Rigid-flex BGA substrate Supplier. the Package Substrate will be made with PI(Flex base materials) and BT, Rogers or Showa Denko and Ajinomoto High speed materials.
The ingenious combination of these elements allows the substrate to flex within defined spatial constraints, significantly enhancing the adaptability of electronic product design.
Conventional rigid circuit boards often face limitations in accommodating numerous connections within confined spaces. Rigid-Flex BGA Substrate ingeniously overcomes this challenge by integrating flexible segments with rigid ones. The flexible component enables the substrate to bend, while the rigid portion provides essential support, enabling the realization of highly intricate circuit connections in compact devices.
Central to the functionality of Rigid-Flex BGA Substrate is BGA technology (Ball Grid Array). Departing from traditional soldering methods, BGA technology orchestrates the formation of a ball array through minute spherical connection points, eliminating fixed pins on the surface. This innovative design not only significantly enhances connection density but also reduces the size of connection points, enabling a greater number of connections within confined spaces.
The constraint of limited space is a recurring challenge in electronic product design. Rigid-Flex BGA Substrate, with its distinctive design, excels in achieving higher-density connections within confined spaces, opening up possibilities for miniaturization and lightweighting of electronic products. The adoption of BGA technology further fortifies connections, a critical aspect for contemporary high-performance equipment.
The widespread adoption of Rigid-Flex BGA Substrate across diverse applications, including mobile devices and medical instruments, attests to its status as the pinnacle choice in electronic packaging technology. Its flexibility, efficient space utilization, and high-density connections showcase not only technological innovation but also its instrumental role in propelling the electronics industry to new heights.
What is the manufacturing process of Rigid-Flex BGA Substrate?
The manufacturing process of Rigid-Flex BGA Substrate is a precise and complex project involving multiple key steps, from multi-layer stack design to final performance and reliability verification, each step is critical.
Multi-layer stack design
The first step in manufacturing Rigid-Flex BGA Substrate is a complex multi-layer stack design. This involves achieving a balance between rigid and flexible layers and ensuring each layer connects correctly. Design engineers must consider the application of BGA technology to achieve high-density connection layout.
Circuit diagram preparation
Following the circuit diagram preparation, chemical etching becomes a vital process in the manufacturing of circuits. Chemical etching is employed to eliminate unwanted metal layers, sculpting the desired circuit pattern. Specialized chemical solutions are used in this step to precisely control the etching process, ensuring that metal is removed only to the depth specified by the design. This meticulous control is crucial for achieving the intended circuit layout and functionality in the final product.
Metallization
Metallization is another critical process step by applying a metal layer to the circuit pattern to achieve the required electrical conductivity. This layer of metal is responsible for connecting different components to form a circuit. Manufacturers must precisely control metallization uniformity and adhesion to ensure circuit board reliability.
Control the importance of every step
Vigilant monitoring and adjustment of critical parameters using advanced technology and equipment are essential to guarantee the product meets elevated standards. The intricacies of the manufacturing process require meticulous attention, and only through careful oversight and adjustment of each step can manufacturers ensure the final Rigid-Flex BGA Substrate attains the desired level of excellence in performance and reliability. This meticulous process control is pivotal to the product’s ability to excel across diverse applications.
What are the advantages of Rigid-Flex BGA Substrate?
Rigid-Flex BGA Substrate presents notable advantages over conventional circuit boards, particularly in optimizing space utilization, enhancing vibration and shock resistance, making it an ideal solution for demanding environments, particularly in aerospace and medical equipment applications.
The flexibility afforded by this substrate opens up possibilities for the miniaturization and lightweighting of electronic products, addressing the growing demand for compact designs in contemporary electronic devices.
In industries like aerospace and medical equipment, where stringent size and weight constraints present significant challenges in product design, the spatial advantage provided by Rigid-Flex BGA Substrate proves to be an invaluable asset. As electronic devices in these fields require compact yet robust solutions, the substrate’s ability to facilitate flexible designs within limited spaces becomes a crucial tool in overcoming these challenges. This makes Rigid-Flex BGA Substrate a compelling choice for applications where both space efficiency and performance are paramount.
Secondly, Rigid-Flex BGA Substrate performs well in vibration and shock environments. Due to the presence of the flexible part, Rigid-Flex BGA Substrate is able to better absorb and disperse the energy of vibration and impact, reducing the impact on circuits and connection points. In aerospace applications, aircraft are often subject to complex vibrations and shocks, and Rigid-Flex BGA Substrate can effectively protect internal circuits from interference from these external environments. Likewise, in medical equipment, especially mobile or portable equipment, the vibration resistance of Rigid-Flex BGA Substrate provides a solid foundation for the reliability and stability of the equipment.
In the aerospace and medical device fields, where precision and dependability are paramount, the Rigid-Flex BGA Substrate’s distinctive features shine. Its flexibility allows it to address space constraints, while its rigid components ensure structural integrity. This combination caters to the industry’s need for compact and reliable electronic solutions.
Rigid-Flex BGA Substrate stands out as a crucial component in high-stakes sectors where uncompromised performance is imperative. Its distinctive features make it a driving force in the ever-evolving electronics industry, ensuring its continued and widespread utilization across diverse fields. The substrate’s adaptability and reliability make it an appealing choice not only for existing aerospace and medical device applications but also for addressing emerging challenges in the dynamic landscape of electronic technology. As technology progresses, the advantages of Rigid-Flex BGA Substrate become increasingly noteworthy, solidifying its position as a key player in critical industries.
Why choose Rigid-Flex BGA Substrate?
Rigid-Flex BGA Substrate emerges as a standout choice among diverse circuit board options, owing to its distinctive advantages, making it an optimal solution for high-density packaging in electronic design.
Primarily, the exceptional flexibility of Rigid-Flex BGA Substrate distinguishes it from traditional circuit boards confined by spatial limitations. This innovative technology allows for the integration of both rigid and flexible materials, enabling more intricate layouts within constrained spaces. This flexibility empowers designers with increased creative freedom, addressing the persistent need for miniaturization and lightweight features in contemporary electronic products.
Additionally, the incorporation of BGA (Ball Grid Array) technology plays a pivotal role in the selection of Rigid-Flex BGA Substrate. BGA technology utilizes ball-shaped solder joints to establish connections between the chip and the substrate, replacing conventional pin connections. This design not only reduces the overall device size but also enhances density and connectivity. The spherical arrangement of BGA facilitates more compact connections between devices, resulting in an overall improvement in performance.
In summary, Rigid-Flex BGA Substrate stands out for its flexibility in design and the application of BGA technology, making it a preferred choice for electronic designs requiring high-density packaging and intricate layouts in constrained spaces.
In terms of high-density packaging, Rigid-Flex BGA Substrate achieves superior performance advantages through its BGA technology. Because the solder ball layout is more compact, the signal transmission path is shorter, thereby reducing the signal transmission delay. This is critical in areas with extremely high performance requirements, such as communications and computer systems. In addition, due to the higher welding quality and stronger reliability of BGA, the probability of circuit board failure in extreme environments is reduced.
In summary, choosing Rigid-Flex BGA Substrate is to take full advantage of its unique flexibility and BGA technology. More than just a medium for connecting electronic components, this circuit board is ideal for achieving innovation, performance and reliability in modern electronic designs. In increasingly complex electronic products, Rigid-Flex BGA Substrate is continuing to demonstrate its huge potential in promoting technological advancement.
What are the application areas of Rigid-Flex BGA Substrate?
The Rigid-Flex BGA Substrate, recognized for its exceptional design flexibility and versatility, has found extensive applications across diverse domains. This discussion will explore its specific uses in smartphones, medical monitoring equipment, and military aviation systems, highlighting its pivotal role in enhancing design flexibility.
Smartphone field
In smartphone manufacturing, extreme space constraints require electronic components to be highly integrated and compactly laid out in a limited space. Through its flexible and bendable design, Rigid-Flex BGA Substrate can perfectly adapt to the three-dimensional structure of mobile phones and achieve flexible layout of circuit boards. This feature enables tighter connections between components inside the phone, improving overall performance and giving phone designers greater creative freedom.
Medical monitoring equipment field
Rigid-Flex BGA Substrate is integral in the medical industry, particularly in the production of medical monitoring equipment. Due to the intricate circuit configurations needed to accommodate diverse sensors and communication modules, medical devices rely on this specialized substrate. Its unique combination of flexible and rigid components enables the circuit board to conform to the device’s shape, minimizing space requirements and enhancing patient comfort. This flexible design not only contributes to the equipment’s reliability and stability but also ensures precise transmission of medical data.
Military aviation systems field
In the realm of military and aviation systems, stringent requirements for electronic equipment necessitate specialized solutions. The Rigid-Flex BGA Substrate emerges as a robust choice, providing robust circuit support for military aviation systems with its notable anti-vibration and anti-shock properties. Its inherent design flexibility facilitates the seamless integration of diverse sensors, communication equipment, and control units into intricate aircraft structures. Moreover, this flexibility not only contributes to a reduction in overall weight but also enhances system performance and reliability.
The versatility of the Rigid-Flex BGA Substrate is a pivotal aspect driving its widespread application across various electronic products. Diverging from conventional rigid or flexible boards, this substrate can be bent freely, adapting to irregular shapes and catering to the diverse design requirements of complex products. This unique flexibility affords product designers increased freedom to effectively balance considerations such as performance, space utilization, and manufacturing costs.
Overall, Rigid-Flex BGA Substrate has successfully penetrated into many fields such as smartphones, medical monitoring equipment, and military aviation systems with its unique design and superior performance. Its flexibility and reliability provide ideal solutions for a variety of complex electronic products, promoting technological progress and innovation in these industries.
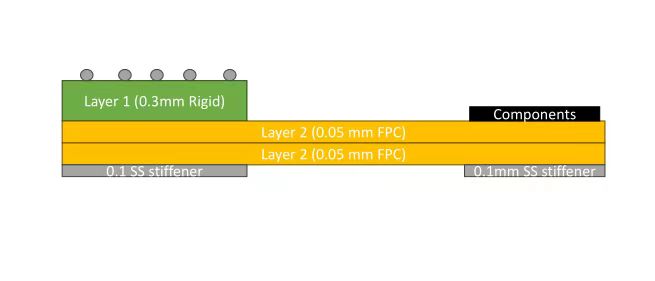
Flex-Rigid BGA Substrate
How to obtain Rigid-Flex BGA Substrate?
The significance of opting for a reputable manufacturer cannot be overstated. Dependable manufacturers leverage extensive experience and cutting-edge technology, effectively addressing the requirements of intricate circuit board designs. Partnering with a seasoned manufacturer not only ensures exceptional products but also grants access to expert technical support and exceptional customer service.
Engaging with a seasoned Rigid-Flex BGA Substrate manufacturer offers a multitude of benefits:
Technical Expertise:Professional manufacturers boast profound technical proficiency, comprehending and meeting customer-specific design requirements. Whether dealing with intricate stack-up designs or high-density BGA layouts, they offer innovative solutions.
Quality Control: Rigorous quality control processes are integral throughout the manufacturing of Rigid-Flex BGA Substrate. Professional manufacturers implement strict measures to ensure each product meets elevated standards of performance and reliability.
Commitment to Innovation and Research: Professional manufacturers prioritize staying ahead of technological advancements and market trends by consistently dedicating resources to research and development. This steadfast commitment enables them to offer cutting-edge technologies and materials, meeting the high-performance circuit board requirements of their customers.
Customized Services:Professional manufacturers excel in delivering personalized, tailored services to meet the unique needs of diverse projects. This customization ensures that the final product aligns seamlessly with the customer’s design specifications.
In conclusion, the choice of a manufacturer profoundly impacts the quality and performance of Rigid-Flex BGA Substrate. Opting for a professional and reliable partner ensures not only top-notch products but also access to technical expertise, stringent quality control, ongoing innovation, and customized solutions for diverse project requirements.
Our company
In the dynamic sphere of Rigid-Flex BGA Substrate manufacturing, our company emerges as a beacon of innovation, an embodiment of top-tier quality, and a stronghold of customer-centric values. Specializing in the artistry of cutting-edge circuit board solutions, we revel in our role as trailblazers in the industry.
Fueled by a fusion of avant-garde manufacturing technology and a seasoned cadre of professionals, we don’t just meet industry benchmarks – we redefine them. Opting for us as your collaborative ally isn’t a mere transaction; it’s a strategic decision to align your projects with a company passionately dedicated to delivering unparalleled Rigid-Flex BGA Substrates.
How to obtain a quotation for Rigid-Flex BGA Substrate?
When choosing a manufacturer of Rigid-Flex BGA Substrate, understanding the price quote is a crucial step. The quotes provided by different manufacturers may vary, but while pursuing price, it is more important to pay attention to product quality and technical support. Here are some key considerations when it comes to getting a quote for Rigid-Flex BGA Substrate.
Quotation Transparency
Before requesting a quote from a manufacturer, make sure their quote system is transparent and clear. Understand exactly what each fee consists of so you can better compare quotes from different vendors and understand how what you pay is divided.
Explore potential supplementary charges beyond the fundamental costs associated with Rigid-Flex BGA Substrate manufacturing. Investigate whether there are any ancillary fees like those related to design modifications, expedited delivery, or special materials usage. This proactive approach ensures that your budget remains resilient against unforeseen expenses.
While cost is a crucial factor, it’s equally imperative to assess the quality and performance offered by a manufacturer. Inquire about their quality control procedures, methods for product testing, and gather feedback from previous clients. This comprehensive evaluation enables you to gauge the reliability of the manufacturer’s products, ensuring a well-informed decision beyond just pricing considerations.
Technical support and services
Technical support and service are also crucial when choosing a Rigid-Flex BGA Substrate manufacturer. Find out about the support they provide during the design phase, production phase and after product delivery. Being able to promptly resolve potential issues and obtain professional advice is key to ensuring a successful project.
Bulk pricing and delivery times
To effectively manage large-scale production, it is crucial to comprehend pricing dynamics across various batch sizes. Additionally, inquire about production lead times and delivery schedules to ensure alignment with your project timelines.
Cultivating solid partnerships with manufacturers is instrumental in securing favorable quotes. Building long-term relationships fosters better cooperation terms, such as discounted pricing and increased flexibility in delivery arrangements.
Frequently Asked Questions about Rigid-Flex BGA Substrate
What are some common design considerations and performance advantages of Rigid-Flex BGA Substrate?
Design considerations include flexible region bending radii, the design of rigid and flex transition zones, and interlayer connection methods. Performance advantages encompass improved reliability, space savings, and adaptability to complex form factors.
High-density packaging, creating compact connections and improving overall performance?
Design considerations include factors like bending radius for the flexible portion, the design of the transition zone between rigid and flexible parts, and the method of interlayer connections. A well-thought-out design ensures that the circuit board withstands stress and mechanical damage during usage.
How can one source high-quality Rigid-Flex BGA Substrate, and what factors should be considered in choosing a manufacturer?
Sourcing high-quality Rigid-Flex BGA Substrate involves selecting a reliable manufacturer. Collaboration with professional Rigid-Flex BGA Substrate manufacturers ensures product quality and performance. Considerations should extend beyond cost, prioritizing factors such as technical support and manufacturing expertise.
In which application areas does Rigid-Flex BGA Substrate find significant use?
Rigid-Flex BGA Substrate is widely employed in various fields, including smartphones, medical monitoring devices, military aviation systems, and more. Its flexibility in design makes it suitable for diverse electronic products with complex requirements.
What are some common design considerations and performance advantages associated with Rigid-Flex BGA Substrate?
Designers should be mindful of factors such as bending radii, the design of the transition zone between rigid and flexible parts, and interlayer connection methods. Performance advantages include superior space utilization, adaptability, and enhanced reliability.