Rigid-flex BGA substrate Manufacture. the Rigid-flex BGA substrate will be made with Flex base materials and hard boards base materials. you can use the High speed materials or other types materials. Features: Ultra-small gap.
Rigid-Flex BGA Substrates, translated as rigid-flexible BGA substrate in Chinese, is an innovative PCB engineering solution that combines the advantages of rigid and flexible substrates to meet the design needs of complex electronic devices. In traditional PCB design, rigid substrates are often used to support and connect electronic components, while flexible connectors are used to connect different parts, such as a screen or keyboard. However, as electronic devices continue to evolve and innovate, the demand for more flexible and lightweight designs continues to increase, which requires a solution that can provide flexibility and reliability in space-constrained situations.
Rigid-Flex BGA Substrates Rigid-Flex BGA Substrates combine rigid and flexible substrate layers to create a unique structure that combines the mechanical stability of a rigid substrate with the bendability of a flex connector. This structure allows electronic equipment to achieve a more compact design while maintaining a high degree of reliability and durability.
The design process for Rigid-Flex BGA Substrates involves the selection of rigid and flexible materials, as well as precision processes such as laminate stacking and circuit patterning. Through careful design and manufacturing, this rigid-flexible BGA substrate can adapt to a variety of environments and application requirements, including aerospace, medical devices, automotive electronics, and more.
Overall, Rigid-Flex BGA Substrates represent an important advancement in PCB engineering, providing greater flexibility and reliability in the design and manufacturing of electronic devices.
What types of Rigid-Flex BGA Substrates are available?
Rigid-Flex BGA Substrates (rigid-flex BGA substrate), as an innovative PCB engineering solution, provide a variety of types to meet different design needs. In practice, single-sided, double-sided and multi-layer Rigid-Flex BGA Substrates are the three most common types. Below we describe them in detail and explore their unique features in terms of flexibility, density and cost-effectiveness.
Single-sided Rigid-Flex BGA Substrates consist of a rigid layer and a flexible layer, where circuitry and components on the rigid layer are connected to circuitry on the flexible layer via flex connectors. This structure provides a degree of flexibility suitable for applications requiring simple curved shapes or slight bends. Single-sided Rigid-Flex BGA Substrates typically have lower manufacturing costs due to fewer layers, making them suitable for cost-sensitive projects.
Double-sided Rigid-Flex BGA Substrates include two rigid layers and a flex layer, where circuitry can be laid out between the two rigid layers and on the flex layer. This structure provides greater design freedom and flexibility for applications requiring more complex shapes or severe bends. Double-sided Rigid-Flex BGA Substrates have higher density and can accommodate more circuits and components, making them suitable for projects that require high performance and high-density integration.
Multilayer Rigid-Flex BGA Substrates consist of multiple rigid and flexible layers connected together by interlayer connectors. This structure provides maximum design flexibility and integration, and can accommodate more complex circuit layouts and more functional modules. Multilayer Rigid-Flex BGA Substrates offer the highest density and flexibility for projects where performance, reliability and space efficiency are critical, such as aerospace and medical devices.
In general, single-sided, double-sided and multi-layer Rigid-Flex BGA Substrates each have their own unique features and advantages, providing design engineers with a broad choice while meeting different application needs.
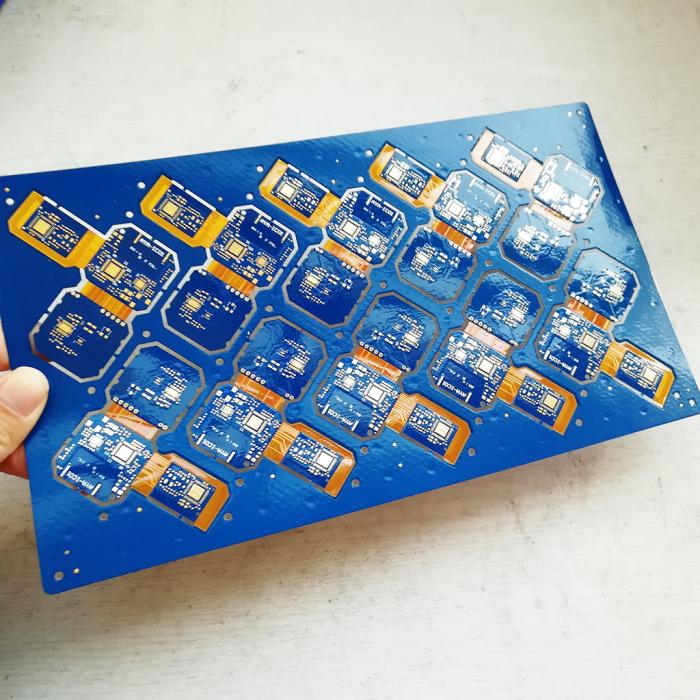
Rigid-flex BGA substrate
What are the advantages of Rigid-Flex BGA Substrates?
Rigid-Flex BGA Substrates are a solution that offers significant advantages in electronic packaging. They combine the advantages of rigid and flexible substrates, providing designers with unique opportunities to implement complex electronic assemblies. Here are a few key benefits of Rigid-Flex BGA Substrates:
First, Rigid-Flex BGA Substrates improve mechanical reliability. Because they reduce the number of connectors and solder points, they reduce the risk of mechanical failure. Compared to traditional rigid PCBs, the flexible portion of Rigid-Flex BGA Substrates can reduce mechanical stress between components, thereby improving overall reliability and longevity.
Second, Rigid-Flex BGA Substrates bring increased design flexibility. Designers can place electronic components more freely, resulting in more compact and lightweight designs. This flexibility makes Rigid-Flex BGA Substrates particularly suitable for applications where space is limited or a high level of integration is required, such as portable devices or medical devices.
In addition, Rigid-Flex BGA Substrates help improve signal integrity. With fewer connectors and jumpers, the signal transmission path is shorter and more stable, reducing the risk of signal attenuation and crosstalk. This is crucial for high-frequency or high-speed data transmission applications to ensure system stability and reliability.
In summary, Rigid-Flex BGA Substrates have significant advantages in electronic packaging. Not only do they increase mechanical reliability, they also increase design flexibility and improve signal integrity. This makes them the solution of choice in many industries, driving the development and innovation of electronic assembly technology.
Why choose Rigid-Flex BGA Substrates?
Rigid-Flex BGA Substrates are an innovative technology in today’s electronic packaging world, and they demonstrate many significant advantages over traditional PCBs and rigid-flex solutions. Rigid-Flex BGA Substrates stands out as the solution of choice in several key areas.
The design flexibility of Rigid-Flex BGA Substrates provides room for innovation in electronic products. They allow combining rigid and flexible structures in a single component, allowing for more complex and compact circuit layouts. This flexibility is especially useful in applications with limited space, such as portable devices and medical devices.
Rigid-Flex BGA Substrates reduce the number of connection points and solder points compared to traditional PCBs, thereby increasing overall mechanical reliability. This structural design reduces the risk of fatigue and breakage, making electronic products more stable and reliable in long-term use.
While the initial investment may be slightly higher than traditional solutions, Rigid-Flex BGA Substrates are often more cost-effective given their design advantages and reliability. Savings from reduced component count, simplified assembly processes, and increased product life cycles ultimately make overall costs more controllable.
Because Rigid-Flex BGA Substrates are designed to reduce trace lengths and connections, signal transmission distortion and interference are reduced. This optimization helps improve signal integrity and ensures high performance and stability of electronic products, especially in high-frequency applications.
The advantages of Rigid-Flex BGA Substrates are not only reflected in specific industries, but also applicable to a variety of applications. Whether it is aerospace, medical equipment or automotive electronics, this solution has demonstrated excellent adaptability and performance, meeting the high requirements for electronic packaging in different industries.
Overall, the reason for choosing Rigid-Flex BGA Substrates is not only their superior design flexibility and mechanical reliability, but also their superior performance in various key areas. This innovative electronic packaging technology brings new possibilities to the design and manufacturing of electronic products, providing engineers with more choices and opportunities.
What is the manufacturing process for Rigid-Flex BGA Substrates?
The manufacturing process of Rigid-Flex BGA Substrates is a precise and complex project that includes multiple critical steps, from substrate preparation to laminate stacking to circuit patterning, each step is critical.
First, the process of manufacturing Rigid-Flex BGA Substrates begins with the substrate preparation stage. At this stage, manufacturers select high-quality rigid and flexible substrate materials. The selection of these materials is critical as they will directly impact the performance and reliability of the final product. Typically, rigid materials such as FR-4 fiberglass composites, while flexible materials may include Mylar or polyimide (PI).
Next comes the lamination stacking stage. At this stage, manufacturers laminate rigid and flexible substrates according to design requirements. This process requires highly precise control to ensure accurate alignment and precise stacking of the layers. Through a heat pressing and chemical curing process, the layers of different materials are firmly bonded together to form an integrated substrate structure.
This is followed by the circuit pattern making stage. At this stage, manufacturers use advanced photolithography techniques to transfer circuit patterns to the substrate surface. This involves applying photoresist to the surface of a substrate and then forming the desired circuit pattern on the substrate through steps such as exposure, development and etching. This process requires high-precision equipment and process control to ensure the accuracy and quality of circuit patterns.
Finally, after the circuit pattern is completed, surface treatment is required. This includes applying protective coatings to protect circuit patterns from environmental factors and mechanical damage. In addition, surface preparation also includes the application of solder paste in order to solder electronic components to the substrate.
Overall, manufacturing Rigid-Flex BGA Substrates is a highly complex and precise process that requires a combination of materials science, process engineering and manufacturing technology. Each step must be precisely controlled to ensure the quality and performance of the final product meet design requirements.
What are the application areas of Rigid-Flex BGA Substrates?
Rigid-Flex BGA Substrates are a versatile PCB engineering solution whose design flexibility and reliability make it widely used in multiple industries. The following are its specific applications in aerospace, medical equipment and automotive electronics:
In the aerospace industry, Rigid-Flex BGA Substrates are widely used in various aerospace equipment and aerospace devices. Because aerospace equipment often operates in extreme environments, such as high temperatures, low temperatures, and high vibration environments, electronic packaging solutions with high reliability and durability are required. Rigid-Flex BGA Substrates play an important role in aerospace equipment by meeting these requirements while allowing designers to implement complex circuit layouts within limited space.
In the field of medical devices, Rigid-Flex BGA Substrates provide an ideal electronic packaging solution for a variety of medical devices and medical sensors. Medical devices often require electronic components with high flexibility, biocompatibility, and stability to meet the special requirements of the medical environment. Rigid-Flex BGA Substrates can provide flexible connections and reliable signal transmission while maintaining good mechanical strength and durability, so they are widely used in applications such as pacemakers, in vitro diagnostic equipment and medical monitoring devices.
In the field of automotive electronics, Rigid-Flex BGA Substrates are widely used in key components such as automotive control units, sensors, infotainment systems and in-vehicle communication equipment. Automotive electronics require high stability, resistance to vibration and temperature changes, and compact package designs to adapt to the challenges in the automotive environment. Rigid-Flex BGA Substrates can meet these requirements while providing flexible design options to make automotive electronic systems more reliable and efficient.
Overall, the wide range of applications of Rigid-Flex BGA Substrates in aerospace, medical devices and automotive electronics demonstrate their importance and value in solving complex electronic packaging problems. As technology continues to evolve and innovate, Rigid-Flex BGA Substrates will continue to play a key role in various industries and drive the performance and functionality of electronic devices.
How do I obtain Rigid-Flex BGA Substrates?
When looking for a reliable Rigid-Flex BGA Substrates manufacturer, there are several key factors to consider. First, you need to make sure that the manufacturer you select has the experience and expertise to meet your specific needs. At the same time, you may want to choose a manufacturer that can provide customized solutions that can be adjusted and optimized to your design requirements.
Choosing an experienced manufacturer is crucial. They should have expertise in Rigid-Flex BGA Substrates manufacturing and be able to provide you with the best solution. By looking at a manufacturer’s history, customer reviews, and their production capabilities and technical equipment, you can evaluate their reliability and capabilities.
As technology develops and application requirements change, customized solutions become increasingly important. Therefore, it is critical to choose a manufacturer that can provide customized Rigid-Flex BGA Substrates. They should be able to flexibly adjust to your design requirements and provide professional advice and technical support to ensure the final product meets your expectations.
If you need to produce Rigid-Flex BGA Substrates in large quantities, it is especially important to choose a manufacturer with mass production capabilities. You should ask the manufacturer about production capabilities, lead times, and supply chain management to ensure they can meet your production needs and maintain consistent product quality.
In terms of supplier selection, our company provides you with a full range of solutions. With many years of Rigid-Flex BGA Substrates manufacturing experience, we are committed to providing customers with high-quality, customized products with flexible production capabilities to meet your needs and ensure timely delivery. Whether you need a customized solution or mass production options, we can provide you with satisfactory service and support.
How much does Rigid-Flex BGA Substrates cost?
Obtaining a quote for Rigid-Flex BGA Substrates is a critical task as it directly affects the cost and feasibility of the project. It’s crucial to understand how to get an accurate quote and what factors influence it.
First, getting a quote for Rigid-Flex BGA Substrates usually requires contacting the manufacturer or supplier. This can be done via the online inquiry form, email or phone. Before providing a quote, manufacturers often require you to provide detailed information about the project, including design specifications, quantities required, delivery time, etc.
There are many factors that influence the price quoted for Rigid-Flex BGA Substrates. These include but are not limited to the following:
Project Complexity: The design complexity of Rigid-Flex BGA Substrates is an important factor in determining the quote. More complex designs may require more layers, higher manufacturing precision, and longer production times, so costs will increase accordingly.
Materials required: Different substrate materials and coating options affect cost. High-performance materials and finishes often increase cost, but may also provide better performance and reliability.
Production scale: The quantity of the order and the production batch size will also affect the quotation. Typically, mass production will bring more cost advantages, while small-scale production may result in an increase in unit price.
Delivery Time: If the item has strict delivery time requirements, the manufacturer may charge additional fees for rush orders. Therefore, flexible delivery schedules may impact quotes.
After providing project details to the manufacturer, they will typically provide a competitive quote based on the above factors. This process can take some time as the manufacturer needs to assess the complexity and needs of the project before they can provide an accurate quote.
In summary, obtaining an accurate quote for Rigid-Flex BGA Substrates requires working closely with the manufacturer and fully considering factors such as project complexity, material requirements, production scale, and delivery time. By clearly communicating your project needs, you can ensure you get the best solution that meets your budget and time requirements.
Frequently Asked Questions (FAQs)
Can Rigid-Flex BGA Substrates be repaired or modified?
Rigid-Flex BGA Substrates can indeed undergo repair or modification, but the feasibility largely depends on the extent and nature of the damage or required modification. Simple repairs like rework of solder joints or trace repair can often be performed, but extensive modifications may necessitate redesign and remanufacture of the substrate.
What are the environmental considerations associated with Rigid-Flex BGA Substrate manufacturing?
Environmental considerations in Rigid-Flex BGA Substrate manufacturing primarily revolve around the choice and disposal of materials. Selecting environmentally friendly materials and adopting eco-friendly manufacturing processes help minimize the carbon footprint. Additionally, proper disposal or recycling of waste materials ensures compliance with environmental regulations.
How does thermal management affect the performance of Rigid-Flex BGA Substrates?
Thermal management plays a critical role in ensuring the performance and reliability of Rigid-Flex BGA Substrates, particularly in applications with high power dissipation. Effective thermal management techniques such as thermal vias, heatsinks, and thermal interface materials help dissipate heat and maintain optimal operating temperatures, thereby preventing thermal-induced failures and ensuring long-term reliability of the substrate.
What is the typical lead time for procuring Rigid-Flex BGA Substrates?
The lead time for procuring Rigid-Flex BGA Substrates varies depending on factors such as substrate complexity, quantity, and supplier capacity. Generally, lead times range from a few weeks for prototype quantities to several weeks or months for larger production volumes. It’s advisable to consult with the manufacturer early in the design phase to plan for lead time requirements effectively.