BGA Package Substrate Vender, we build ultra-small bump pitch IC/BGA substrate from 2 layer to 20 layers, ultra-small trace and spacing packaging substrate and smallest gap PCBs.
At the forefront of modern technology, the electronics industry relies heavily on various essential components. Among these, packaging substrates and printed circuit boards (PCBs) stand out as fundamental elements in constructing electronic devices and systems. They assume a pivotal role in facilitating the functionality and performance of electronic products.
This article will delve into the distinctions between packaging substrates and PCBs, emphasizing the critical need for electronic engineers, manufacturers, and product designers to grasp these differences. Whether you are a seasoned professional or an enthusiast with a keen interest in electronics, a comprehensive comprehension of these foundational concepts will empower you to gain deeper insights into the production and optimization of electronic products.
This article will focus on the differences between packaging substrates and PCBs and how important it is for electronic engineers, manufacturers and product designers to understand the key differences between them. Whether you are a professional or an individual interested in the field of electronics, a thorough understanding of these fundamental concepts will help you better understand the manufacturing and performance optimization of electronic products.
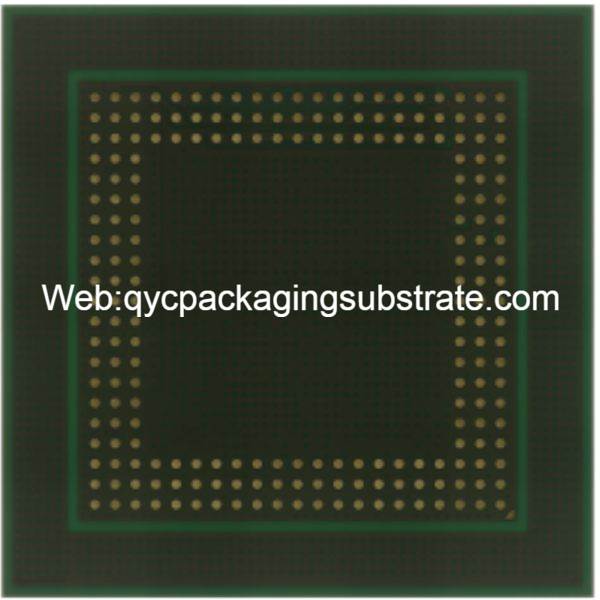
BGA package substrate
PCB and Package Substrates: Basic Concepts
PCB is a flat base material, usually made of insulating material, covered with conductive material to form circuit patterns.
The primary purpose of a PCB is to furnish mechanical support and electrical connections for electronic components, all while upholding the circuit’s reliability and stability. PCBs find wide-ranging applications in various electronic devices, including computers, mobile phones, televisions, and automobiles.
Basic Principles and Functions of Packaging Substrates
Packaging substrates, a distinct category of base materials, are routinely employed to encapsulate and interconnect microelectronic packages such as integrated circuits (ICs) and other packaged components. Their principal function is to serve as a platform for linking and upholding microelectronic components, ensuring their proper functionality.
Packaging substrates assume a pivotal role in high-performance electronic devices by facilitating signal transmission, heat management, and mechanical support. Consequently, they enhance the performance and reliability of electronic devices. A deeper understanding of these two fundamental concepts allows for a more comprehensive exploration of their distinctions and significance.
Difference 1: Structure and Design
Structural differences: There are significant structural differences between printed circuit boards (PCBs) and packaging substrates. PCBs are usually made from an insulating base material (such as FR-4) with a conductive layer, where copper foil usually forms the circuit path. The packaging substrate usually adopts a multi-layer structure, including an insulating layer, a conductive layer and a packaging bottom material. This multi-layer structure makes the packaging substrate more suitable for the needs of high-performance packaging and integrated circuits.
Circuit design and wiring differences: PCB and package substrate have different requirements in terms of circuit design and wiring. PCB is often used in traditional circuit design, where the design focus is on the optimization of connections and wiring. While packaging substrates have advantages in high-density packaging and microelectronic packaging, their designs need to better manage factors such as signal speed, power distribution, and thermal management. Therefore, the design of the packaging substrate is more complex, involving more layers and density.
These two structural and design differences give PCBs and packaging substrates different roles and suitability in electronic systems, so understanding their differences is critical to choosing the right solution.
Difference 2: Application fields
Wide application fields of PCB
Printed circuit boards (PCBs) are an essential component in the electronics industry, finding widespread application in critical areas, including:
Computer Technology: PCBs assume a vital role in computer motherboards, memory modules, and peripherals, providing the necessary infrastructure for high-speed data transmission and signal processing.
Communication Sector: PCBs are instrumental in the production of various communication devices, including mobile phones, routers, and base stations. They must meet intricate signaling requirements to ensure the reliability of communications.
Consumer Electronics: PCBs are widely used in consumer electronics products such as smartphones, televisions, and audio systems. They support multimedia processing and interconnection.
Packaging substrates for high performance and integrated circuit applications
Packaging substrates have unique application requirements in high-performance packaging and integrated circuits, including:
High-density packaging: Packaging substrates are widely used in high-density integrated circuit (IC) packaging. Its complex structure allows the IC to be connected to other components and provides good electrical performance.
Radio Frequency (RF) Applications: The performance of packaging substrates in RF and microwave circuits is critical. They are used to support high-frequency signal transmission, such as communications and radar systems.
High-Performance Computing: Modern high-performance computing and data centers require packaging substrates to support high-speed data transmission and heat dissipation to meet the needs of processing complex tasks.
These different application areas highlight key differences between PCB and packaging substrates, including performance, design and material requirements. Understanding these requirements is critical to choosing the right solution.
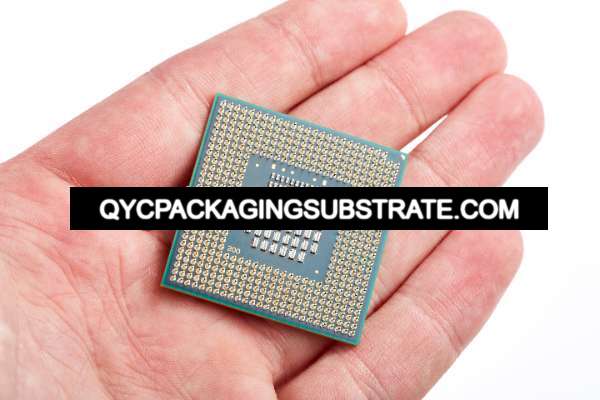
BGA package substrate
Difference Three: Materials and Manufacturing
PCB manufacturing process and materials
Printed circuit boards (PCBs) are commonly crafted from several layers of fiberglass and composite materials, including FR-4.
The manufacturing of PCBs encompasses various steps like etching, cutting, drilling, and more, which are essential for establishing circuit patterns.
PCB manufacturing predominantly relies on standardized processes and is well-suited for large-scale production.
In contrast, the production of packaging substrates entails a more intricate and diverse set of processes and materials.
Manufacturing processes and materials for packaging substrates
The packaging substrate uses high-performance substrates, such as ceramics (Ceramic), high-frequency materials, etc., to meet the needs of high-frequency signal transmission and thermal management.
Manufacturing packaging substrates requires more complex processes, such as multi-layer stacking, metal layer deposition to obtain interconnects, and complex hole processes.
These advanced materials and processes ensure the high performance, thermal stability and reliability of the packaging substrate.
These differences in materials and manufacturing have a significant impact on the performance and reliability of PCB and packaging substrates.
Difference 4: Performance and requirements
Comparison of performance requirements
In the electronics world, there are significant differences in performance requirements between PCBs and packaging substrates. First, PCBs are typically used for low-speed signal transmission and are suitable for lower signal speeds and frequencies. In contrast, packaging substrates excel at high-speed signal transmission and are suitable for high-frequency applications such as high-performance microprocessors and radio frequency circuits.
In addition, packaging substrates have higher requirements for signal integrity and interconnection impedance control to ensure accurate signal transmission. This is critical for high-speed data transmission and differential signal processing. PCBs, on the other hand, are generally easier to implement and do not require as precise impedance matching as package substrates.
Unique role in electronic systems
Despite differences in performance and applications, PCBs and packaging substrates have unique roles in electronic systems. PCB is usually used in the motherboard design of electronic products as a bridge between different components. They support the connection and mounting of electronic components while providing a circuit path.
Packaging substrates play a key role in high-performance electronic packaging. They are used in integrated circuit packaging to provide electrical connections, heat dissipation and signal transmission. The high-performance requirements and complex design of packaging substrates make them suitable for areas requiring high-speed signal transmission and complex electronic functions, such as high-end servers, communication equipment, and computer processors.
In general, although there are performance and application differences between PCB and packaging substrates, they both play an important role in electronic systems and meet the needs of different electronic devices. The choice between these materials depends on the specific application, performance requirements and design goals.
In conclusion
Summarize the key differences between PCB and packaging substrate
In this article, we explore in detail the important differences between printed circuit boards (PCBs) and packaging substrates. We found significant differences between the two from multiple perspectives such as structure, design, application areas, materials and performance requirements. These differences impact their core functionality and use in the electronics industry.
Emphasizes the importance for electronic engineers and manufacturers of understanding their differences
Understanding the difference between PCB and packaging substrate is critical for electronics engineers and manufacturers. It helps ensure that the right technology and materials are selected to meet the needs of a specific application. This understanding can improve performance, reliability, and efficiency during design and manufacturing, driving continued advancements in electronics. Therefore, understanding these key differences is a critical step in successful electronic product development and production.