Semiconductor FC BGA Substrate Firm, We mainly produce ultra-small bump pitch substrate, ultra-small trace and spacing packaging substrate. Most of the FCBGA substrates were made with ABF base materials.
The Semiconductor FC BGA substrate stands out as an exemplary manifestation of semiconductor packaging technology, seamlessly amalgamating the exceptional benefits of Flip-Chip and Ball Grid Array (BGA). This technology finds widespread application in the electronic equipment domain, offering a closer inspection of its intricacies reveals its pivotal role in contemporary electronic design.
At its core, the Semiconductor FC BGA substrate is a sophisticated technology employed for packaging integrated circuits. The nomenclature is indicative of its composition, with “FC” denoting Flip-Chip and “BGA” representing Ball Grid Array. Notably, the distinctive characteristic of this packaging technology lies in the method wherein the chip is inverted onto the substrate and intricately connected through a solder ball array. The outcome is a compact and highly efficient packaging structure, marking the essence of Semiconductor FC BGA substrate technology.
Contribution of Flip-Chip Technology
Flip-Chip technology is the cornerstone of Semiconductor FC BGA substrates. By flipping the chip to the back, shorter signal paths and a more compact layout are achieved. This construction makes signal transmission more efficient, reduces the effects of resistance and inductance, and improves circuit performance.
Innovative applications of Ball Grid Array
The Ball Grid Array (BGA) offers uniformly distributed connections throughout the package, featuring a solder ball array situated at the chip’s bottom. These solder balls establish a robust and reliable electrical connection with the substrate, forming a resilient bond. This spherical arrangement not only facilitates a higher connection density but also exhibits superior tolerance for thermal expansion, thereby laying a sturdy foundation for the reliability and stability of electronic devices.
Widely employed in electronic equipment, Semiconductor FC BGA substrates find applications across a spectrum of devices—from smartphones and computers to communication equipment and medical devices. Its flexibility and high performance position it as the preferred choice for contemporary electronic designs. In smaller devices, its compact packaging structure enables streamlined designs, while in larger devices, the high-density connections ensure steadfast signal transmission.
The future outlook for Semiconductor FC BGA substrates is promising. As electronic devices persistently pursue high performance and miniaturized design, this packaging technology will undergo continual evolution spurred by technological innovation. From heightened integration to more intricate application scenarios, Semiconductor FC BGA substrates will maintain a pivotal role in the ever-progressing field of semiconductor packaging.
In summary, Semiconductor FC BGA substrates epitomize cutting-edge technology in semiconductor packaging. Their distinctive structure and outstanding performance position them as indispensable components in contemporary electronic design.
What are the types of Semiconductor FC BGA substrates?
Semiconductor FC BGA substrate, as a semiconductor packaging technology, has emerged in many types, each of which shows unique characteristics and applicable fields in the electronic field. The following is an in-depth analysis of the main types of Semiconductor FC BGA substrates.
By optimizing circuit layout and heat dissipation design, this substrate is suitable for applications with higher performance requirements, such as computer servers, graphics processing units, etc. Its unique heat dissipation characteristics enable it to maintain stable performance under high load operation.
In addition, the design of the flexible Semiconductor FC BGA substrate pays more attention to its plasticity. This substrate has high flexibility and is suitable for devices that require curved shapes, such as wearable devices, curved displays, etc. Its flexible design makes it possible to integrate circuits within complex-shaped housings, providing room for innovative designs.
In addition, the temperature-stable Semiconductor FC BGA substrate performs well in high temperature or extremely cold environments.
This substrate connects the chip on one side and the external system on the other side, providing an efficient connection solution for multi-module or double-sided devices, such as devices where camera modules and display modules are integrated at the same time.
Overall, the diversity of Semiconductor FC BGA substrates enables it to meet the needs of various application scenarios. Different substrate types can be selected based on the specific requirements of the device to achieve optimal performance and design flexibility. This makes Semiconductor FC BGA substrate one of the most popular packaging technologies in the electronic field.
What are the advantages of Semiconductor FC BGA substrate?
The Semiconductor FC BGA substrate (Flip-Chip Ball Grid Array) has emerged as a dependable choice for high-density integrated circuits in contemporary electronic design, owing to a series of distinct advantages. In comparison to traditional packaging technology, its benefits are readily apparent.
Foremost, the Semiconductor FC BGA substrate distinguishes itself through its remarkable level of integration. Leveraging Flip-Chip technology, the chip establishes a direct connection with the substrate, bypassing the conventional method of using wires. This results in a notable reduction in circuit area, enabling the integration of more functions within a confined space. The outcome is a highly integrated circuit board, aligning seamlessly with the demands of cutting-edge electronic devices for compact size, lightweight design, and high performance.
Secondly, Semiconductor FC BGA substrate has excellent electrical properties. Flip-Chip connection method reduces resistance and inductance, increases signal transmission rate, reduces signal delay, thereby optimizing overall circuit performance. This is particularly important for high-frequency applications such as communications equipment and processors. By using FC BGA substrates, designers can achieve faster data transmission rates and lower power consumption, providing a solid foundation for improving the performance of electronic products.
Furthermore, the noteworthy heat dissipation capability of Semiconductor FC BGA substrates deserves attention. The direct connection between the chip and the substrate facilitates more efficient heat conduction and dissipation compared to traditional packaging technologies. This results in a lower operating temperature for electronic devices, enhancing system stability and reliability, a critical advantage for high-performance processors and graphics processing units.
Moreover, Semiconductor FC BGA substrates demonstrate outstanding space utilization efficiency. Their compact design and three-dimensional integration capabilities enable the accommodation of a greater number of components within confined spaces. This attribute is especially crucial for portable devices and embedded systems, where optimizing spatial constraints is of paramount importance.
Its application range covers a wide range of fields from communication equipment to computer systems, providing electronic engineers with a flexible and reliable solution. By deeply analyzing these advantages of Semiconductor FC BGA substrate, we can better understand why it occupies such an important position in modern electronic design.
Why choose Semiconductor FC BGA substrate instead of other circuit boards?
First, Semiconductor FC BGA substrates perform excellently in terms of space utilization efficiency. Because it uses Flip-Chip packaging technology, the chip is connected to the substrate upside down, and components can be arranged more compactly than traditional packaging methods. This design makes Semiconductor FC BGA substrates even better in miniaturized and lightweight applications, such as mobile devices and embedded systems.
Secondly, Semiconductor FC BGA substrate has superior electrical performance. This makes Semiconductor FC BGA substrates particularly excellent in high-frequency and high-performance applications, such as those with increasing demands in the communications and computing fields.
Furthermore, the Semiconductor FC BGA substrate boasts notable advantages in heat dissipation. The Flip-Chip packaging design facilitates direct contact between the back of the chip and the heat dissipation substrate, thereby significantly enhancing heat dissipation efficiency. This attribute holds particular significance for applications demanding prolonged high-load operation, such as servers and computer systems.
In terms of applicability, Semiconductor FC BGA substrate is particularly suitable for scenarios that require high circuit board heights. For example, in the aerospace industry, where space is limited and weight requirements are extremely high, Semiconductor FC BGA substrates can become the first choice due to their lightweight and compact design.
Overall, the Semiconductor FC BGA substrate was chosen over other circuit boards mainly for its superior performance in terms of space efficiency, electrical performance and heat dissipation. In applications that have strict requirements on circuit board performance and size, Semiconductor FC BGA substrates will become the ideal choice for designers.
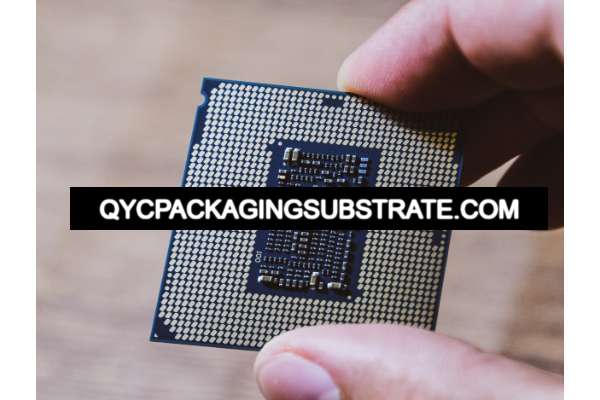
Semiconductor FC BGA Substrate
What is the manufacturing process of Semiconductor FC BGA substrate?
The manufacturing process of Semiconductor FC BGA substrates is a highly precise process that goes through a series of steps to achieve high quality and reliability. From Motherboard to Substrate, the entire process requires precise control and technology.
Motherboard manufacturing process
Design Phase: The initial stage in Semiconductor FC BGA substrate manufacturing involves a meticulous design process encompassing circuit layout, hierarchy, and Ball Grid Array arrangement. Employing sophisticated CAD tools and specialized expertise is crucial to ensure the final circuit layout aligns with the device’s performance and spatial specifications.
Substrate Preparation: An integral step involves the careful selection of suitable substrate material. Commonly employed materials include glass fiber-reinforced epoxy resin (FR-4), renowned for its exceptional electrical properties and mechanical strength. The chosen substrate material undergoes precision cutting and surface treatment to meet the specific design requirements.
Lamination: The designed circuit layer and the substrate are combined through a lamination process. This step involves heating and pressing materials such as copper foil and fiberglass cloth between layers to form a multi-layer board structure. This helps achieve a high level of integration on multi-layer circuit boards.
Substrate manufacturing process
Bonding: Establish a secure connection between the designed semiconductor chip and a specific region on the motherboard through a meticulous bonding process. Typically achieved through the use of adhesives or soldering, this ensures a robust bond between the chip and the substrate.
Flip-Chip Connection: Employ Flip-Chip technology, a crucial aspect of Semiconductor FC BGA substrates. In this phase, the chip is inverted and affixed to the substrate through minute solder joints, enhancing the circuit’s performance and reliability.
Ball Grid Array (BGA) Fabrication: Following the completion of the Flip-Chip connection, attach minuscule solder balls (BGA balls) to the chip’s underside. These balls undergo fusion soldering to corresponding pads on the motherboard, forming a dependable electrical connection.
Testing and Inspection: Implement rigorous testing and inspection procedures at each manufacturing stage. This includes scrutinizing circuit connectivity, chip power consumption, and the quality of solder connections. Only by successfully passing all tests can the quality and reliability of Semiconductor FC BGA substrates be assured.
Ensure high quality and reliability
Manufacturing Semiconductor FC BGA substrates involves a intricate and highly technical process necessitating advanced equipment, precise processes, and stringent quality control systems. Rigorous process control is imperative at every manufacturing step to ensure material consistency and maintain standardized process parameters, thereby minimizing variability in production.
The implementation of a comprehensive quality management system is crucial. This involves meticulous quality inspections at each stage of manufacturing, enabling the timely identification and disposal of substandard products. This proactive approach ensures that only products meeting the highest quality standards progress through the production pipeline.
Furthermore, a commitment to technological innovation is essential. Staying abreast of the latest manufacturing technologies and industry innovations is imperative to ensure that Semiconductor FC BGA substrates remain adaptable to evolving market needs and design challenges. This emphasis on innovation not only fosters product evolution but also positions manufacturers to navigate dynamic market landscapes.
In adhering to these key principles, manufacturers can successfully produce Semiconductor FC BGA substrates characterized by high performance, reliability, and suitability for diverse applications.
What are the application fields of Semiconductor FC BGA substrate?
Semiconductor FC BGA substrates, representing an advanced semiconductor packaging technology, hold significant importance in the realm of electronic equipment. Their distinctive design and exceptional performance have led to widespread utilization across various domains, offering highly integrated and reliable solutions for diverse application scenarios.
Primarily, Semiconductor FC BGA substrates play a pivotal role in the arena of mobile devices. The demanding requirements for compact design and high performance in smartphones, tablets, and other portable devices make Semiconductor FC BGA substrates an optimal choice. The heightened integration features of these substrates enable more compact circuit board designs, effectively meeting the imperative for miniaturization and lightweighting in these devices.
In the field of communications, Semiconductor FC BGA substrate also plays a vital role. Communication equipment has extremely high requirements for high-speed data transmission and stability, and the design of Semiconductor FC BGA substrate enables it to perform well in high-frequency and high-bandwidth applications. This includes base station equipment, communication modules, etc., ensuring the efficient operation of the communication network.
Medical equipment is also one of the important areas for Semiconductor FC BGA substrate applications.Medical equipment places exceptionally stringent demands on the reliability and performance of electronic components, often necessitating the integration of numerous functions within confined spaces. The Semiconductor FC BGA substrate, with its flexibility and high integration capabilities, proves adept at meeting the intricate requirements of medical devices, particularly in the development of compact, high-performance electronic systems like portable monitoring equipment and medical imaging devices.
The robust characteristics of Semiconductor FC BGA substrates make them indispensable in meeting the elevated standards of adaptability and resilience required in the automotive industry.
Semiconductor FC BGA substrate ensures stable operation in complex automotive environments through its reliable packaging and connection technology.
The Semiconductor FC BGA substrate stands as an indispensable component across various electronic equipment domains. Renowned for its exceptional level of integration, robust reliability, and heightened flexibility, it stands as the primary preference for contemporary electronic engineers engaged in the design of advanced electronic systems. As technology continuously advances, the Semiconductor FC BGA substrate is poised to unlock innovative applications across an expanding array of fields, thereby catalyzing further advancements in the electronics industry.
How to obtain Semiconductor FC BGA substrate?
For readers keen on incorporating this advanced technology into their projects, understanding the process of acquiring Semiconductor FC BGA substrates is paramount. Leveraging our expertise as professional suppliers, we recognize the critical nature of this endeavor and offer the following suggestions and guidance to facilitate the successful procurement of the Semiconductor FC BGA substrate you require.
The initial step in obtaining Semiconductor FC BGA substrates involves identifying a reliable supplier, a task achievable through the following means:
Online Platforms and Markets
Explore renowned online platforms and electronic component markets within the industry, such as Digi-Key, Mouser Electronics, and others. These platforms host multiple suppliers offering Semiconductor FC BGA substrates, allowing you to review and choose from a diverse range of options.
Industry communities and forums: Post inquiries in relevant electronic engineer communities and industry forums to obtain recommendations and experience sharing from other professionals.
Cooperate with our company
Customized solutions: Provide customized Semiconductor FC BGA substrate solutions to meet customer-specific technical and design requirements.
Technical support: Provide a professional technical support team to help customers solve technical problems that may be encountered in Semiconductor FC BGA substrate applications.
Reasonable price and delivery time: Provide competitive prices and have certain flexibility in delivery time to meet customers’ project needs.
With the above suggestions, we believe you will be able to obtain the required Semiconductor FC BGA substrate more smoothly and achieve success in your electronic projects. Whether you are looking for a supplier or looking to strengthen your relationship with one, detailed knowledge and insight will help ensure a smooth project.
How to get a quote for Semiconductor FC BGA substrate?
When obtaining a quotation for Semiconductor FC BGA substrate, there are a series of key factors that need to be carefully considered. These factors directly affect the cost and overall manufacturing efficiency. The following are factors to note when obtaining a quote for Semiconductor FC BGA substrates:
Size and number of layers
The size and number of layers of Semiconductor FC BGA substrate are one of the key factors that determine the cost. Larger sizes and more layers typically require more materials and production steps, resulting in increased costs.
Intra-layer structure and technical requirements
The in-layer structure and technical requirements of Semiconductor FC BGA substrate are one of the factors that affect the cost. For example, whether complex interlayer connections, blind via drilling, or other advanced processes are required will have an impact on cost.
Impedance control and signal integrity
If the design requires precise impedance control or has strict requirements on signal integrity, higher-precision manufacturing processes and materials will be required, which may increase costs.
Order volume and delivery time
Generally speaking, high-volume orders may enjoy lower unit prices, while urgent delivery times may incur additional charges. Therefore, order volume and delivery time are also factors that need to be carefully weighed.
When obtaining quotes for Semiconductor FC BGA substrates, manufacturers and suppliers need to understand the specific requirements of the project in detail in order to provide an accurate quote. Making informed decisions by balancing performance, cost and production requirements ensures the most cost-effective Semiconductor FC BGA substrate.
Frequently Asked Questions (FAQs)
What is Semiconductor FC BGA substrate?
The Semiconductor FC BGA (Flip-Chip Ball Grid Array) substrate represents an advanced semiconductor packaging technology that seamlessly merges the benefits of both Flip-Chip and Ball Grid Array configurations. This innovative approach delivers a high-density and dependable support structure for integrated circuits within electronic devices.
What types of Semiconductor FC BGA substrates are there?
There are many types of Semiconductor FC BGA substrates, mainly classified according to different characteristics and applicable fields. Common types include…
What are the advantages of Semiconductor FC BGA substrate compared to traditional packaging technology?
Compared with traditional packaging technology, Semiconductor FC BGA substrate has the advantages of high integration, superior electrical performance and excellent heat dissipation effect. It provides electronic devices with more design flexibility and reliability.
Why choose Semiconductor FC BGA substrate instead of other circuit boards?
Semiconductor FC BGA substrate has unique advantages in high-density integrated circuits. In what scenarios is it more suitable? What was the reason for choosing it?
What is the manufacturing process of Semiconductor FC BGA substrate?
What are the key steps involved in the manufacturing process of Semiconductor FC BGA substrates? From a Motherboard and Substrate perspective, how does the manufacturing process ensure high quality and reliability?
In what application areas are Semiconductor FC BGA substrates widely used?
Semiconductor FC BGA substrates are widely used in electronic equipment, including but not limited to… How do these application areas reflect their diversity and flexibility?
How to obtain Semiconductor FC BGA substrate?
What are the ways to obtain Semiconductor FC BGA substrate? What are some recommended suppliers and manufacturers?
How to get a quote for Semiconductor FC BGA substrate?
If you want to get a quotation for Semiconductor FC BGA substrate, what factors should you pay attention to? What are the main factors affecting costs?
By addressing these commonly asked questions, our aim is to furnish readers with lucid and thorough insights, enabling a better understanding of the attributes, applications, and associated aspects of Semiconductor FC BGA substrates. This information equips readers to make informed decisions in PCB design and harness the full potential of Semiconductor FC BGA substrates.