring technology, IC substrates can achieve compact circuit designs, thereby improving device performance. This means electronic devices can be smaller and lighter while offering more functionality. In addition, the IC substrate also has excellent heat dissipation performance, which helps the device maintain a stable temperature during long-term use and ensures reliability. Therefore, IC substrates not only improve performance but also provide superior reliability in electronic device manufacturing.
Communication technology
In the field of communication technology, the application of IC substrates provides support for high-speed data transmission and connections. For example, in wireless communication modules, IC substrates are used to connect various radio frequency (RF) components and antennas to ensure efficient signal transmission. This is crucial for achieving stable communication. IC substrates also provide more compact circuit designs through high-density wiring technology, adapting to growing communication needs. From 5G networks to Internet of Things (IoT) devices, IC substrates enable communications technology to better meet growing data transmission requirements.
Military and aerospace fields
In the military and aerospace fields, the importance of IC substrates is even more prominent. These fields require highly reliable electronic systems that can function properly in extreme environments. IC substrate durability and reliable connections are critical in these areas. They are resistant to extreme temperatures, vibrations and electromagnetic interference, ensuring that electronic systems function properly during critical moments. In addition, the high-density wiring technology of IC substrates allows for more miniaturized electronic system designs, improving the performance of aircraft, satellites and military equipment.
In summary, IC substrates play a key role in electronic equipment manufacturing, communication technology, and military and aerospace fields. Not only do they improve performance and reliability, they also support the continued growth of the electronics industry. In the ever-changing electronics field, the criticality of IC substrates cannot be underestimated, making huge contributions to our modern life and technological progress.
Future trends of IC packaging substrates
IC packaging substrate is a key component of the electronics industry. As technology continues to evolve, its future trends will have a profound impact on the entire industry. The following are the future trends of IC packaging substrates:
Impact of future technology
The development of future technology will have a revolutionary impact on IC packaging substrates. First, 3D stacking technology will further promote high-density wiring of IC packaging substrates. This technology allows multiple packaging layers to be stacked vertically, increasing circuit density and performance. High-density wiring not only means smaller package size, but also provides more design freedom, making innovation more possible.
Second, advances in materials science will improve the heat dissipation performance of IC packaging substrates.
Sustainability and environmental trends
As sustainability and environmental protection trends emerge, the design and manufacturing of IC packaging substrates will be more eco-friendly. New manufacturing processes and material options will reduce the generation of waste and hazardous materials, helping to reduce pressure on the environment. In addition, sustainability practices include extending the life cycle of equipment and reducing resource waste.
In addition, the sustainability of IC packaging substrates also involves energy efficiency. The new generation of packaging substrates will be designed to be more energy efficient and reduce the power consumption of electronic devices. This is critical for extending battery life, reducing energy consumption and mitigating your carbon footprint.
In short, the future of IC packaging substrates is full of hope. By embracing innovative technologies and firmly advancing sustainable practices, IC packaging substrates will continue to advance the electronics industry, providing faster, more powerful and greener solutions. Advances in this industry will not only meet current needs, but will also shape the future technology landscape and move us towards a more sustainable and environmentally friendly future.