Professional Packaging Substrate Firm, the Substrates were made with Mitsubishi materials. ABF materials, Rogers materials, and we also can use other series materials.
Packaging substrate, as an advanced electronic packaging substrate that is crucial in modern electronic design and manufacturing, its unique design and structure plays an irreplaceable key role in the practical application of electronic components.
First, packaging substrates are unique in that they combine rigid and flexible materials. The advantage of this structure is that it can simultaneously meet the support and connection needs of electronic components. The rigid part can provide strong mechanical support and stability, while the flexible part gives the circuit greater flexibility, allowing the packaging substrate to adapt to various complex design requirements.
In electronic design, packaging substrates play the role of a bridge connecting and supporting electronic components. Its design not only considers the physical connections between components, but also focuses on how to most elegantly arrange circuits within limited space. This design concept makes the packaging substrate an ideal choice for realizing highly integrated, miniaturized, and lightweight advanced electronic products.
In contemporary electronics manufacturing, packaging substrates serve as a fundamental underpinning for the stability and optimal performance of electronic components. Facilitating dependable electrical connections to diverse electronic devices, their high flexibility allows circuit boards to adapt to varying shapes and spatial constraints. This adaptability is particularly critical for applications such as mobile devices, medical monitoring equipment, and military technology.
Beyond connectivity, packaging substrates play a pivotal role in enhancing the overall performance and reliability of electronic products. Their exceptional electrical performance and reliability ensure the efficient operation of electronic products across diverse environmental and application conditions. Moreover, the design of packaging substrates takes into careful consideration factors like thermal management, thereby safeguarding electronic components from the adverse effects of excessive heat during operation.
Overall, packaging substrates provide innovative solutions for electronic design and manufacturing with their unique designs and structures. In today’s ever-evolving electronic technology landscape, packaging substrates are undoubtedly a key element in driving electronic products to achieve higher levels of performance and wider applications.
What types of packaging substrates are there?
Rigid substrates are suitable for scenarios with high stability requirements, flexible substrates are more suitable for occasions that require bending and free-form design, and rigid-flexible packaging substrates provide an ideal solution for applications that meet both rigid and flexible requirements.
In modern electronic design, the diversity of packaging substrates provides room for innovation. By in-depth understanding of the characteristics and applicable fields of each type, engineers can better select and apply packaging substrates and promote the continuous development of electronic technology. Behind this variety of choices are the efforts of packaging substrate manufacturers through continuous innovation and provision of professional services, which contribute important forces to the development of the electronics industry.
What are the advantages of packaging substrates?
In the realm of modern electronic design and manufacturing, package substrates exhibit distinct advantages over traditional circuit boards, owing to their unique performance and characteristics. These advantages encompass not only remarkable flexibility but also exceptional space utilization and lightweight attributes, rendering them an ideal choice for electronic product design.
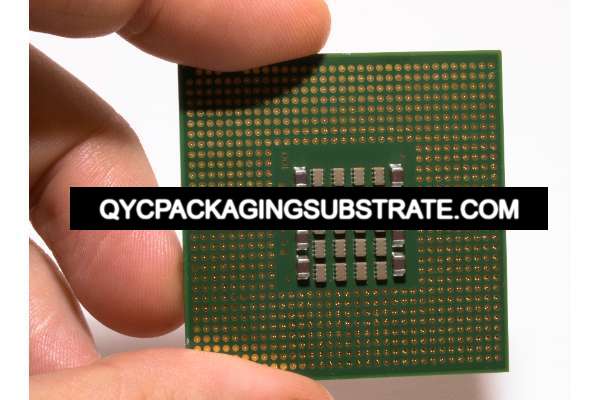
Packaging substrate manufacturer
Outstanding space utilization stands as another key advantage of packaging substrates. The substrate’s ability to flexibly adapt to the arrangement of electronic components enables designers to make more efficient use of limited space. Given the rising popularity of compact yet powerful electronic devices, packaging substrates play a crucial role in compressing product sizes by tightly integrating circuits, enabling the implementation of complex circuits within confined spaces.
The lightweight feature further distinguishes packaging substrates, aligning with the contemporary emphasis on product weight reduction in mobile devices and portable electronics. Leveraging lightweight materials and structures, packaging substrates contribute to overall product weight reduction, enhancing portability for consumers and finding applications in the aerospace sector.
Collectively, these advantages position packaging substrates as standout elements in electronic product design. Their flexibility, space utilization efficiency, and lightweight properties provide designers with expanded possibilities, fostering innovation in electronic technology. Looking ahead, with the continuous advancement of packaging substrate manufacturing technology, it is anticipated that their application across various fields will broaden, infusing new vitality into the development of electronic products.
Why choose a packaging substrate manufacturer?
In the fiercely competitive landscape of electronic design, the selection of a packaging substrate manufacturer has emerged as a critical decision, surpassing conventional circuit boards to address a spectrum of design requirements. The significance lies not only in the inherent superiority of the packaging substrate itself but also in the manufacturer’s capacity to deliver professional customization services, offering customers innovative solutions fueled by technology and experience.
The popularity of packaging substrate manufacturers is rooted in their adept understanding and capability to cater to varied design needs. In contrast to traditional circuit boards, packaging substrates offer enhanced flexibility and diversity in design. Manufacturers leverage this deep comprehension of flexibility to furnish customers with tailored, professional solutions, reflecting a keen awareness of the evolving demands in electronic design.
First, packaging substrate manufacturers usually have advanced technical equipment and highly skilled engineering teams. This allows them to utilize advanced design tools and production equipment to accurately meet customers’ stringent requirements for circuit board performance, size and shape. Whether in small mobile devices or complex communication systems, the application of this technology can provide customers with unique solutions.
Furthermore, manufacturers of packaging substrates leverage extensive years of expertise to comprehend and anticipate the diverse requirements of various application scenarios. Their wealth of experience in material selection and process optimization is dedicated to ensuring the dependability and stability of designs. This accumulated knowledge is evident not only in the technical proficiency of the manufacturer’s team but also in their collaborative efforts with customers, offering practical suggestions based on their deep understanding.
In the provision of professional customized services, packaging substrate manufacturers prioritize close cooperation with their customers. They ensure that every step involves a tightly integrated process with customers, delving into a profound understanding of their needs and product design specifications. This collaborative approach enables manufacturers to gain a nuanced understanding of their customers’ objectives, allowing them to deliver tailored solutions.
In essence, the decision to select a packaging substrate manufacturer extends beyond the excellence and flexibility of their products; it hinges on their ability to offer professional and customized services. By deeply comprehending the requirements of diverse industries, harnessing advanced technology, and drawing from rich experience, manufacturers deliver comprehensive solutions, establishing themselves as indispensable and crucial partners in the realm of electronic design.
What is the manufacturing process of packaging substrates?
In delving into the manufacturing process of packaging substrates, it becomes imperative to grasp the intricacies of this intricate and precise procedure. Manufacturers navigate a series of meticulous steps, progressing from the motherboard to the substrate, with the overarching goal of ensuring that the final product adheres to stringent standards of quality and performance excellence.
This stage is the cornerstone of the entire manufacturing process and involves circuit design, material selection, and clear definition of technical parameters. Among them, manufacturers must pay close attention to customer needs and carry out precise customization according to application scenarios and design requirements.
The manufacturer then proceeds to select the appropriate material, a crucial step in packaging substrate manufacturing. The choice of rigid and flexible materials directly affects the bendability and overall performance of the product. Good manufacturers often take full advantage of the latest materials technology to ensure their products perform well in a variety of environments.
Next comes the layer-by-layer process, where the manufacturer layers carefully selected materials according to the design requirements. This step involves highly precise process control to ensure that each layer meets specifications and is free of any defects. This is the basis of the packaging substrate and a key link to ensure the quality of the entire circuit board.
Next is the preparation of the circuit pattern. Through techniques such as chemical etching, the manufacturer will imprint the designed circuit pattern on the substrate. This step requires manufacturers to have a high level of technology and advanced equipment to ensure the clarity and accuracy of circuit graphics.
Then, blind hole drilling became an important part of the manufacturing process. Accurate drilling of blind vias is critical in multi-layer packaging substrates, providing channels for connections between the layers of the circuit board. This is also a step that requires a high degree of process control to avoid any damage or errors.
Next comes metallization, by coating the surface of the circuit board with metal, the manufacturer ensures good conductivity and connectivity. This step requires manufacturers to precisely control materials to prevent problems such as unevenness or oxidation of the metal layer.
In general, the manufacturing process of packaging substrates is a precise and complex project involving many processes and technical details. Only when the manufacturer has highly specialized process technology and comprehensive technical reserves can it ensure that the packaging substrate meets the highest standards in all aspects.
In what areas are packaging substrates widely used?
Package Substrate, as an advanced electronic packaging substrate, plays an extensive and critical role in various electronic products. Its unique design and flexibility make it possible to implement complex circuits in limited space, providing ideal solutions for smartphones, communication equipment, medical monitoring equipment and other fields.
Communication device
In modern communication equipment, such as base stations and communication terminals, packaging substrates also play a key role. These devices usually need to work in complex environments, placing high demands on the performance and reliability of circuit boards. The design of the packaging substrate not only meets the need for high flexibility, but also provides resistance to vibration and temperature changes through its rigid-flex properties. These characteristics make communication equipment more adaptable and durable.
Medical monitoring equipment
The utilization of packaging substrates is becoming more prevalent in medical monitoring equipment. In medical settings, equipment often requires the integration of diverse sensors, processors, and communication modules to facilitate real-time monitoring and data transmission for patients. The adaptable design features of packaging substrates empower engineers to implement intricate circuit structures within compact medical devices. This capability significantly contributes to the advancement of portable monitoring equipment, enabling medical staff to conveniently monitor and diagnose patients with greater ease and efficiency.
Flexible design
The flexibility of the packaging substrate plays a key role in these applications. It can adapt to various complex circuit structures to meet the high design and performance requirements of electronic products. It is precisely because of the design flexibility of packaging substrates that modern electronic products can combine powerful functions, thinness and compactness in a limited space.
In electronic products like smartphones, communication equipment, and medical monitoring devices, the extensive use of packaging substrates underscores their indispensable role in driving innovation in electronic technology. The inherent design flexibility of these substrates not only grants engineers greater creative latitude but also delivers consumers more cutting-edge, lightweight, and potent electronic products.
Where to find packaging substrate manufacturers?
Securing a dependable packaging substrate manufacturer is a crucial aspect of achieving success in electronic product design and manufacturing. In the fiercely competitive contemporary market, the selection of an experienced and reputable manufacturer stands as a pivotal step in guaranteeing the quality and performance of the final product. Exploring various avenues to identify a packaging substrate manufacturer is essential, accompanied by a thorough consideration of key factors when making the supplier selection.
Online supplier
In the era of the Internet, a convenient method for locating packaging substrate manufacturers is by utilizing online suppliers. Search engines enable users to discover the websites of numerous professional manufacturers, offering insights into their product range, manufacturing capabilities, service offerings, and other pertinent details. Online platforms frequently feature customer reviews and feedback, providing valuable input for making an initial assessment of a manufacturer’s credibility and business standing.
Professional exhibition
Participating in professional electronics shows and exhibitions proves to be a highly effective means of engaging directly with prospective packaging substrate manufacturers. These events serve as global gatherings for electronics manufacturers and suppliers, offering companies a valuable platform to delve into the latest industry trends, technological advancements, and potential partnerships. Engaging in on-site discussions allows for a more thorough comprehension of a manufacturer’s strengths and professional capabilities, providing a firsthand insight into their expertise.
Industry connections
Another effective method to identify packaging substrate manufacturers is through networking within the industry. Actively engage with electronics manufacturing industry organizations, forums, and social media platforms to gather information and establish professional relationships. By participating in discussions and communicating with peers, you can garner valuable recommendations and insights from other companies, facilitating a more informed selection of a suitable packaging substrate manufacturer.
The importance of experienced and reputable manufacturers
Strategically selecting an experienced and reputable packaging substrate manufacturer holds paramount importance. Such manufacturers typically leverage advanced production technology and state-of-the-art equipment to ensure the quality and stability of their products. Their extensive experience positions them well to comprehend customer needs, enabling them to offer professional technical support and effective solutions.
Moreover, reputable manufacturers often enjoy positive industry standing, boasting higher customer satisfaction with their products and services. Opting for such a manufacturer enables companies to mitigate cooperation risks, ensuring a seamless production process and ultimately enhancing the competitiveness of their products.
Through a comprehensive consideration of these criteria and factors, companies can gain a nuanced understanding of the strengths and characteristics of packaging substrate manufacturers. This informed approach facilitates the establishment of long-term, stable partnerships with the most suitable manufacturers. In the fiercely competitive electronics market, prudent choices not only enhance product quality but also confer a substantial competitive advantage to enterprises.
What is the quotation from the packaging substrate manufacturer?
When selecting a packaging substrate manufacturer, a thorough understanding of the quoting mechanism is a critical step in ensuring final product quality and cost-effectiveness. The custom quote provided by the manufacturer directly affects the feasibility of the design and the overall production cost, so understanding this process is critical to the success of the project.
What is necessary to understand a quote?
In the process of choosing a packaging substrate manufacturer, a crucial step is comprehending the quotation. This not only aids the client in gauging the economic viability of the project but also furnishes the design team with essential insights to ensure the project stays within the allocated budget. Understanding the quote is integral to making informed decisions during the design and production phases.
How to adapt to design requirements?
Quotations provided by manufacturers should be able to accommodate specific design requirements. This may involve the selection of different materials, hierarchies, and the need for special technologies and manufacturing processes. The accuracy of the quotation is directly related to the implementation of the design plan and cost control.
Custom quotes from manufacturers
Consider design requirements: Manufacturers often ask customers to provide detailed design requirements, including board dimensions, hierarchy, material requirements, etc. This helps tailor quotes to ensure they match the actual needs of the design.
Consider Material Cost: Material cost is an important component of the quote. Manufacturers consider the type of substrate used, thickness, layering, etc. to calculate the material cost of the final product. Transparency in this area helps customers understand the key components of product costs.
Impact of production process: The quotation also needs to consider the production process, including metallization, etching technology, blind hole drilling, etc. Different production processes have different impacts on costs, so these factors are also taken into consideration when customizing quotations.
Batch size and lead time: Manufacturers often also consider production batch size and lead time factors. Larger production volumes may receive some discounts, while urgent delivery times may result in additional charges. These factors will all affect the final customized quote.
When selecting a packaging substrate manufacturer, fully understanding the quoting mechanism is a critical step in ensuring project success. By providing design requirements in detail, taking into account the impact of material costs and production processes, manufacturers are able to provide customized quotes that meet customer needs.
Frequently Asked Questions (FAQs)
What are the advantages of installing substrates over traditional circuit boards?
Package substrates have significant advantages over traditional circuit boards. Its high degree of flexibility and excellent space utilization make it ideal in modern electronic designs. In addition, the packaging substrate’s lightweight nature and superior electrical performance and reliability make it excellent in a variety of applications.
What are the key factors in selecting a packaging substrate manufacturer?
Key factors in selecting a packaging substrate manufacturer include its level of experience, technical capabilities, quality of customization services, and reputation. The manufacturer should have extensive experience in understanding and meeting the unique design needs of its customers, and its reputation should be solid.
What are the common design considerations for packaging substrates?
In the design of packaging substrates, careful attention must be given to factors such as the bending radius of flexible sections, the configuration of rigid-to-flexible transition zones, and the methodology employed for interlayer connections. A well-executed design is essential to mitigate stress concentration and prevent mechanical damage to the circuit board during usage.
What are the environmental considerations for packaging substrates?
During the manufacturing process, manufacturers should prioritize the selection of eco-friendly materials and adopt sustainable processes. Opting for recyclable materials and embracing green manufacturing practices is essential to minimize the environmental footprint and contribute to a more sustainable production approach.
What is the future development direction of packaging substrates?
Looking ahead, packaging substrates are anticipated to find broader applications in emerging fields like artificial intelligence and the Internet of Things. The continuous optimization of their performance and increased cost competitiveness is expected to elevate electronic product design and manufacturing to new heights.
By addressing these commonly asked questions, our aim is to provide readers with a comprehensive insight into the role of packaging substrate manufacturers and their significance in electronic design. This knowledge empowers readers to make informed decisions when choosing manufacturers and designing products, fostering a deeper understanding of this crucial aspect of electronic technology.