High-precision Package substrate manufacturer. We use advanced Msap and Sap technology to produce High multilayer interconnection substrates from 2 to 20 layers.
In modern electronic equipment, packaging substrate (Package Substrate) plays a vital role. It is the support and connection hub of electronic components and plays a key role. To deeply understand the packaging substrate, we must first understand its basic structure and one of its important components the die.
Packaging substrates represent a fundamental technology within electronic equipment, akin to the central stage for electronic components. These plate-like structures, typically crafted from insulating materials, serve as the backbone, supporting and interconnecting dies, wires, packaging materials, and other essential components. Packaging substrates find applications across a broad spectrum of electronic devices, spanning from smartphones and tablets to computer servers and automotive electronic systems. Their design and quality wield a direct and profound impact on the equipment’s performance, reliability, and cost, making them a critical determinant of overall device excellence.
This article will delve into the critical role of die and packaging substrate in the packaging process. We will look at what dies are, what they do, and how they are closely interrelated with the packaging substrate. We also discuss die and packaging substrate material selection and how they affect the performance of electronic devices. Finally, we’ll look to the future to explore trends in packaging substrate technology and how innovation and sustainability practices can be leveraged to drive advancements in electronics.
As we dive deeper into these key elements, you’ll better understand the centrality of packaging substrates and their integral role in modern electronics. Through this article, we encourage readers to pay attention to the importance of packaging substrates and actively participate in the continued innovation of electronic technology. This will not only promote the development of the electronics field, but also help achieve more sustainable and environmentally friendly electronic device manufacturing.
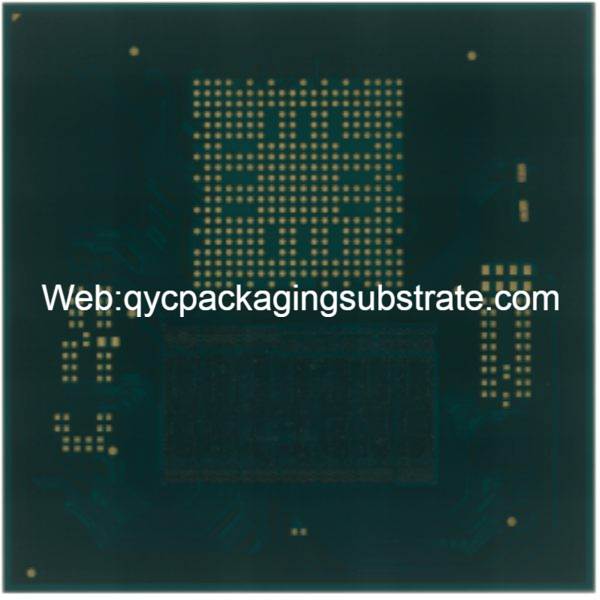
Die substrate package
What is a die?
Explain the definition and role of grains
Dies, often called “die”, are a vital component in the field of electronic packaging. It is a tiny semiconductor chip made of silicon or other semiconductor materials. Microscopic electronic components such as transistors, capacitors and resistors are integrated on the die, which together form a fully functional electronic device. This microchip contains the key functions of electronic devices, such as microprocessors, memory chips, sensors, and integrated circuits.
Dies, often referred to as “die,” stand as indispensable components within the realm of electronic packaging. These steps are carried out with exacting precision to create the intricate circuitry and components that enable the chip to perform its intended functions. The use of advanced materials and cutting-edge technology is pivotal in the fabrication of these semiconductor dies, allowing them to power the modern electronic landscape with their compact yet immensely powerful capabilities.The outcome of this precision craftsmanship is a microchip with the ability to process and store digital information, a driving force behind the evolution of modern electronic devices.
Revealing the importance of die in packaging substrates
The die is one of the core elements of the packaging substrate, which undertakes the key task of connecting electronic components to the circuit board. When the dies are packaged onto a substrate, electrical connections between them and other electronic components are established, enabling the functionality of the device. The location and layout of the die determines the performance and efficiency of the circuit.
Furthermore, the semiconductor dies themselves also play a pivotal role in heat conduction within the packaging substrate. In the contemporary landscape of high-performance electronic devices, the efficient dissipation of heat is essential to prevent potential damage from overheating. The precise positioning and dimensions of these dies are of paramount importance in the realm of thermal management. They frequently collaborate with heat sinks and thermally conductive materials to ensure that the device maintains a safe and controlled temperature range.
In essence, semiconductor dies serve as the heart of electronic devices, and their design and arrangement wield a significant impact on the device’s overall performance, reliability, and heat dissipation capabilities. As a result, the meticulous consideration and optimization of die layout and design are integral elements in the crafting and design of packaging substrates.
What is Package Substrate?
Packaging substrate, also known as packaging substrate, is a vital component in electronic packaging. It is usually a substrate with circuit lines and electrical connections used to support and connect multiple electronic components, such as dies, resistors, capacitors and other packaged components. The main functions of the packaging substrate include providing mechanical support, electrical connections, thermal management, and circuit routing.
As a physical foundation, the packaging substrate plays the role of transmitting signals and power, dissipating heat from electronic components, and providing mechanical stability. It acts as a bridge between electronic components in electronic devices, enabling them to work together through its multi-layer structure and circuit design.
The key role of packaging substrate in electronic packaging
Packaging substrates play a vital role in electronic packaging. More than just a physical platform for connecting components, it plays a key role in circuit performance, signal transmission, and overall system reliability.
Circuit performance improvement: The design and material selection of the packaging substrate have a direct impact on circuit performance. It provides the required electrical characteristics such as resistance, capacitance and inductance to ensure the quality of signal transmission.
Signal transmission: The circuit layout and hierarchy of the package substrate determine the speed and accuracy of signal transmission. A well-designed packaging substrate can reduce signal delay and improve the response speed of the device.
Thermal Management: Package substrates help control the temperature of electronic components through thermal dissipation technologies such as thermal circuits and thermal pads. This is critical to extending component life and ensuring performance stability.
Reliability: The reliability of the packaging substrate is a key factor in system stability. It must be resistant to temperature changes, vibration, humidity and other environmental factors to ensure continued normal operation of the equipment.
In modern electronic packaging, the design and manufacturing of packaging substrates has become an integral part. It provides a solid foundation for electronic equipment and supports the continuous development of electronic technology.
Die, packaging substrate and packaging process
In electronic packaging, the relationship between die and package substrate is crucial. The die is usually the core of a microchip and contains a microprocessor, integrated circuit or other functional electronic component. These grains are often very small, but contain millions of crystal lattice structures that perform specific electronic functions. The packaging substrate is a key component that supports the die and provides connection, protection and heat dissipation. Therefore, the die can be regarded as the brain of the electronic device, and the packaging substrate is the structure that supports and protects this brain.
The key functions of the die are to perform computations, store data, and control devices. However, they often need to work in conjunction with other dies, sensors, antennas, and other components to achieve the full functionality of the device. This is where the value of packaging substrates lies. The packaging substrate not only provides physical support, but also ensures that the different components work together effectively by providing electrical connections and signal transmission. Therefore, close cooperation between the die and the packaging substrate is a key factor in achieving high performance and functionality in modern electronic devices.
The packaging process is a critical step in bringing the die and packaging substrate together while ensuring they can work together. This process involves multiple key links, including packaging substrate design, die placement, welding, sealing and testing. The following are the general steps of the packaging process:
Design the packaging substrate: Before the packaging process begins, engineers need to design the packaging substrate suitable for the specific application. This includes selecting substrate materials, determining hierarchies and defining connection points.
Placement of die: On the designed packaging substrate, the die is precisely placed at its designated location. This often requires highly sophisticated automated equipment.
Soldering: Once the dies are placed in place, they need to be connected to the circuitry on the package substrate. This is usually achieved through soldering techniques such as ball grid array soldering (BGA).
Sealing: To protect the die and other internal components from the external environment, packages need to be sealed. This usually involves special encapsulation materials such as resin or silicone on the encapsulation substrate.
Testing: Finally, the assembled package will undergo rigorous testing to ensure that the die and package substrate are functioning properly. This includes electrical testing, temperature testing, and other performance testing.
Through these steps, the packaging process organically combines the die and packaging substrate to ensure the stability and performance of the electronic device. This close collaboration enables modern electronic devices to perform complex functions, ranging from smartphones to high-performance computers. Therefore, the coordinated working of the die, packaging substrate and packaging process is critical to the success of the electronics industry.
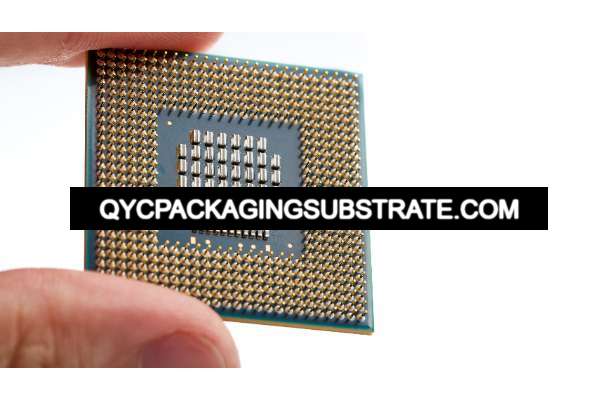
Die substrate package
Material selection of die and packaging substrate
In the field of electronic packaging, selecting appropriate materials is crucial to the performance and reliability of the die and package substrate (Package Substrate). This section will explore the factors to consider when selecting these materials and highlight the criticality of material selection to performance.
Discussing factors in selecting die and packaging substrate materials
Electrical performance requirements: First, it is critical to consider the electrical performance requirements of the die and packaging substrate. The material’s conductivity, dielectric constant, and magnetic properties all affect the performance of the circuit. Different applications require different electrical performance characteristics, so the choice of materials must be optimized based on specific needs.
Thermal Performance: Another Vital Consideration
Thermal performance stands as another crucial factor. Electronic devices frequently generate heat, necessitating efficient heat dissipation to maintain safe temperature levels. The thermal conductivity and coefficient of thermal expansion of a material play significant roles in determining its efficacy in high-temperature environments.
Mechanical Strength: Safeguarding Electronic Devices
The mechanical strength of materials assumes a paramount role in ensuring the physical protection of electronic devices, particularly during transportation and installation. Mechanical stress can impact the die and packaging substrate. Thus, selecting materials with adequate mechanical strength is imperative to guarantee the resilience of the devices.
Chemical stability: Some applications may be exposed to chemicals, such as corrosive liquids or gases, which require materials to have good chemical stability to resist corrosion.
Emphasis on the importance of choosing the right materials for performance
Selecting the appropriate materials has a significant impact on the performance and reliability of electronic packaging. Wrong material selection can lead to circuit failure, thermal problems, or mechanical damage. Here are some key performance aspects of importance:
Reliability: Appropriate material selection can improve the reliability of the die and packaging substrate and reduce the risk of failure.
Performance Optimization: Optimized selection of materials can improve circuit performance such as signal transmission speed, thermal management, and power consumption.
Energy saving: By choosing materials with better thermal conductivity, the energy consumption of the equipment can be reduced and energy saving improved.
Cost-Effectiveness: Material selection also affects manufacturing costs. Choosing the right materials can improve performance while reducing production costs.
In summary, the selection of appropriate materials is critical to the performance of the die and packaging substrate.
Future trends in packaging substrate technology
As technology continues to evolve, die and packaging substrate technologies are also constantly developing to meet the growing needs of the electronics market. Future trends will explore the technological development of die and packaging substrates in the following aspects, and emphasize the importance of continuous innovation for electronic packaging.
Discuss the development direction of die and packaging substrate technology
Three-dimensional packaging: In the future, die and packaging substrate technology will develop more towards three-dimensional packaging. This means the dies will be vertically stacked, allowing for higher performance density and smaller package sizes.
High-density interconnection: In order to meet the needs of high-speed communication and big data, die and packaging substrates will develop towards higher-density interconnection technology to support faster data transmission speeds and more functional integration.
Material innovation: In the future, die and packaging substrates will continue to seek new material innovations to provide better heat dissipation performance, higher reliability and lower costs.
Emphasizing the impact of continuous innovation on future electronic packaging
Energy Saving and Sustainability: As the focus on energy efficiency and sustainability continues to increase, die and packaging substrate technologies will develop in a more energy-saving and environmentally friendly direction to reduce energy consumption and resource waste.
Automation and Intelligence: As we look ahead, the manufacturing processes for packaging substrates will increasingly lean on automation and intelligent technologies. This strategic shift aims to enhance both production efficiency and the precision of quality control measures.
Security and Reliability: In the era characterized by smart devices and the pervasive Internet of Things, the paramount considerations are security and reliability. Hence, future developments in die and packaging substrate technologies will place heightened emphasis on ensuring data security and bolstering system stability.
In general, future die and packaging substrate technologies will develop in the direction of smaller, faster, more energy-efficient, more reliable and smarter. Continuous innovation will be the key to advancing the field of electronic packaging, paving the way for more innovative electronic products and applications.