LED Ceramic Substrate Manufacturer. Ceramic materials PCBs, Ceramic materials LED PCBs, Ceramic materials BGA substrates Vendor. we offer Ceramic Substrate from 1 layer to 20 layers.
LED ceramic substrate is an indispensable component of modern electronic equipment and plays an important role in LED lamps, automotive lighting and other fields. As the support and connection basis for LED chips, LED ceramic substrates have excellent heat dissipation and electrical insulation properties. This article will delve into the manufacturing process of LED ceramic substrates, from design, process to cost, presenting readers with a comprehensive perspective and helping readers better understand the importance of LED ceramic substrates and their manufacturing process.
What is LED ceramic substrate?
LED ceramic substrate is a basic material used to support and connect LED chips. Its excellent heat dissipation and electrical insulation properties make it an ideal choice for LED lamps. In the LED lighting industry, LED ceramic substrates play a vital role. It not only provides the support structure of the LED chip, but also effectively transfers current to the LED chip and effectively disperses the generated heat through heat dissipation, keeping the operating temperature of the LED chip within a safe range.
First of all, LED ceramic substrate has excellent heat dissipation performance. The LED chip will generate a large amount of heat during its working process. If the heat cannot be dissipated in a timely and effective manner, the performance of the LED chip will be reduced or even damaged. The LED ceramic substrate has excellent thermal conductivity and can quickly conduct heat to the external environment to ensure the stable operation of the LED chip.
Secondly, LED ceramic substrate has good electrical insulation properties. LED chips need to receive current when working, and LED ceramic substrates can provide good electrical insulation to prevent safety issues such as current leakage and short circuits, ensuring the reliability and safety of LED lamps.
Because LED ceramic substrates have these excellent characteristics, they have been widely used in the design and manufacturing of LED lamps. It can be used not only for indoor and outdoor lighting, but also for automotive lighting, medical equipment, communication equipment and other fields. In general, LED ceramic substrates, as the core component of LED lamps, provide reliable support for the development and promotion of the LED industry.
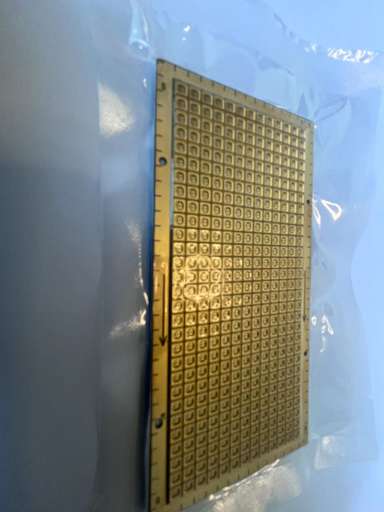
Ceramic Substrate
How to design LED ceramic substrate?
The design of LED ceramic substrate is a key step to ensure the performance and reliability of LED equipment. The design process requires comprehensive consideration of multiple factors, including circuit layout, heat dissipation requirements, and mechanical suitability, to meet the needs of LED equipment in different application scenarios. This article will delve into the design process and related key points of LED ceramic substrates.
First of all, circuit layout is one of the important considerations in LED ceramic substrate design. Reasonable circuit layout can reduce interference and noise in the circuit and improve the stability and reliability of signal transmission. During the design process, engineers need to reasonably arrange the layout of circuit components based on the functions and requirements of the LED equipment, minimize line lengths and crossovers, and reduce the circuit loop area to reduce the possibility of electromagnetic interference.
Secondly, heat dissipation requirements are an important aspect that cannot be ignored in the design of LED ceramic substrates. As an optoelectronic device, LED generates a lot of heat during its working process, and good heat dissipation design can effectively reduce the operating temperature of the LED chip and extend the service life of the LED equipment. During the design process, engineers need to consider the layout and size of the radiator, select appropriate heat dissipation materials, and rationally design heat dissipation channels to improve heat dissipation efficiency.
In addition, mechanical suitability is also one of the important considerations in the design of LED ceramic substrates. LED devices usually require mechanical connections to external structures, so the size, shape and mounting hole locations of the LED ceramic substrate need to match the external structure. During the design process, engineers need to reasonably design the shape and structure of the substrate based on the actual application scenarios and installation requirements of the LED equipment to ensure that the LED equipment can be installed accurately and stably in the target structure.
In order to ensure the accuracy and reliability of LED ceramic substrate design, engineers usually use CAD software to design, simulate and analyze. CAD software has powerful functions that can help engineers quickly draw circuit diagrams and layout diagrams, conduct circuit simulation and analysis, discover potential design problems and solve them, thereby ensuring that the performance and reliability of the LED ceramic substrate meet expected requirements.
To sum up, the design of LED ceramic substrate is a complex process that takes multiple factors into consideration and requires engineers to have rich experience and professional knowledge. By properly considering factors such as circuit layout, heat dissipation requirements, and mechanical suitability, and using CAD software for design and analysis, the performance and reliability of LED ceramic substrate design can be ensured to meet the needs of LED equipment in different application scenarios.
What is the manufacturing process of LED ceramic substrate?
The manufacturing process of LED ceramic substrates is a complex and precise process that involves multiple key steps, from material preparation to final testing. The manufacturing process of LED ceramic substrates will be introduced in detail below.
The manufacturing process of LED ceramic substrates first requires the preparation of the required materials, which mainly include ceramic substrate materials, metallized materials, semiconductor chips, etc. These materials undergo rigorous quality control and testing to ensure they meet manufacturing requirements.
In the process of manufacturing LED ceramic substrates, the printed circuit board (PCB) plays a vital role. PCB manufacturing usually includes substrate pretreatment, photolithography, etching, metallization, electroplating and other steps. These steps require precision equipment and process control to ensure PCB quality and performance.
Once the PCB is manufactured, the next step is to print the circuit pattern on the ceramic substrate. This step usually uses screen printing technology or photolithography technology to print the desired circuit pattern onto the surface of the ceramic substrate.
Soldering is an important step in securing electronic components to ceramic substrates. Through welding technology, LED chips, resistors, capacitors and other components are connected to the printed circuit pattern. The welding process requires precise temperature control and welding process to ensure welding quality and reliability.
The last critical step is to test the manufactured LED ceramic substrate. Testing includes functional testing, electrical testing, optical testing and temperature testing. Through these tests, it can be ensured that the LED ceramic substrate meets the specification requirements and has good performance and reliability.
In general, the manufacturing process of LED ceramic substrates involves multiple key steps, each of which requires precise process control and quality management. Only through strict manufacturing processes and high-level technical strength can high-quality LED ceramic substrate products be produced.
How to control the manufacturing cost of LED ceramic substrates?
As one of the indispensable components in the modern electronics field, LED ceramic substrates’ manufacturing cost control is an important issue that manufacturers need to seriously consider. The manufacturing cost of LED ceramic substrates is affected by multiple factors, including material cost, process complexity and production scale.
First of all, material cost is one of the important factors affecting the manufacturing cost of LED ceramic substrates. LED ceramic substrates usually use materials with high thermal conductivity, such as alumina, silicon nitride, etc. The prices of these materials directly affect the overall manufacturing cost. When selecting materials, manufacturers need to comprehensively consider factors such as the material’s thermal conductivity, electrical insulation performance, and cost to optimize cost performance.
Secondly, process complexity is also one of the important factors affecting the manufacturing cost of LED ceramic substrates. The manufacturing process of LED ceramic substrates involves multiple links, including material preparation, PCB manufacturing, circuit patterning, welding, testing, etc. The selection of different process flows and process parameters will directly affect the efficiency and cost of manufacturing. Therefore, manufacturers need to continuously optimize process processes, improve production efficiency, and reduce manufacturing costs.
In addition, production scale is also one of the important factors affecting the manufacturing cost of LED ceramic substrates. Typically, the larger the production scale, the lower the cost per unit product. Therefore, LED ceramic substrate manufacturers need to reasonably plan the production scale and achieve large-scale production based on market demand and their own production capabilities, thereby reducing the manufacturing cost of unit products.
In order to effectively control the manufacturing costs of LED ceramic substrates, manufacturers can take a series of measures. First, through optimized design, the amount of material used is reduced and material costs are reduced. Secondly, through continuous improvement of process flow, production efficiency is improved and manufacturing costs are reduced. Finally, through effective supply chain management, raw material procurement costs are reduced and the flexibility and response speed of the supply chain are improved. To sum up, controlling the manufacturing cost of LED ceramic substrates requires manufacturers to comprehensively consider factors such as materials, processes, and production scale, and take corresponding measures to optimize to improve product competitiveness and market share.
What is the material of LED ceramic substrate?
As a key electronic component, LED ceramic substrate plays a vital role in LED lamps and other electronic devices. It not only requires good electrical insulation properties, but also requires excellent heat dissipation characteristics to ensure the stable operation of the LED chip. Therefore, the material selection of LED ceramic substrate is crucial.
Usually, the manufacturing materials of LED ceramic substrates mainly include high thermal conductivity materials such as aluminum oxide and silicon nitride. These materials have the following characteristics:
First of all, alumina is a common LED ceramic substrate material. It has excellent thermal conductivity and electrical insulation properties, and can effectively dissipate the heat generated by the LED chip to the external environment, thereby ensuring that the operating temperature of the LED chip is within a controllable range. In addition, alumina also has good mechanical strength and chemical stability, and is suitable for various processing processes.
Secondly, silicon nitride is also a commonly used LED ceramic substrate material. Silicon nitride has higher thermal conductivity and lower thermal expansion coefficient than aluminum oxide, allowing it to dissipate heat more efficiently. This makes silicon nitride widely used in applications that require higher heat dissipation performance, such as high-power LED lamps and automotive lighting systems.
In addition to aluminum oxide and silicon nitride, some other materials are also used in the manufacture of LED ceramic substrates, such as aluminum borate, zirconia, etc. These materials have different properties and applications and can be selected based on specific needs.
In general, the material selection of LED ceramic substrate directly affects its heat dissipation performance and electrical performance, thereby affecting the performance and reliability of the entire LED lamp. Therefore, during the design and manufacturing process of LED ceramic substrates, the selection of materials must be extremely careful to ensure that the heat dissipation needs of the LED chips can be met and the performance and reliability of LED lamps can be improved.
Who makes LED ceramic substrates?
The manufacturing of LED ceramic substrates is a complex process involving cooperation between multiple parties, in which suppliers play a vital role. In the LED ceramic substrate manufacturing industry, choosing the right supplier is crucial to product quality and production efficiency. So, who makes LED ceramic substrates? let’s see.
First of all, the manufacturing of LED ceramic substrates is usually completed by professional LED ceramic substrate manufacturers. These manufacturers have advanced production equipment and rich experience to provide customized solutions according to customer needs. Not only are they able to ensure product quality, they are also able to provide professional technical support and advice during the manufacturing process.
In terms of supplier selection, many companies will choose to cooperate with LED ceramic substrate manufacturers who can provide a package of services. These manufacturers can not only provide standardized LED ceramic substrate products, but also carry out customized design and production according to customer needs. They usually have a complete supply chain management system and can meet customer orders in a timely and accurate manner.
As one of the suppliers of LED ceramic substrates, we are committed to providing customers with high-quality LED ceramic substrate products and excellent services. We have advanced production equipment and technical team to meet the various needs of our customers. Whether it is small batch customization or mass production, we are able to provide customers with satisfactory solutions.
In addition, we also focus on communication and cooperation with customers to ensure that our products can truly meet customer needs. Adhering to the principle of “customer first, quality first”, we continuously strive to improve product quality and service levels, and grow together with our customers to create a better future.
To sum up, the manufacturing of LED ceramic substrates involves multi-party cooperation, and suppliers are a crucial part of it. As one of the suppliers of LED ceramic substrates, we will continue to uphold a professional, responsible and honest attitude to provide customers with high-quality products and services.
FAQS
How do I ensure proper thermal management with LED Ceramic Substrates?
Proper thermal management involves designing the substrate to efficiently conduct heat away from the LEDs and dissipate it into the surrounding environment. This may include incorporating features like thermal vias, metal layers, or heatsinks, as well as selecting appropriate materials and mounting techniques.
Are there any reliability concerns with LED Ceramic Substrates?
LED Ceramic Substrates are generally highly reliable due to their robust construction and excellent thermal properties. However, proper handling, assembly, and operation are important to prevent issues such as thermal stress, cracking, or delamination, especially in high-power LED applications.
What are some common applications of LED Ceramic Substrates?
LED Ceramic Substrates are used in a wide range of applications including general lighting, automotive lighting, display screens, signage, horticultural lighting, and industrial lighting where high brightness, efficiency, and reliability are required. They are particularly suited for high-power LED applications where thermal management is critical.
How does LED Ceramic Substrate compare to other substrates?
Compared to traditional substrates like FR4 (fiberglass-reinforced epoxy laminate), LED Ceramic Substrate offers superior thermal conductivity and reliability, especially in high-power LED applications.
Can LED Ceramic Substrate be customized?
Yes, LED Ceramic Substrate can be customized in terms of size, shape, and thermal properties to meet the specific requirements of different LED applications.