Package substrate materials introduction and package substrate manufacture. You can use BT series core, High frequency series Core, high speed series Core materials. We use advanced Msap and Sap technology, High multilayer interconnection substrates from 2 to 20 layers.
In the manufacturing of modern electronic devices, packaging substrates play a vital role. As the supporting structure of electronic components, packaging substrates not only provide physical support for circuit connections, but also play an important role in circuit design and performance optimization. As a medium for information transmission and energy conversion, it carries the core functions of electronic products.
Nonetheless, the efficacy of a packaging substrate extends beyond its design and manufacturing process; the selection of materials plays a pivotal role. This article delves deeply into the distinct properties of various packaging substrate materials and scrutinizes their specific impact on the performance of electronic devices. By offering a thorough analysis of material properties related to high-frequency applications, thermal management, signal integrity, and more, our objective is to equip engineers and decision-makers with essential insights for making informed decisions in packaging substrate design.
Through this comprehensive examination, we not only enhance our understanding of the central importance of packaging substrates but also illuminate the trajectory for the future development of the electronics industry. Let’s embark on a deeper exploration of this seemingly unassuming yet indispensable component—the packaging substrate—and unveil its irreplaceable role in shaping the performance of electronic products.
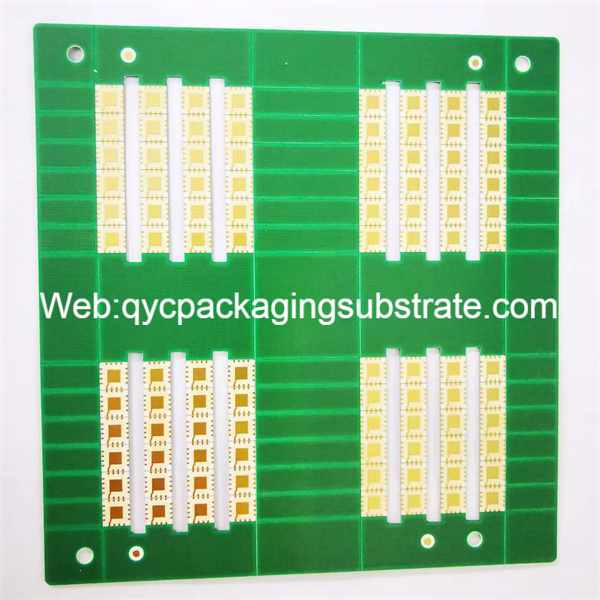
Package substrate materials
Types of packaging substrate materials
In the manufacturing of modern electronic equipment, the selection of packaging substrate materials is crucial and directly affects the performance and reliability of the product. The following are some common packaging substrate materials, the characteristics and applicable scenarios of each material.
FR-4 (fiberglass reinforced epoxy resin)
FR-4 is a common and affordable packaging substrate material with the following properties:
Mechanical Strength: FR-4 material has excellent mechanical strength and is able to withstand the daily use of electronic devices.
Electrical Performance: In typical circuit applications, FR-4 demonstrates commendable electrical performance, making it well-suited for low-frequency and medium-frequency circuits where reliable conductivity is crucial.
Cost-Effectiveness: Thanks to its cost efficiency, FR-4 finds extensive use in a myriad of consumer electronics products, providing an economical yet reliable choice for manufacturers in the industry.
High Density Interconnect (HDI)
HDI is a specialized packaging substrate material suitable for scenarios that require higher packaging density and performance.
High-density design: HDI allows for a more compact layout, providing higher connection density for small and lightweight electronic devices.
Multi-layer design: HDI supports multi-layer design, which helps improve the performance and complexity of circuits.
Adaptable to high-frequency applications: For applications that need to process high-frequency signals, HDI can usually provide better performance.
Optimal performance and cost-effectiveness in various application scenarios can be achieved through thoughtful material selection. In this process, engineers must carefully weigh the unique requirements of electronic devices, encompassing considerations such as circuit frequency, mechanical strength, and heat dissipation needs. By gaining a thorough understanding of the distinctive properties of each material, engineers can align product design with specific requirements, thereby fostering advancements in the electronics industry.
Material selection and performance relationship of packaging substrate
Material selection for the packaging substrate plays a critical role in influencing performance. The following are key considerations for different performance aspects:
Material Selection in High Frequency Applications
In high-frequency environments, proper material selection is critical. The transmission of high-frequency signals requires materials with low dielectric loss and propagation delay. For example, PTFE (polytetrafluoroethylene)-based materials perform well at high frequencies due to their low dielectric losses and superior signal fidelity.
Thermal Management and Material Properties
In high-temperature environments, the stability of performance is crucial, and two key indicators for this are thermal conductivity and coefficient of thermal expansion. Thermal conductivity signifies a material’s ability to efficiently dissipate heat, while aligning the thermal expansion coefficients of both the substrate and components is essential to mitigate thermal stress and maintain overall performance stability.
Signal Integrity and Material Properties
In high-speed communications and data transmission, maintaining signal integrity is critical. Materials with low dielectric constant and low dissipation factor help reduce signal distortion and propagation delay, ensuring that the signal remains stable during transmission.
By trading off material properties for different performance aspects, packaging substrate manufacturers can achieve superior performance and reliability in a variety of applications. This comprehensive material selection strategy is not only related to product performance, but also has a profound impact on the stability and sustainability of the entire electronic system.
Manufacturing process and materials of packaging substrate
In the production of packaging substrates, the synergy between material selection and manufacturing processes is integral and profoundly influences performance outcomes. Here, we delve into a detailed examination of how manufacturing processes intricately interact with materials to shape the performance and reliability of packaging substrates.
The manufacturing of packaging substrates is an intricate and exacting process, where each step holds a direct or indirect impact on material performance. The initial lamination process, for instance, directly influences the substrate’s multi-layer structure. Different lamination methods yield notable variations in circuit performance, heat dissipation capabilities, and overall size. Through judicious stacking design, it becomes possible to achieve higher performance density and enhance heat dissipation effectively.
Secondly, copper foil bonding is another critical process step. Different bonding methods, such as dry film bonding and wet film bonding, have a direct impact on the thermal conductivity and mechanical strength of the substrate. This further emphasizes how process choices can shape the physical properties of materials in practical applications.
The synergy of material selection and manufacturing processes is key to ensuring superior packaging substrate performance. In high-density wiring technology, by selecting substrate materials with excellent electrical properties, combined with advanced processes, smaller package sizes and higher signal integrity can be achieved.
Thermal management is another challenge in package substrate design, and different thermal designs and material selections can have a significant impact on temperature control. By synergizing excellent materials and innovative heat dissipation design, stable operation in high-performance applications can be achieved.
The manufacturing process and material selection of the packaging substrate are complementary to each other, and the best performance can be achieved by closely combining the two. When facing the challenges of the ever-evolving electronics industry, engineers need to pursue collaborative innovation in the selection of materials and processes to ensure that packaging substrates maximize performance and reliability in different application scenarios. This close synergy not only promotes the continuous advancement of packaging technology, but also provides a solid foundation for the development of the electronic field.
Strategies for Material Selection of Package Substrates
In the design of packaging substrates, material selection is one of the key decisions that directly affects performance, cost and manufacturing feasibility. Here are some strategic considerations to help engineers make an informed choice among the many options.
Performance orientation: When selecting packaging substrate materials, we must first clarify the performance indicators required for the product. For example, for high-frequency applications, materials need to be selected with low loss and high signal integrity. Clarifying performance goals can help narrow down the material scope.
Environmental Compatibility: The selection of materials must carefully account for the specific environmental conditions in which the product will be deployed. In instances of extreme temperatures or high humidity, it is imperative to opt for materials that exhibit resilience to elevated temperatures and moisture. This consideration ensures the stability of product operation across diverse working conditions.
Manufacturability: A thorough understanding of the manufacturing challenges and costs associated with various materials is essential to guarantee that the chosen materials align with production requirements. Strategic considerations for manufacturability can significantly enhance production efficiency and contribute to an overall reduction in costs.
Supply chain stability: Choose materials whose supply chains are relatively stable to reduce the risk of material shortages and delivery delays. Build strong relationships with suppliers to ensure you have access to the materials you need.
How to balance performance needs, cost and manufacturing feasibility
Performance and cost balance: For some high-performance materials, the cost may be higher. When weighing performance and cost, the best balance needs to be found to meet product needs while remaining economically viable.
Use of customized materials: For specific application scenarios, customized materials can be considered. This better meets performance needs and, although the cost may be higher, can provide significant advantages in key areas.
Life cycle cost considerations: When selecting materials, consider their entire life cycle costs, including the procurement, production, use and disposal stages. This allows for a more complete assessment of the economics of material selection.
Through the above strategic considerations, engineers can make more informed choices about packaging substrate materials to ensure that the product achieves the best balance of performance, cost and manufacturing feasibility. This strategic material selection is a key component in advancing the electronics industry, laying a solid foundation for future innovation and sustainable practices.
Future trends in packaging substrates
The continuous development of packaging substrate materials is an important driving force for innovation in the electronics industry. Looking to the future, we can foresee a series of compelling trends that will shape a new face of packaging substrates and bring greater performance and sustainability to electronic devices.
The future evolution of packaging substrate materials will mainly focus on the following aspects:
The Emergence of Advanced Materials: As technology continues its relentless progression, there is anticipation for the emergence of new materials that are not only lighter and stronger but also more conductive. This evolution is poised to broaden the spectrum of options available for packaging substrates.
Integration of High-Performance Thermally Conductive Materials: With the ever-increasing power density of electronic devices, thermal conductivity challenges have gained prominence. Future packaging substrates are likely to incorporate high-performance thermally conductive materials to more effectively manage heat, ensuring device stability and reliability.
Rise in Popularity of Flexible Substrates: The surge in wearable technology and flexible electronics is steering the packaging substrate landscape towards flexibility. Flexible substrates are expected to be a prominent developmental focus, facilitating more adaptable designs and broader applications for electronic devices.
Environmental Focus in the Packaging Substrate Industry’s Future: In the coming years, the packaging substrate industry is anticipated to intensify its focus on sustainability and environmental protection practices, evidenced by the following trends:
Emphasis on Recycling: Confronting the mounting issue of electronic waste, future packaging substrates are poised to incorporate more recyclable materials, aiming to minimize the environmental impact.
Enhanced Energy Efficiency: Future packaging substrate designs will prioritize energy efficiency, employing materials and manufacturing processes with lower energy consumption. This approach aims to reduce the carbon footprint both during production and use, aligning with broader sustainability goals.
Green manufacturing processes: Manufacturers will promote greener production processes, reduce the emission of hazardous waste, and use clean energy to achieve green production of packaging substrates.
Generally speaking, future packaging substrates will move towards higher performance, more flexible design, and more environmental protection, providing a solid foundation for the sustainable development of the electronics industry. These trends will drive innovation to not only meet growing performance demands, but also help build a more sustainable electronics industry ecosystem.