Global Semiconductor packaging Substrate Firm. High speed and high frequency material packaging substrate manufacturing. The packaging substrate will be made with BT materials, ABF materials, Rogers materials. or other series base materials.
The PCB Package Substrate, a pivotal component within semiconductor packaging, is a common facet encountered in daily professional interactions. Yet, what precisely does it encompass? PCB denotes Printed Circuit Board, acting as the base for electronic circuits. Package Substrate refers to the material utilized for encasing integrated circuits. Thus, PCB Package Substrate essentially denotes the material employed for encapsulating chips on a printed circuit board.
The significance of PCB Package Substrate extends beyond mere chip packaging. It carries the crucial responsibility of facilitating a secure electrical connection between the chip and the PCB, while also providing essential mechanical support to ensure the operational stability and reliability of the packaged chip. Essentially, PCB Package Substrate serves as the foundation of chip packaging, directly influencing the performance and reliability of the entire circuitry.
In semiconductor packaging processes, the selection of appropriate Package Substrate is paramount. Different chip types and application scenarios necessitate distinct Package Substrate types to fulfill specific requirements. For instance, high-density packaging demands Package Substrate with advanced interconnection technologies to accommodate intricate circuit layouts. Conversely, flexible electronic products necessitate Package Substrate with Rigid-Flex structures to enable degrees of bending and twisting.
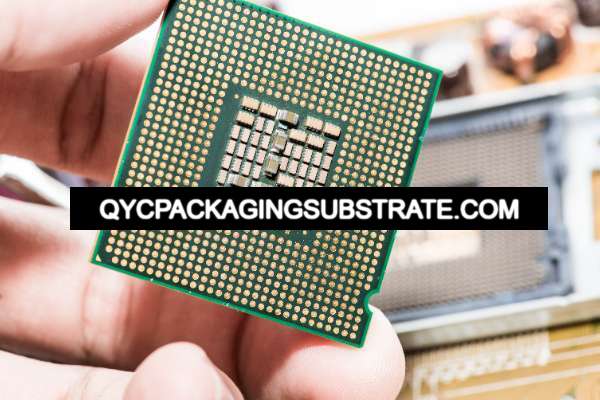
Global Semiconductor packaging Manufacturer
PCB package substrate plays a vital role in semiconductor packaging by serving as both a foundational material and a conduit between the chip and the PCB. Understanding its essence and significance is crucial for optimal selection and application of packaging materials, ultimately driving advancements and innovations in the semiconductor industry.
What are the different types of Package Substrate?
These diverse Package Substrate variants possess unique attributes concerning their structure and utilization, catering to distinct scenarios and requirements.
Initially, High-Density Interconnect (HDI) boards represent a specialized category of PCBs distinguished by exceedingly high line and interconnection densities. They employ sophisticated manufacturing techniques like micro-line fabrication, blind vias, and buried vias to achieve greater signal layers and a more condensed layout.
This configuration facilitates intricate three-dimensional arrangements and enhanced spatial utilization while ensuring superior mechanical stability and reliability. Rigid-Flex boards find applicability in scenarios requiring folding, bending, or confined spatial constraints, such as medical apparatus and aerospace technologies.
Choosing the appropriate Package Substrate type depends on specific application requirements, including design requirements, performance requirements, space constraints and other factors. Therefore, when choosing Package Substrate, you need to consider these factors comprehensively and choose the most suitable type to meet the project needs.
Why do global semiconductors use Package Substrate?
In the global semiconductor packaging manufacturing industry, there are many reasons for choosing to use Package Substrate. These reasons mainly cover how it improves performance, reliability, and its advantages in a variety of application scenarios. These aspects are discussed in detail below:
Package Substrate can improve the performance of semiconductor devices. By using advanced manufacturing processes and materials, Package Substrate can achieve higher density and lower signal transmission delays, thereby improving device efficiency and response speed.
It can effectively resist the effects of mechanical stress and thermal stress, reducing device failure rates caused by environmental changes or workload. This makes Package Substrate the packaging material of choice for many key application fields, such as automotive electronics, aerospace and other fields, which require extremely high reliability.
The Package Substrate offers a versatile design and manufacturing framework tailored to diverse application needs. Its adaptable nature allows for customization, accommodating various specifications such as size, architecture, and connectivity options. This adaptability renders Package Substrate applicable across a broad spectrum of industries, including but not limited to consumer electronics, industrial automation, and medical devices. Its versatility ensures alignment with evolving market demands and technological advancements. In essence, semiconductor packaging manufacturers globally opt for Package Substrate due to its capacity to enhance performance, reliability, and its compatibility with a multitude of application contexts. As technology progresses and market dynamics shift, Package Substrate will continue to be a pivotal driver in fostering innovation and progress within the semiconductor packaging sector.
What is the manufacturing process of PCB Package Substrate?
The production process of PCB Package Substrate is a intricate and exacting procedure crafted to ensure optimal levels of product quality and performance. Below, we delineate the pivotal stages of the process and methods to uphold quality and performance.
The manufacturing journey of Package Substrate commences with the design and strategizing phase. During this stage, engineers engage with clients to grasp their needs and specifications, devising Substrate boards and Motherboards accordingly. This phase is pivotal as sound design and meticulous planning directly impact the subsequent manufacturing efficiency and quality.
Following the design finalization, the subsequent step involves procuring the requisite materials for fabrication. These materials typically encompass substrate elements, metallic layers, dielectric layers, alongside other indispensable materials and chemicals. During this juncture, stringent quality checks and material curation are imperative to guarantee the stability and dependability of the end product.
Manufacturing the Motherboard stands as a significant stride in the Package Substrate manufacturing process. Typically, this entails cutting the substrate material to the required dimensions, then integrating layers of metal, printed circuits, etc., onto its surface through chemical or physical means. This stage necessitates a high level of precision and expertise to ensure the flatness and precision of the motherboard.
Subsequently, manufacturing the Substrate emerges as another critical phase in the Package Substrate manufacturing journey. The Substrate commonly comprises a composite material consisting of multiple layers of thin films, serving to provide electrical connections and mechanical support. Manufacturing the Substrate involves stacking layers of diverse materials as per design, employing pressure and temperature to bind them together. Throughout this process, temperature and pressure must be meticulously controlled to secure robust, bubble-free bonding between the various Substrate layers.
Post-completion of manufacturing, Package Substrate undergoes rigorous quality and performance assessments. These evaluations typically encompass visual inspection, dimensional measurement, electrical testing, reliability testing, etc. Only upon successful clearance of these assessments can the product be deemed qualified and primed for utilization.
Through the aforementioned steps, the Package Substrate manufacturing process culminates. Each phase demands precision technology and stringent quality management to ensure that the final product’s quality and performance align with customer requisites and standards.
In what fields does PCB Package Substrate have practical applications?
As a crucial element of semiconductor packaging, PCB Package Substrate finds extensive application across various sectors such as telecommunications, healthcare, automotive, and more. It is favored for its ability to ensure consistent electrical connections, offer mechanical reinforcement, and fulfill other essential functions, thereby enhancing product performance, dependability, and competitiveness.
In the realm of telecommunications, including the production processes of 5G base stations and networking devices, Package Substrate assumes a pivotal role. It is extensively utilized in radio frequency (RF) modules, antenna assemblies, and other components to facilitate high-frequency, high-speed signal transmission, meeting the demanding performance criteria of contemporary communication technologies.
Within the domain of medical equipment manufacturing, Package Substrate finds wide-ranging use in diverse electronic medical devices like imaging equipment and implantables. These substrates guarantee steadfast and trustworthy electrical connections, ensuring seamless operation of medical apparatus while adhering to the stringent safety and reliability standards mandated by the medical industry.
In the realm of automotive electronics, Package Substrate plays an essential role, permeating vital elements like electronic control units (ECUs), automotive radar systems, and vehicle communication networks, all contributing to the progression of automotive intelligence, automation, and electrification. Employing Package Substrate optimizes the amalgamation and effectiveness of automotive electronic systems, thereby elevating vehicle safety, convenience, and driving satisfaction.
Across these sectors, semiconductor packaging manufacturers worldwide persistently innovate and develop Package Substrate solutions tailored to diverse application scenarios, driving the advancement and progression of related industries. As technology evolves and market needs shift, Package Substrate will remain instrumental in furnishing robust and dependable foundational support for products across various sectors.
How to obtain PCB Package Substrate?
If you’re keen on acquiring top-notch PCB package substrates, there exist numerous avenues and channels to explore. Our company stands out as a pivotal supplier to worldwide semiconductor packaging manufacturers, offering a plethora of options and tailor-made solutions.
There are myriad professional semiconductor packaging manufacturers globally that offer diverse varieties and specifications of package substrates. Directly reaching out to these manufacturers allows access to detailed product information, technical specs, and personalized services. This approach not only guarantees product quality but also facilitates expert guidance from the manufacturer to cater to specific requirements.
Certain professional supply chain platforms and electronic component trading hubs serve as crucial means to procure package substrates. On these platforms, users can peruse products from multiple manufacturers, compare prices and services, and engage directly with suppliers. This method offers flexibility and suits scenarios requiring specific specifications or small batch needs.
Establishing robust partnerships is paramount in securing high-quality package substrates. Through forging close ties with global semiconductor packaging manufacturers, one gains access to enhanced resources and support. This encompasses regular supply chain management meetings to collaboratively develop new products or address potential supply chain challenges, ensuring timely access to requisite package substrates.
Global semiconductor packaging manufacturers often extend customized solutions to meet clients’ distinct requirements. By closely collaborating with manufacturers, one can customize substrate design, materials, and production processes to precisely align with project needs. This personalized service is typically achieved through a tightly knit working relationship with the manufacturer.
Moreover, global semiconductor packaging manufacturers frequently furnish online resources and technical assistance, comprising product manuals, technical specifications, and FAQs. Thoroughly reviewing this information aids in better comprehending product performance and applications, enabling well-informed purchasing decisions.
In essence, there are myriad avenues to procure PCB package substrates, contingent upon specific needs and priorities. By fostering solid relationships with global semiconductor packaging manufacturers, one can secure high-caliber, customized products to underpin project reliability.
What factors affect the quotation of PCB Package Substrate?
The quotation of PCB Package Substrate is affected by many factors, including materials, design complexity, order volume, etc. Understanding these factors is critical to developing a sound budget and selecting the appropriate solution.
First of all, material is one of the main factors affecting Package Substrate quotation. The choice of different types of substrates, metal layers, and special materials directly affects costs.
Complex designs require more process flows and processing steps, which increases production costs. For example, if a design requires the use of more layers, higher density, or finer features, the corresponding manufacturing costs will increase.
Additionally, the quantity of orders will also impact the pricing of PCB Package Substrate. Generally, larger orders can secure lower per-unit costs due to economies of scale achieved through mass production, as well as favorable bulk purchasing discounts. Conversely, smaller orders typically incur higher per-unit prices due to production inefficiencies and inadequate spreading of fixed costs, resulting in higher per-unit expenses.
In summary, the pricing of PCB Package Substrate is influenced primarily by materials, design intricacy, and order volume. When selecting an appropriate Package Substrate, customers should carefully weigh these factors and make informed decisions based on their project’s specific requirements. Collaborating with manufacturers enables customers to obtain tailored solutions and procure the most cost-effective products tailored to their exact needs.
What are the frequently asked questions about PCB Package Substrate that need to be answered?
What are some common challenges associated with PCB Package Substrate?
Common challenges include ensuring compatibility with specific chip designs, managing thermal dissipation, and optimizing signal transmission across the substrate.
How does the manufacturing process of PCB Package Substrate unfold, particularly concerning Motherboard and Substrate production?
The manufacturing process involves intricate steps ensuring the quality and performance of both Motherboard and Substrate. This meticulous approach ensures the effectiveness of the final product.
How can businesses and individuals acquire PCB Package Substrate, and what channels are available for procurement?
Procuring PCB Package Substrate involves engaging with global semiconductor packaging manufacturers. These manufacturers offer a variety of types and specifications, tailored to meet diverse customer needs and application scenarios.
What factors influence the pricing of PCB Package Substrate?
Several factors, including materials, design complexity, and order volume, impact the pricing of PCB Package Substrate. Understanding these elements helps businesses make informed decisions based on their specific requirements.
How does the manufacturing process of PCB Package Substrate unfold, particularly concerning Motherboard and Substrate production?
The manufacturing process involves intricate steps ensuring the quality and performance of both Motherboard and Substrate. This meticulous approach ensures the effectiveness of the final product.