Package substrate fabrication and FCBGA Packaging prototypes. We use advanced Msap and Sap technology, High multilayer interconnection substrates from 2 to 20 layers.
As an indispensable element within contemporary electronic devices, the packaging substrate assumes a pivotal role. Primarily, it functions as a foundational support and connection platform for electronic components, facilitating the transportation and interconnection of essential circuit elements to realize the functionalities of electronic equipment. This centrality is not only inherent in its structural role but also in its direct influence on equipment performance, stability, and reliability.
Beyond its role in end-product manufacturing, the significance of the packaging substrate’s manufacturing process extends to the overall quality and performance of electronic devices. A detailed exploration of the manufacturing process sheds light on crucial aspects such as optimizing circuit layout, enhancing thermal efficiency, and improving electrical performance. This not only contributes to heightened product quality but also propels ongoing innovation within the electronics industry.
As we delve into the manufacturing intricacies of packaging substrates, we aim to underscore their critical role in electronic devices while emphasizing the pivotal importance of their manufacturing process. This approach serves as both an in-depth analysis of packaging substrate technology and a comprehensive review of the contemporary electronics manufacturing industry. Through this detailed exposition, readers gain a more profound understanding of the central position occupied by packaging substrates and their irreplaceable contribution to propelling the development of the electronic field.
Overview of the manufacturing process of packaging substrates
Packaging substrate manufacturing is a meticulous integration of precision processes aimed at encapsulating electronic components onto a stable substrate, enabling their proper functionality within electronic devices. This intricate procedure involves a sequence of steps that must be adhered to rigorously, spanning from the meticulous preparation of raw materials to the stringent quality control measures applied to the final product.
Commencing with a thorough comprehension of the design, the manufacturing process for packaging substrates intricately considers the structure of the circuit board (PCB) and the type and layout of components. This meticulous attention to detail ensures that the end product aligns seamlessly with the specific needs of electronic devices. Positioned at a critical juncture within the electronics manufacturing industry, this process plays a pivotal role, directly influencing the performance and reliability of the resulting equipment.
The production of packaging substrates assumes a critical role in the realm of electronic manufacturing, primarily serving to establish a stable foundation for the organized arrangement of electronic components, forming a cohesive circuit system. This system encompasses a variety of components, including integrated circuits, capacitors, and resistors.
In contemporary electronic devices, packaging substrates play a pivotal role in supporting and interconnecting diverse electronic components. The intricate structure and exacting manufacturing processes associated with these substrates directly influence the performance, power consumption, and overall dimensions of the device. Hence, the precision and control exerted during the manufacturing process are paramount in ensuring the stability and functionality of electronic devices.
Furthermore, the manufacturing of packaging substrates is continually evolving to adapt to the introduction of new technologies and design concepts. Innovations, ranging from high-density interconnect technologies to advancements in material selection, are propelling the entire electronics manufacturing industry forward.
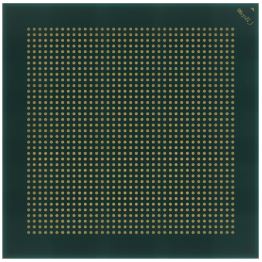
Package Substrate Fabrication
Key steps in the manufacturing process of packaging substrates
In the manufacturing process of packaging substrates, key raw materials include electronic grade substrates, conductive materials (such as copper foil), insulating materials, and soldering materials. The quality and characteristics of these raw materials directly affect the performance and reliability of the final packaging substrate.
Selecting high-quality raw materials that meet specific requirements is key to ensuring packaging substrate performance and sustainability. Reasonable selection of raw materials can help improve product stability, reduce energy consumption, and meet environmental standards.
Printed circuit board (PCB) manufacturing
The manufacturing of PCB involves steps such as the conversion of circuit diagram design, selection of board materials, and circuit diagram printing. In the packaging substrate, the PCB serves as the support structure and circuit transmission medium for electronic components, so its manufacturing quality is directly related to the performance of the entire packaging substrate.
Circuit component installation
The mounting of circuit components is a critical step in the packaging substrate manufacturing process and involves precision soldering and layout processes. The accurate execution of this step directly affects the availability and stability of the entire electronic device.
Precise placement of circuit components helps reduce resistance, increase signal transmission speed, and ultimately improve the device’s response time and efficiency.
Encapsulation and encapsulation
Encapsulation and encapsulation are critical steps in caching circuit components and connections into a protective layer from the external environment. This helps protect circuits from the outside environment and improves the durability of electronic devices.
Using modern packaging technologies, such as ball grid array (BGA) or dual in-line packaging, helps improve connectivity and durability.
Quality control and testing
Introducing a comprehensive quality control process, including visual inspection, automated testing, etc., to ensure that each package substrate meets design specifications.
Comprehensive testing of the packaging substrate, including electrical properties, temperature tolerance, etc., to ensure that it performs stably and reliably in actual use.
By optimizing each critical step of the packaging substrate manufacturing process, selecting high-quality raw materials, and adopting advanced technologies and sustainable practices, we can achieve superior performance, sustainability, and innovation in packaging substrates in the electronics field.
Technological Innovation in Manufacturing Processes
In the continuous evolution of packaging substrate manufacturing, the industry is adopting a series of innovative technologies to adapt to the needs of the rapidly developing electronics industry. The following are some of the latest technologies in current packaging substrate manufacturing:
Advanced material applications: Use new generation materials, such as flexible substrates and advanced thermal conductive materials, to improve the performance and durability of packaging substrates.
The integration of artificial intelligence (AI) and automation technology into manufacturing processes defines intelligent manufacturing and automation. This approach leverages intelligent manufacturing systems to optimize operations, automate production processes, enhance manufacturing efficiency, and ultimately reduce costs.
Three-dimensional packaging technology, exemplified by integrated stack packaging, is at the forefront of advancements. This technology aims to elevate the density of circuit components, consequently enhancing the overall performance of electronic equipment.
In the realm of manufacturing precision, advanced printing and coating technology play a crucial role. High-precision printing and coating techniques are employed to ensure the accuracy and consistency of circuit board manufacturing, thereby contributing to the heightened reliability of the final product.
The application of these latest technologies has brought significant efficiency gains and product quality improvements in the packaging substrate manufacturing process:
Improve production efficiency: The introduction of smart manufacturing and automation technology makes the production process more efficient and precise. Machine learning algorithms optimize production plans, ensure optimal utilization of raw materials, and quickly detect and correct potential problems during manufacturing.
Increase product performance: Using advanced materials and three-dimensional packaging technology, electronic components on the packaging substrate can be more tightly integrated, increasing circuit density, thereby improving device performance and response speed.
Guarantee product quality: High-precision printing and coating technology ensures the consistency of the manufacturing process of each packaging substrate, reduces manufacturing errors and defects, and improves the quality and reliability of the final product.
Taken together, these technological innovations not only promote the technical level of packaging substrate manufacturing, but also provide a more reliable and high-performance foundation for the manufacturing of electronic equipment. As these technologies evolve further, we can expect to see packaging substrates play an even more important role in the electronics industry.
Sustainable practices in the manufacturing process of packaging substrates
Sustainability practices play a key role in the manufacturing process of packaging substrates, not only helping to reduce environmental impact but also improving the overall quality and competitiveness of the product. Below is a detailed discussion of sustainable practices in packaging substrate manufacturing:
Against the backdrop of current environmental concerns, packaging substrate manufacturers are taking a series of practical sustainability measures to reduce resource waste and environmental impact.
Energy efficiency improvement: Adopt advanced production technology and equipment to reduce energy consumption and carbon footprint.
Waste management: Implement efficient waste recycling and treatment mechanisms to minimize the burden on the environment.
Green Supply Chain: Work with sustainable suppliers to ensure sustainable practices throughout the supply chain.
The packaging substrate manufacturing industry has seen a series of best practices that not only drive sustainability at the company level but also set an example throughout the industry. Here are some of the industry’s best practices for driving sustainability:
Standards and Certification: Standards and certification bodies within the industry are gradually developing and promoting sustainability standards to encourage companies to fulfill their social responsibilities.
Industry cooperation: Through industry associations and cooperative organizations, we develop and promote common sustainability goals and jointly promote the progress of the entire industry.
Technological innovation: Promote technological innovation and find more environmentally friendly and efficient manufacturing methods by investing in research and development.
Information sharing: When it comes to sustainable practices, information sharing within the industry is key. By sharing successes and challenges, progress across the industry can be accelerated.
By integrating these sustainability practices, the manufacturing of packaging substrates is progressively transitioning towards a more environmentally conscious and socially responsible trajectory. This shift not only supports the sustainable development of the planet but also bolsters a company’s reputation and market standing. Moving forward, it is anticipated that these practices will undergo further evolution to align with the increasing environmental and social responsibility expectations.
In conclusion
The manufacturing process of packaging substrates is a critical component within the electronic manufacturing landscape, and its pivotal steps significantly impact the performance and reliability of the end product. The ensuing overview highlights key stages in the packaging substrate manufacturing process, underscoring the central roles of technological innovation and sustainable practices in propelling advancements in the electronics manufacturing sector.
Raw Material Preparation: The initial phase of the manufacturing process involves meticulous selection and preparation of raw materials. Opting for high-quality, sustainable materials is paramount to ensuring the ultimate performance of the final product.
Printed Circuit Board (PCB) Manufacturing: This phase encompasses intricate printing and etching processes integral to determining the layout and interconnection of electronic components. The precision and intricacy of PCB manufacturing are crucial elements influencing the overall functionality of electronic devices.
Circuit component installation: Precisely install electronic components on the PCB to ensure that the circuit connections between components are correct.
Encapsulation and encapsulation: In this step, the packaging substrate is wrapped or encapsulated to provide protection and stability while ensuring thermal dissipation and electromagnetic compatibility.
The culmination of the manufacturing process involves quality control and testing, ensuring that each packaging substrate meets stringent standards and specifications. This meticulous phase guarantees the reliability and performance of the final product.
Simultaneously, the field of packaging substrate manufacturing is undergoing a transformative phase marked by technological innovation. This includes the incorporation of advanced materials, high-precision manufacturing techniques, and intelligent manufacturing technology. These innovations not only enhance production efficiency but also elevate the overall performance of the products.
In response to the escalating societal emphasis on sustainability, packaging substrate manufacturers are adopting diverse practices to align with environmental goals. This involves the utilization of recyclable materials, enhancements in energy efficiency, and effective waste management. Beyond reducing environmental impact, these practices contribute to cultivating a socially responsible image for the companies.
In summary, the continual evolution and innovation in packaging substrate manufacturing processes are propelling the electronics manufacturing industry forward. Emphasizing quality, technological advancements, and sustainability enables manufacturers to distinguish themselves in a highly competitive market, offering consumers more reliable and high-performance electronic products. This ongoing trend is expected to drive further progress and development in the electronics field in the future.