Showa Denko/Ajinomoto Packaging Substrate Manufacturer. Showa Denko and Ajinomoto packaging substrate material design rules. Advanced ABF packaging substrate manufacturer. Design rules for packaging substrates are an important part of the semiconductor manufacturing and electronic packaging fields. They are a set of guidelines developed to ensure that packaging substrates are designed to meet the needs of a specific application to improve performance, reliability and production efficiency. In this article, we’ll take a closer look at packaging substrate design rules, why they’re critical, and how to apply them effectively.
Design rules for package substrates
The importance of design rules:Design rules are critical to the success of packaging substrates. They help ensure that the electrical performance, thermal management, mechanical stability and reliability of the package substrate are considered during the design phase. Here are the importance of design rules:
Performance optimization: By following design rules, the performance of the packaging substrate can be optimized, including signal transmission speed, electrical characteristics and heat dissipation performance.
Reliability enhancement: Design rules help reduce electrical failures and physical damage on circuit boards and improve the reliability of packaging substrates.
Cost Savings: Effective design rules reduce manufacturing and maintenance costs as they help avoid unnecessary errors and repairs.
Standardization: Design rules help standardize the design process to ensure consistency and maintainability.
Package Substrate Common design rules
Design rules can vary based on the specific package substrate type and application, but here are some common design rule examples:
Layer stacking rules: This includes determining how many layers of packaging substrate will be used for a specific application as well as layer spacing rules.
Line width and line spacing rules: These rules specify the minimum width of circuit lines and the minimum distance between lines to ensure electrical performance.
Hole rules: The diameter, spacing, and location of holes are specified to accommodate the pins or ball grids of connecting components.
Packaging standard rules: These rules include regulations on package size, shape and materials.
Thermal Management Rules: Determine rules for heat sinks, cooling pads, and heat dissipation channels to effectively manage heat.
Impedance matching rules: These rules involve controlling the characteristic impedance of the circuit to ensure signal integrity.
Pin and ball grid rules: stipulate the location, arrangement and connection of pins or ball grids.
Key steps in applying design rules
The application of design rules is a systematic process that requires experience and expertise. Here are the key steps for applying design rules:
Determine requirements: First, clearly define the application requirements for the packaging substrate, including performance, functionality, and environmental conditions.
Select appropriate design rules: Select applicable design rules based on application needs, which may include standard industry rules or custom rules.
Design layout: Create the layout of the package substrate, including the layout of circuits, components, pins, heat sinks, etc.
Comply with rules: Ensure that the design complies with the selected design rules and use design tools for verification and simulation.
Prototype testing: Prototype packaging substrates are made and tested to verify performance, reliability and quality.
Continuous improvement: Continuous improvement of the design based on test results to meet needs and improve performance.
Mastering Advanced Packaging Substrate Designs
Design rules are a key tool in ensuring that packaging substrates meet specific application requirements. They help optimize performance, increase reliability and reduce costs. When designing a packaging substrate, following applicable design rules and performing appropriate verification and testing are critical steps to ensure a successful project. Effective application of design rules will help meet the growing electronics market’s demand for high-performance, high-reliability packaging substrates.
Packaging substrate material introduction
Package substrate (Package Substrate) is an important part of electronic manufacturing and plays a key role in connecting and supporting integrated circuits (ICs). There are many types of these packaging substrates, each suitable for different application needs and design challenges. Here are some of the major Package Substrate types that play an important role in electronics manufacturing:
1.Printed Circuit Boards (PCBs): Printed circuit boards are one of the most common types of Package Substrate. They are typically made from multiple layers of composite materials, including conductive layers, insulating layers and vias. PCBs have a wide range of applications, from consumer electronics to communication equipment, because their multi-layer structure can support complex circuit designs.
2.Multi-Chip Modules (MCMs): Multi-Chip Modules are a Package Substrate designed to accommodate multiple chips on a single substrate. This design form provides a highly integrated solution suitable for space-constrained applications such as mobile devices and communication systems.
3.Ceramic Substrates: Ceramic packaging substrates use ceramic materials with high thermal conductivity, such as aluminum oxide (Alumina) or aluminum nitride (Aluminum Nitride), to effectively dissipate heat. This makes them ideal for high-power electronic devices such as power amplifiers and LED packaging.
4.Organic Substrates: Organic packaging substrates usually use organic resin composite materials, such as epoxy resin (FR-4). They are lightweight, cost-effective and suitable for use in many consumer electronics products such as smartphones and tablets.
5.Interposers: Interposers is a specially designed Package Substrate to provide a connection interface between the chip and the package. They support heterogeneous integration and highly complex packaging technologies such as 2.5D and 3D stacking.
Each Package Substrate type has its own unique characteristics and applicability, allowing it to meet the needs of different electronic devices. As technology continues to evolve, different types of Package Substrate will continue to evolve to meet changing market needs and innovative design challenges. In electronics manufacturing, the correct selection of the appropriate Package Substrate type is critical to ensuring product performance and reliability.
Production equipment and process capability of packaging substrate
Production equipment and process capabilities for packaging substrates are core elements in the semiconductor manufacturing and electronic packaging processes. The effective application of these equipment and processes is critical to ensuring high quality, reliability and performance of packaging substrates. This article will provide an in-depth introduction to the production equipment and process capabilities of packaging substrates to help understand their critical role in electronics manufacturing.
Production equipment
Printing machine: The printing machine is used to print conductive ink or solder film on the surface of the package substrate to create circuits and connections. High-precision printing machines ensure the accuracy of line width and line spacing.
Lithography equipment: Lithography equipment is used to form precise patterns and structures on packaging substrates. This is important for creating complex lines and connections.
Etching equipment: Etching equipment is used to remove excess material in order to form the required circuit pattern. It can use chemical etching or laser etching techniques.
Laminator: A laminator is used to laminate different layers of multi-layer packaging substrates together to form an overall structure. This ensures connections between circuit layers.
Drilling machine: Drilling machine is used to drill holes in the package substrate to insert connecting pins or ball grids.
Heat treatment equipment: Heat treatment equipment is used to heat and cool the packaging substrate to complete process steps such as curing and bending.
Process capability
Precision and resolution: The precision and resolution requirements for packaging substrate manufacturing are very high. This includes accuracy of line width and spacing, control of hole diameter and location, and clarity of pattern.
Material selection and compatibility: Process capabilities need to consider the type of materials used, such as organic substrates, ceramic substrates, or high-frequency dielectric substrates. The process must be compatible with the material chosen.
Lamination and penetration capabilities: For multi-layer packaging substrates, the process must be able to achieve lamination and penetration between different layers to ensure circuit connectivity.
Heat treatment and heat dissipation: For high-power applications, the process must have appropriate heat treatment capabilities to ensure heat dissipation and thermal management.
Impedance matching and signal integrity: High-speed and high-frequency applications require processes that can achieve impedance matching to maintain signal integrity.
Quality control and traceability: The process requires strict quality control and traceability to ensure that the product meets standards and specifications.
Key Process Challenges
The manufacturing process of packaging substrates involves many complex steps and materials, and therefore presents several challenges, including:
Accuracy and consistency: Ensure that different batches of packaging substrates have the same performance and quality requirements.
Material compatibility: Make sure the selected materials are compatible with the manufacturing process to avoid adverse reactions or bonding issues.
Production efficiency: Improve production efficiency to reduce production time and costs.
Environmental factors: Ensure that the process complies with environmental protection regulations and standards.
In short, the production equipment and process capabilities of packaging substrates are key factors to ensure that packaging substrates meet high performance, high reliability and high quality requirements. Manufacturers need to invest in advanced equipment and process technology to meet the needs of the evolving electronics market. These capabilities not only affect product quality, but also have an important impact on production efficiency and competitiveness.
Quality requirements for packaging substrates
The quality requirements of packaging substrates are critical in electronics manufacturing because they directly affect the performance, reliability and longevity of the final product. Quality requirements cover many aspects, including the quality of materials, control of the manufacturing process, and testing and inspection procedures.
Material quality
Quality requirements for packaging substrates start with the quality of the materials selected. Here are some key material quality requirements:
Chemical composition and purity: Materials must meet specific chemical composition and purity standards to ensure the stability of their electrical and physical properties.
Mechanical Properties: A material’s mechanical properties, such as flexural strength, tensile strength and hardness, must meet the application requirements to prevent buckling or cracking.
Thermal Properties: Materials must have appropriate thermal conductivity properties for effective heat dissipation and thermal management, especially in high-power applications.
Dimensional stability: The dimensions of the material must remain stable across temperatures to ensure the accuracy and reliability of the packaging substrate.
Manufacturing process control
The manufacturing process of the packaging substrate is a key factor in ensuring quality. The following are some quality requirements related to manufacturing process control:
Process parameter control: Various parameters of the manufacturing process, such as temperature, pressure and time, must be strictly controlled to ensure consistent product quality.
Prevent contamination: Manufacturing environments must be tightly controlled to prevent the entry of impurities and contaminants that could cause electrical failure or degraded performance.
Lamination and penetration control: For multi-layer packaging substrates, lamination and penetration must be strictly controlled to ensure circuit connections between layers.
Material Handling: Material handling processes, such as chemical treatments and coatings, must be precisely controlled to ensure their performance and quality.
Testing and Inspection Procedures
Quality requirements for packaging substrates also include testing and inspection procedures to ensure products meet specifications. The following are some relevant quality requirements:
Electrical Performance Testing: Package substrates must undergo electrical testing to ensure connectivity, impedance matching, and signal integrity.
Thermal performance testing: For high-power applications, thermal performance testing must ensure the effectiveness of heat dissipation and thermal management.
Reliability testing: Package substrates must undergo reliability testing, such as accelerated life testing and environmental testing, to evaluate their long-term performance.
Size and shape inspection: The size and shape of the package substrate must meet specifications to ensure that it will fit and connect correctly.
Visual Inspection: A visual inspection is used to detect any cosmetic defects such as cracks, bubbles or stains.
Traceability
Quality requirements also include product traceability, which means that each packaging substrate must have clear identification and traceability information to allow tracking and traceability if needed. This is critical for troubleshooting, quality improvement and market surveillance.
Compliance
Package substrates must comply with applicable regulations and standards, including environmental regulations, safety standards and industry specifications. This helps ensure the legality and acceptability of the product in the market.
In general, the quality requirements of packaging substrates are a crucial factor in electronic manufacturing, so
They are directly related to the performance, reliability and cost of the final product. Manufacturers need to ensure the quality of materials, control of manufacturing processes, and effectiveness of testing and inspection procedures to meet market and customer needs. High-quality packaging substrates help ensure the long-term reliability and performance of electronic products, which is critical to meeting changing market demands.
What is a semiconductor package substrate?
Definition of semiconductor packaging substrate
Semiconductor packaging substrate, often referred to as packaging substrate or circuit board, is a flat substrate, usually made of insulating materials, such as organic resin, ceramics or glass, on which conductive lines and pins for connecting components are laid. Its main purpose is to connect ICs, transistors, capacitors, resistors and other electronic components together to build a complete circuit while providing support and electrical connections.
Functions of semiconductor packaging substrates
Electrical connection: The wires on the package substrate and the pins of the connecting components are used to connect ICs with other electronic components to achieve electrical connection and signal transmission. This electrical connection is key to the proper functioning of electronic devices.
Thermal management: Semiconductor devices generate heat when running. In order to prevent overheating damage and ensure stable performance, the packaging substrate must have the functions of heat dissipation and heat conduction. Some package substrates use materials with good thermal conductivity properties, such as ceramics, to help dissipate heat.
Mechanical support: The packaging substrate provides mechanical support to prevent ICs and other components from being damaged in the physical environment. They ensure that electronic components are securely positioned against shock, shock, and other stresses.
Environmental protection: The packaging substrate can provide a certain degree of protection against dust, moisture and chemical substances from invading electronic components. This is critical to extending the life and reliability of your equipment.
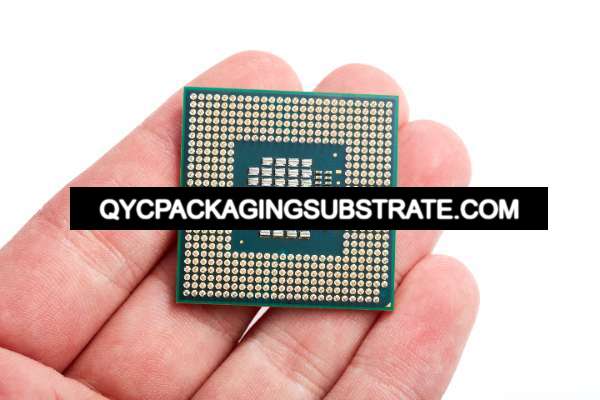
Showa Denko/Ajinomoto Packaging Substrate
The key role of semiconductor packaging substrate
Integrated circuit protection: The packaging substrate provides protection for ICs from mechanical and environmental damage. This is critical to maintaining the performance and reliability of ICs.
Circuit connection and signal transmission: Through circuits on the packaging substrate, ICs can communicate with other components to achieve data transmission and signal processing. This makes the packaging substrate the basis for realizing various functions in electronic devices.
Thermal management and heat dissipation: The heat generated by high-performance semiconductor devices needs to be effectively dissipated to prevent overheating damage. Package substrates can help manage heat through material selection and structural design.
Size and weight control: The design of the packaging substrate can affect the size and weight of the device, so they are critical to the design of thin, light, and portable devices.
Reliability of electronic equipment: The design and manufacturing quality of packaging substrates are directly related to the reliability of electronic equipment. High-quality packaging substrates help reduce device failure rates.
Overall, semiconductor packaging substrates are critical components of modern electronic devices. They play important roles in providing electrical connections, thermal management, mechanical support and protection. Their design and material selection are critical to device performance, reliability and cost, and therefore play a vital role in semiconductor manufacturing. Continuous technological innovation and process improvement will continue to promote the development of packaging substrates to meet the growing needs of the electronics market.
Types of semiconductor packaging substrates
Semiconductor packaging substrates are vital components in electronics manufacturing and come in a variety of different types, each suited to specific applications and needs. These different types of packaging substrates are commonly used to connect, support and protect integrated circuits (ICs) and other electronic components.
Organic Substrates
Organic packaging substrates are usually made of organic resin composite materials, such as fiberglass-reinforced epoxy resin (FR-4). They are one of the most common packaging substrate types.
Features
Lightweight: Organic packaging substrates are very light and suitable for thin and light electronic devices.
Low cost: They are usually competitively priced and suitable for high-volume production.
Electrical insulation: Organic packaging substrates have good electrical insulation properties.
Package Substrate Application areas
Consumer electronics: such as smartphones, tablets and laptops.
Communications equipment: such as routers, switches and base stations.
Ceramic Substrates
Ceramic packaging substrates are usually made of aluminum oxide (Alumina) or aluminum nitride (Aluminum Nitride), which have excellent thermal conductivity and can effectively dissipate heat in high-power electronic applications.
Features
High thermal conductivity: Ceramic package substrates can effectively dissipate heat and are suitable for high-power applications.
Mechanical stability: They have high mechanical strength and stability.
Application areas
High-power semiconductors: such as power amplifiers, LED packages and laser diodes.
High temperature applications: such as heat-sensitive electronic equipment.
High-Frequency Substrates
High frequency dielectric packaging substrates are specifically designed for radio frequency (RF) and microwave applications. They are usually made of polytetrafluoroethylene (PTFE) materials such as TEFLON.
Features
Low dielectric loss: High-frequency dielectric encapsulation substrates have low dielectric loss to help maintain signal integrity.
High Frequency Characteristics: They are suitable for high frequency RF applications.
Application areas
Communication equipment: such as radio frequency antennas, microwave circuits and satellite communication equipment.
High frequency radar system.
Glass Substrates
Glass packaging substrates are usually made of glass materials and have excellent flatness and dimensional stability.
Features
Flatness: Glass packaging substrates are extremely flat and suitable for high-precision applications.
Dimensional stability: Their dimensions remain stable at different temperatures.
Application areas
Display technologies: such as liquid crystal displays (LCD) and organic light-emitting diode (OLED) displays.
Optical components: such as lenses and fiber optic connections.
Composite Substrates
Composite packaging substrates are often layered from different types of materials to address different performance requirements.
Features
Performance diversity: Composite material substrates can combine the advantages of different materials to meet diverse needs.
Application areas
High-end applications requiring multiple performance requirements.
In general, there are many types of semiconductor packaging substrates, each suitable for different application areas and needs. Engineers and designers need to select the appropriate packaging substrate type based on specific project requirements to ensure device performance, reliability and cost are protected.