Semiconductor packaging substrates fabrication. we mainly produce semiconductor substrate from 2 layer to 20 layers, ultra-small trace and spacing packaging substrate. High speed and high frequency materials, or other types of low CTE materials.
Semiconductor packaging substrates are a vital component of modern electronic devices. These substrates act as a bridge between the chip and the outside world, enabling close collaboration between electronic components. In the rapid development of the electronic field, the role of packaging substrates has become increasingly prominent, providing key support for the performance and functions of various types of equipment.
Semiconductor packaging substrates serve as the equivalent of the nervous system in electronic devices, intricately connecting minute chips to form a cohesive and operational unit. Among its primary functions is the facilitation of electrical connections, enabling chips to transmit signals and receive power. Additionally, these substrates play a pivotal role in thermal management, ensuring that chips maintain an optimal temperature during operation, thereby enhancing the stability and lifespan of the device.
To delve deeper into the diverse landscape of semiconductor packaging substrates, this exploration will meticulously analyze common types. Through a comprehensive examination of FCBGA, CSP, QFN, and BGA varieties, their distinctive characteristics and ideal use cases will be uncovered. This detailed discussion aims to empower readers with insights, enabling them to make well-informed decisions when selecting the most fitting packaging substrate for their specific application needs. By establishing a thorough comprehension of these fundamental elements, this article endeavors to provide readers with a robust foundation to navigate the intricate domain of semiconductor packaging.
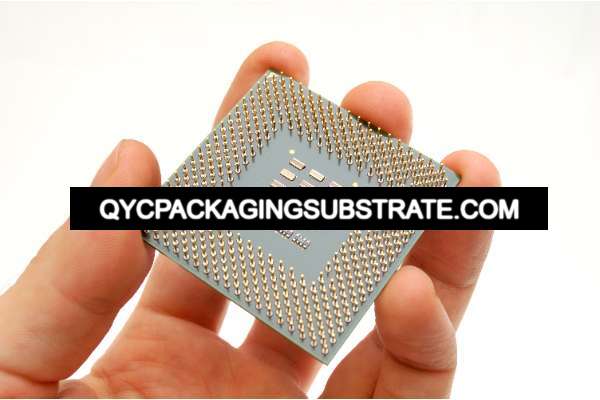
Semiconductor packaging substrates
In-depth analysis of FCBGA packaging substrate
FCBGA, short for Ball Grid Array packaging, represents an advanced semiconductor packaging technology employing a grid of ball-shaped pins to establish connections between the chip and the printed circuit board (PCB). This configuration ensures outstanding connectivity and performance for electronic devices.
Extensive Application: FCBGA packaging finds widespread application in semiconductor domains encompassing microprocessors, graphics processors, and embedded systems. Its design is particularly well-suited for high-performance computing and intricate electronic equipment, making it a go-to choice in these fields.
High-density connections: FCBGA provides high-density pin connections with its compact spherical arrangement. This design enables more connections on a small chip, providing more functionality for advanced electronics.
Superior Thermal Management: Due to the ball grid array structure, the FCBGA package has excellent thermal management performance. This makes it ideal for high-performance chips, ensuring stability over long periods of operation and under high load conditions.
Reliability and performance advantages: The FCBGA package provides excellent reliability through its rugged connections and low-resistance paths. Not only does this help reduce signal distortion, it also improves overall performance and responsiveness.
Through in-depth research on FCBGA packaging, we can see its multiple advantages in the semiconductor field, providing strong support for the design and manufacturing of advanced electronic equipment.
CSP packaging substrate
CSP, or Chip Scale Packaging, is an advanced packaging technology whose basic principles revolve around encapsulating the entire chip in a small, compact packaging substrate. Compared with traditional packaging, CSP adopts a more compact design and integrates circuits, connecting wires and packaging materials directly around the chip, achieving higher integration and performance.
The core of this technology is to minimize the physical size of the package and integrate the package and chip into a whole through clever layout and design. CSP usually adopts bare die packaging, that is, the exposed chip is placed on the packaging substrate and connected through micro-arc welding or other high-density connection technology. This design eliminates external wiring and connectors used in traditional packages, minimizing the physical size of the package.
The importance of CSP lies in its ability to meet the needs of modern small devices. As the size of electronic products continues to shrink, the space requirements for packaging substrates have become more stringent. In this regard, CSP has been widely used due to its compact design and highly integrated features.
Small mobile devices: In small mobile devices such as smartphones and wearable devices, CSP’s small size and lightweight design make it an ideal choice. It not only provides higher performance, but also effectively reduces the overall size of the device, making the device more lightweight and compact.
In the medical realm, the micro-encapsulation capabilities of Chip Scale Packages (CSP) offer heightened flexibility in the design of medical devices. Particularly in applications like medical sensors and implantable medical equipment that demand extensive integration and miniaturization, the adoption of CSP emerges as a pragmatic solution.
In the realm of portable consumer electronics, CSP is steering the transformation of devices ranging from headphones to smart glasses. The compact design facilitated by CSP not only enhances portability but also ensures that these devices maintain optimal performance without sacrificing functionality.
Overall, the CSP packaging substrate provides an advanced and efficient packaging solution for small devices with its unique design and adaptability, and has become an important technology that cannot be ignored in the electronics industry.
In-depth analysis of QFN packaging substrate
QFN (Quad Flat No-Leads) packaging substrates stand as a crucial technology within the semiconductor packaging landscape, earning profound respect in the industry for their distinctive characteristics. Notably, the leadless design of QFN packages sets them apart. In contrast to traditional lead packaging, QFN forgoes leads by directly soldering the chip’s pad to the PCB, resulting in a more compact and reliable connection. This design not only enhances circuit reliability but also significantly reduces package size, making it a prevalent choice in highly integrated electronic equipment.
A standout feature of QFN is its exceptional heat dissipation performance. Direct connection to the PCB allows the package’s bottom to efficiently dissipate heat. This heat dissipation design markedly improves chip stability during high-load operations, particularly beneficial for applications with stringent heat dissipation requirements, such as high-performance computers and communication equipment.
Furthermore, QFN’s compact size is a key attribute. Its design, with thinness in the vertical direction, proves crucial for electronic products emphasizing slim and lightweight profiles. Compared to alternative packaging forms, QFN utilizes space more efficiently, delivering a smaller footprint and positioning itself as an optimal choice for mobile devices and similar applications.
In the dynamic landscape of the semiconductor industry, QFN packaging substrates find widespread use in electronic equipment manufacturing, owing to their unique attributes. The combination of a compact design and exceptional thermal performance offers an ideal solution for crafting high-performance and miniaturized devices in today’s design landscape. Through a comprehensive grasp and application of QFN technology, electronics manufacturers can foster greater innovation in product design, enhance performance, and adeptly respond to evolving market demands.
BGA package substrate
BGA, or ball grid array packaging, is an advanced semiconductor packaging technology. Its structure is unique, and its core lies in connecting the chip and the substrate with spherical solder joints to form a dense arrangement structure. Each ball-shaped solder joint represents an electrical connection, forming an electrical connection bridge between the semiconductor chip and the substrate. This design allows BGA to play an important role in high-density circuit integration.
The BGA’s ball grid array layout allows for more connection points and is more space efficient than traditional packaging. This makes BGAs ideal for highly integrated circuits, especially where a large number of connections need to be accommodated in a limited space.
BGA packages provide short and direct connection paths, reducing resistance and inductance for signal transmission and improving electrical performance. This is critical for applications in high-density integrated circuits where signal integrity needs to be maintained.
Since the BGA ball solder joints cover the entire bottom, its heat dissipation performance is relatively good. In high-density integrated circuits, device stability and performance are often closely related to heat dissipation, and BGA excels in this regard.
Another advantage of BGA packaging in high-density integrated circuits is its strong maintainability. The structure of the ball grid array makes welding and repair relatively easy, reducing the difficulty of overall maintenance.
The high degree of integration and excellent performance of BGA packaging substrates make it one of the most important and widely used packaging technologies in today’s electronic field. Through its unique structure and application advantages, BGA has shown strong potential in high-density integrated circuit design and promoted the continuous progress of electronic technology.
Future development trends of semiconductor packaging substrates
In the field of semiconductor packaging substrates, continuous innovation is the engine that drives industry development. In the future, we can expect the rise of the following innovation directions:
Integration of advanced materials: The semiconductor industry will strive to develop and integrate more advanced materials to improve the performance and reliability of packaging substrates. For example, exploring new heat dissipation materials to solve the heat dissipation needs of high-performance chips.
Popularization of embedded technology: Embedded packaging technology will become a future trend, allowing more functions to be integrated into small chips. Such innovations will drive the miniaturization and performance improvement of electronic devices.
Higher-density interconnections: As the demand for higher performance in electronic devices continues to grow, semiconductor packaging substrates will evolve towards higher-density interconnections to meet the requirements of complex circuit layouts.
The continuous advancement of technology has a profound impact on the semiconductor industry and will show significant changes in the following aspects:
Artificial Intelligence Integration: Semiconductor packaging substrates will be increasingly used to support artificial intelligence (AI) applications. This includes the development of specialized chips to handle complex AI algorithms more efficiently.
5G technology promotion: With the popularization of 5G technology, packaging substrates will require higher performance and lower latency. This will drive the demand for new packaging substrates to accommodate high-speed data transmission and processing requirements.
Sustainability practices: As society’s focus on sustainability increases, the semiconductor industry will focus on developing environmentally friendly packaging substrates to reduce its impact on the environment.
Customized design: Technological progress will promote the trend of customization of packaging substrate design to meet the specific needs of different industries and applications.
Overall, semiconductor packaging substrates will usher in more innovations amid the changing technological trends, thereby promoting the development of the entire electronics industry. The key is to maintain a focus on sustainability and environmental protection while constantly exploring new technologies to ensure the sustainable development of the industry.