Professional ABF Substrate Supplier, The package substrate were made with Ajinomoto base materials: they are GX92R, GXT31R2,GZ41R2H,GL102R8HF. and other types material.
ABF Substrate (Build-Up Film substrate containing colloidal copper phosphate) is an advanced material in the field of PCB engineering. The technological innovation behind it provides strong support for the development of electronic equipment. This substrate material has attracted much attention mainly due to its unique design concept and exquisite manufacturing process.
The “colloid-free” feature of ABF Substrate distinguishes it from traditional substrate materials. It uses a colloid-free structure, which means there is no adhesive layer of traditional colloids between the substrate layers. Instead, a highly sophisticated manufacturing process is used to effectively stack the layers together to create a strong and tight structure.
The realization of this colloid-free structure not only requires precise control of every step in the manufacturing process to ensure precise alignment of each layer, but also requires the use of advanced production equipment and technology. Through this highly precise manufacturing process, ABF Substrate is able to achieve its unique design goals and provide outstanding performance for electronic devices.
In the manufacturing of ABF Substrate, the key colloidal copper phosphate plays a vital role. This special material, with its excellent electrical and thermal conductivity, provides circuits with good signal transmission and thermal management capabilities. By cleverly integrating colloidal copper phosphate into a colloid-free structure, ABF Substrate not only ensures the stability of the circuit, but also meets the stringent requirements for high-frequency signal transmission and thermal management.
Overall, the definition of ABF Substrate reflects the continuous pursuit of advanced technology. Its colloid-free structure and highly precise manufacturing process are a revolutionary attempt in PCB engineering, providing more reliable and efficient substrate materials for electronic devices. In the pursuit of smaller, lighter, and stronger electronic products, ABF Substrate’s innovative design has become a key part of achieving this goal.
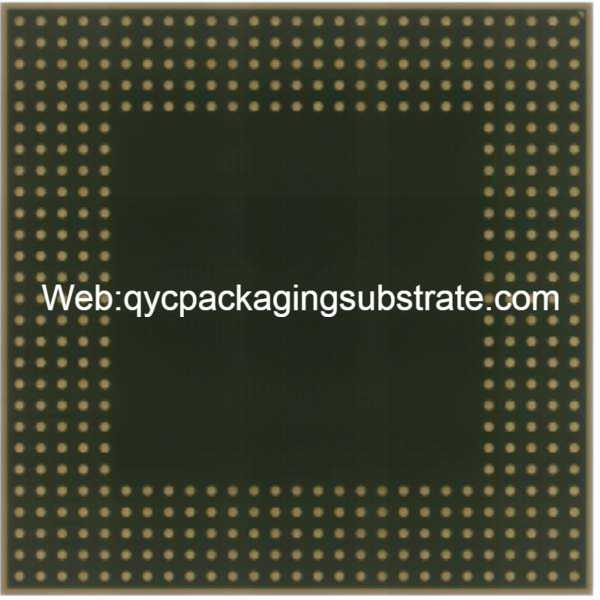
ABF Substrate
What are the functions of ABF Substrate?
ABF Substrate is an innovative substrate material that plays a vital role in PCB engineering. Its unique design uses a colloidal copper phosphate-free structure and uses a highly precise manufacturing process to provide excellent performance in electronic devices. In this article, we will delve into the capabilities of ABF Substrate in electronic devices, including its critical role in high-frequency signal transmission, thermal management, and packaging.
First of all, one of the key roles of ABF Substrate in electronic devices is to achieve low-loss characteristics of high-frequency signal transmission. Its colloid-free structure allows it to perform well at high frequencies, ensuring the stability and reliability of signal transmission. This characteristic is crucial for the high-frequency communication and data transmission requirements in modern electronic devices, making ABF Substrate ideal for advanced electronic devices.
Simultaneously, ABF Substrate assumes a crucial role in thermal management within electronic systems. Its commendable thermal conductivity becomes instrumental in efficiently dissipating heat generated during the operation of electronic devices, contributing to the maintenance of a stable operating temperature. In the context of contemporary highly integrated electronic systems, effective thermal management stands out as a pivotal factor ensuring optimal device performance and longevity.
In addition, ABF Substrate also shows strong support capabilities in packaging. As the ideal basis for IC packaging, ABF Substrate uses advanced packaging technology to provide reliable protection and connection for the chip. This comprehensive combination of high-frequency signal transmission, superior thermal management and advanced packaging technology makes ABF Substrate increasingly popular in electronic device design and manufacturing.
To sum up, ABF Substrate not only excels in high-frequency signal transmission, but also plays a key role in thermal management and packaging. Its application promotes the performance and stability of electronic devices and brings new innovations and possibilities to the field of PCB engineering. As technology continues to advance, ABF Substrate will undoubtedly continue to play a key role in future electronic device design, pushing the entire industry to new heights.
What are the types of ABF Substrate?
ABF Substrate, or colloidal copper phosphate substrate, stands as a pivotal material in the field of PCB engineering, offering a diverse range of types that broaden the scope of application possibilities for electronic equipment. Categorized primarily into single-layer, multi-layer, and high-density integrated circuits (HDI), each variant plays a distinct role in specific application scenarios.
The single-layer ABF Substrate serves as a fundamental material ideal for applications with cost constraints. Its uncomplicated structure, predominantly composed of a single material, presents a cost-effective solution for crafting lightweight electronic devices. Widely deployed in consumer electronics such as smartphones and digital cameras, this type of ABF Substrate caters to the demand for devices that are thin, light, and highly portable.
Multi-layer ABF Substrate comes into play in scenarios that require higher complexity circuits. By stacking multiple layers of films, more complex circuit designs can be achieved, providing higher integration and performance. This type of ABF Substrate is widely used in fields such as computers, communication equipment, and automotive electronics, meeting the requirements for high performance and high reliability.
High-density integrated circuit (HDI) ABF Substrate is an advanced material that achieves the ability to integrate more functions in a smaller space by using fine line widths and higher inter-layer connection density. This makes HDI ABF Substrate an ideal choice for advanced electronic products such as high-end servers, network equipment and medical electronics. Its excellent electrical performance and compact design enable it to accommodate high-density layouts and advanced packaging technologies.
Overall, different types of ABF Substrate have unique advantages in the design and manufacturing of electronic devices. Single layer is suitable for simple and economical scenarios, multi-layer is suitable for more complex applications, and HDI ABF Substrate provides innovative solutions for high-density and high-performance fields. By flexibly using these types, PCB engineers can choose the most appropriate ABF Substrate according to specific needs, pushing electronic product technology to new heights.
What is the relationship between ABF Substrate and IC packaging?
ABF Substrate (colloidal copper phosphate substrate) plays a vital role in modern electronic manufacturing, especially in the field of integrated circuit (IC) packaging. This advanced substrate material provides critical support for advanced chip packaging through its unique structure and precise manufacturing process.
In the field of IC packaging, ABF Substrate occupies an indispensable position. Its colloid-free structure provides the ideal basis for advanced packaging technologies. By using a highly precise manufacturing process, ABF Substrate ensures a stable connection between the chip and the substrate, providing a solid foundation for the reliability and performance of electronic devices.
The application of ABF Substrate is not only simple substrate support, but also involves innovation in packaging technology. Its packaging technology classification includes:
Improved HDI manufacturing technology: ABF Substrate enables smaller, lighter, and higher-performance IC packages through improvements in high-density interconnect (HDI) technology. This technological improvement allows more circuit components to be integrated into a smaller space, improving device integration and performance.
Improved semi-additive method: ABF Substrate adopts a semi-additive method to achieve a high degree of customization of the substrate structure through additional thin film layers and fine processing techniques. This method improves the reliability and stability of the substrate and adapts to diverse packaging needs.
The combination of these two packaging technologies makes ABF Substrate an ideal choice for advanced IC packaging, promoting continuous innovation in the size, performance and functionality of electronic devices.
The reason why ABF Substrate is so popular in IC packaging is not only because of its physical properties, but also because of its comprehensive support for advanced chip packaging. From high-density interconnection to semi-additive methods, ABF Substrate provides a stable support structure for chips and a reliable platform for the implementation of advanced packaging technologies.
In the rapid development of the electronics industry, the advancement of IC packaging technology is crucial to the performance and reliability of the entire electronic device. Through its unique position and innovative technology in the packaging field, ABF Substrate has injected new vitality into advanced chip packaging and promoted the continuous evolution of electronic devices.
How is ABF Substrate different from traditional PCB?
As an advanced substrate material, ABF Substrate presents many significant differences when compared with traditional PCBs. From structure, manufacturing technology to application, ABF Substrate provides more efficient and reliable solutions for electronic devices by adopting a colloid-free structure and highly precise manufacturing processes.
First of all, in terms of structure, compared with traditional PCB, ABF Substrate adopts a design that does not contain colloidal copper phosphate. This colloid-free structure makes ABF Substrate more compact in circuit layout, reduces signal transmission losses, and improves the stability of high-frequency signal transmission.
Secondly, in terms of manufacturing technology, ABF Substrate adopts advanced high-density integrated circuit (HDI) manufacturing technology. Compared with the traditional PCB manufacturing process, HDI technology can achieve smaller and higher-density component layout, improving the performance of the circuit board. This technological breakthrough enables ABF Substrate to be capable of more complex electronic devices and meet the needs of today’s advanced electronic products for small, lightweight, and high performance.
In terms of application, the adoption of ABF Substrate has also had an impact on all aspects of PCB. For PWBs and PCBs, improvements in the structural characteristics and manufacturing technology of ABF Substrate make it more suitable for high-performance, high-frequency electronic equipment, such as communication equipment and computers. For motherboards and substrate-like PCBs (SLP), the colloid-free structure of ABF Substrate improves its heat dissipation performance, which is crucial for the long-term stable operation of electronic components. In terms of HDI substrates, ABF Substrate achieves a more compact design and improves the overall performance of electronic equipment through highly integrated component layout.
In general, ABF Substrate, as a cutting-edge substrate material, has ushered in revolutionary improvements in structure, manufacturing technology and applications, bringing more possibilities to PCB engineering. The use of this material not only improves the performance of electronic equipment, but also promotes the development of the PCB field in a more advanced and efficient direction.
What is the structure and production technology of ABF Substrate?
As a key component of high-performance electronic equipment, ABF Substrate (colloidal copper phosphate substrate) occupies an important position in the field of PCB engineering due to its excellent structural design and advanced production technology. Let’s dive into ABF Substrate’s structure and production technology, which covers improved HDI manufacturing technology and semi-additive methods, providing a solid foundation for it to be the pinnacle of cutting-edge materials.
ABF Substrate’s structural design is the cornerstone of its success. It uses a colloid-free structure, made by stacking layers of thin film materials, and has excellent electrical properties. The colloidal copper phosphate layer in its structure acts as a conductive channel in the circuit, while achieving good support for electronic devices.
Improved HDI manufacturing technology
In the production process of ABF Substrate, improved HDI manufacturing technology plays a vital role. Through high-density wiring and tiny holes, HDI technology enables circuit boards to achieve more compact designs and improves the performance of electronic devices. ABF Substrate’s innovative application in this area makes it excellent in high-frequency signal transmission and high-density circuit layout.
Semi-additive method
In the manufacturing of ABF Substrate, the semi-additive method is a trend-setting technology. Compared with the traditional additive method, the semi-additive method reduces the manufacturing cost and improves the reliability of the circuit board by reducing the number of added layers. This technological innovation enables ABF Substrate to better adapt to advanced packaging needs and promotes the development of IC packaging technology.
The excellence of ABF Substrate’s structure and production technology provides solid support for the high performance of electronic devices. It is widely used in high-frequency signal transmission, thermal management and advanced packaging fields, and has become the first choice material for electronic engineers pursuing excellent performance.
In conclusion, ABF Substrate has not only made a huge breakthrough in structural design, but also provided strong support for its wide application in the field of PCB engineering through the application of improved HDI manufacturing technology and semi-additive methods. The new application prospects of this cutting-edge material will surely promote the entire electronics manufacturing industry to develop towards a higher level of technology.
ABF Substrate Frequently Asked Questions (FAQs)
What is the difference between ABF Substrate and regular PCB?
ABF Substrate is a colloidal-free copper phosphate substrate that has significant differences in structure and manufacturing technology compared to traditional PCBs. Traditional PCBs usually use colloid connections, while ABF Substrate achieves a colloid-free structure through a highly precise manufacturing process, providing better signal transmission and thermal management performance.
What application scenarios is ABF Substrate suitable for?
ABF Substrate is widely used in high-performance electronic equipment, especially in scenarios that require high-frequency signal transmission and excellent thermal management performance. Its types include single-layer, multi-layer and high-density integrated circuits (HDI), which are suitable for various advanced electronic devices and packaging technologies.
How to make ABF Substrate?
The manufacturing of ABF Substrate involves improved HDI manufacturing technology and semi-additive methods. These advanced manufacturing processes ensure the realization of colloid-free structures while maintaining a high degree of precision to meet the stringent substrate requirements of modern electronic devices.
What is the thermal management performance of ABF Substrate?
ABF Substrate is known for its good thermal conductivity properties, which aids in thermal management of electronic devices. This means that it can effectively dissipate heat during high-load operation, ensuring that the device operates within a reliable operating temperature range.
What are the advantages of ABF Substrate in IC packaging?
ABF Substrate has significant advantages in IC packaging, especially when using improved HDI manufacturing technology and semi-additive methods. These technologies improve packaging reliability and support advanced chip packaging requirements.
What is the future development trend of ABF Substrate?
As a cutting-edge material for PCB engineering, ABF Substrate will continue to develop in the future. As the demand for high performance and miniaturization in electronic equipment continues to increase, ABF Substrate is expected to be widely used in more fields and promote technological innovation in PCB engineering.
Full text overview of ABF Substrate
ABF Substrate, a substrate containing colloidal copper phosphate (Adhesiveless Build-Up Film Substrate), is an important cutting-edge material in the field of PCB engineering. Its colloid-free structure and highly precise manufacturing process provide breakthrough support for the performance of electronic devices, while playing a key role in promoting technological progress in the PCB field.
Among the applications of ABF Substrate, the most striking thing is its excellent performance in high-frequency signal transmission. By achieving low-loss characteristics, ABF Substrate ensures the stability of signal transmission and provides a faster and more reliable data transmission channel for electronic devices. This not only makes high-performance electronic products more responsive, but also provides technical support for innovation in communications, entertainment and other fields.
ABF Substrate also demonstrates excellent performance in thermal management. Its excellent thermal conductivity helps dissipate heat and effectively maintain a stable operating temperature of electronic devices. In today’s pursuit of smaller, higher-performance electronic devices, good thermal management not only extends the life of the device, but also improves the overall performance of the device.
Compared with traditional PCBs, ABF Substrate’s differences in structure and manufacturing technology further highlight its cutting-edge status. From PWBs and PCBs to motherboards and substrate-like PCBs (SLP), to high-density integrated circuit (HDI) substrates, the adoption of ABF Substrate promotes innovation in PCB engineering and provides strong support for the continuous upgrading of electronic products.
Especially in IC packaging, ABF Substrate plays a key role. By adopting improved HDI manufacturing technology and semi-additive methods, ABF Substrate provides reliable support for advanced chip packaging, achieving higher integration and smaller packaging volume, thereby further promoting the development of chip technology.
Overall, the wide application of ABF Substrate not only improves the performance of electronic devices, but also leads the way in promoting technological progress in the PCB field. By gaining an in-depth understanding of its structure, production techniques and applications in different types of electronic devices, we can better understand how this cutting-edge material has become an important enabler in the field of electronic engineering. In the future, with the continuous development of technology, ABF Substrate will continue to lead the innovation direction of PCB engineering and inject more possibilities into our electronic life.